Material replenishment is an essential part of supply chain management, and it is crucial to have a system that ensures the right materials are in the right place at the right time. Several types of material replenishment systems are available, and each has its own advantages and disadvantages.
- Kanban System: This is one of the simplest and most commonly used material replenishment systems. It works by using visual signals such as cards or containers to trigger the movement of materials from one stage to another in the production process. The Kanban system is most effective in a pull-based manufacturing environment where production only occurs when a customer orders.
- Just-In-Time (JIT) System: JIT is a pull-based material replenishment system that focuses on delivering the right materials to the right place at the right time. It closely monitors inventory levels and schedules deliveries to match the pace of production. JIT systems are most effective in reducing waste and improving efficiency, but they also require a high level of coordination and communication between suppliers and manufacturers.
- Material Requirements Planning (MRP) System: MRP is a push-based material replenishment system that uses forecasting and inventory data to plan the production and delivery of materials. It works by calculating the material requirements for each stage of the production process and scheduling deliveries accordingly. MRP systems are most effective when used in an environment where a set schedule drives production.
- Reorder Point System: A reorder point system is a simple, rule-based material replenishment system that determines when to place an order for more materials based on the current inventory levels and lead time. This system is easy to implement and maintain, but it can be less flexible and responsive than other material replenishment systems.
Push System
- Focuses on maximizing output, optimization of resource utilization (man and machine)
- A traditional system of production and material planning
- Relies on Material Requirements Planning (MRP)
- Production is often in monthly buckets
- Computer generated schedules
- Production is usually in batches at every workstation
- Long lead times
- No visual signals
Pull System
- MRP is used for long-term planning and forecasting only
- Production tied to actual demand
- Inventory is reduced, lead time is reduced, and material turnover is greatly enhanced
- Abnormalities and variation is exposed, and quality improves
- Relies on visual signals
Pull and Kanban
A continuous supply of components, parts and supplies, such that workers have what they need, where they need it when they need it. – Japanese: Kan = “card,” ban = “signal,” so… Kanban means “signal cards” – Continuous (automatic) replenishment of a small stock required to perform a job; a part of “Just in ‘Time” inventory – Required by a “pull” system since downstream demand triggers replenishment.
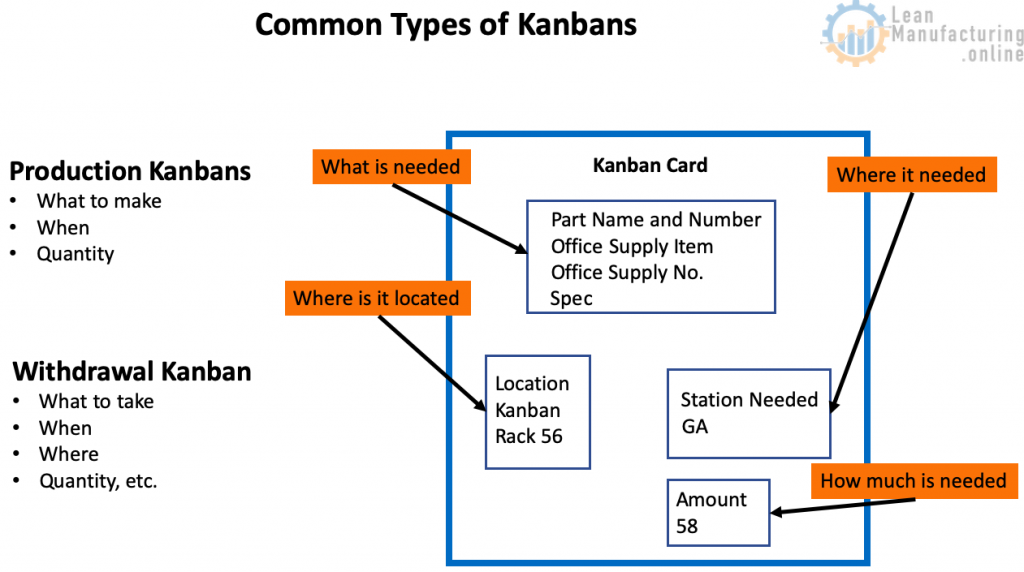
In conclusion, the type of material replenishment system you choose will depend on your business’s specific needs, production processes, and inventory levels. It is important to carefully consider the advantages and disadvantages of each system before making a decision and to work with a knowledgeable supplier or consultant who can help you implement and optimize your material replenishment system.