To understand the satisfaction that Autonomous Maintenance brings, people need to experience plenty of success. This can be arranged by giving the operators every possible opportunity to get their hands dirty, find lots of equipment defects, and fix them by themselves. By correcting problems and making improvements, operators will be able to see the positive results that this brings, and gain a real sense of achievement.
Taking on something you have never done before can be tough, but it obliges you to develop your knowledge and creativity to meet the challenge. This is a crucial process. As the proverb says, “Two heads are better than one, ” which certainly applies to team activities, enabling the operators to pool their thoughts and ideas. In science, original ideas come from a questioning attitude. Likewise, on the shop floor, the action of overcoming difficulties can trigger the development of creative and original teamwork.
Operators also need to be given improvement projects to work on to maintain a high level of team activity and raise individuals’ improvement skills to bring substantial benefits to the business. This can be done by allocating selected Focused Improvement topics that allow them to rise to the challenge, exercise their creativity, and realize more and more of their potential. Since Focused Improvement activities increase individual operators’ enthusiasm for improvement and generate tangible benefits in terms of reducing losses, they should be introduced from Step 2 onwards, as shown in Figure “Focused Improvements by Teams”. The topics to be addressed should be determined in the preparation phase; the existing situation is then examined carefully during Step 1 to highlight any problems, and improvements are made in Step 2 to rectify these. The team then continues to make improvements throughout the remaining steps.
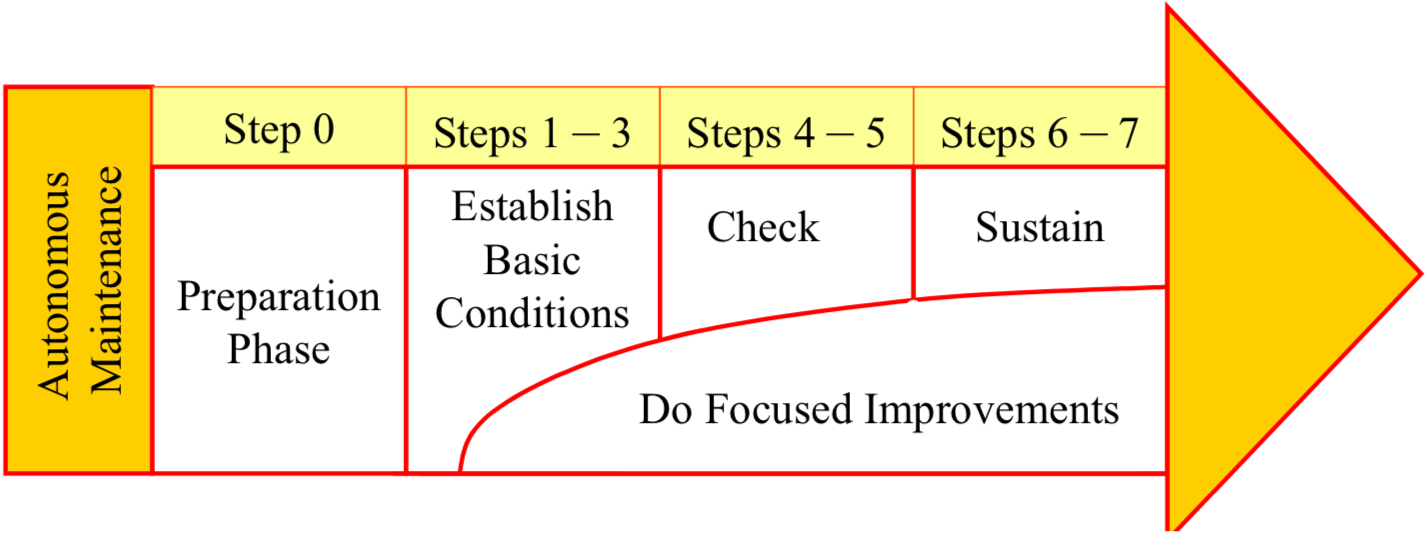
Include Focused Improvements in team activities
Each team needs to spend a certain proportion of its time sustaining the quality of the work it is responsible for at its particular level in the organizational hierarchy, and a certain proportion of its time improving that work (Figure “How the Balance between Sustainment and Improvement (and Radical Change) Varies with Position on the Corporate Ladder” shows how the teams’ time might be divided up). This of course means that the scope each team has for becoming involved in Focused Improvement is necessarily limited.
Focused Improvement topics to be addressed by front-line TPM teams should be selected carefully, bearing in mind the improvement requirement and the team’s level of energy and enthusiasm. The situation must not be allowed to develop where teams are left to tackle large-scale projects that ought to be done by managers, while the managers sit back and do nothing, claiming that they are doing their job by delegating. On the contrary, in dividing the responsibility for Focused Improvement activities, topics suited to management must be assigned to them, whilst topics appropriate to teamwork are assigned to the teams (see Figure “Division of Responsibilities for Focused Improvements”).
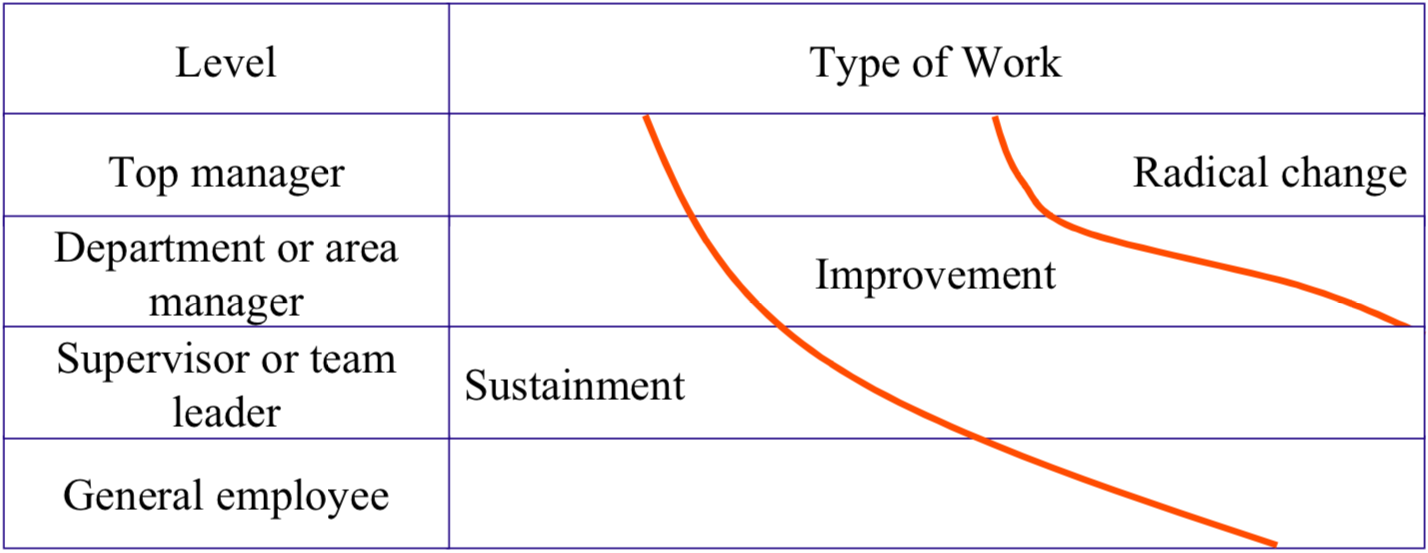

Handle requests for maintenance work promptly
Promptness is important when correcting irregularities exposed by Autonomous Maintenance activities, and implementing improvements. A large part of this work will need to be done by the maintenance department. Inevitably, Autonomous Maintenance will generate a good deal of extra work, over and above what the department itself had planned to do, and this will become a considerable burden. Nevertheless, this extra work cannot be allowed to pile up. Unless the maintenance department deals promptly with all the extra requests, no progress will be made. The Autonomous Maintenance rollout will not get anywhere, and the teams will lose heart.
The maintenance department will just have to find ways to keep up with the extra demand. This could be done by developing more efficient ways of working, reviewing staff deployment and shift patterns, doing overtime after hours or at weekends, or resorting to subcontracting.