- To make hidden losses on the shop floor visible;
- To reduce these losses;
- To improve OEE;
- To increase labour productivity and add more value;
- To reduce conversion costs;
- To improve profitability;
- To raise analytical and improvement abilities through loss reduction programs
Focused Improvement and Autonomous Maintenance
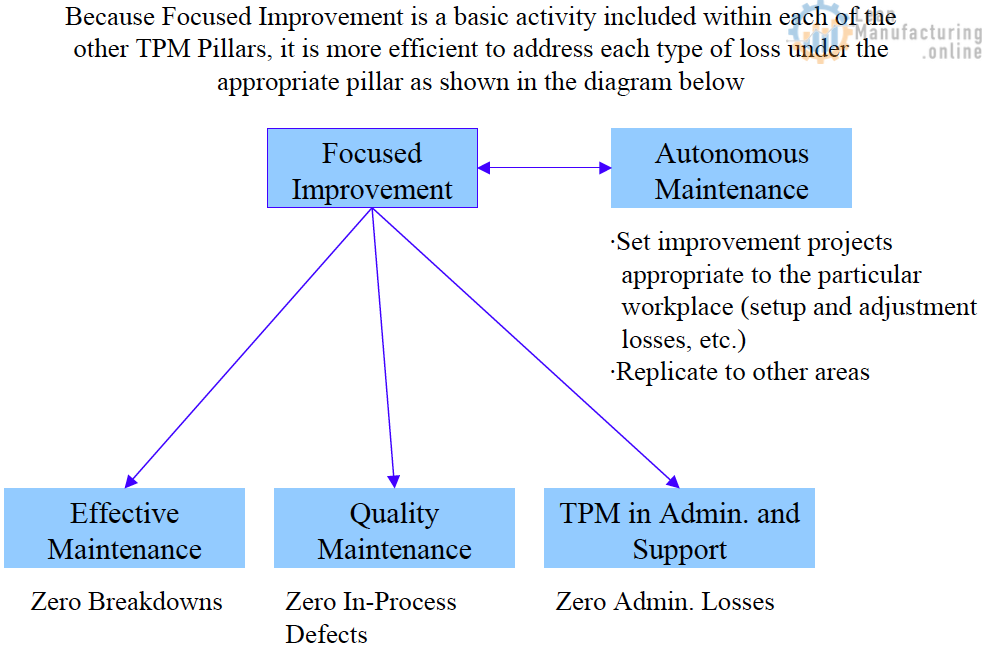
How to Do Focused Improvement

Why-Why Analysis Review
Why-Why Analysis is a technique for systematically tracking down undesirable phenomena’ root causes logically and methodically, based on the facts, instead of merely brainstorming. It is conducted using one of the following two basic approaches:
- Approach starting from ‘what should have happened (but didn’t).’
- Think what the necessary conditions must be (the conditions that must be satisfied for everything to work as possible) and list them up as items to investigate. Then investigate each condition on the spot to see whether it is actually satisfied.
- Approach starting from first principles
- Focusing on the point at which the problem occurred, go back to the first principles, and do the first step of the analysis by asking why these principles failed to operate.
Seven essential considerations when implementing Why-Why Analysis
- Use simple phrases like ‘A became B’ when defining the phenomenon and answering the WHYs
- Check the logical structure of the analysis by reading back from the last ‘Why?’ to the phenomenon.
- Reading the analysis backward, check that all the possible causes have been identified for each event.
- Continue asking ‘Why?’ until you identify the actions that will prevent the problem from recurring.
- Only note items that deviate from normal.
- Avoid trying to identify causes lying in human psychology.
- Do not use negative words such as ‘bad.’
Why-Why Analysis Sheet (approach from ‘what should have happened?)
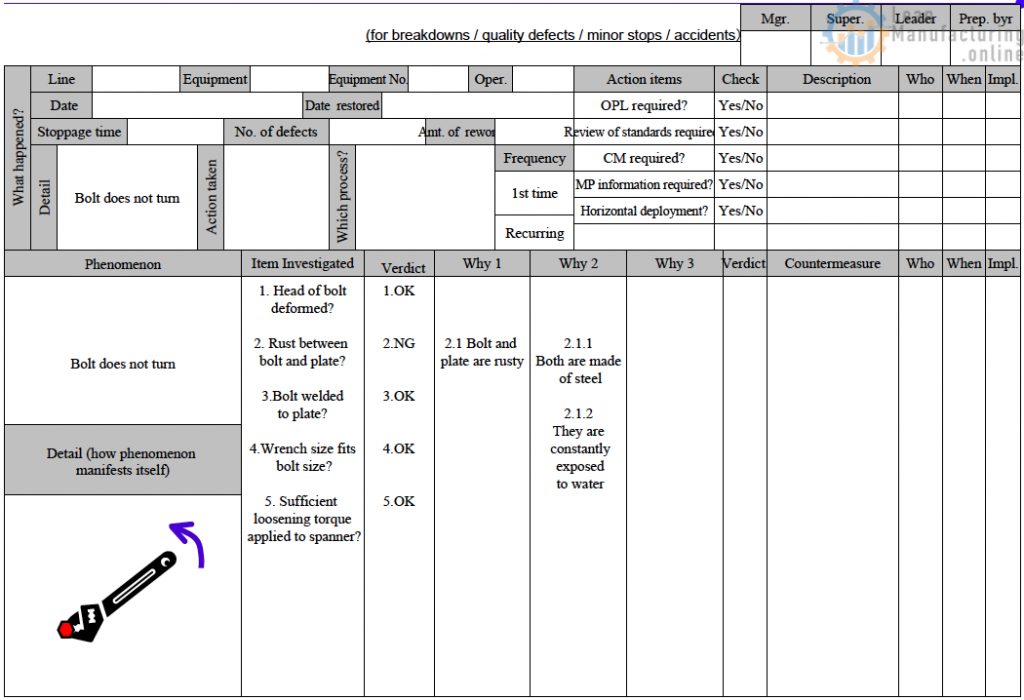
Why-Why Analysis Sheet (approach from first principles)
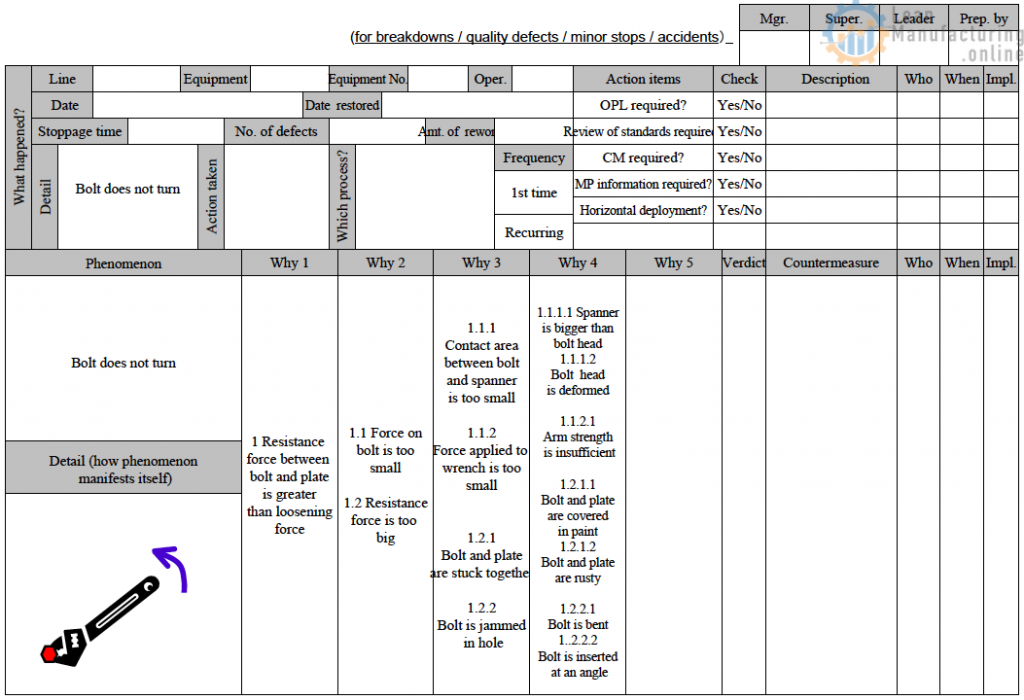
The Anatomy of Why-Why Analysis

Kaizen Steps
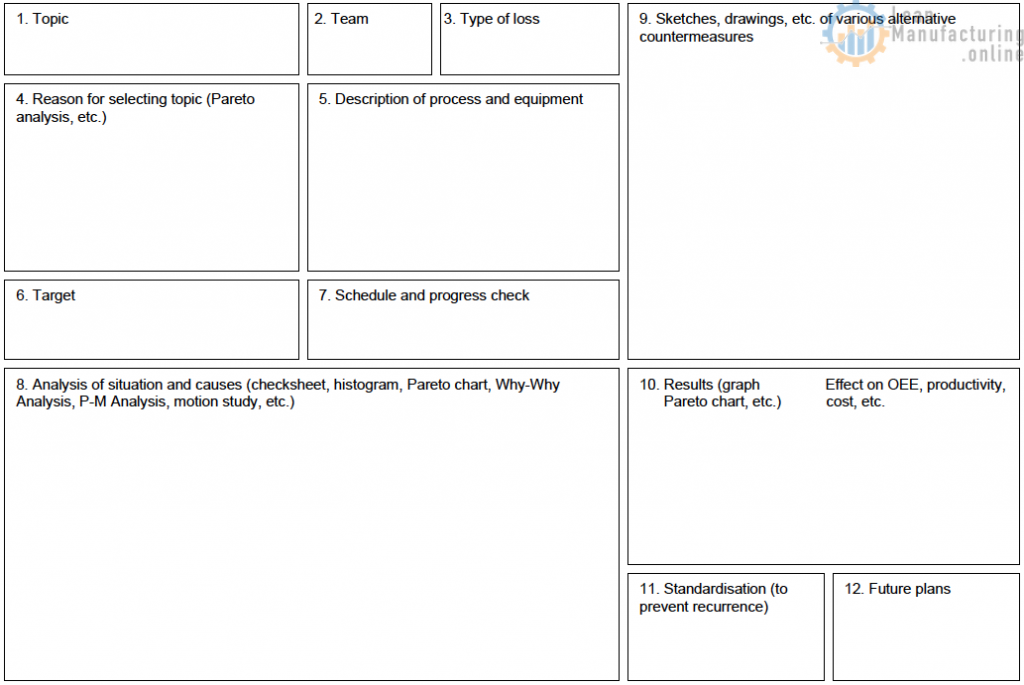
Why-Why Analysis Sheet
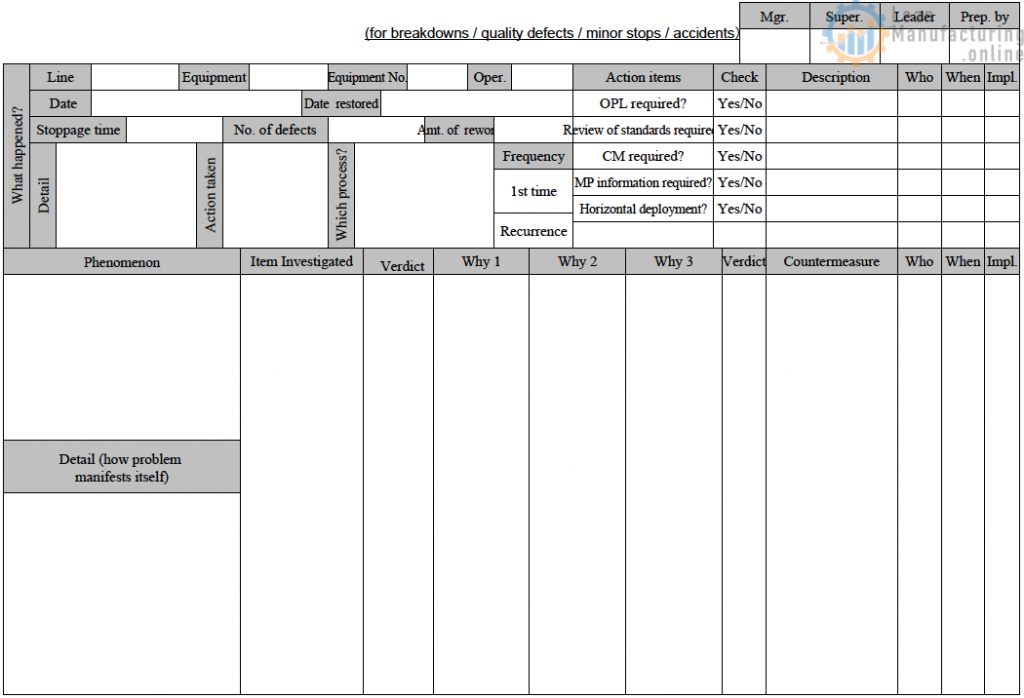
Zero Loss Concept
The Conventional Improvement Approach and the Zero Approach Compared
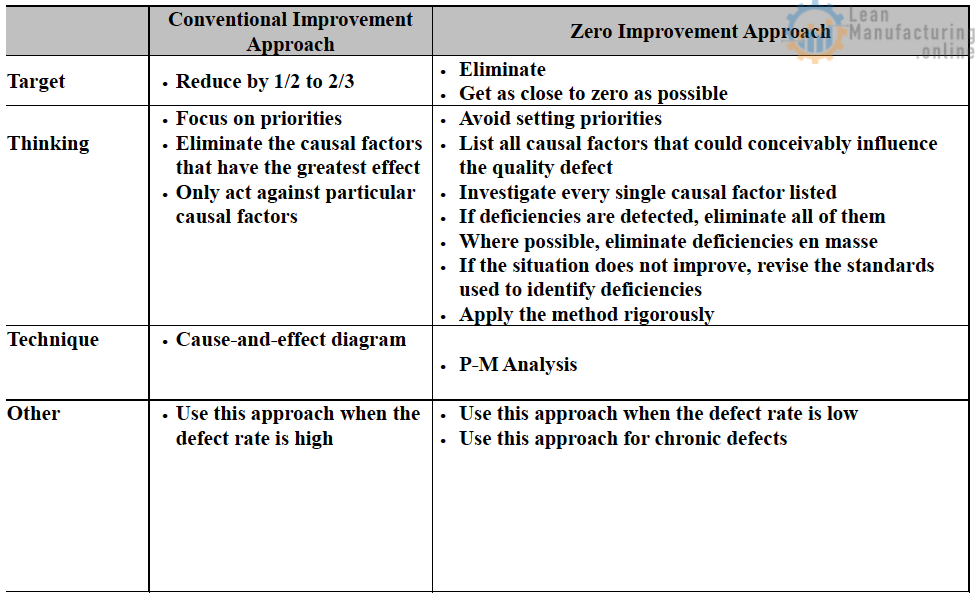
Conventional KAIZEN
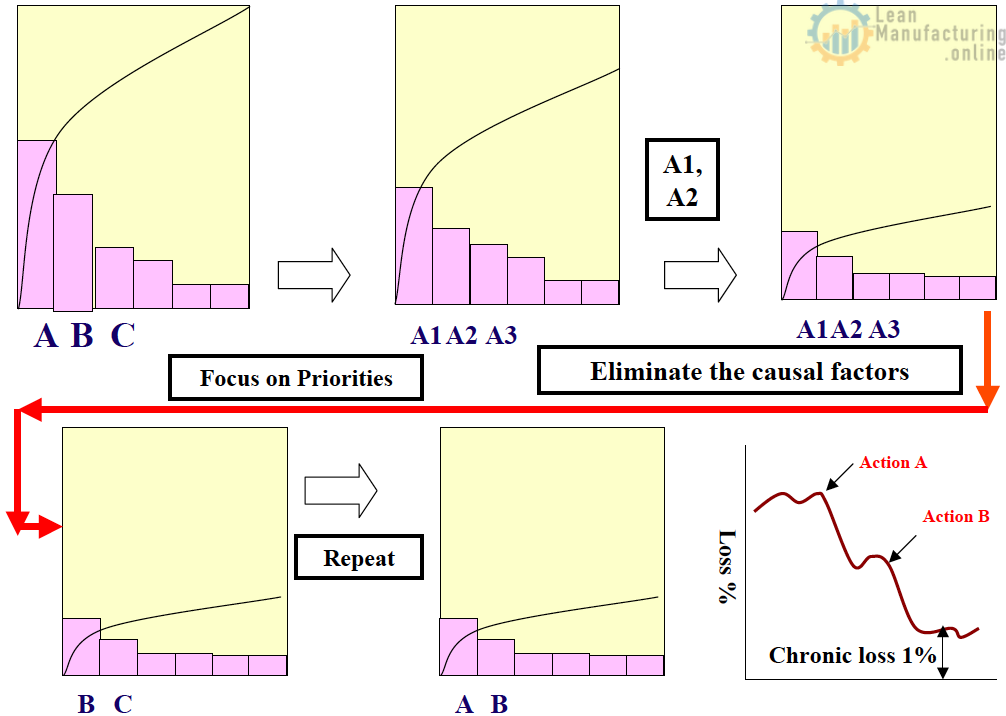