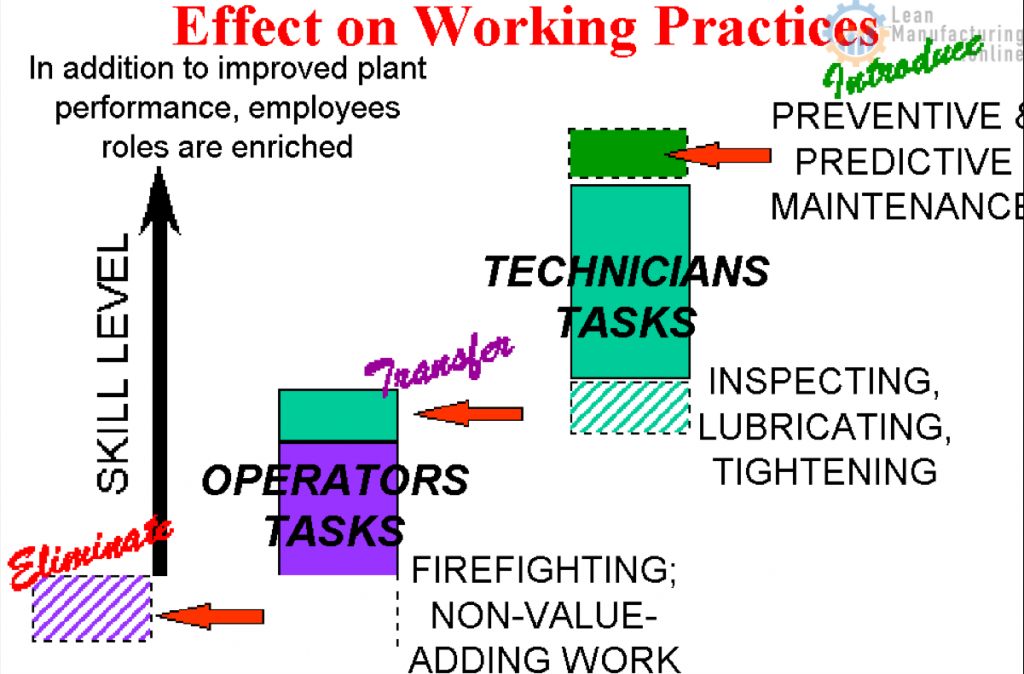
To perform gap analysis, relative rankings of different facilities (sites) need to be captured:
- Parts and Materials in Store Room
- Computerized Maintenance Management Software (CMMS) utilization
- Criticality of assets ranked and maintained
- Planning and Scheduled work
- Work order system
- Effectiveness of Preventative Program (PM)
- Maintenance Management Duties, Tactics and Best Practices
- Number of Technical Training Days/Men
- Overtime needed every month on average
- Maintenance Planner’s Duties, Tactics and Best Practices
- Trades’ Duties, Tactics and Best Practices
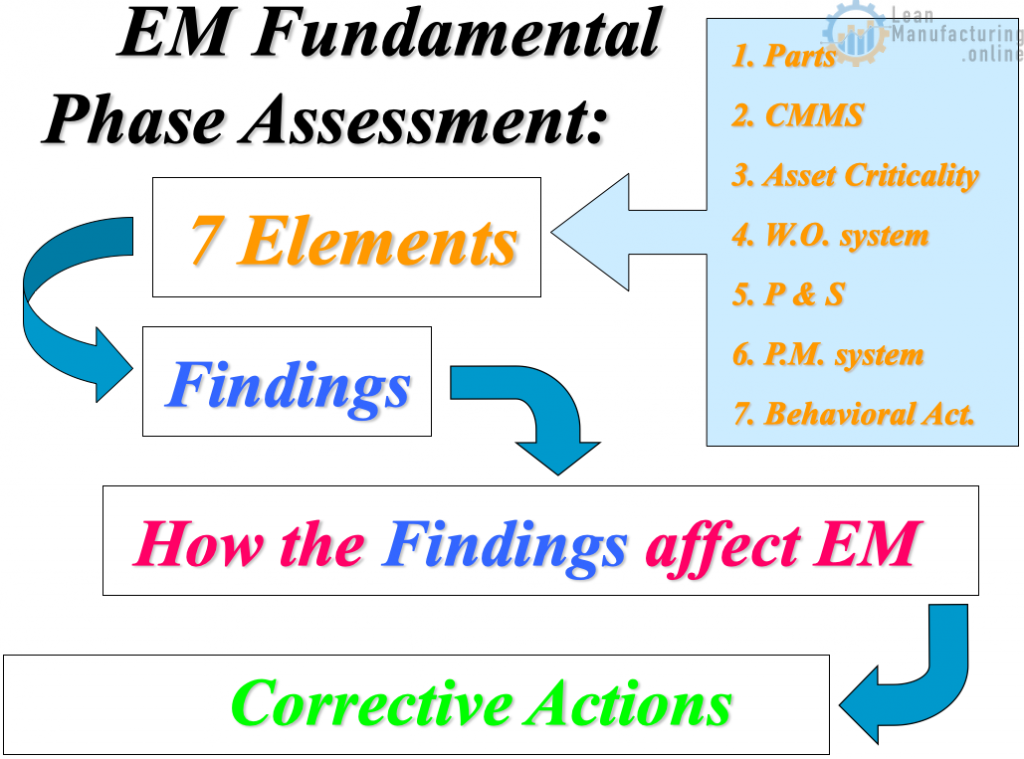
Example of Overall Assessment: Reactive Breakdown Maintenance Prevails
- Parts: Deficient tracking & control
- CMMS: Tool not effectively leveraged
- Asset Criticality: Not established
- Planning: Generally not practiced
- Work Orders: Systems lacking
- PM: Schedules not adhered to
- Behaviour: Focus on fixing breakdowns, not preventing them. Firefighting is rewarded
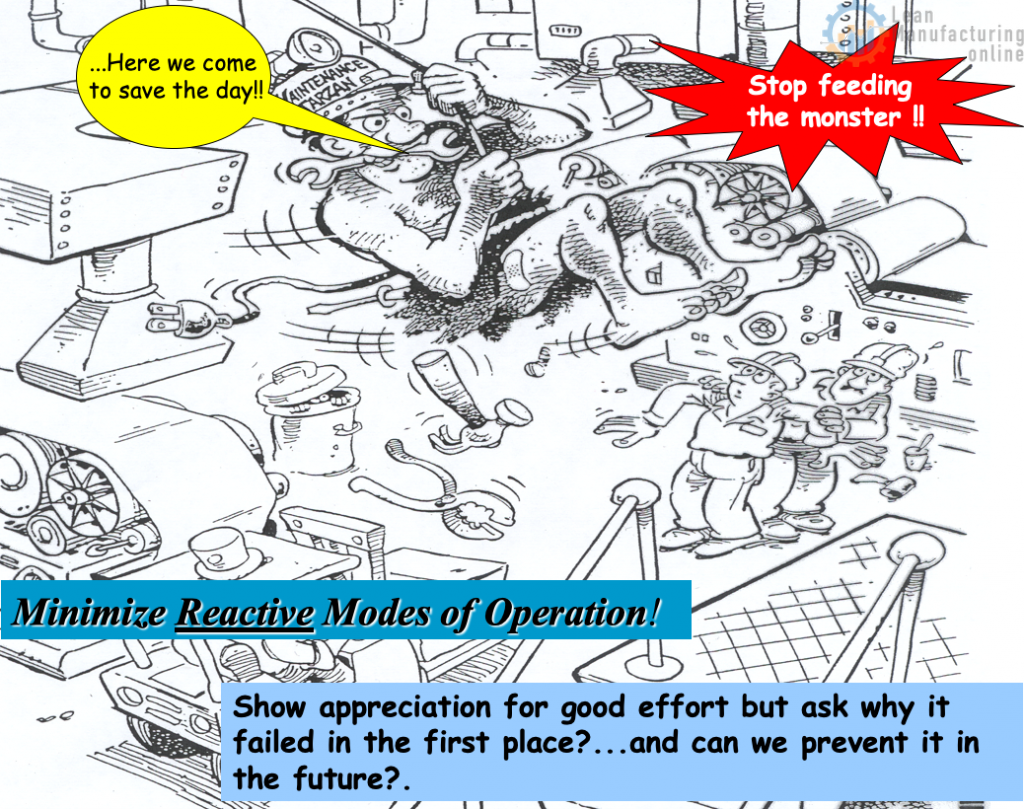
Leadership Support of the EM Process
When visiting the sites, ask about EM status:
- Number of Breakdowns (Baseline vs. actual)
- Number of Breakdowns analyzed and documented
- % Improvement in Breakdowns
- Parts Inventory (Baseline cost, number of line items)
- Parts stocked but not used in 6 months, one year, two years)
- Status of the PM program (number of equipment with at least a PM procedure attached (100% of type “A” most critical equipment)
- % of available man-hours documented in a work order program ( > 95%)
Example of findings. Parts
- Lack of SOPs & KPIs
- Incomplete Parts attributes
- Poor Housekeeping
- Inventory value and number of line items unknown
- No routine analysis of parts usage
- Poor parts tracking – suppliers leveraging us
- Parts Issuing not linked to WOs/assets
- Inventory accuracy not frequently monitored
How Findings Affect EM:
- Critical Parts not available when needed
- Many Purchase orders with single items
- Good and bad parts mixed
- Duplication of Inventory
- Higher cost to expedite parts needed
- Equipment Breakdowns longer than necessary
- Increased cannibalization of parts/assemblies
- Incomplete Maintenance cost
Corrective Actions “in Progress”:
- Stockroom Re-organization
- Preparing operating procedures
- Establish & set parts attributes for stock items
- Establishing Performance Indicators
- Where possible, closing the stockroom
- Condensing the number of stock locations
- Using the CMMS to manage parts
Example of findings. CMMS
- Discipline is not in place for the use of the tool
- Analysis of “data entered” often non-existing
- Imputed data not monitored for effectiveness
- The system has not expanded across the plant
- An incomplete record of parts issued, where, when
- An incomplete record of labour consumed by the equipment
- Lack of standard system
How Findings Affect EM:
- Undocumented Costing
- Lack of info to justify equipment improvements
- Difficulty in knowing where budgets will be used
- Excess Spare Parts Inventory and growing
- High stockouts on Parts
- Cumbersome queries and info tracking
- Lack of “I have a hunch” supporting data
It broke therefore we must fix it, …..but we must ask “why it broke in the first place”?
Corrective Actions “in Progress”:
- Preparing operating procedures
- Re-establishing minimum functionality
- Purging/Cleaning of present data
- Training of Users
- Expanding to include all assets maintained
- Shifting to Trades using the PC for knowledge gain, documentation, and troubleshooting
Example of findings. Asset Criticality
- No Asset criticality list was developed or maintained
- Maintenance work independent of asset’s importance, level of redundancy or work priority
- Preventive or Predictive Maintenance Costs not linked to equipment improvements
- Purchasing and stocking of parts not ranked by “most critical” first, or where is used
How Findings Affect EM:
- Resources available are spent on non-critical assets. Not prioritized
- Less effective use of the Maintenance budget
- Labour usage not maximized
- Increased costs expediting non-critical Parts
- Increased bonding to Reactive Maintenance
- Unneeded effort spent on low usage, low production, low-risk assets, redundant assets
Corrective Actions “in Progress”:
- Developing asset criticality list in order of importance to the business
- Publicizing the list
- Assigning a keeper to update the list
- Obtaining input from all and commitment from local Steering Committees
- Beginning to manage resources by following the list order
Example of findings. Planning & Scheduling (P&S)
- No real dedication to operating by P&S
- None or partial Maint. Planners assigned
- Reactivity still controls the resources
- PM procedures not monitored for effectiveness
- The coordinator spent much time planning jobs on the fly
- Cancellation or delay of work w/o review of consequences
- Each shift operates differently, with inadequate coordination, following different WOW
How Findings Affect EM:
- Labour is not used effectively, requiring an increased number each year
- Inflated number of parts in stock
- Not having the right part available when needed
- Breakdowns are repeated
- Parts/Assemblies cannibalization growing
- Wear trends not predicted or tracked effectively
Corrective Actions “in Progress”:
- Establishing Maint. Planners (1:15 trades)
- Preparing PM procedures and linking them to critical assets
- Maintaining relevant parts in stock and leveraging parts suppliers
- Eliminating Breakdowns due to increased attention by planners
Example of findings. Work Order (WO) system
- No / limited work order system in place
- Parts used were not linked to a WO upon the issue
- WOs not covering all equipment maintained
- Labour hours are not entered on the WO
- Entries not monitored for correctness
- WO is used for PM work only
- Lack of Equipment I.D. system in place
- WO is not a whole part of the Maintenance WO workflow
How Findings Affect EM:
- Equipment history is unreliable for making $ decisions
- Maintenance costs are incomplete or hard to track
- Work backlog challenging to calculate and schedule
- Every job done starts from scratch every time
- Documentation for tracking warranties, permits, audits & inspections diminished by lack of data
- Analysis of the history of CBM & TBM becomes impossible to perform
- Failure trends not detected in time
Corrective Actions “in Progress”:
- Expanding the system to all equipment maintained
- Establishing disciplines, procedures & WO workflow
- Using the WO module in the CMMS to more consistently track repairs, improvements, F-tags
- Activating the work requisition function plant-wide to track, enter, and respond to work needed.
Example of findings. PM program
- PM schedules not adhered to
- PM procedures have details missing
- Labour & parts not pre-planned and ready
- No one was assigned to check PM effectiveness
- Often not linked to pre-inspections
- No dedicated team is in place since there is a low commitment to execute
- “Seat of the pants” Lubrication plan
How Findings Affect EM:
- Failures repeated, new failures unpredicted
- The cost of maintenance is 3 to 5 times higher
- The Spare Parts inventory is twice the size
- Minor stoppages sabotage good production runs and contribute to reactivity in EM
- Budgets spent on equipment restoration were wasted due to discontinued or bypassed PM schedules
- Lower MTBF due to lack of formal PM Inspections of critical assemblies
Corrective Actions “in Progress”:
- Existing PM procedures are under review and checked for completeness
- Newly added value procedures created
- Scheduling PM now includes participation in Production planning
- Planners check PMs for effectiveness before scheduling
- Procedure creation involves operators & crafts
Example of findings. Preferred Behavioral Activities
- Equipment failures not documented/analyzed
- No open reviews of top failures encountered
- All crafts resources placed on Reactive Maintenance
- Many trades still believe that “No matter what, Production rules.”
- Crafts have low knowledge of the cost of parts, breakdowns, repetitive failures, poor lubrication
- Planners not utilized in proactive tasks
How Findings Affect EM:
- The seat-of-the-pants solutions are not designed to eliminate recurrences
- Maintenance costs escalating
- Breakdowns take more time to repair ( > MTTR)
- Repairs are more frequent (shorter MTBF)
Corrective Actions “in Progress”:
- EM managers re-organizing Maintenance
- Changing present Reactive techniques to more Proactive ones
- Leveraging the Planners (to provide summaries and information about where resources are used & why and to track trends of repairs)
- Establishing new working disciplines & procedures
- Providing training to trades and capturing in Skill Matrix