This is a crucial step, at which the cleaning is inspection concept is put into practice. It is not a matter of just making the equipment look clean on the surface; the process of cleaning exposes abnormalities, such as leaks, loose fastenings, or damaged parts. This step aims to get to grips with the equipment, getting our hands dirty and removing every last bit of dust or grime, and keeping our eyes open as we do so because this is by far the best way of discovering problems.
Since initial cleaning is a key step in which the equipment is cleaned thoroughly to make any abnormalities visible, it is also called “Checking through Cleaning”. By carrying out this step, operators not only get their equipment clean and find out what is wrong with it; they also experience for themselves, in a very practical way, that cleaning and inspection are actually the same things.
When embarking on an Autonomous Maintenance program, it is important to ensure that everyone taking part understands exactly just what cleaning really means, so this topic will now be discussed in a little more detail.
(1) What is cleaning?
Basically, cleaning the equipment means exactly what it says: removing all foreign matter, such as dirt, dust, oil stains, swarf, sludge, and so on, from the machinery, molds, tools, jigs, and other equipment used to make the product. Getting every last corner of the equipment thoroughly clean is the best way of revealing hidden defects, as emphasized by the slogan cleaning is inspection. It is not a cosmetic exercise; only a real ‘deep clean’ will do the job. Less-than-thorough cleaning leads to a host of harmful effects, some of which are noted in Table “Some Harmful Effects of Inadequate Cleaning”.
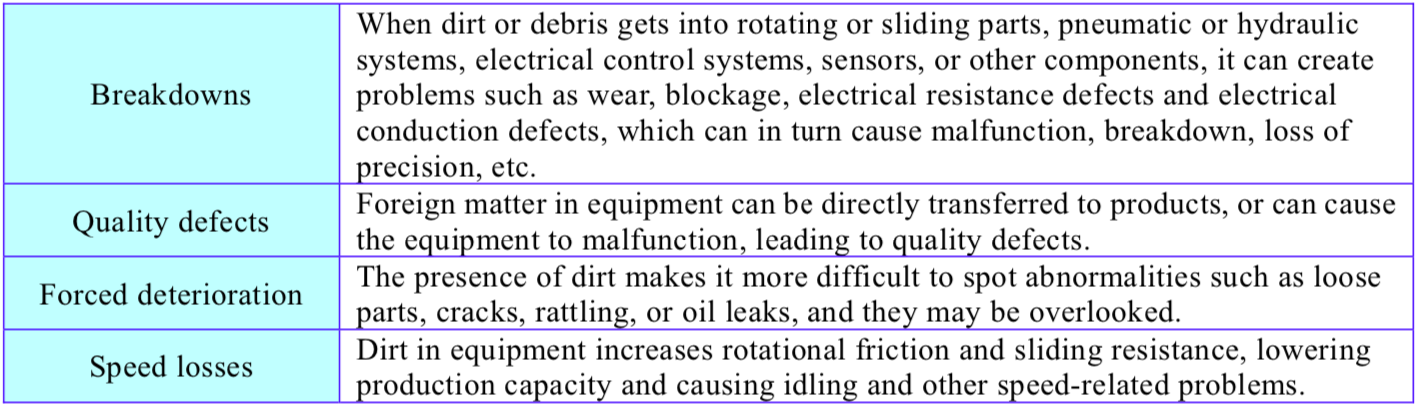
(2) Cleaning is Inspection
We describe this approach as Cleaning is Inspection because it aims to discover as many equipment abnormalities as possible. Painstakingly cleaning the equipment like this, touching every nook and cranny, often reveals hundreds and hundreds of minor defects.
Key Points
- Always check safety conditions carefully before starting to clean.
- Operators should really get involved and see cleaning as an integral part of their job.
- Remove every last bit of built-up grime.
- Eliminate dust and dirt from every corner of the equipment. To do this, operators should open up covers and flaps that they have never looked under before.
- Cleaning should not be confined to the main body of the equipment. The exteriors and interiors of peripheral devices such as conveyors, fuse boxes, and hydraulic fluid reservoirs need to be cleaned as well.
- Operators should not give up if their equipment gets dirty again as soon as it has been cleaned. They should observe it carefully to see where, when and how much dirt starts to appear again.
Implementation
Key Points
(1) Give the basic instruction required for carrying out Step 1
Operators must be trained so that they properly understand the safety requirements, how their equipment is constructed and how it works, and how to perform tasks such as checking, lubricating, and tightening. This training must be kept practical, through the use of one-point lessons (see Figure ” A Typical TPM One Point Lesson”), or shop floor practice sessions using the actual equipment. One Point Lesson (OPL) Template can be downloaded here.
(2) Create a cleaning plan
By drawing up a cleaning map and using some kind of ranking scheme to decide what order the equipment should be cleaned in, a cleaning plan can be prepared showing the cleaning procedure to be followed. The plan should cover 5-S activities, and list the tools and materials that will be required.
(3) Remove all unnecessary objects
Begin by scouring the entire work area (not just the equipment and its immediate surroundings) for unnecessary objects, and removing them. Freeing up space in this way is an essential preliminary step in initial cleaning.
(4) Do initial cleaning
To detect abnormalities and defects, operators need to scrutinize their equipment, touch it, feeling it, and moving the working parts. They should use all of their senses to detect problems, such as play, looseness, wear, misalignment, vibration, irregular noise, overheating, oil leaks, and so on. They should pay particular attention to the parts that give them concern on a day-to-day basis.
(5) Find sources of contamination
Any sources of contamination that cause the equipment to become dirty again after cleaning must be clearly identified, and everyone should be impressed with the need to deal with these so that the equipment stays clean.
Figure “Workflow for Step 1 (Initial Cleaning)” illustrates the overall workflow for this step, and Figure “Step 1 Initial Cleaning (Checking through Cleaning) 1, 2” shows further details.
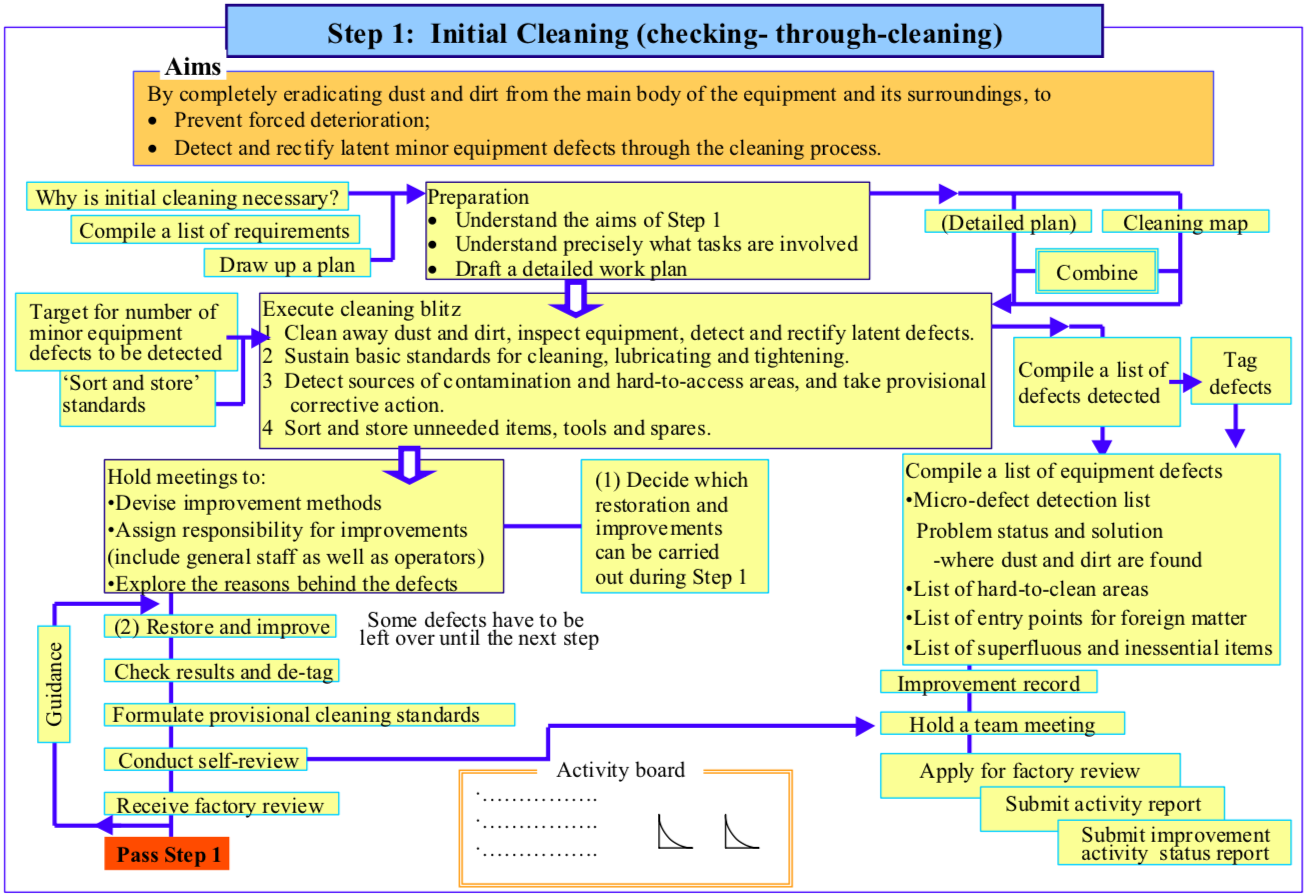
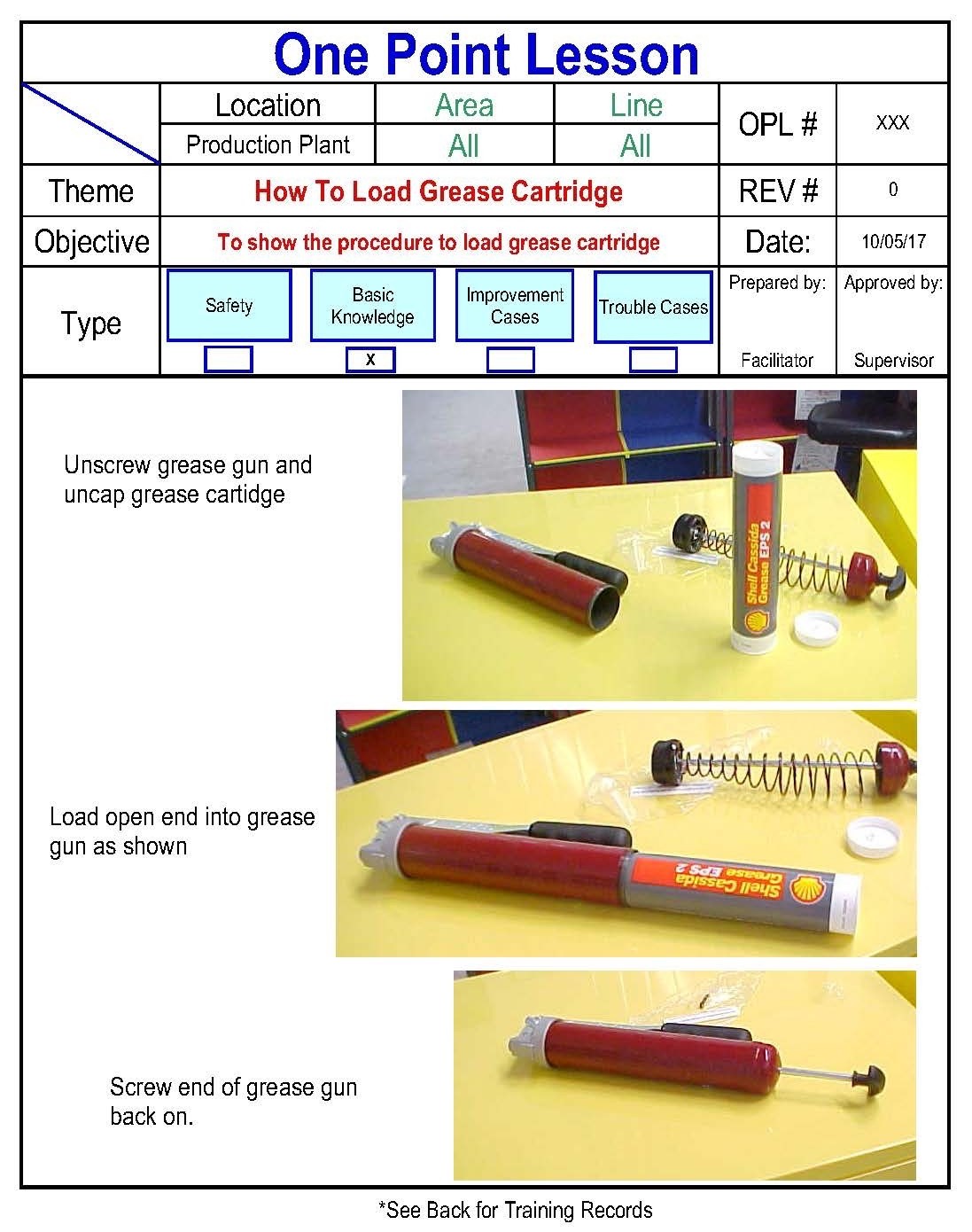
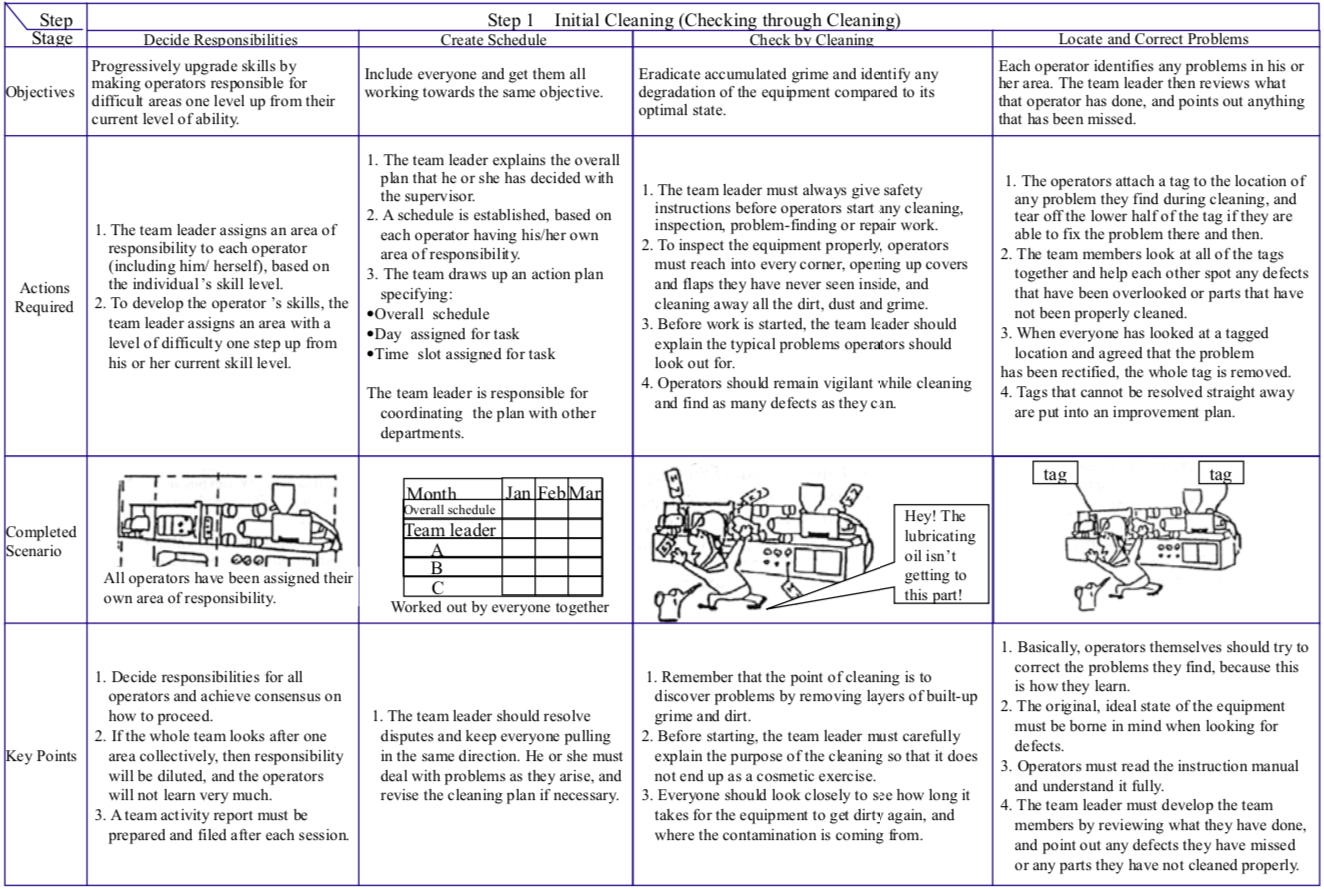
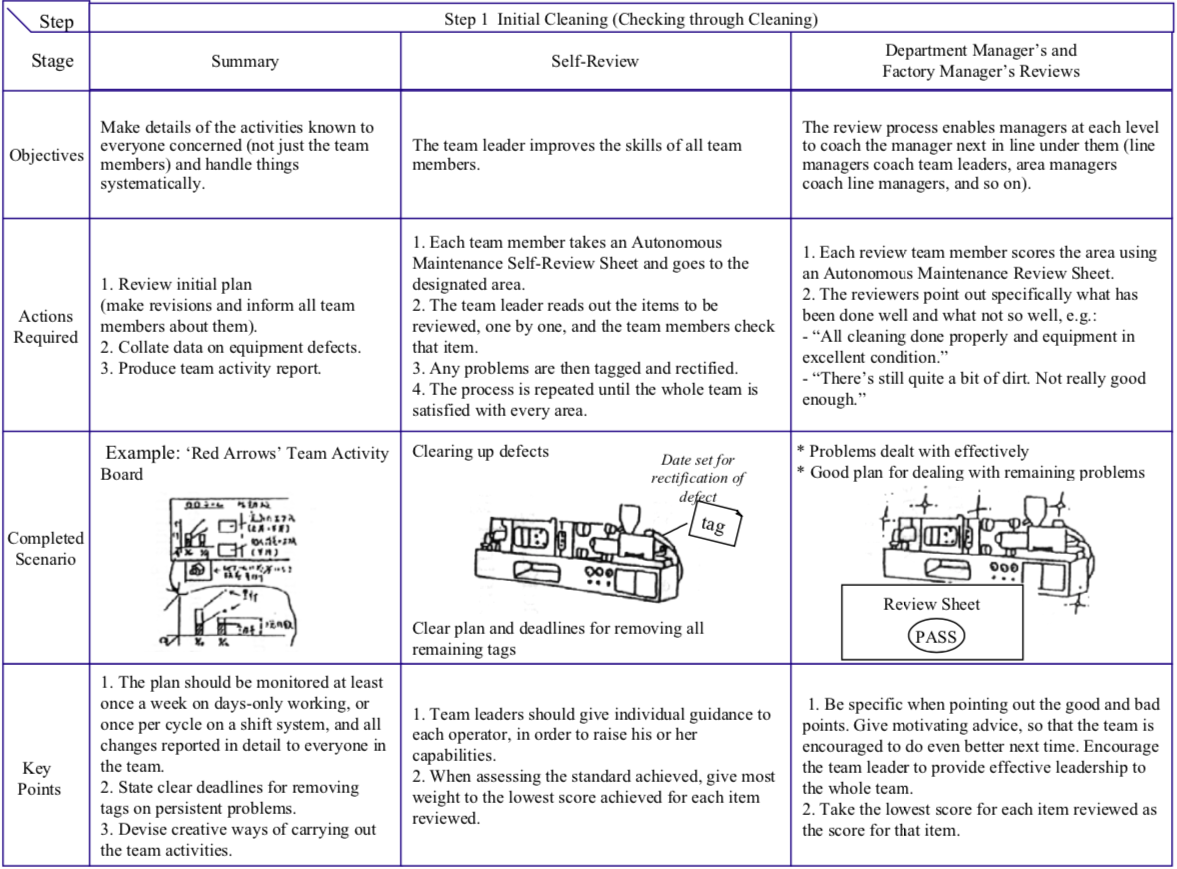
Next→Autonomous Maintenance. Step 2: Tackling Contamination Sources and Hard-to-Access Areas