This case study shows the progress of the Planned Maintenance Pillar of a food manufacturing facility.
The facility is located in North America.
Situation Before TPM
Analysis of the situation was done using 4M methodology:
Man
- Low level of skills
- People with high stress
- Low spirit of work team
- Lack of trust and cooperation between maintenance and production
Machine
- A large number of breakdowns
- High level of deterioration and abnormalities
Method
- Lack of data tracking
- Lack of maintenance plan
- Lack of cost control
Material
- No proper tools for repairs
- No spare parts are available in the warehouse
Pillar Vision, Mission and Targets
Vision
To be recognized as the best supplier of services in the company, guarantee the highest level of reliability, safety, quality, and maintenance costs of the assets.
Mission
By using planned maintenance techniques, we will add value to manufacturing activities with a professional team, raising the reliability and productivity of the assets, always with a positive attitude.
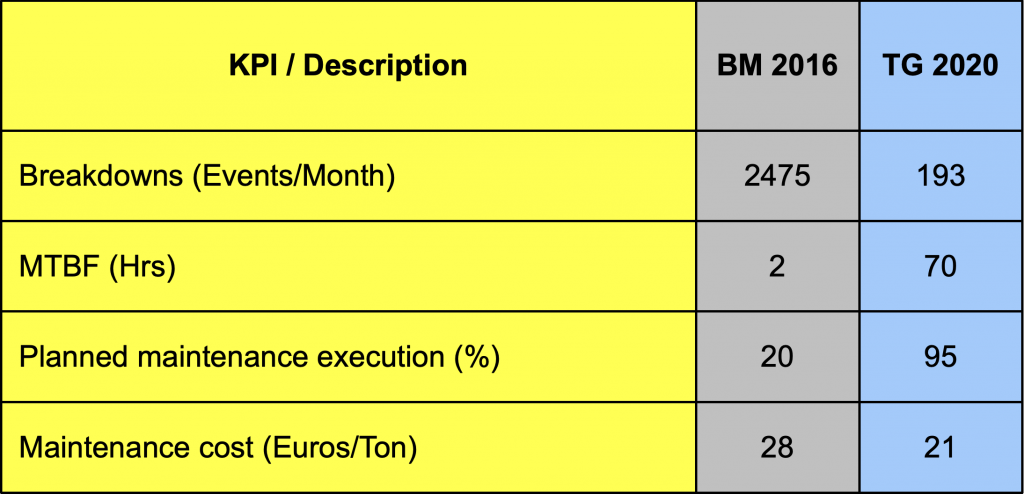
Pillar Organization
This team is responsible for implementing the Planned Maintenance Pillar in the Manufacturing Plant.
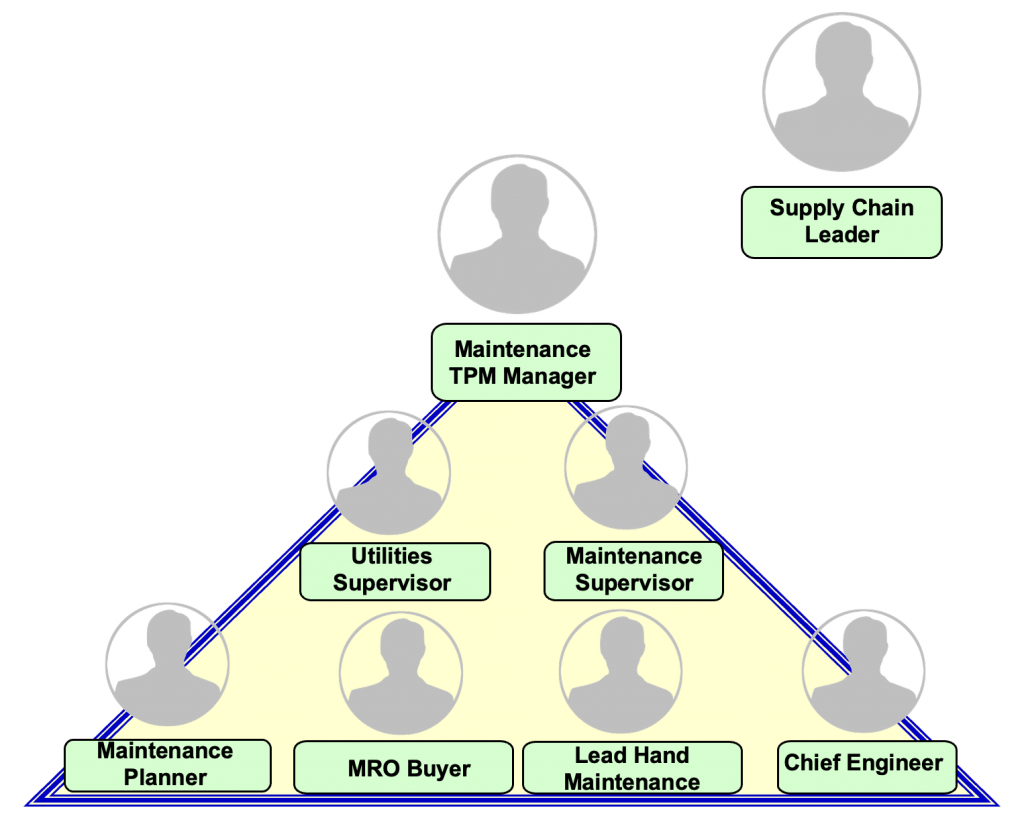
Master Plan
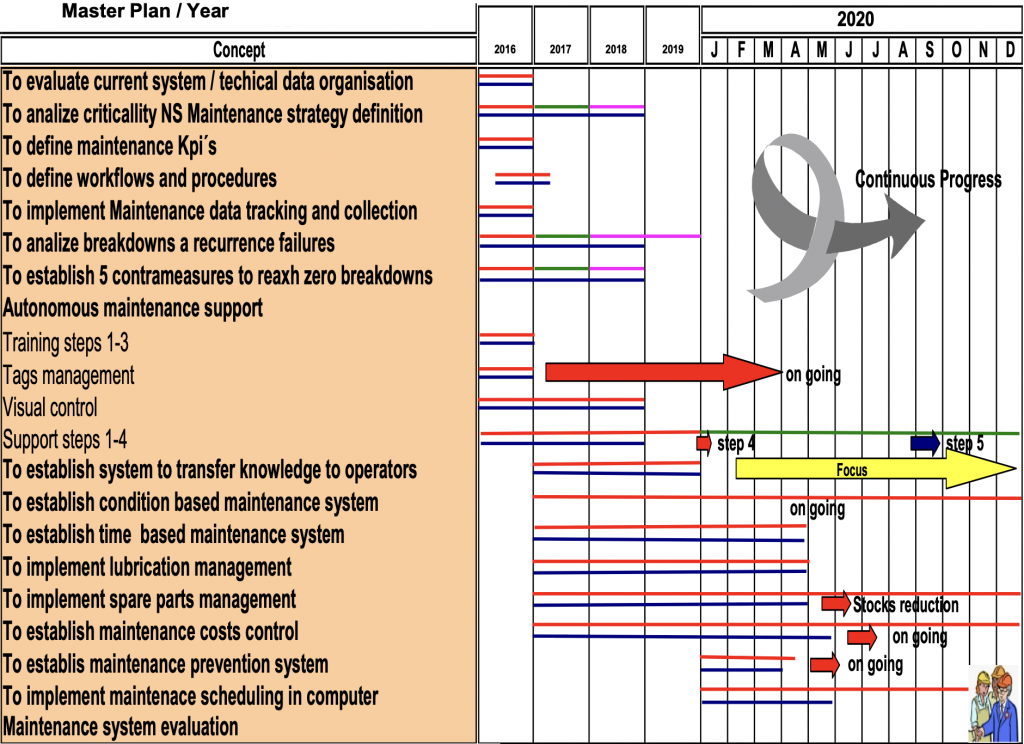
📚 From the book “Maintenance Planning and Scheduling Handbook” by Doc Palmer:
“Planned maintenance helps organizations reduce equipment breakdowns, minimize downtime, and increase productivity by proactively addressing potential issues.”
Maintenance Key Activities
We developed a framework to orient our key activities with an integral maintenance vision to meet business needs and manufacturing requirements.
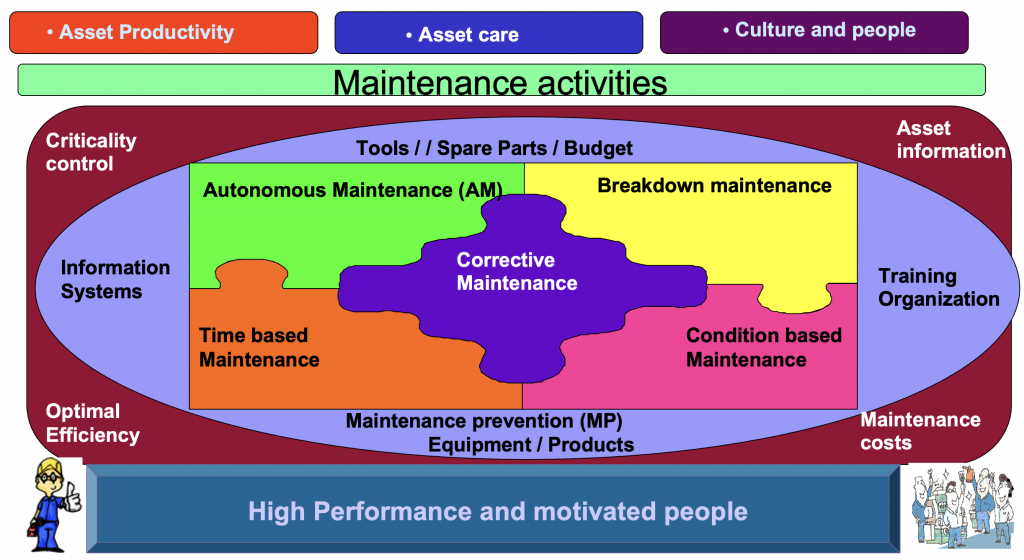
It was necessary to incorporate the maintenance concepts into practical activities, making our TPM methodology applications reach zero breakdowns and cost reduction.

Risk-Based Equipment Life Assessment
This assessment allowed us to focus on critical equipment and defining a maintenance strategy. We found out that the breakdowns significantly wasted time and money in the utility area and aseptic plant.
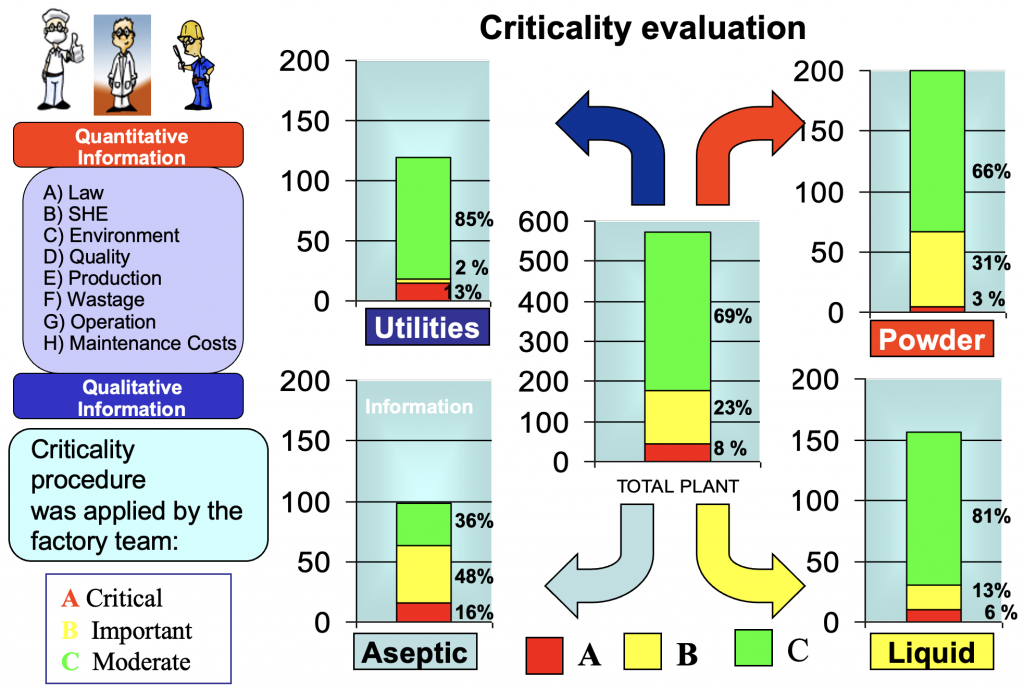
Criticality analysis allows us to have an inventory of all equipment in the plant and orients us to define the type of maintenance required by each one.
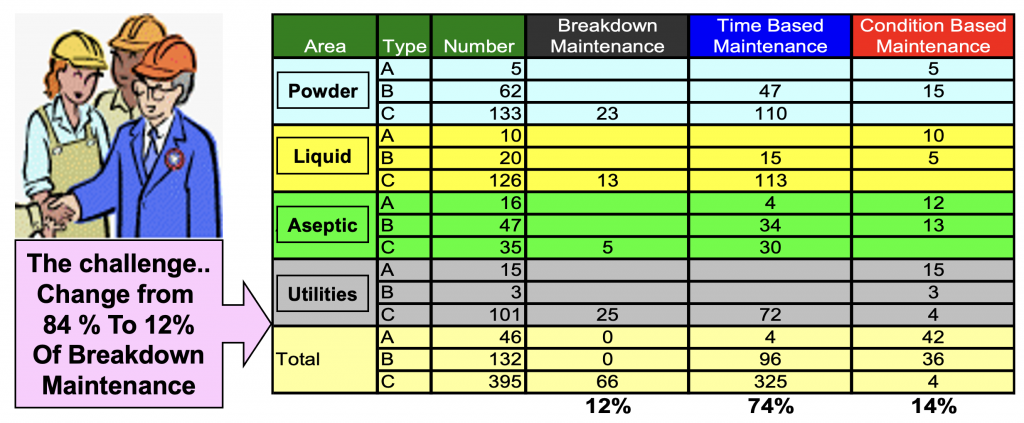
Autonomous Maintenance Support
Red Tags Management
In 2016, we started using red tags to identify and solve abnormalities; because of the machines’ high level of deterioration, “Red Tag” became the language between production and maintenance areas.

We detected that the maintenance personnel generated significant work to support the autonomous maintenance. Often, solved red tags never benefited the OEE, creating disappointment and a lack of motivation for technicians and operators. We designed and implemented a system that allowed us to set priorities and reflect the benefit of the efficiency of the equipment.
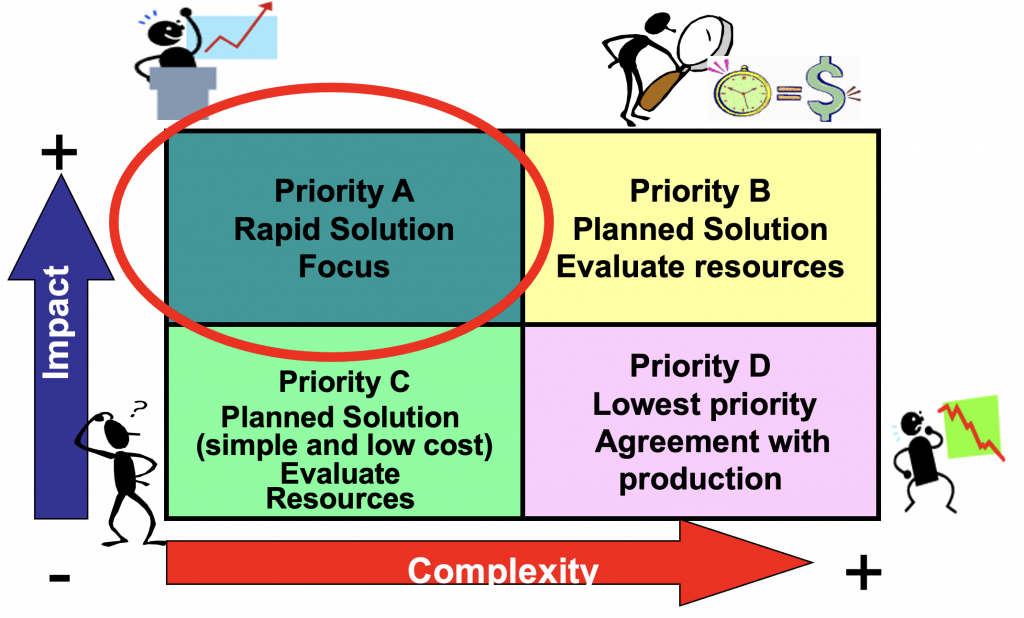
Red Tags vs Breakdown
The high level of abnormalities in the three departments (plants), Powder, Aseptic, and Liquid, required a significant effort to support Autonomous Maintenance activities. Training the operators to identify abnormalities and make the proper restorations in the equipment was necessary. One point lessons and red tags were the vehicles.

Identifying the nature of the red tags to guide the training was essential, which was the key to reducing abnormalities. The focus was on Mechanical issues.
Autonomous Maintenance Support in Action
The activities in the Powder Plant were focused on restoring mechanical and electrical abnormalities, which were the leading causes of breakdowns in equipment.
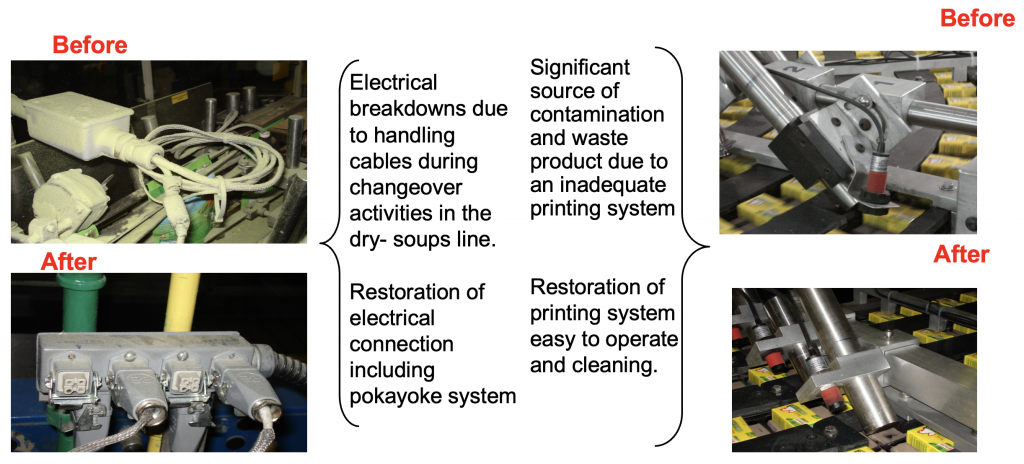
In an Aseptic plant, water leakage is one of the most critical sources of contamination, wastewater, and safety risk.
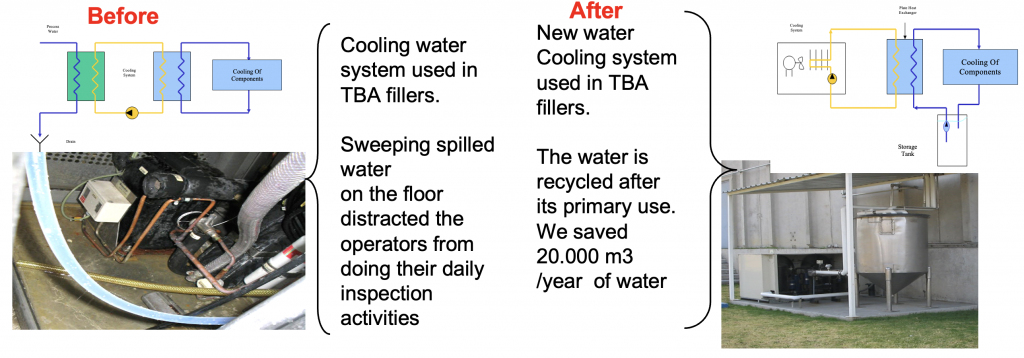
The high level of dust and difficult access areas were the focus during the autonomous maintenance support in the Liquid Plant.
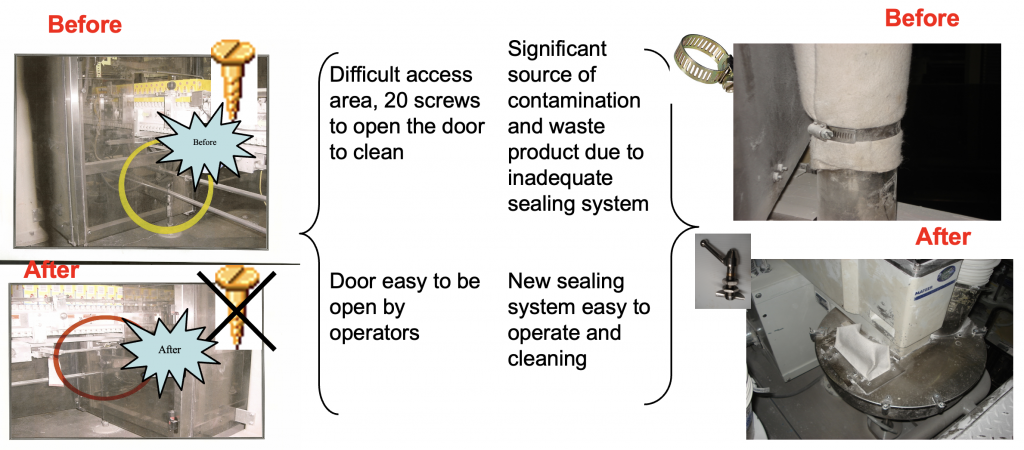
From 2017, to support autonomous maintenance and maintain correct operation by operators, it was necessary to help them develop the provisional standards, making the job easier for them. Over 6,548 points were transferred.
Due to the number of machines and the characteristics of the Powder and Liquid Plants facilities, they were favoured with this type of activity.
The following graphics show the effectiveness of the relationship between operators and technicians. More points translated to autonomous maintenance, more minor breakdowns in the equipment and better MTBF. It’s a great combination.
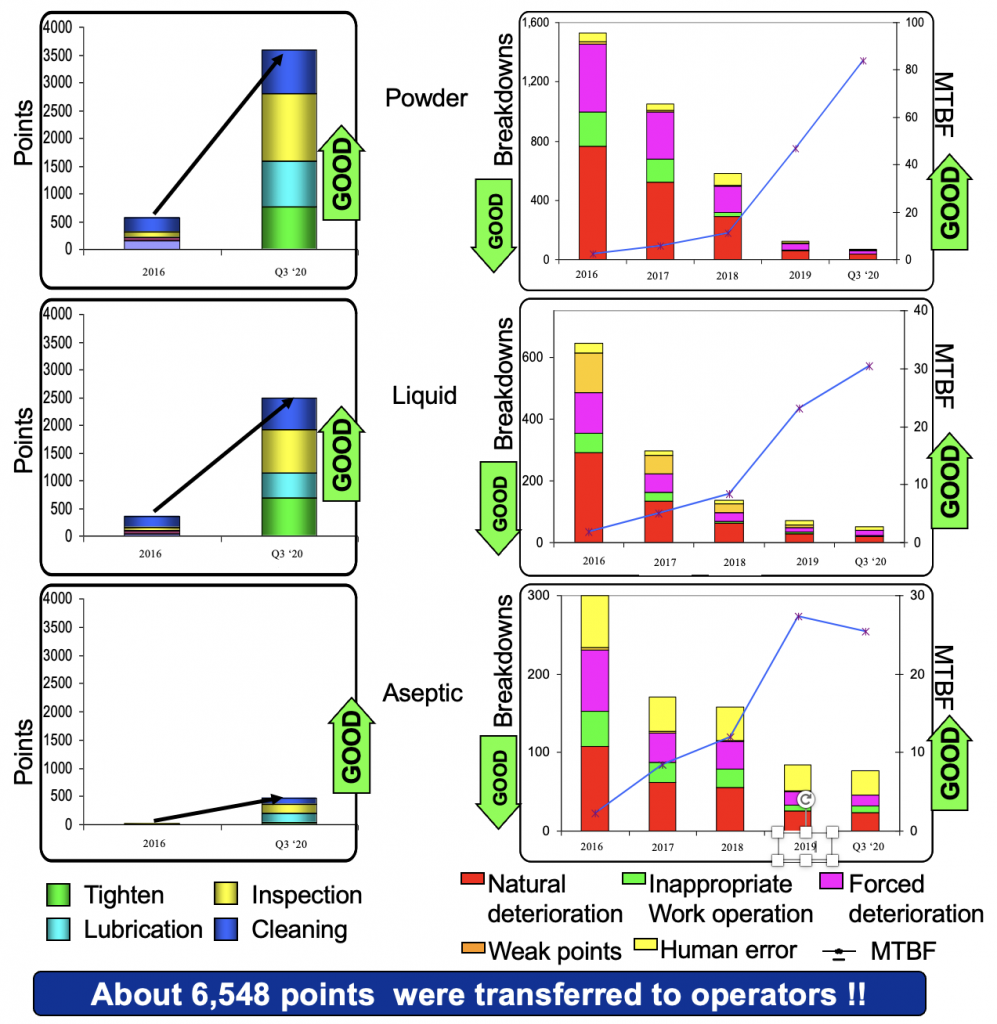
Lubrication. Powder Plant Example
Lubrication activity control was one of the most critical issues in improving our overall operational efficiency. Many breakdowns were related to inappropriate lubrication practices since maintenance people could not cover all the lubrication points effectively. Because of the characteristics of the plant, Powder was the most affected plant in this issue.
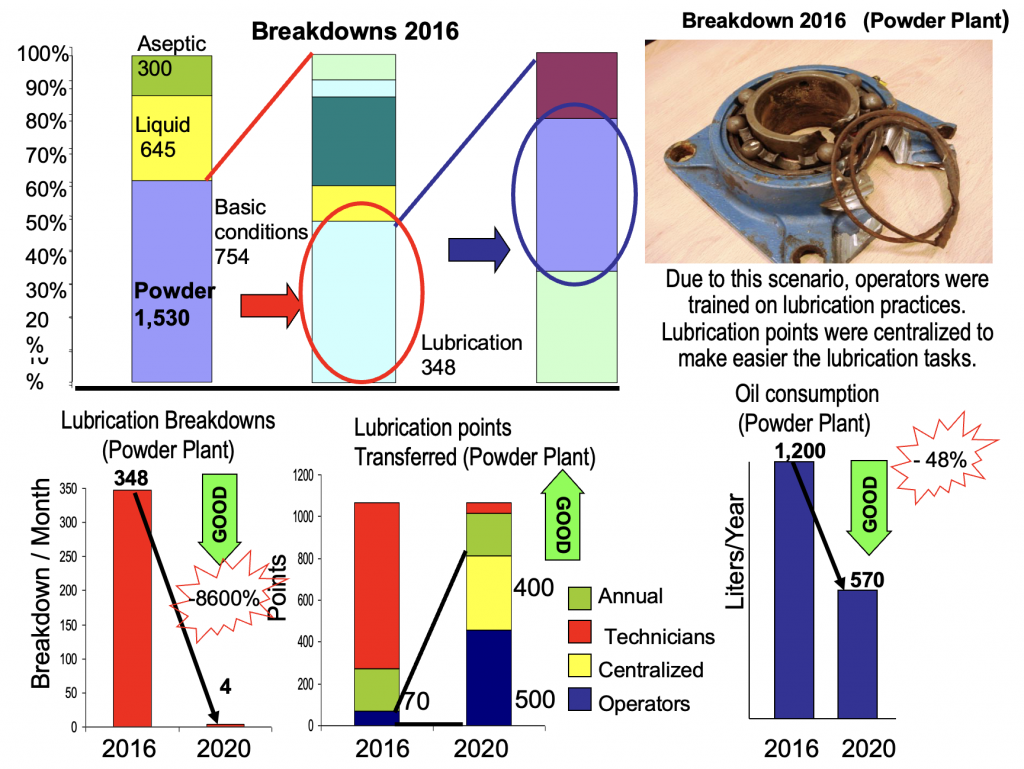
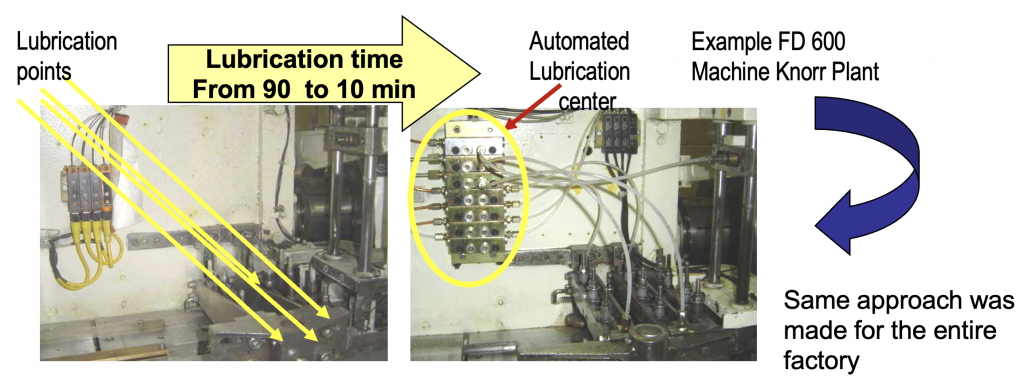
Training to Support Autonomous Maintenance Step 4
It was necessary to improve the operator’s knowledge to continue with breakdown reduction. Operators learn about basic principles concerning mechanisms and incorporate them into their standards.


Zero breakdown orientation
Simultaneously, with the support of autonomous maintenance, we implemented the analysis of breakdowns to reduce them and ensure that the most critical ones were deeply analyzed to find their root causes and eliminate them. The recurrence and severity aspects were considered.
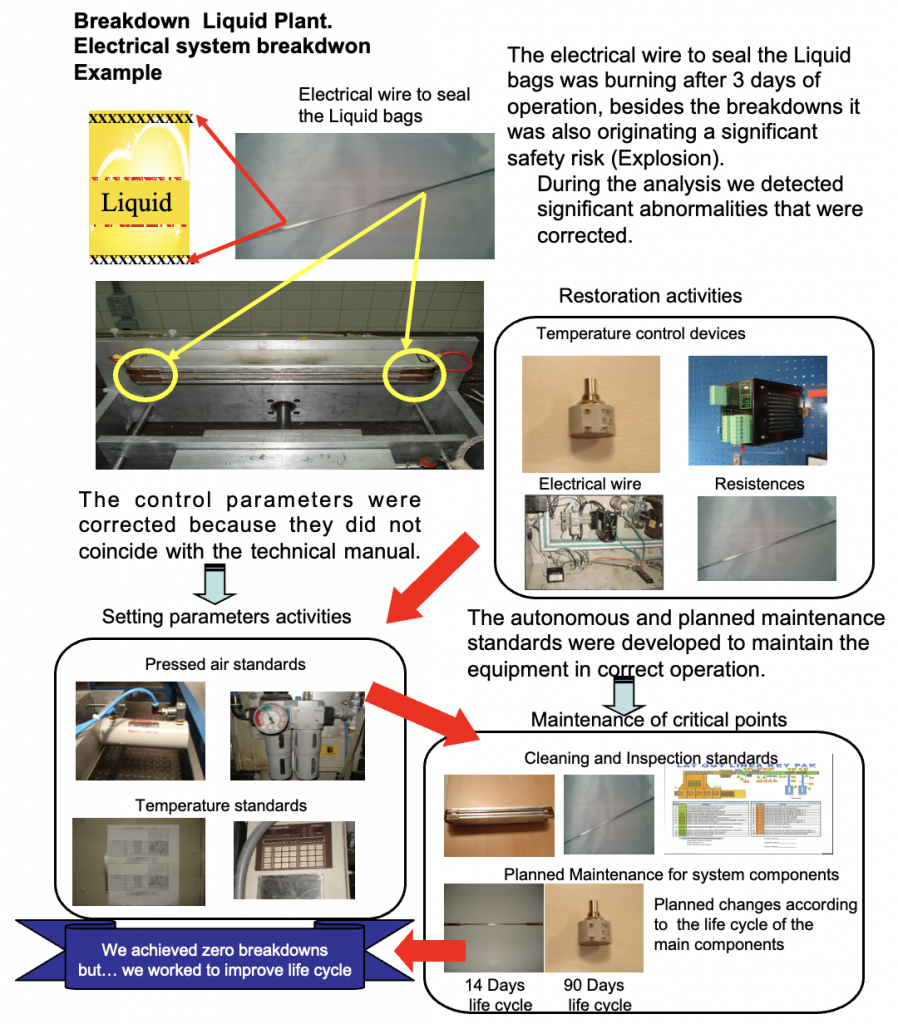
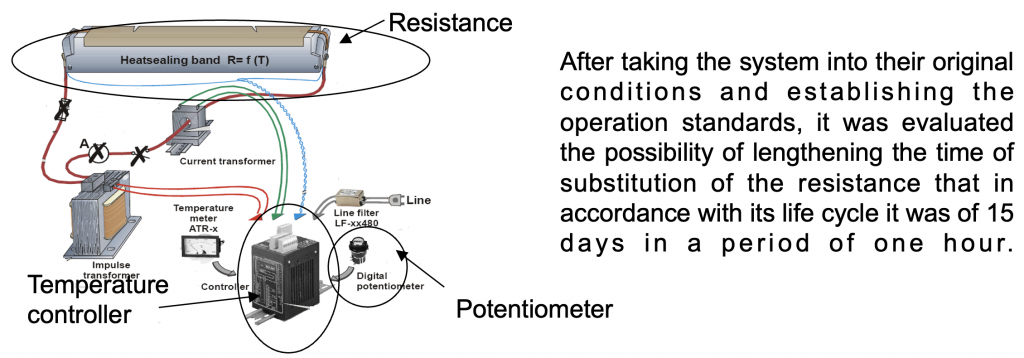
We analyzed the following components:
Resistance: is made of nichrome and loses resistance properties through time (more amperage that it needs). Potentiometer: allows the temperature controller to send the pulses. It is made of a coal track, and with its use, it suffers natural wear.
Temperature Controller: it can constantly work vertically sealed and eliminates risks. The analysis let us know the importance of working continuously or by pulses. The system was redesigned, and some components were eliminated. This improvement that was carried out in the sealing system will be commented on the shop floor.
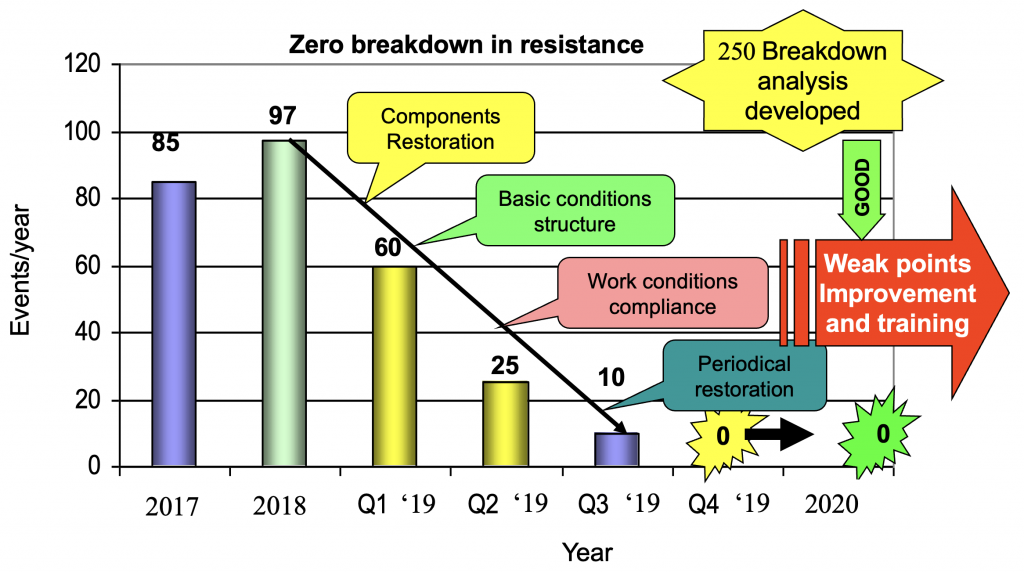
Time-Based maintenance
We had many breakdowns when we started, and the maintenance was focused on acting until the breakdown appeared. This practice had catastrophic effects when it affected critical equipment, that it was one of the major causes, we began the planned maintenance, based on time in its first stage, and we were supplementing it with maintenance based on conditions, progressively.
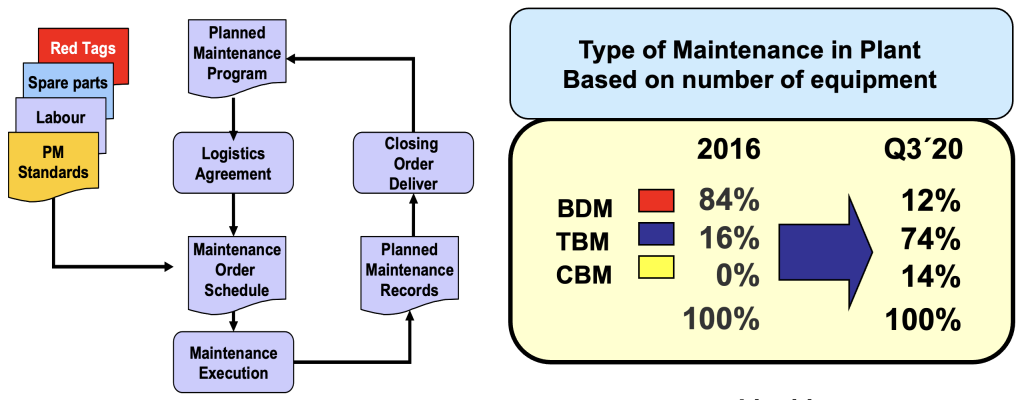
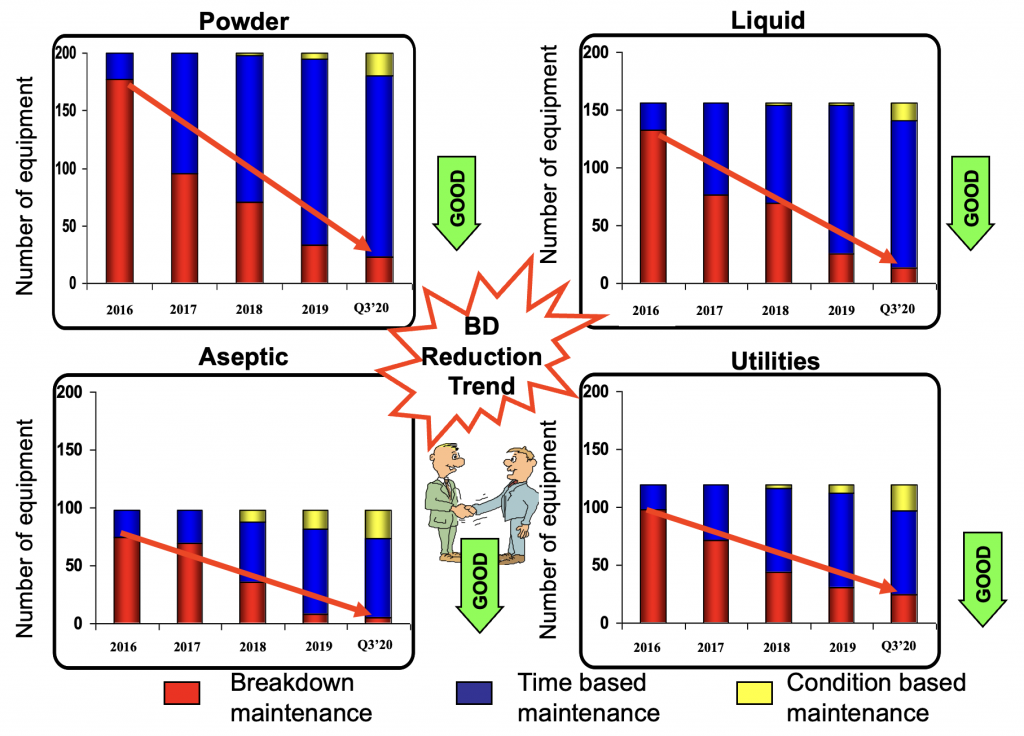
Condition-Based Maintenance
We are applying CBM tools to improve the reliability of critical equipment, and serious breakdowns were avoided due to this practical methodology.
Example: Vibration analysis in Soya Miller. (Very critical equipment)
- The criticality matrix indicates the type of equipment and type of maintenance
- Applicable predictive techniques to equipment that in this case are – vibration analysis and electrical tests
- The corresponding measurements are performed according to the maintenance plan
- Evaluate the conditions of the equipment’s components in order to gain an advantage about their maximum working life by means of a root causes analysis, concerning failures
- Failures were reduced from six to zero, by means of the condition-based maintenance study results
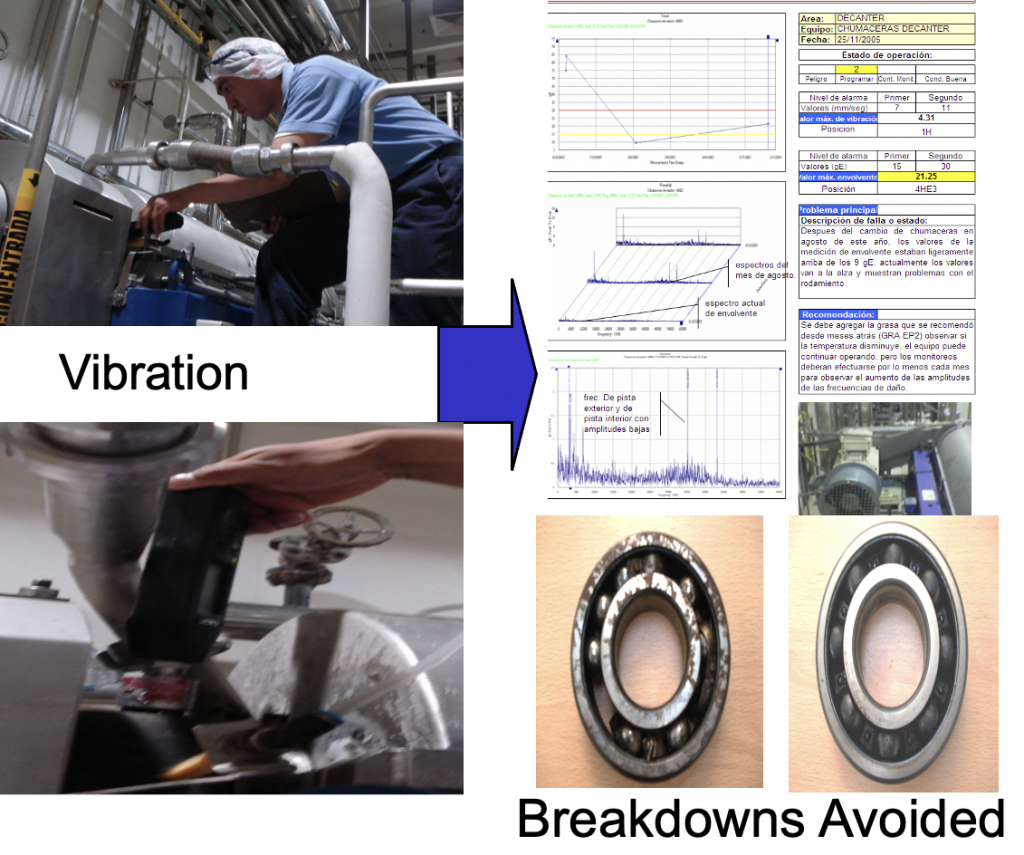
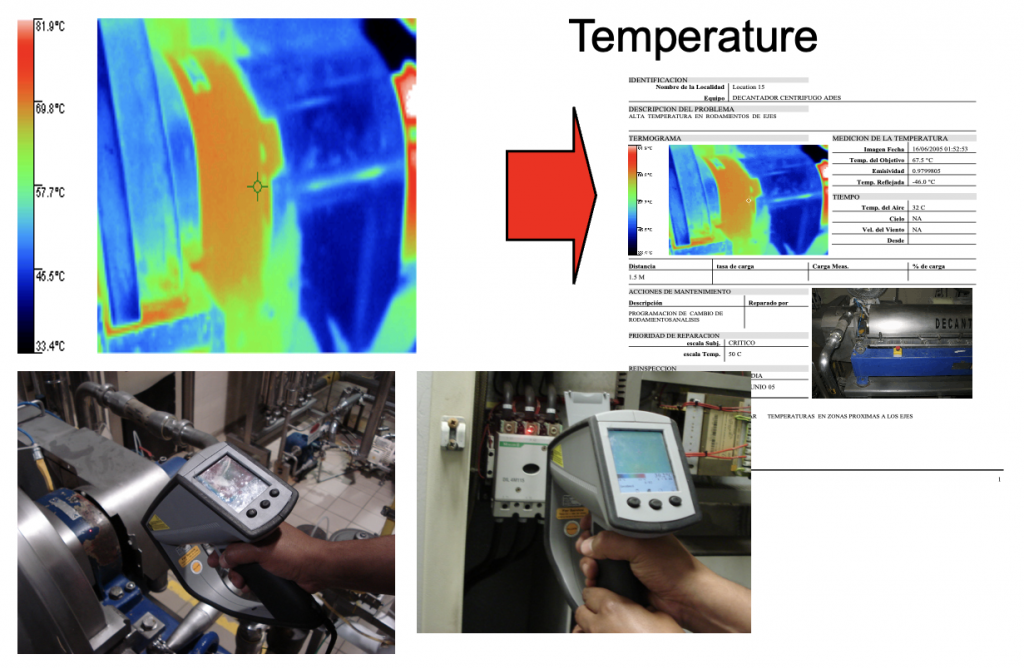
Corrective Maintenance
Another essential part of our frame developed was Corrective Maintenance activities; in spite of compliance with our basic standards, weak points of our critical equipment were analyzed and solved through technical improvements to avoid breakdowns and raise the cycle life of the components.


There were two options to solve our problem; one was to change the diameters of the blue and red gear to raise their torque or reduce the system’s RPM. In addition, a different device was installed to improve the lubrication method and avoid the source of contamination.
With this new arrangement, we could reduce from 890 to 0 of the breakdowns.
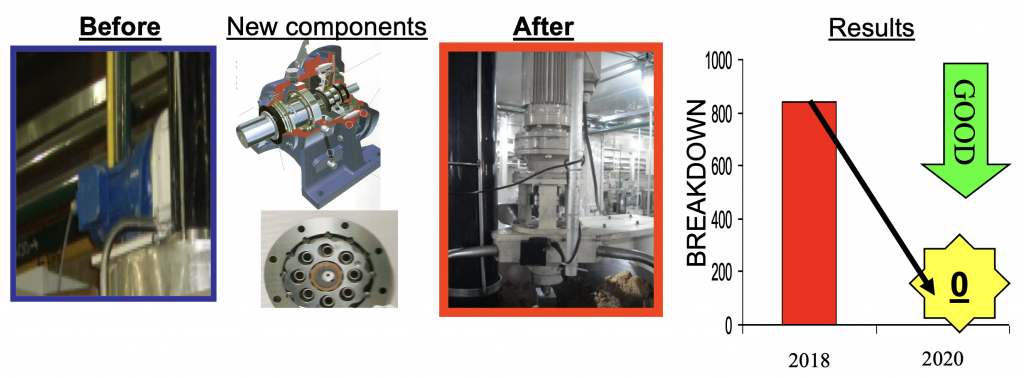
Taking advantage of the concept of Karakuri, during 2020, we started to implement systems that help us to make our operation easier and improve the usage of energy available in the current systems.
Karakuri Kaizen
The product was transferred to another direction by a pneumatic piston. With minor arrangements, we can use gravity to do the same task.

The product was transferred to a blue belt (Check-weigher) by another previous belt (black). With the proposal, we eliminate the black belt, and the product is pushed by another product to the belt blue (Check-weigher).
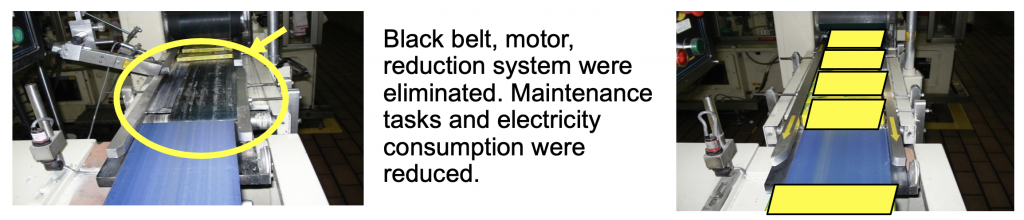
The operator handled the product to put it into the box. We4M eliminated a human motion to handle the product without additional energy with the proposal.
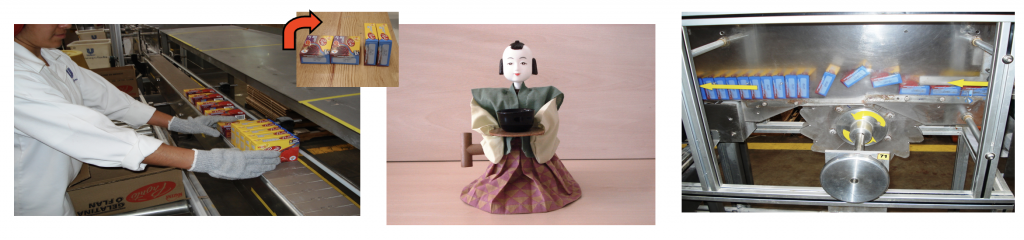
Maintenance Budget
We improved our maintenance budget control in each area according to our expectations. This classification allowed us to orient our decision, considering the management of spare parts, maintenance and cost-effectiveness.
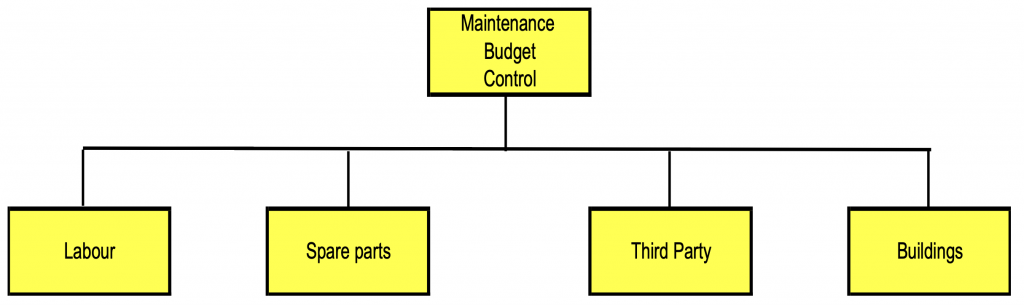
Maintenance Budget Type
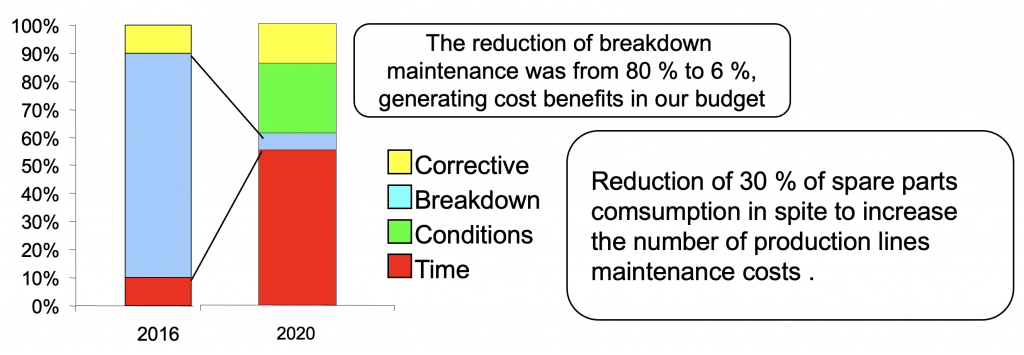
Maintenance Budget Concept
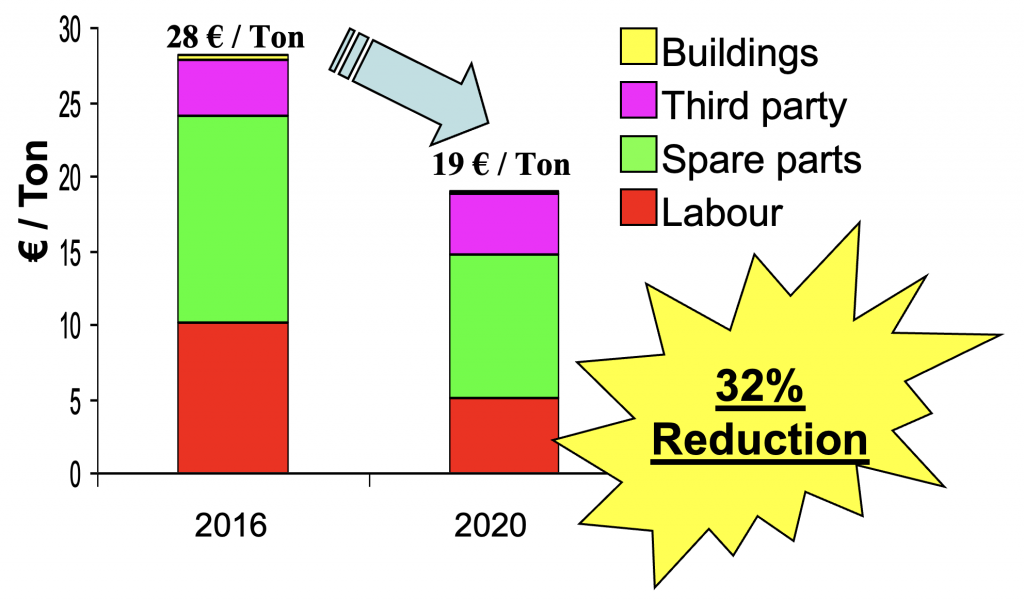
Spare Parts
We implemented an effective plan to reduce spare part costs by changing the external suppliers sourcing to local suppliers sourcing; besides this, a reconstruction process of spare parts was Implemented so that it allows us to improve spare parts control.
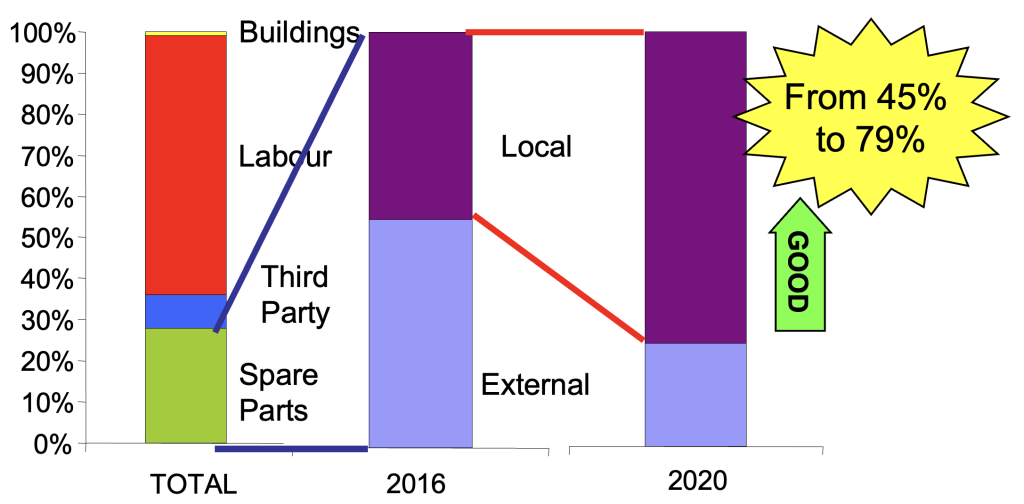
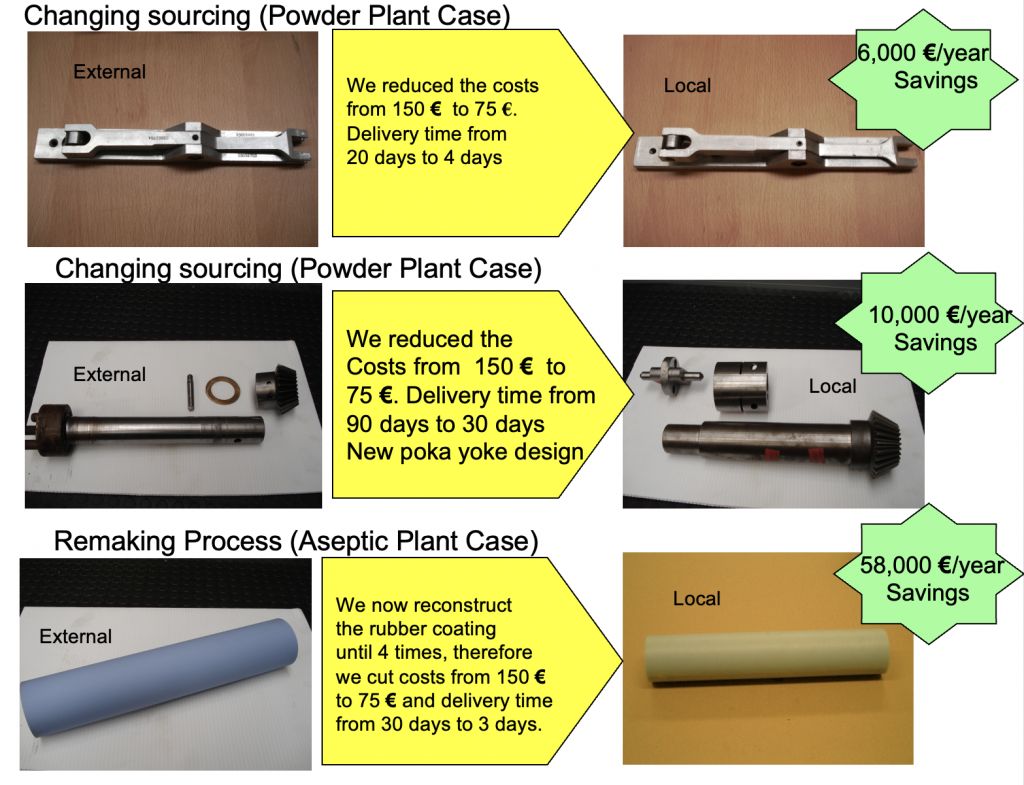
Results


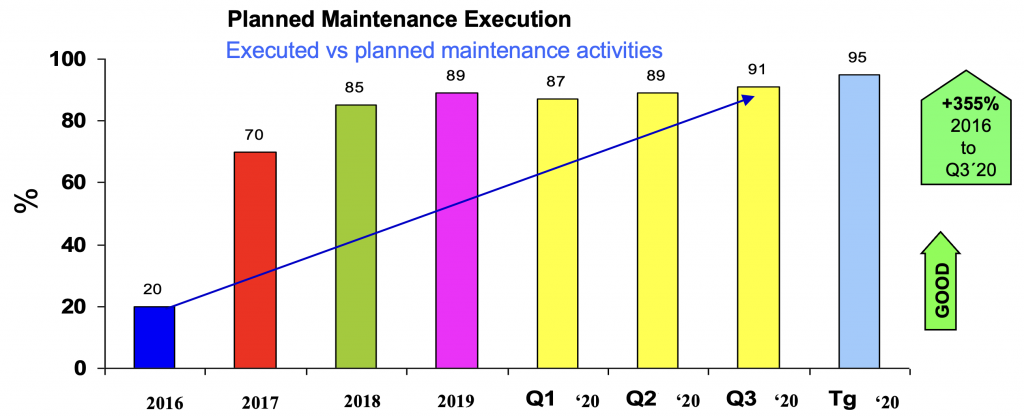

Next steps
- Implement MTTR monitoring system
- Support the Chokotei’s reduction in factory widely
- Raise the skills and competence of technicians continuously
- Increase the usage of predictive techniques
- Implement Planned Maintenance Activities in Management System
- Implement RCM
📚 From the book “Reliability-Centered Maintenance” by John Moubray:
“Planned maintenance plays a crucial role in maintaining and enhancing equipment reliability, which directly impacts the bottom line of any organization.”
The case study of the food processing plant demonstrates the immense benefits of implementing a planned maintenance approach in an industrial setting. By proactively addressing potential issues, the plant was able to significantly reduce equipment breakdowns, improve overall equipment effectiveness (OEE), and optimize resource allocation. Moreover, proper training and engagement in the planning process enhanced employee morale and skillsets.