Aims
Up to this stage, the Autonomous Maintenance activities have focused on the equipment, and in particular, the basic equipment conditions and the daily checks required to maintain them. The aim of Step 6, in addition to consolidating what has been done so far, is to expand the operator’s role to cover the equipment’s surroundings as well as the equipment itself, continue to drive down the losses closer and closer to zero, and put the finishing touches to the team’s ability to manage their own work.
Implementation
In Step 6, while sustaining optimal conditions through Autonomous Checking, operators keep on making improvements and record any defects, equipment failures, or minor stops that occur. They rectify the problems that arise and lock improvements into place by upgrading the standards.
In Step 6, they also focus on their own movement and actions. By getting together and examining the way in which they perform each task, the operators can figure out how to make their work easier and more pleasant to carry out, and then go about creating the appropriate conditions for this to happen. Figure “Workflow for Step 6 (Standardization)” gives an overview of how these activities are developed.
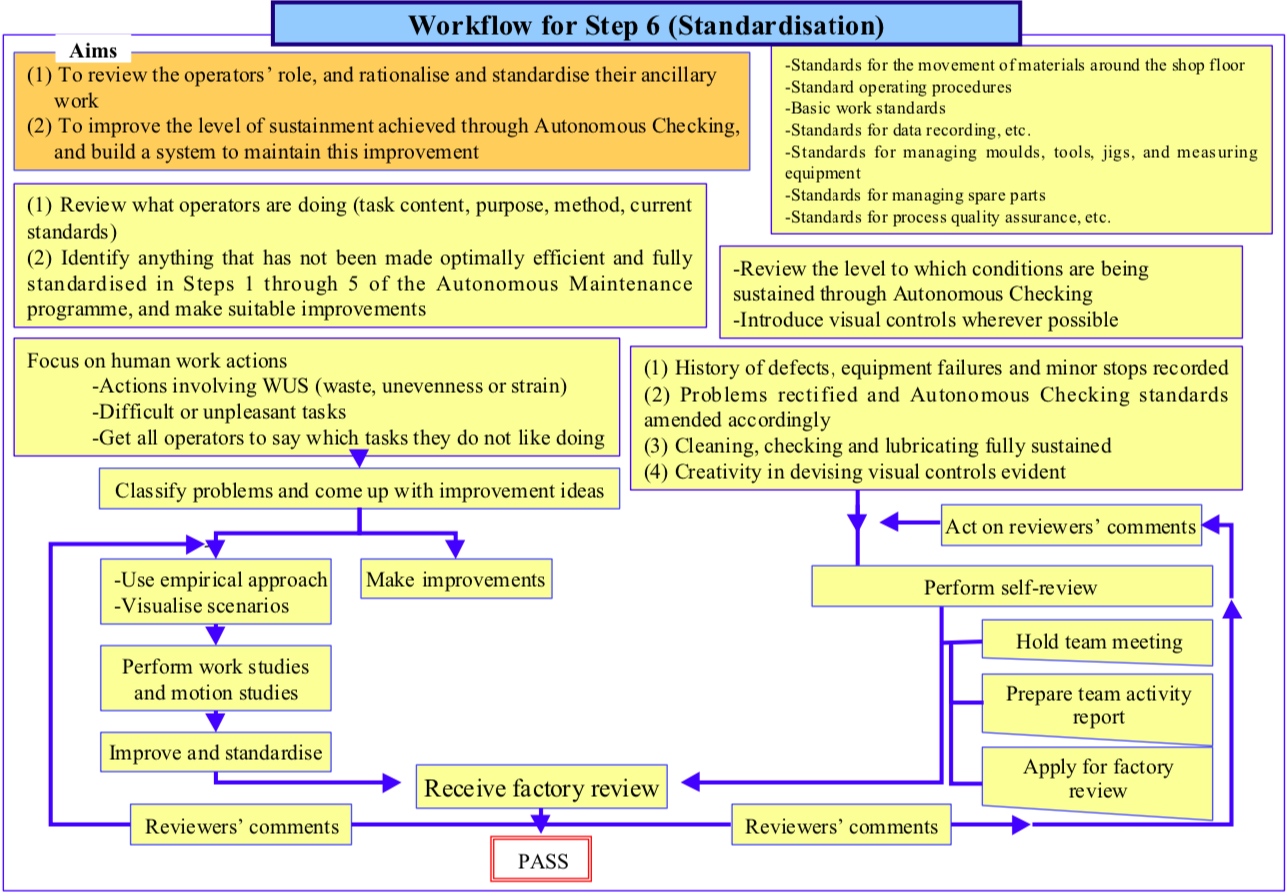
Looking at the development of Steps 1 to 6, it can be seen that the focus is initially directed at the equipment, then shifts to quality, and finally moves to the actions of the operators themselves. This focus on the human role and the search for ‘worker-friendly processes’ provides the vital finishing touches to self-management. We want our line teams to be fully competent to get on with the job by themselves, because only then can we think about allowing them to take total charge of their own workplaces. Step 6 addresses the issue of standardization from this standpoint.
What the standards should cover
- Standards for the movement of materials around the shop floor
- Standard operating procedures
- Basic work standards
- Standards for data recording, etc.
- Standards for managing molds, tools, jigs, and measuring equipment
- Standards for managing spare parts
- Standards for process quality assurance, etc.
Key points
- At Step 6, the role of the operator is broadened to cover the work done in and around the equipment. Operators must look at why they do each task, separating out the routine work from the non-routine work, checking whether standards have been defined for each repetitive routine task, and establishing them if necessary. Non- routine work, on the other hand, may give rise to quality defects, meaning that all products have to been screened, or may result in over-production, with the upshot that the plant runs out of storage space and products or components have to be shifted around. Problems of this kind should be handled separately, and specific improvements made to rectify them.
- Some of the routine tasks will involve WUS (waste, unevenness, and strain) or other imperfections when viewed from the objective of maximizing the efficiency of the operators and the equipment. Suitable improvements must be made, and the revised tasks must then be standardized. This requires each operator to observe his or her own work closely, and then discuss with the rest of the team how to perform it in an ideal way.
- Combine small improvements to make big ones. Each small improvement focusing on an individual operator will produce a small labor-saving of, say, 0.5 or 0.3 person-hours. These savings must be combined and translated into actual reductions in the number of people required to operate particular processes, thus linking directly to the business goals.
- Promote ways of sustaining Autonomous Checking. To ensure that the regime of cleaning, checking, and lubricating is sustained, and optimal conditions are always in place, it is essential to have a clear follow-up plan. One good way of doing this is to have a system of ongoing factory reviews, based around the Autonomous Maintenance standards. For example, after each factory review, a pass certificate is issued and the date of the next review is decided. It is best not to leave too large a gap between one review and the next – an interval of three months is about right.