1. Autonomous Maintenance Implementation Steps
7 steps to Autonomous Maintenance. Examples of steps to implement AM
Step 1. Initial cleaning (cleaning and inspection)
Complete elimination of waste and dirt, focusing on the equipment main body, implementation of lubrication and retightening, discovery of equipment problems and the restoration thereof.
Step 2. Countermeasures for generating sources (sources of contamination, SOC) and difficult-to-access locations (hard-to-access areas HTA)
Prevent causes and scattering of waste and dirt, improve difficult-to-access locations for cleaning, lubrication, retightening and inspection, and reduce the time required for these activities.
Step 3. Creation of tentative autonomous maintenance standards
Formulate behavioral standards so that cleaning, lubrication, retightening and inspection can be steadily maintained in a short period of time (need to indicate the time limit which can be used daily and periodically).
Step 4. General inspection
Education on inspection skills through the inspection manual, and the identification and restoration of minor equipment defects through implementation of general inspection.
Step 5. Autonomous inspection
Creation of cleaning, lubrication and inspection standards that can be efficiently and steadily maintained, and the creation and implementation of autonomous inspection checklists.
Step 6. Standardization
Standardization of the various on-site management items, and complete systematization of support management:
- On-site distribution standards;
- Standardization of data records;
- Standardization of die, jig and tool management;
- Standardization of process quality assurance, etc.
Step 7. Thorough implementation of autonomous management
Implementation of the company policies and goals, constant implementation of improvement activities, steady recording of MTB analysis, and improvement of equipment through analyzing the records.
7 steps for Equipment Industry
Implementation Table of 7 Steps for the Autonomous Maintenance Equipment Industry
Implementation of Steps by Division
7 Steps for the Autonomous Maintenance Assembly Division
4 Steps for the Warehouse and Distribution Divisions
2. Creation of an Autonomous Maintenance Master Plan
Autonomous Maintenance Education Curriculum
Autonomous Maintenance Introduction Education Schedule
Selection and Model Machine
Model Equipment Selection Standards
- Use the points in the score column for evaluation, and use no other points;
- General evaluation standard:
- 26 points or greater: Rank A (greater than 60% of maximum);
- 18 points or greater: Rank B (40-60% of maximum);
- 17 points or less: Rank C (under 40% of maximum).
- The model machine selected should be an “A” rank machine, and should have a sufficient level of replicability in other machines.
Model Machine Registration
List of Autonomous Maintenance Registered Machines (Machines on Which the Autonomous Maintenance Step is to be Implemented)
Board for Displaying Registered Machines and Managing Progress of Steps
3. Autonomous Maintenance Diagnosis System
Autonomous Maintenance Diagnosis Flow Chart
Application Form for Autonomous Maintenance Diagnosis Autonomous Maintenance Diagnosis Sheet
Application Form for Top Executive Diagnosis of Autonomous Maintenance
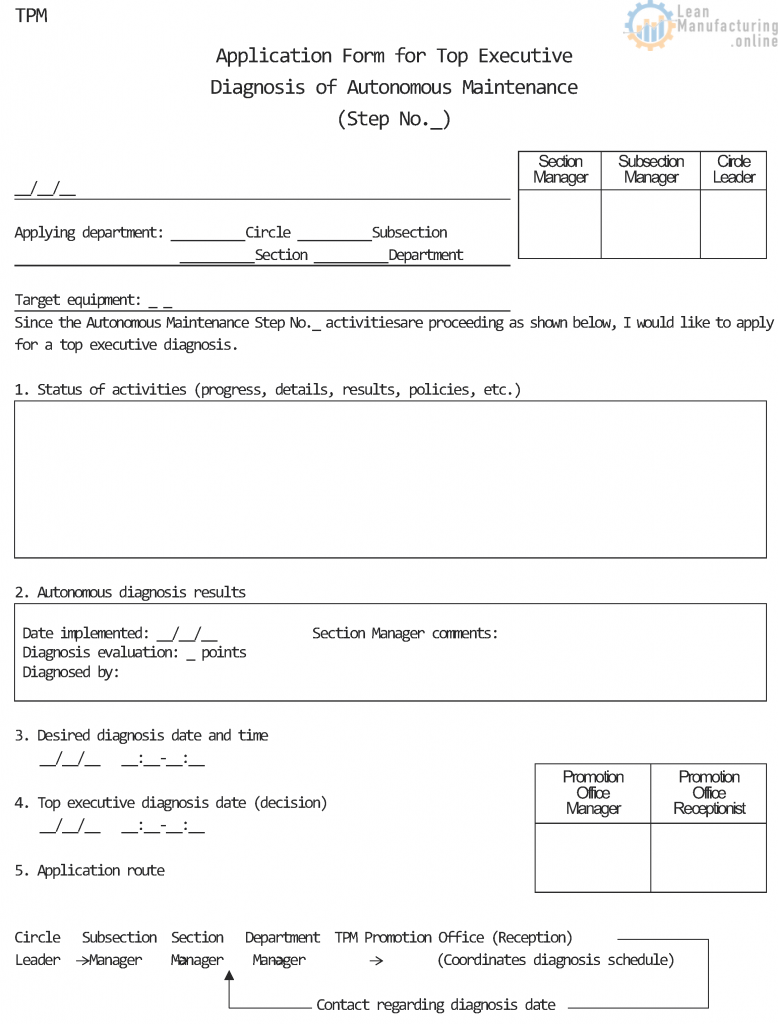
Autonomous Maintenance Passed Diagnosis Seal
Usage method
Utilize these step charts in the course of implementing autonomous maintenance so that the level of progress of each equipment or line can be seen at a glance.
Affix the “activity in progress” seal on the steps that are currently in progress. When the step has passed a diagnosis, write the date on the “passed” seal and affix the seal on the step. Further, affix the “activity in progress” seal on the next step at that time.
- The printed set of “activity in progress” seals include steps “4-1-4-6” (“6-1-6-6” are used for administrative/indirect divisions).