The purpose of this procedure is to define the steps to do a 4M Analysis of a system or subsystem. The goal of this 4M Analysis Procedure is to reduce losses in the factory by using the Equipment Attributes as a guideline to achieve this end.
Focused Improvement training can be taken here
4M Analysis Steps
- Define Improvement Statement
- List Issues into Categories
- Resolve Issues
Define Improvement Statement
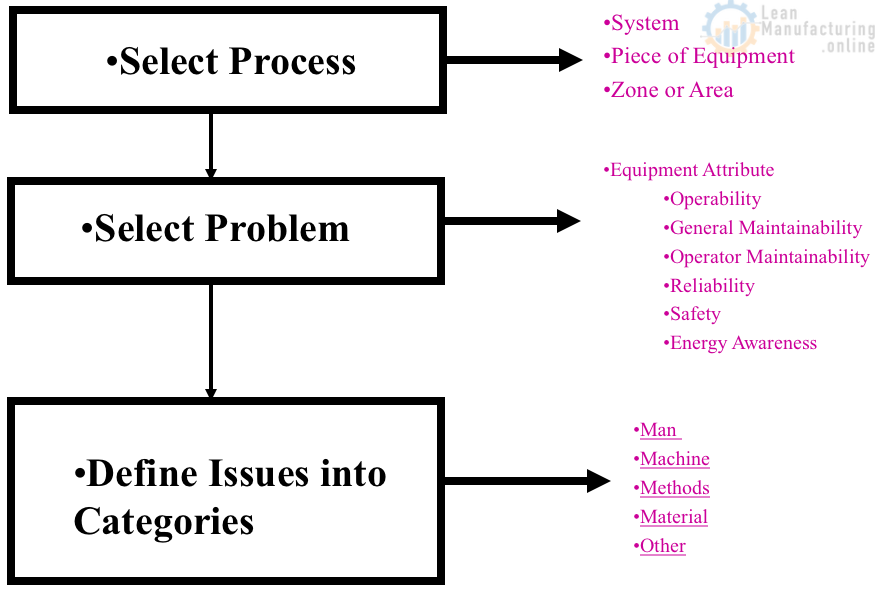
4M Fishbone Diagram
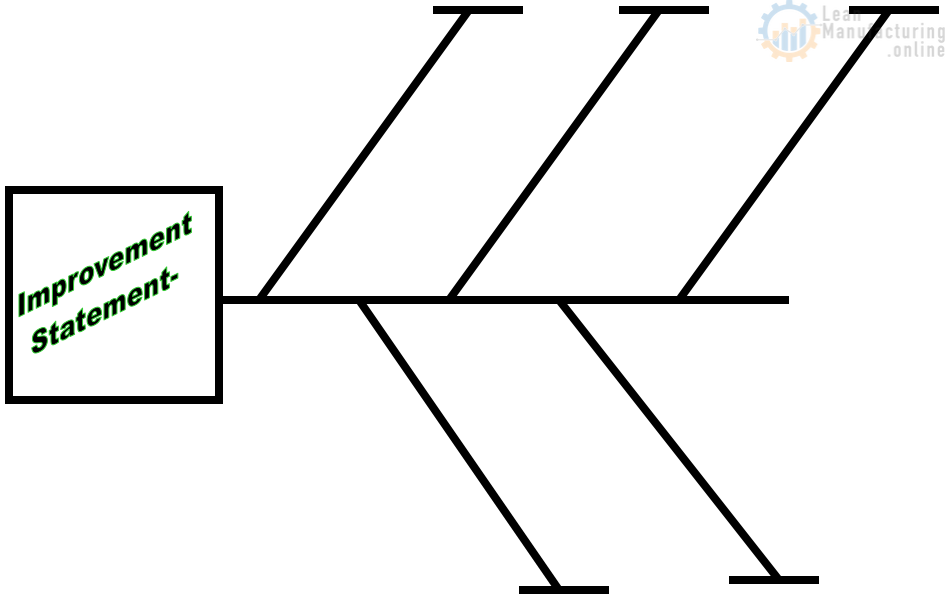
- Select a process system or item that can be replaced by another type of system if necessary.
- Each attribute contains a definition and a set of details that define its purpose
Define Statement for Fishbone
- “Improve”
- Select Process
- Select Attribute
- Statement
- Improve
- COB Unloading Area
- General & Operator Maintainability
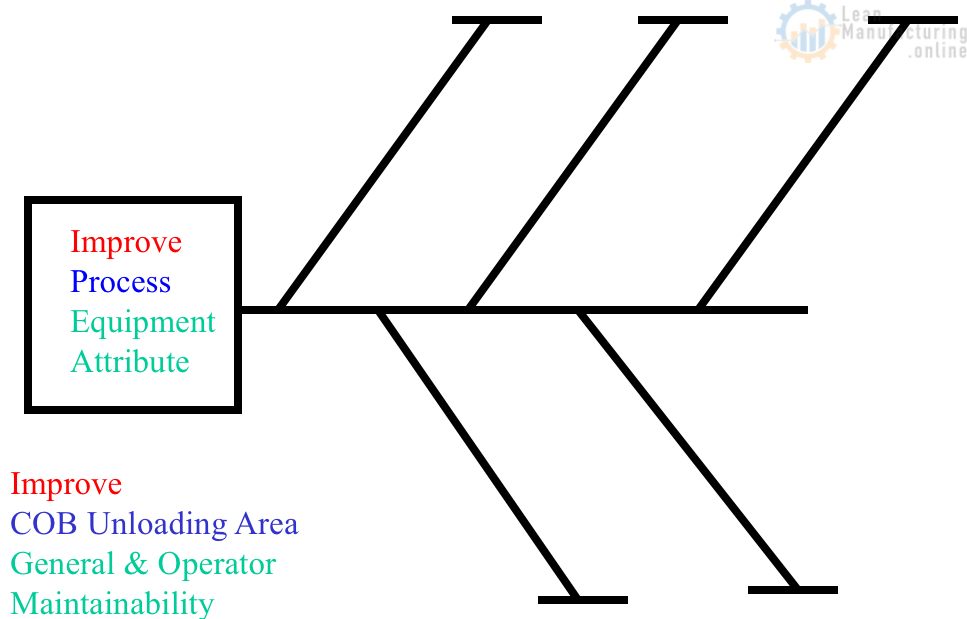
List Issues Into Categories
- Put a category on each branch of the fishbone and fill in the attributes of each category on the branch
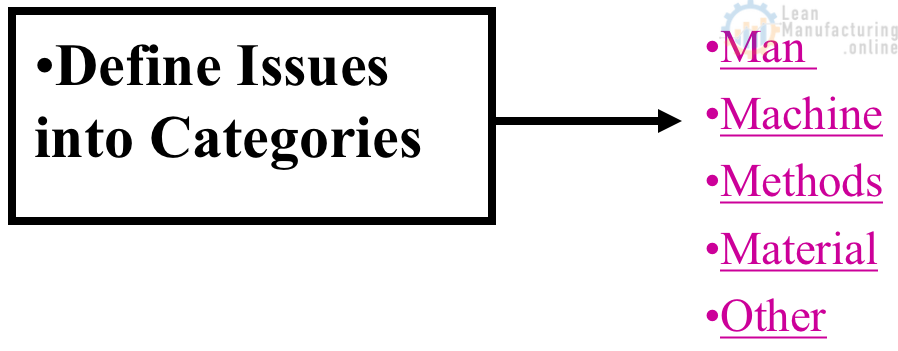
4M Fishbone Diagram
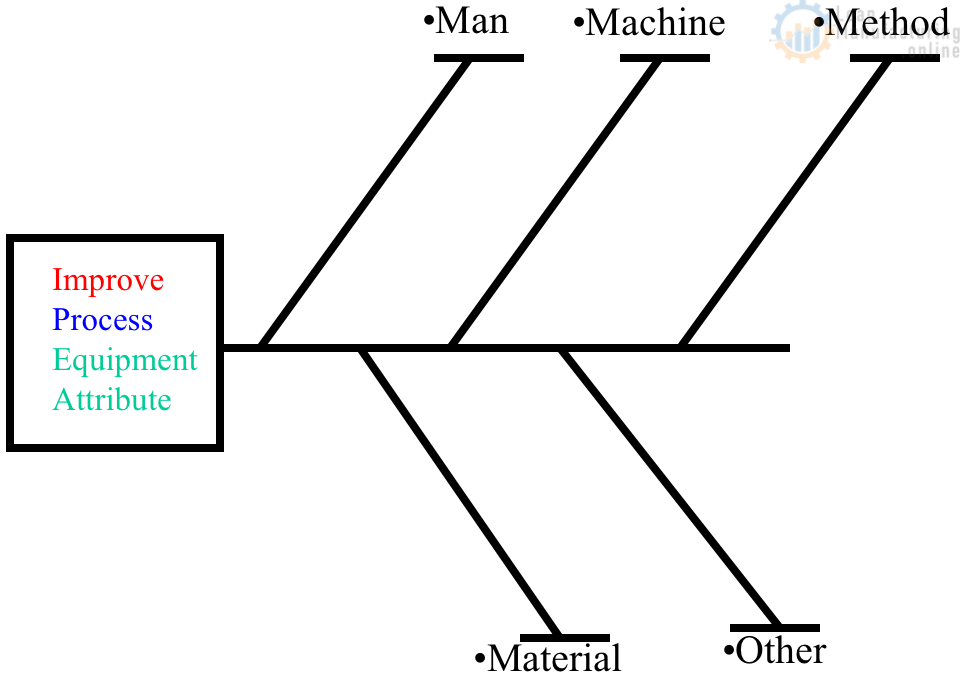
List Issues Into Categories
- Man
- Skill
- Technology
- Organization
- Resources
- Communications
- Machine
- Design
- Installation
- Supplier
- Methods
- Schedule
- Procedure
- Material
- Design
- Quality
- Other
- Budget
- Demand
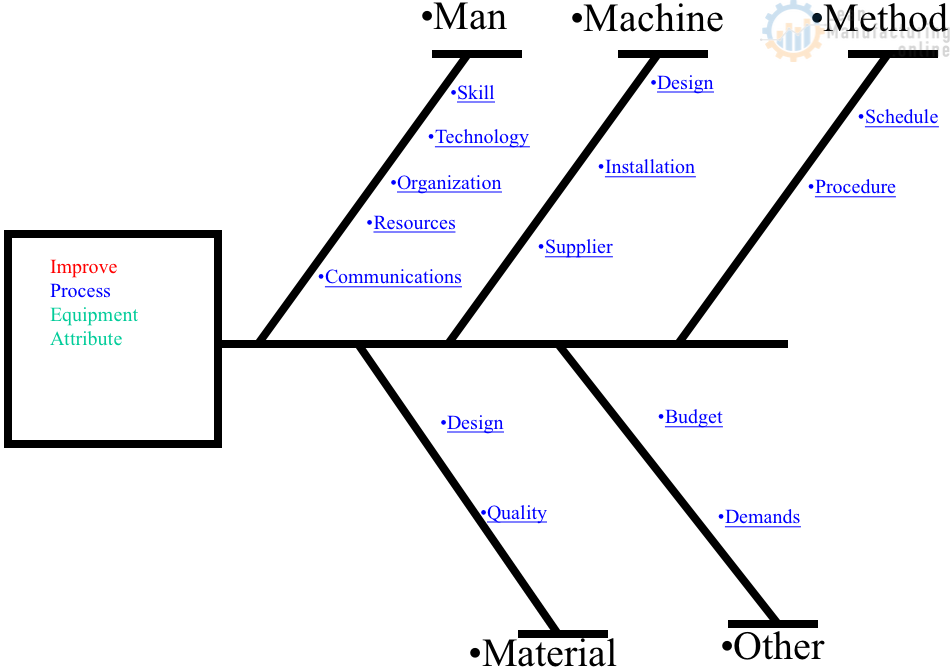
- Now the team asked the questions of each category: (Evaluating “Man & Skill”) How does “a person’s skill affect the process we are trying to improve”.
- After each question, all of the issues that arise are listed under that subcategory of the 4M
Capture & List Issues into Categories
Machine |
Design |
Visual access limited |
Easy access limited |
Maintainability limited (bearings) |
Installation |
Mounting brackets not clean design |
Conveyors stacked on top of one another |
Supplier |
Too much string |
Too many damaged cases |
4M Analysis Resolution of Issues

- Select Condition from list of Issues on the fishbone
- Example: “Design – Visual access limited”
- Select Proper Problem Solving Methodology
- Problem Solving Methodologies
- Autonomous Maintenance Process
- Standards
- Inspection, Cleaning & Lubrication
- Root Cause Analysis
- Cap Do Process
- 5S Checklist
- One Point Lesson Plans
- Re-engineering (MP Data)
- Project Safety Checklist
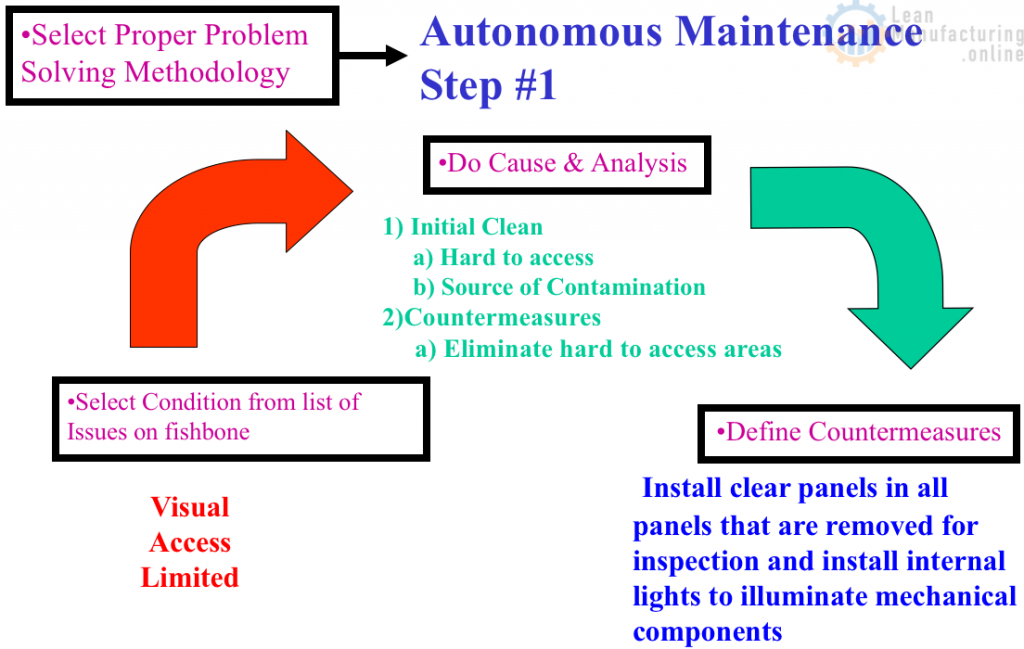
- Select Owner of Countermeasures
- Create work order to schedule work for trades
- Schedule Countermeasure Completion
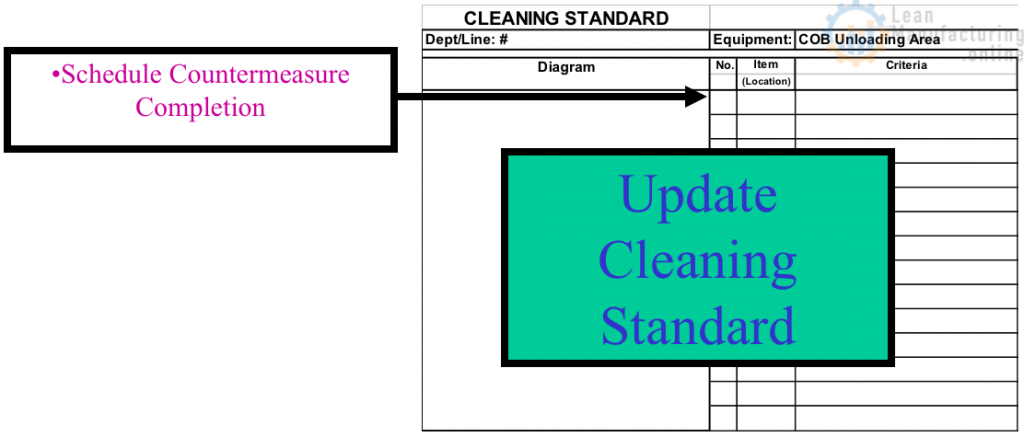
- 30 days after completion, evaluate countermeasure to ensure that all of the expectations, of the owners, have been met. If not, re-do cause and analysis.
kindly send news letter
Thanks for your interest in our Lean Manufacturing training materials. An email was just sent to confirm your subscription. Please find the email now and click ‘Confirm Follow’ to start subscribing.
Please send me How to write strategies of zero accident
Thanks for interest in our products. Can you please be more specific about your question, type of industry, what can of hazards your employees are exposed to, current methods of accident prevention etc.
Some of the answers can be found here: http://leanmanufacturing.online/safety-health-and-environment-tpm-pillar/
Hi
very useful information , my note is” we can use 5 whys Tool also to define root cause for ” Example: “Design – Visual access limited”.
Thanks.
kindly send a questionnaire on 4M change management min. 40 questions
Need help to understand 4 M change Analysis followed by Figure-8 analysis
Figure-of-eight method can be reviewed here: https://leanmanufacturing.online/the-figure-of-eight-method-basic-concepts-and-development-steps/
need help to understanding 4 M , for maintenance
Hi Mahfud,
Thank you for your interest in our products. Kindly let us know about the training requirements for your maintenance team, and we will be pleased to help you.
Can you help me to get details on “Know-Why Analysis” and “Why-OK Analysis” with example.
Hi Vilas, thanks for your interest in our blog. Here is a quick definition and samples of the requested:
Know-Why Analysis
Know-Why Analysis is an analytical method that leverages causality to understand the systemic nature of problems. It seeks to understand why a problem occurs, delving deep into the root cause instead of just dealing with symptoms. This analysis is a more comprehensive approach compared to other troubleshooting methods that might only address the symptoms of an issue, allowing the root cause to persist.
For instance, imagine a manufacturing facility that repeatedly faces a machine breakdown. The immediate response might be to repair or replace the machine. However, a Know-Why Analysis would investigate why the machine breaks down. The problem might be due to inadequate maintenance, improper operation, or an outdated machine model incapable of handling current demands. By understanding the root cause, the organization can implement a more effective solution, such as improving maintenance procedures, training operators better, or updating machinery to modern standards.
Why-OK Analysis
Why-OK Analysis, on the other hand, is a problem-solving approach that investigates why things are working correctly. It identifies the conditions and actions that lead to the desired outcome, making it a valuable tool for optimizing and improving processes.
For example, suppose a software development team has been particularly successful in delivering high-quality code on time. A Why-OK Analysis would investigate the factors contributing to this success. It could be that the team has a strong communication culture, they use an efficient project management tool, or their testing procedures are robust. Understanding these factors allows an organization to replicate the successful conditions in other teams or projects, leading to overall improvement.
Hope it helps!
sorry late to replay ,
I’m still learning and reading your product, your product is good. what I’m asking is, what is the best first step to accomplish the PM goals and maintenance KPI.this is my first program to do PM
I want to understand how to analyze process for improvement and choose the best solution. with example–
It was really helpful and easy understanding content, I would like to know more about problem solving tools.