Any attempt to maintain the equipment systematically and cost-effectively will be frustrated if it continues to fail regularly and the intervals between those failures are always changing because this makes it impossible to put together a dependable maintenance plan. To begin with, breakdowns must be systematically reduced by following the four-phase approach illustrated in Figure “The 4 Phases to Zero Breakdowns”.
Phase 1 (Eliminate forced deterioration)
Phase 1, which focuses on reducing variation in the time interval between failures, corresponds to Steps 1 and 2 of the Autonomous Maintenance program. It contains the following two main strands:
(1) Correct neglected deterioration
The first thing is to correct any obvious deterioration left untreated because of labour or budget constraints or lack of awareness. We should look for the following sorts of situations and deal with them:
- Used all the time but left untended
- Left loose
- Left detached
- Left out of kilter
(2) Eliminate forced deterioration
The second thing is to eliminate forced deterioration, which is abnormal deterioration caused by stress exceeding the value specified in the equipment’s design. To do this, we:
Sustain basic conditions (Keep the equipment clean, properly lubricated, and securely tightened)
Observe correct operating conditions
- Prevent external sources of disturbances
- Knocks, vibration, noise, …
- Ensure that the conditions are compatible with the specifications of the unit and components
- Environmental conditions, proper installation method, etc.
- Ensure that the load matches the equipment’s capacity
Phase 2 (Extend lifetimes through corrective maintenance)
In Phase 2, we try to lengthen the equipment’s intrinsic working life, principally through the following three approaches:
(1) By identifying weaknesses, try to increase the working life of any equipment that soon fails even after all forced deterioration has been eliminated
- Correct design weaknesses
- Insufficient strength
- Installation problems
- Fabrication problems
- Improve equipment’s ability to cope with overloading. If the load cannot be reduced, then the equipment’s weak points must be strengthened.
- Select parts suitable for conditions of use
(2) Eliminate unexpected breakdowns
- Eliminate repair errors
- Instill basic repair skills
- Improve repair methods, etc.
- Eliminate operating errors
- Standardize operating methods
- Introduce error-proofing techniques (poka-yoke), etc.
(3) Correct visible deterioration
Conduct a comprehensive external inspection of hydraulics, pneumatics, drive systems, and electrics, and correct any visible deterioration.
Phase 3 (Monitor and control deterioration)
(1) Estimate the equipment’s working life and periodically restore it to its original condition.
The actions are taken in Phases 1 and 2 extend the equipment’s working life and increase the accuracy with which that life can be estimated. This makes periodically correcting deterioration very reliable and cost-effective.
1 Improve maintainability
Modify the structure of the equipment to make it easier to maintain. For example:
- Use standard components wherever possible
- Make it possible simply to swap failed units in and out
- Simplify disassembly and assembly procedures
- Improve existing jigs and tools, and develop new special-purpose ones
2 Standardize periodic maintenance, and implement the following:
• Periodic checking
• Periodic inspection
• Periodic servicing
• Spare parts standardisation
(2) Use the five senses to spot signs of internal deterioration
If the working life of a unit is hard to estimate, or is inherently variable, then operators must rely on identifying the warning signs of failure. Based on past experience, they should answer questions such as:
- Did the failure give off any warning signs before it happened?
- Is it the type of failure that could actually produce warning signs?
- What kinds of warning signs could be used to identify the impending failure?
- Why weren’t the warning signs recognized before the failure occurred?
- What must be done to make sure that the warning signs are recognized in the future?
- What knowledge and skills does the operator need in order to recognize the warning signs?
Phase 4 (Carry out predictive maintenance)
(1) Use diagnostic techniques to predict the onset of failure
Some typical failure modes, and the diagnostic methods used to measure them, are listed below:
- Leaks
- Fracture
- magnetic scanning, X-rays
- Corrosion
- Abnormal noise
- Abnormal temperature
- infrared thermography
- Abnormal vibration
- vibration measurement
- Deterioration in materials
- AE (acoustic emission)
- Deterioration in lubricants
- SOAP (spectrometric oil analysis program)
- Looseness
- Electrical anomaly
- insulation measurement
(2) Estimate and extend working life breakdowns
- Analysis of fracture surfaces
- stress concentration
- Analysis of material fatigue
- repeated load
- alternating load
- Analysis of gear tooth surfaces

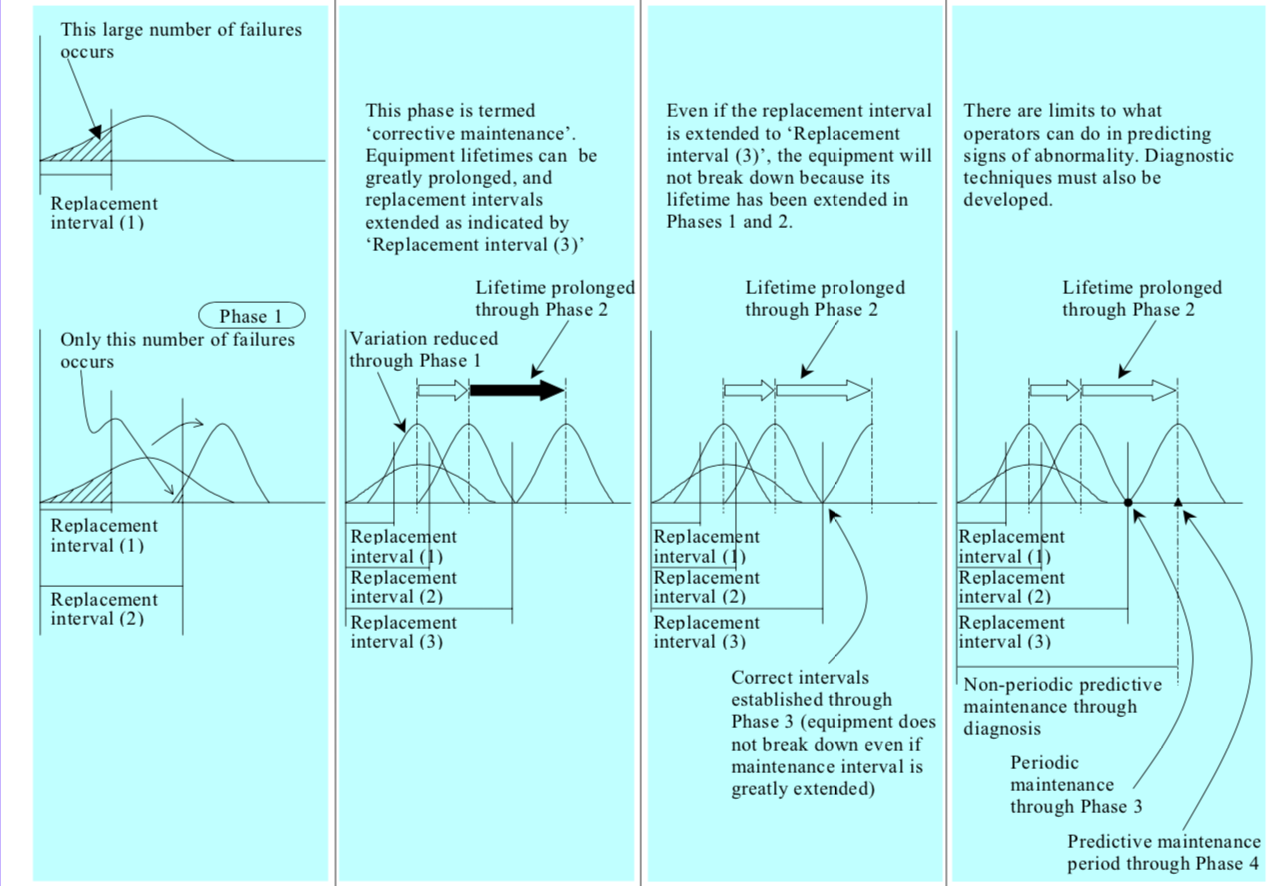
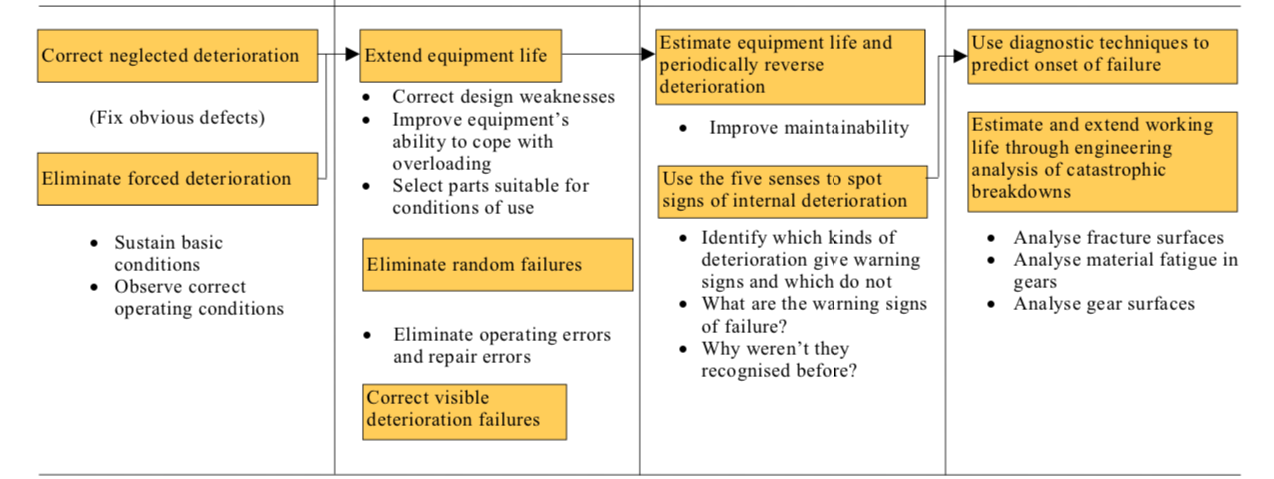