In any company, nothing will happen unless its departmental and area managers make it happen, and the Autonomous Maintenance program must likewise be led from the front. In fact, the success or failure of the program depends entirely on the leadership shown by managers. The rollout should start with a pilot machine on which managers learn the essentials of each step by carrying it out themselves. A successful rollout requires managers who clearly understand what Autonomous Maintenance is about, and can provide effective guidance and training to everyone working under them. As mentioned before, when it is the turn of the line teams to start doing Autonomous Maintenance, it helps to use a “horizontal rollout” strategy, completing an activity on one machine before progressing to the others, rather than starting on all machines at once.
Take it one step at a time
Trying to do too many things at once is a recipe for failure – something that will be all too familiar to many managers. Therefore, it makes sense to prioritize the tasks and focus on a few things at a time, and Autonomous Maintenance is no exception to this rule. For a successful rollout, set attainable targets, and don’t try to run before you can walk. The Autonomous Maintenance program is divided up into a preparation phase and seven distinct steps for good reason. Make sure each step is thoroughly mastered, and the required level really has been reached, before the next step is embarked on. Each step then becomes a milestone that people can aim for. They feel a sense of achievement when they pass, building their confidence and giving them the energy and enthusiasm required for taking the next step.
Review every step
Each time a step is completed, management and staff should carry out a lineside review to judge whether the team has attained a satisfactory level. They should use the review process as an opportunity for team coaching. At each step in the program, it is essential to remind everyone of their objectives and give them additional guidance to upgrade their workplace management skills. Managers have to do far more than just pointing out the problems and leaving the rest up to the teams.
Use relay teaching
Autonomous Maintenance requires everyone to master new knowledge and skills, so training is a crucial part of the process. Training has to be handled in a flexible, creative way because different levels of knowledge and skill are expected of people at different levels, and the relay teaching system (where training is cascaded down by having team leaders and members teach their colleagues) was devised to meet this need.
Relay teaching is based on the philosophy of learning through teaching and is suitable for various training scenarios, not only those relating to Autonomous Maintenance. Team leaders receive basic instruction, and then prepare one-point lessons (see Figure “Typical One Point Lessons”) and other training aids to help them pass on what they have learned to the operators in their teams. The beauty of this system is that, in order to explain it to their teams, the team leaders have to understand the subject matter fully themselves.
One point lessons must be easy to understand, and designed to fulfill a particular objective. They can generally be divided into the following four categories:
(1) Safety
This type of lesson is used to make sure all activities are performed safely.
(2) Basic knowledge
This type of lesson is used to fill in gaps in the operators’ knowledge, by checking that they really know what they need to know.
(3) Improvement
This type of lesson is used for the horizontal rollout of successful improvements, looking at the approach and practical methods used, and the benefits obtained. The focus in on tackling the root causes of problems.
(4) Troubleshooting
This type of lesson is designed to prevent problems from occurring twice, by identifying the shortcomings in knowledge and skills that have allowed a problem to arise.
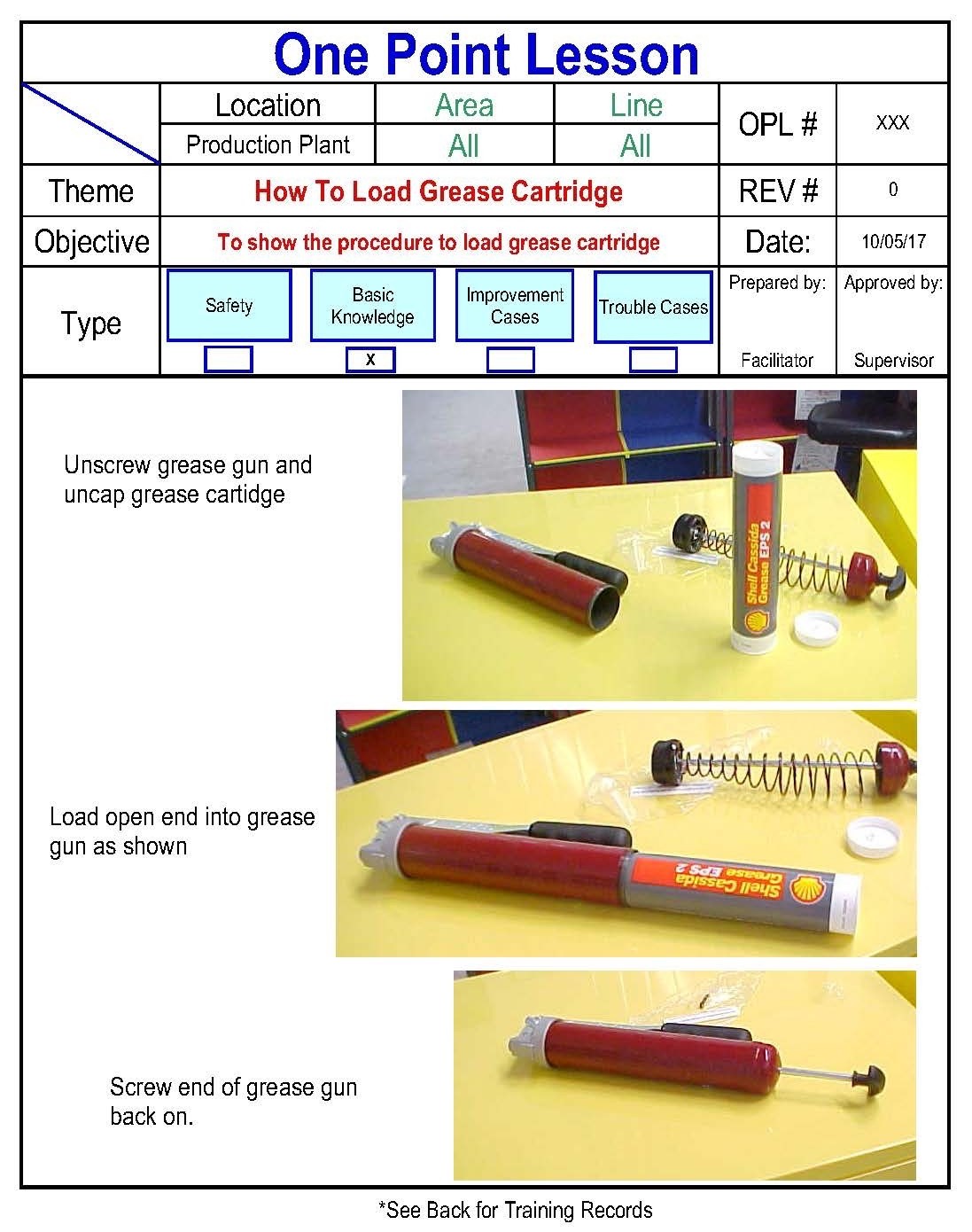