(1) Prioritizing the equipment
Each factory should determine its own machines’ priorities, depending on their effect on the factory’s overall production (volume and quality) and factors such as how much damage the machines would sustain if they broke down.
Generally speaking, machines are assessed in terms of the following six aspects, with each aspect being scored and the total score determining whether the equipment is ranked AA, A, B, or C. The appropriate maintenance system is then selected in accordance with this priority ranking.
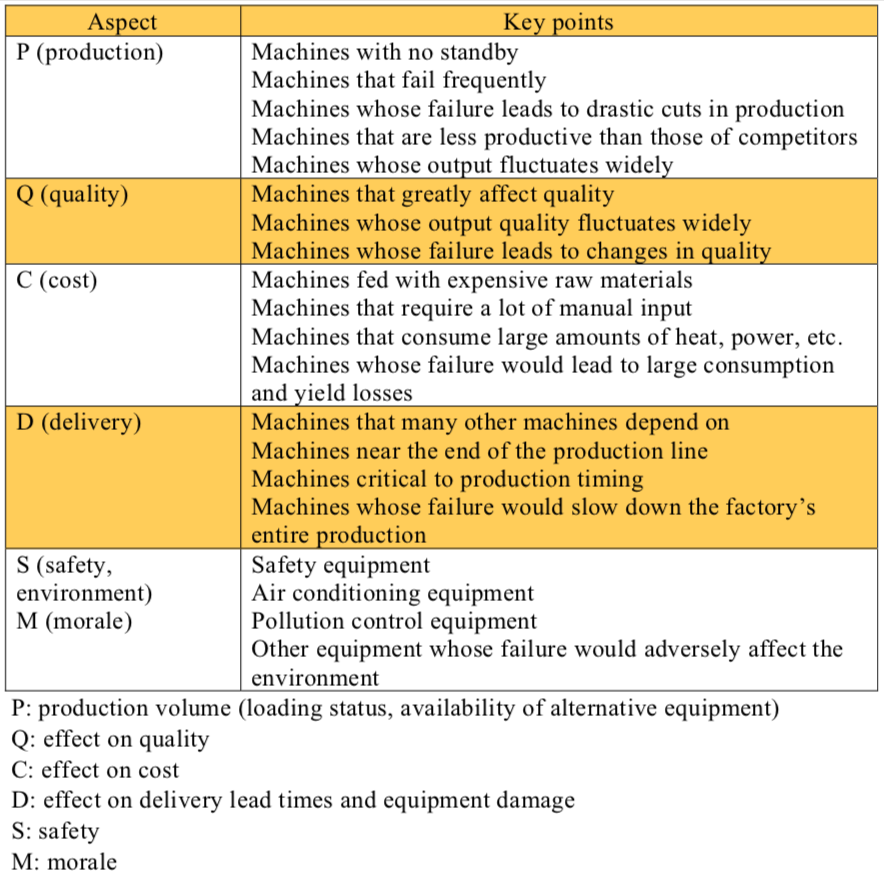
Although, as shown in the table, there are various practical ways of evaluating equipment, the ultimate decision depends on the company’s business judgment, and there is little point in pedantically insisting on a ranking system based on scoring alone. As a guideline, the percentage of equipment within each rank should be in the region of 5-7% for AA, 25% down to A, 60% down to B, and the rest C.
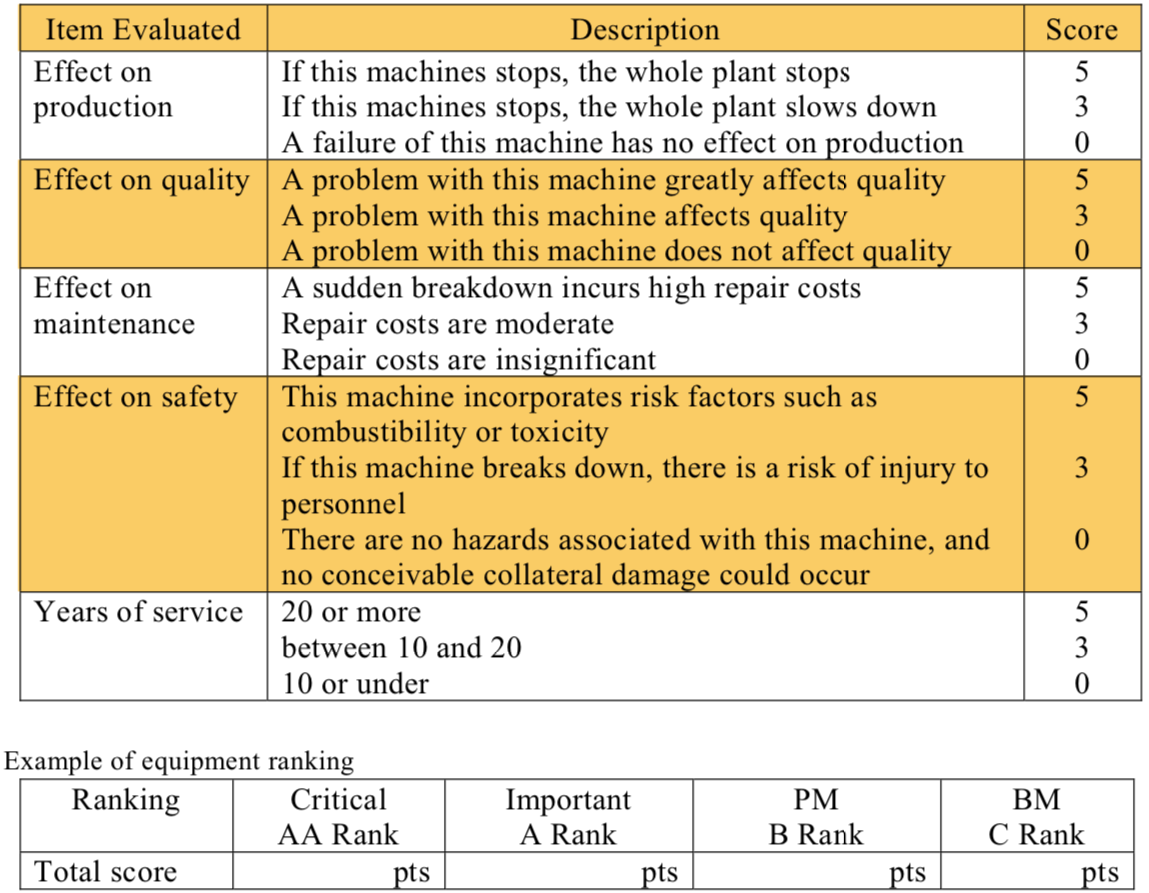
The appropriate maintenance system should then be selected for each rank, as illustrated below:
AA: Top-level CBM system (monitoring equipment permanently installed)
A: Intermediate CBM system (periodic simple and precision diagnosis)
B: Time-based preventive maintenance system (TBM)
C: Breakdown maintenance system (BM)
Most companies generally follow the above procedure when selecting their maintenance systems.
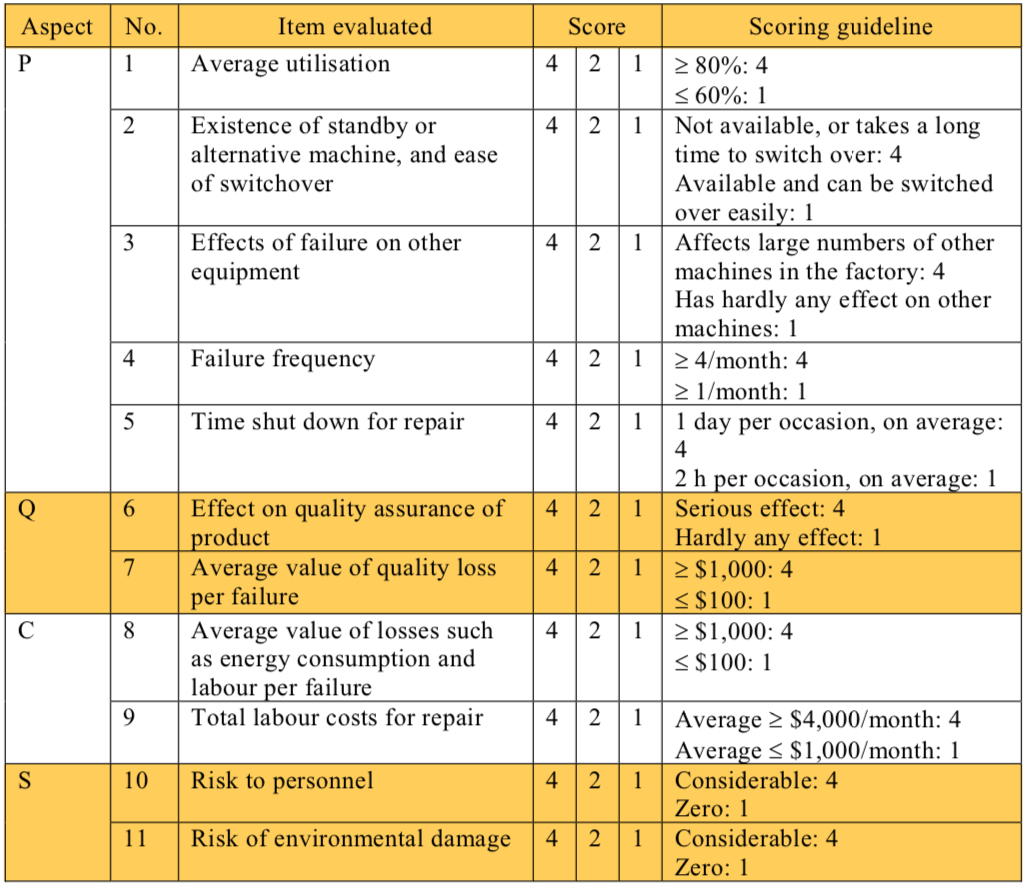
Notes:
- Refer to the guidelines when scoring each item
- Use only the scores printed in the scoring columns
- The total score determines the ranking (A, B, or C)
- Ultimately, top-priority equipment is marked A, medium-priority equipment is marked B, and low-priority equipment is marked C.
(2) Selecting the maintenance system
Once the equipment and the parts to be maintained have been prioritized, the maintenance system to be applied to the equipment within each rank must be decided. The parts to be maintained should ideally be identified at the design and fabrication stages by using techniques such as FMEA and FTA. In practice, however, they are usually identified through the experience of repairing many breakdowns while the equipment is in use.
When deciding which maintenance system to use, the two principal factors described below must be taken into account:
- The equipment’s priority
- The causes of the equipment’s deterioration.
As well as determining the causes of deterioration, it is also important to establish whether or not the speed with which the machine deteriorates is proportional to a parameter such as time, production volume, number of strokes, etc. If a proportional relationship exists, time-based maintenance can be used; if not, condition-based maintenance or periodic overhaul must be used. In practice, the above two factors are considered together when deciding on the maintenance system.
A general approach to selecting the maintenance system is outlined below
1 Is the service life between one overhaul and the next guaranteed?
If the service life can be relied on, the machine can be periodically overhauled at appropriate intervals, as long as it is operated under conditions of zero forced deterioration.
2 If the lifetime is not guaranteed, have any causes of forced deterioration been left untreated?
This means verifying whether or not the equipment is being properly managed on a daily basis. If any causes of forced deterioration have been overlooked, go back to basics and eliminate them.
3 If the equipment is being properly managed, is its service life acceptable?
Check whether there are any design problems making the lifetime unacceptable. If there are, carry out corrective maintenance to prolong the lifetime.
4 If the service life is acceptable, is it stable?
Examine the equipment’s history and decide whether or not its lifetime varies significantly. If it is stable, choose TBM.
5 If the service life is not stable, can the deterioration pattern be identified?
In other words, does the part to be maintained deteriorate in an identifiable way with time? If the deterioration pattern cannot be identified, study the relevant part until it can.
6 If the deterioration pattern can be identified, is there a parameter by which the deterioration can be measured?
If no parameter can be identified, study the situation until one can. If a parameter can be identified, choose CBM.
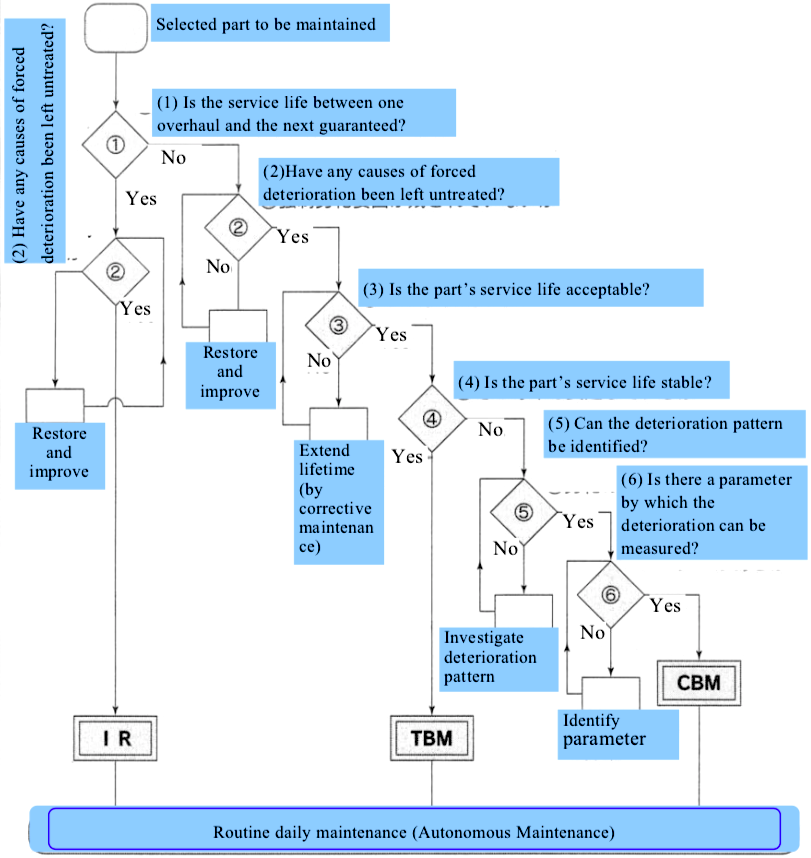
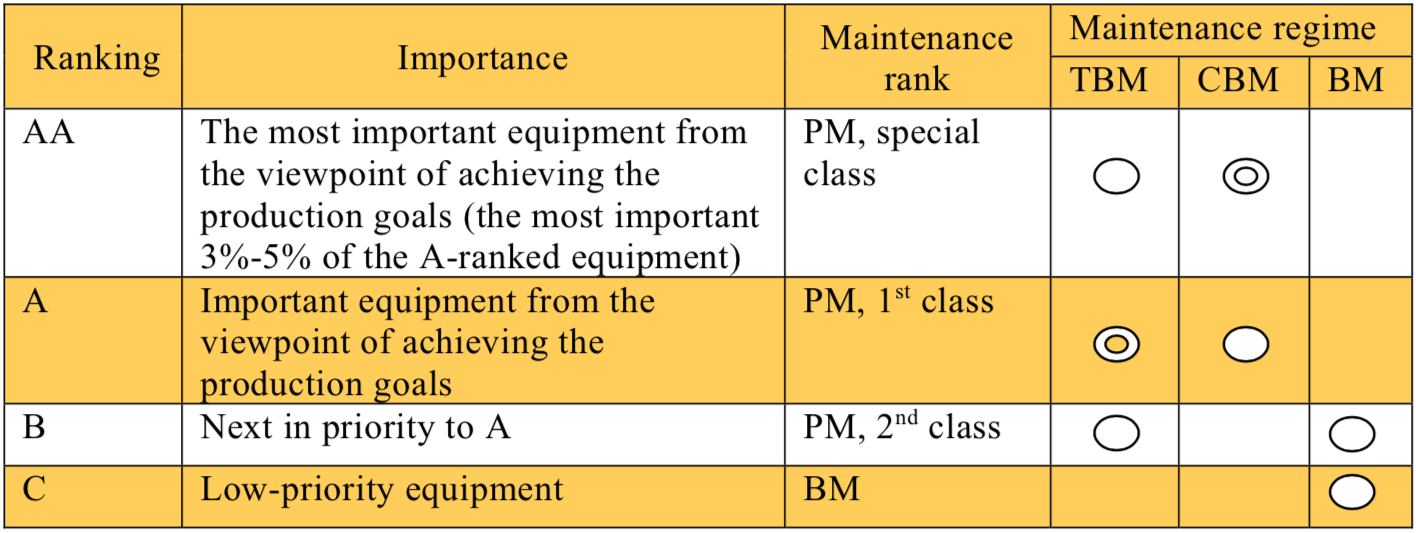
1 Comment