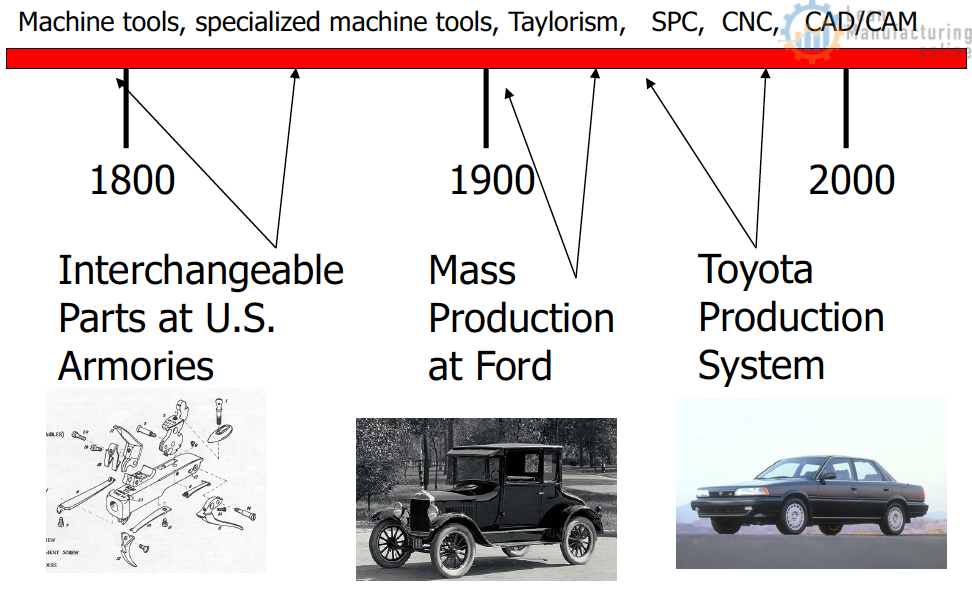
1980’s OPEC oil embargo drives up fuel prices, Japan imports small cars with increased fuel mileage.
How we learned about TPS
- Quality of cars – but not right away
- Pilgrimages – Hayes, Wheelwright, Clark
- Joint ventures – Nummi-Geo…
- Japanese NA operations-Georgetown, KY
- Japanese sages- Ohno, Shingo, Monden
- American translation – “Lean”, J T. Black…
- Consulting firms – Shingijutsu…
Toyota Production System Development History – Taiichi Ohno
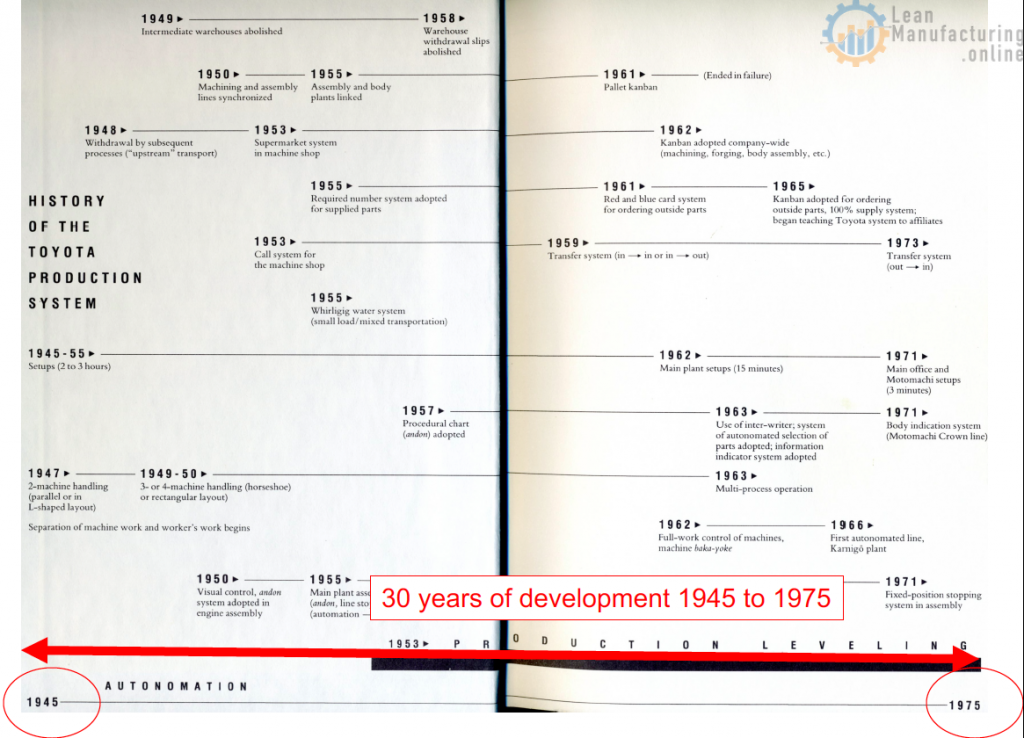
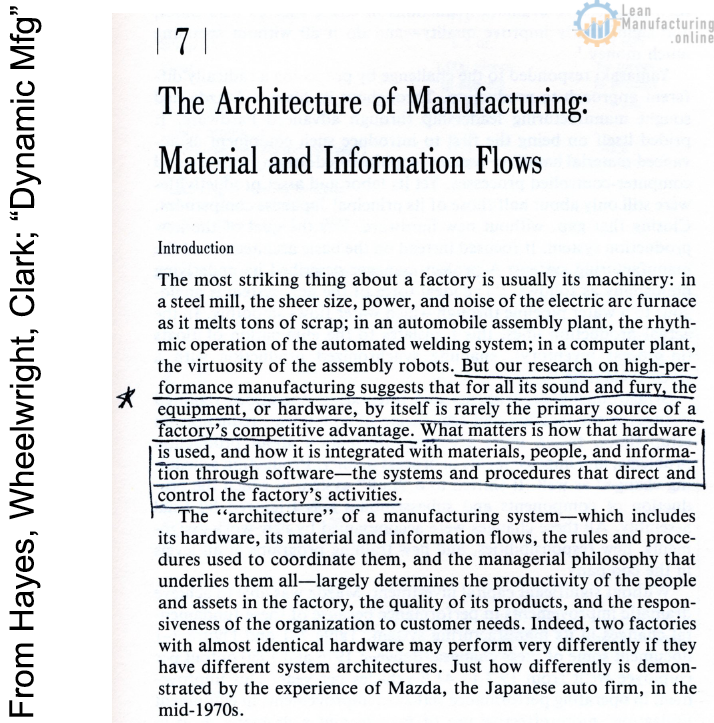
References on the Toyota Production System
- Taiichi Ohno, “The Toyota Production System” Productivity Press 1988
- Shigeo Shingo, “A Study of the Toyota Production System” Productivity Press 1989
- Yasuhiro Monden, “Toyota Production System”, 2nd Ed 1983
- Hayes, Wheelwright, and Clark, “Dynamic Manufacturing” Free Press 1988
- Womack and Jones, “Lean Thinking” Simon and Schuster, 1996
- Spear & Bowen, “The DNA of the TPS’ 1990 HBR 1999
Performance Observations
- Early observations of reliability, after some initial start-up problems;
- IMVP got actual factory level data 1980’s – defect counts – direct labor hours for assembly – the level of automation.
Summary of Assembly Plant Characteristics, Volume Producers, 1989 (Average for Plants in Each Region)
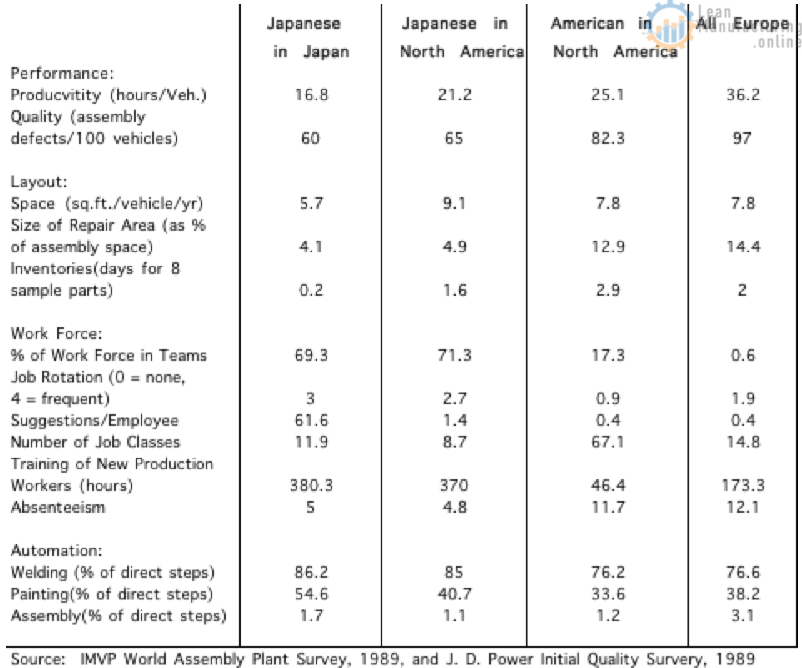
Cost vs Defects
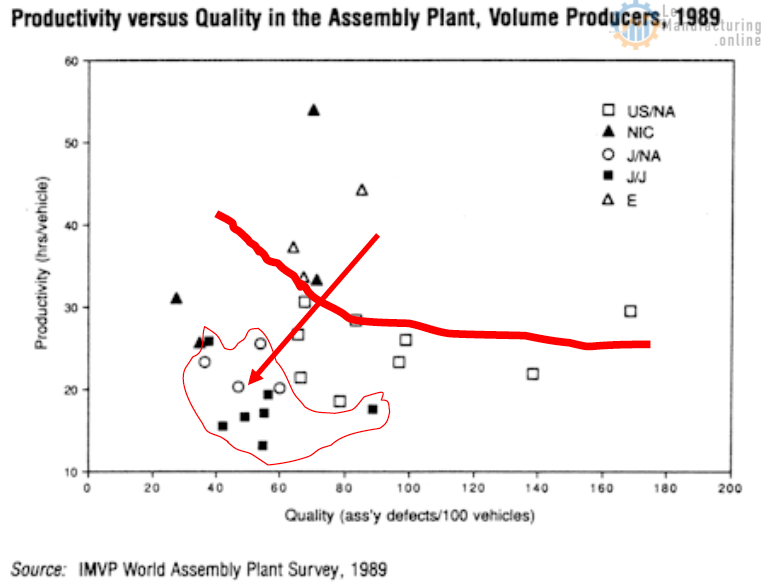
Cost vs Automation
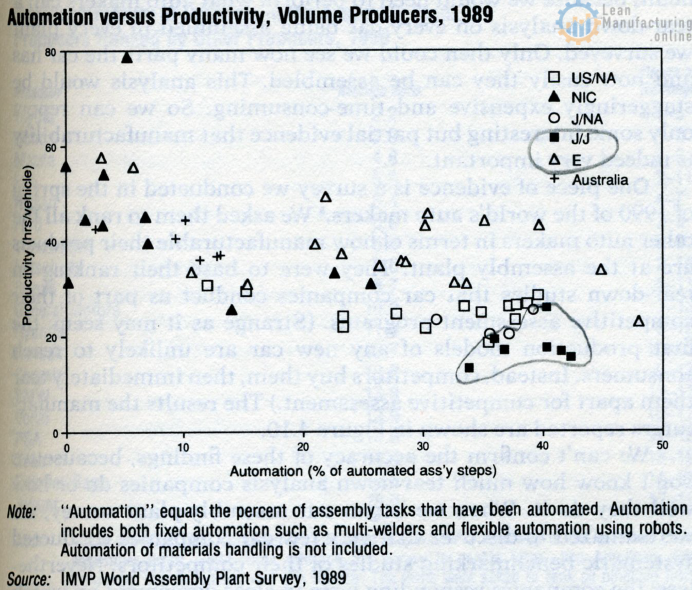
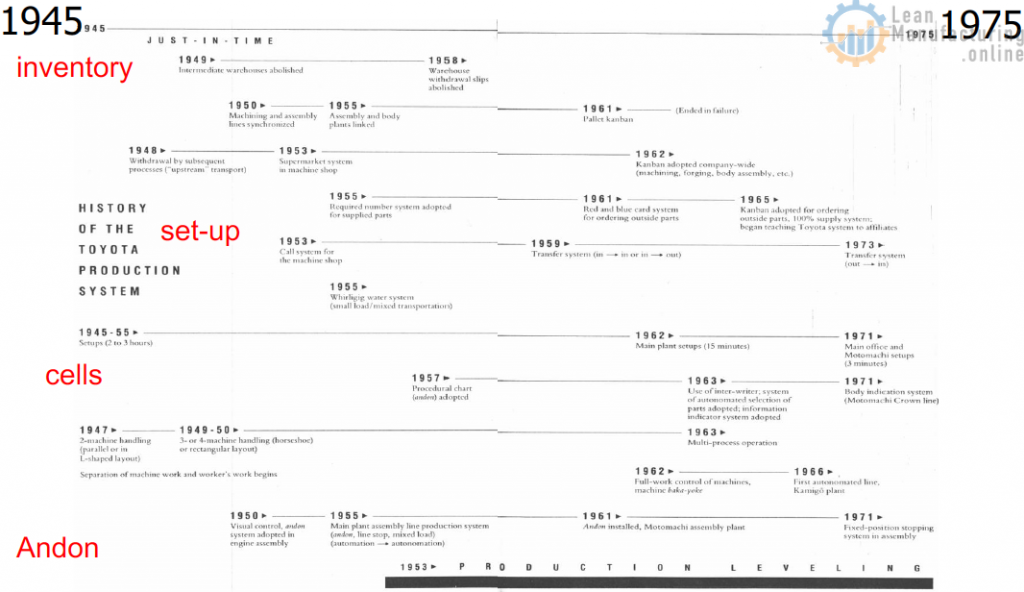
How Cost, Quality, Quantity, and Humanity are improved by the Toyota Production System
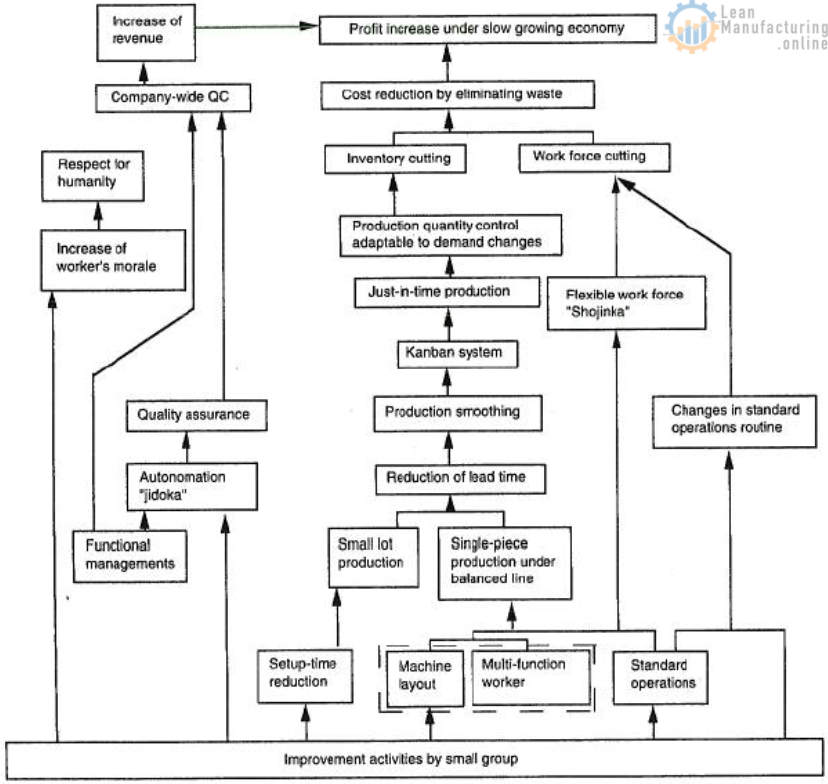
Basic Goal
- To reduce cost by
- Elimination of waste
- Excessive production resources
- Overproduction
- Excessive inventory
- Unnecessary capital investment
- Respect for people
Simulation of a 20 machine, 19 buffer (cap = 10 parts) Transfer line. Each machine with one minute cycle time could produce 4800 parts per week. MTTF 3880 minutes, MTTR 120 minutes.
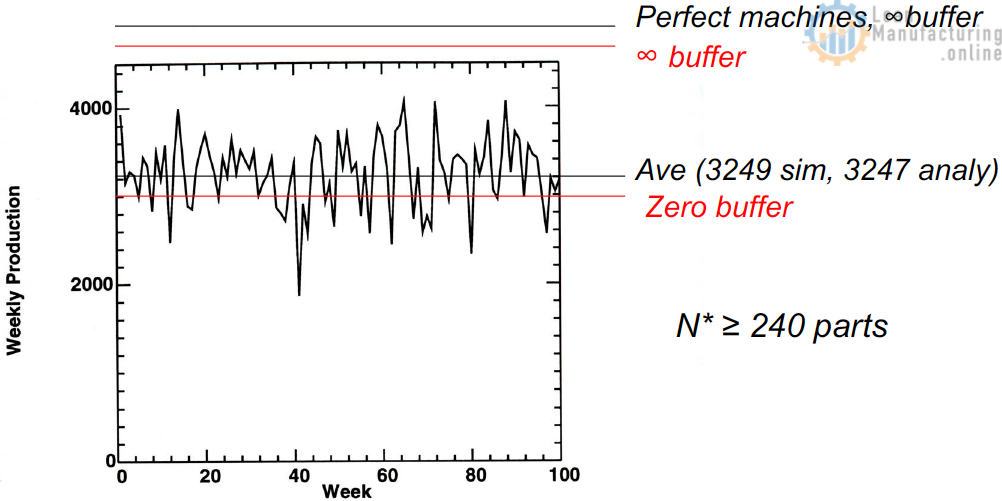
Buffer capacity vs MTTR
- MTTR = 120 minutes
- N* ~ 2 x 120 x 1 part/minute = 240
- 240 x 19 buffers = 4560 (~ one week)
There must be a better way!
CHANGE THINKING, REDUCE VARIATION
What causes variation?
- Quality issues
- Check quality, prevent propagation
- Delivery time issues
- Just in Time, smooth flow, mix models, standard work
- Unavailable resources issues
- Flexible machines and cross-trained workers
Quality Issues
- Make quality problems obvious
- Error checking (Poka Yoke), Pull system
- Reduce WIP, which hides problems
- Stop the line
- Fix it now
- Cooperative problem solving
Delivery Time Issues
- Kanban card: type & quantity needed
- Smooth production
- “Takt” time = available time/demand
- Standardize work
- Reduce set-up
- Design machine layout – TPS cells
- Autonomation – autonomous defect control
Unavailable Resource Issues
- Fast set up
- Single Minute Exchange of Dies (SMED)
- Flexible (general purpose) machines
- Toyota Cells
- Cross-trained workforce
Autonomation…
Monden claims that the word “autonomation” comes from the Japanese word Jidoka. Which has two meanings, the first is automation in the usual sense, to change from a manual process to a machine process. The second meaning is “automatic control of defects”. He says this is the meaning coined by Toyota. This second meaning is sometimes referred to as Ninbennoaru Jidoka, which literally translates into automation with a human mind. Monden goes on to say that “although autonomation often involves some kind of automation, it is not limited to machine processes but can be used in conjunction with manual operations as well. In either case, it is predominantly a technique for detecting and correcting production defects and always incorporates the following devices; in mechanism to detect abnormalities or defects; a mechanism to stop the line or machine when abnormalities or defects occur. When a defect occurs, the line stops, forcing immediate attention to the problem, an investigation into its causes, and initiation of corrective action to prevent similar defects from occurring again…”
Reference: Yasuhiro Monden, Toyota Production System

J T. Black’s 10 Steps
Ref. The Design of the Factory With a Future by J. Temple Black
- Form cells
- Reduce setup
- Integrate quality control
- Integrate preventive maintenance
- Level and balance
- Link cells – KANBAN
- Reduce WIP
- Build vendor programs
- Automate
- Computerize
1. Form Cells. Sequential operations, decouple operator from the machine, parts in families, single-piece flow within the cell
2. Reduce Setup. Externalize setup to reduce down-time during the changeover, standardize set-up
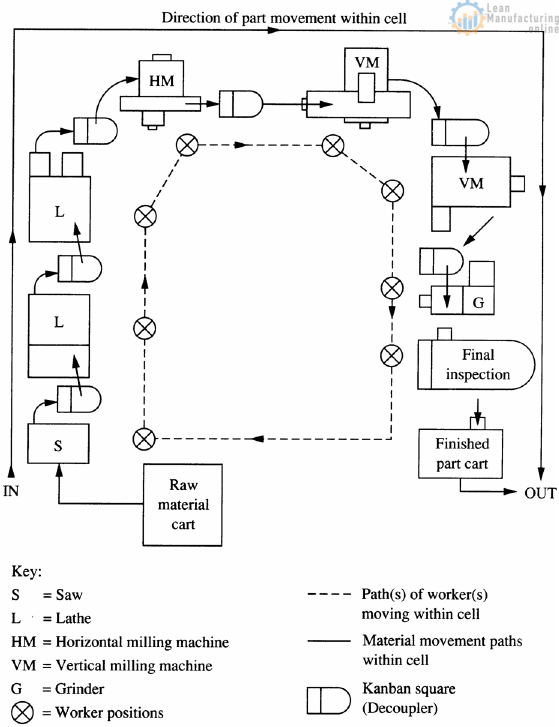
3. Integrate quality control. Check part quality at the cell, Poka Yoke, stop production when parts are bad, make problems visible, Andon – info about work being done…
4. Integrate preventive maintenance. A worker maintains the machine, runs slower, operator owns production of the part
5. Level and balance. Produce to Takt time, reduce batch sizes, smooth production flow, produce in the mix to match demand
6. Link cells – Kanban. Create “pull” system – “Supermarket” System that indicates the status of the system
Balancing and Leveling
- Balanced line: adjust process time for smooth flow “Takt time”
- Leveled Line: each product is produced in the needed distribution.

Pull System at the Supermarket

Pull Systems – The orders arrive at the end of the line and are “pulled” out of the system. WIP between the machines allows quick completion.

- The system stops when there are no orders
- Disruptions are obvious
- Product differentiation at the end
Push Systems – Order (from centralized decision process) arrives at the front of the system and is produced in batches of size “B”. Process time at each step may not be balanced
7. Reduce WIP. Make system reliable, build in mechanisms to self-correct, reduce inventory
8. Build Vendor Program. Propagate low WIP policy to your vendors, reduce # of vendors, make on-time performance part of the expectation
TPS Cell: Example
- Workflow (part separate from worker)
- Standard work (highly specified)
- Production rate flexibility
Machining Cell
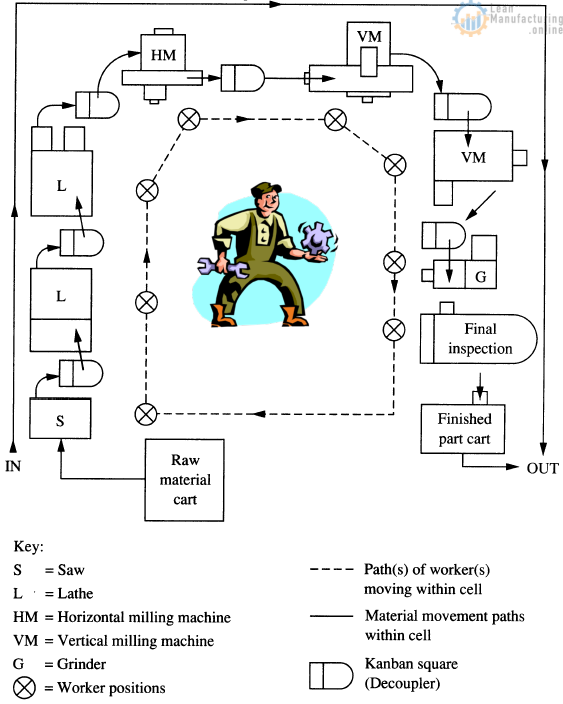
Cell Features
- “Synchronized”, sequential production
- Operator decoupled from individual machines
- Operator integrated into all tasks
- Goal: single piece Flow
- Best with single-cycle automatics, but can be done manually too
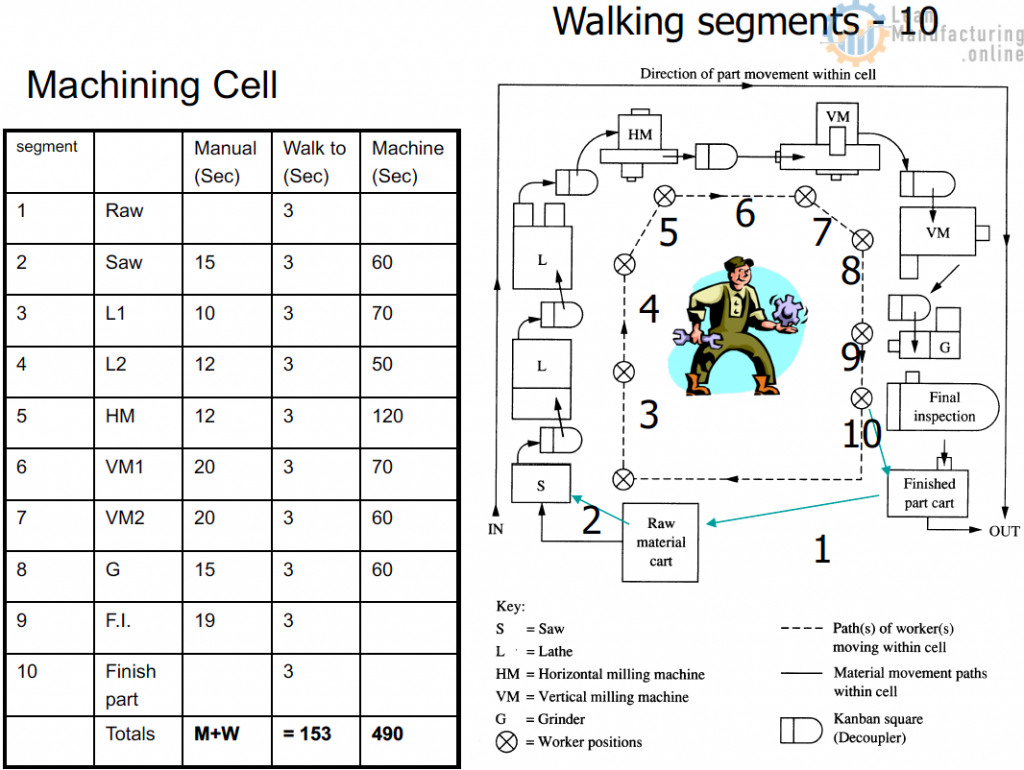
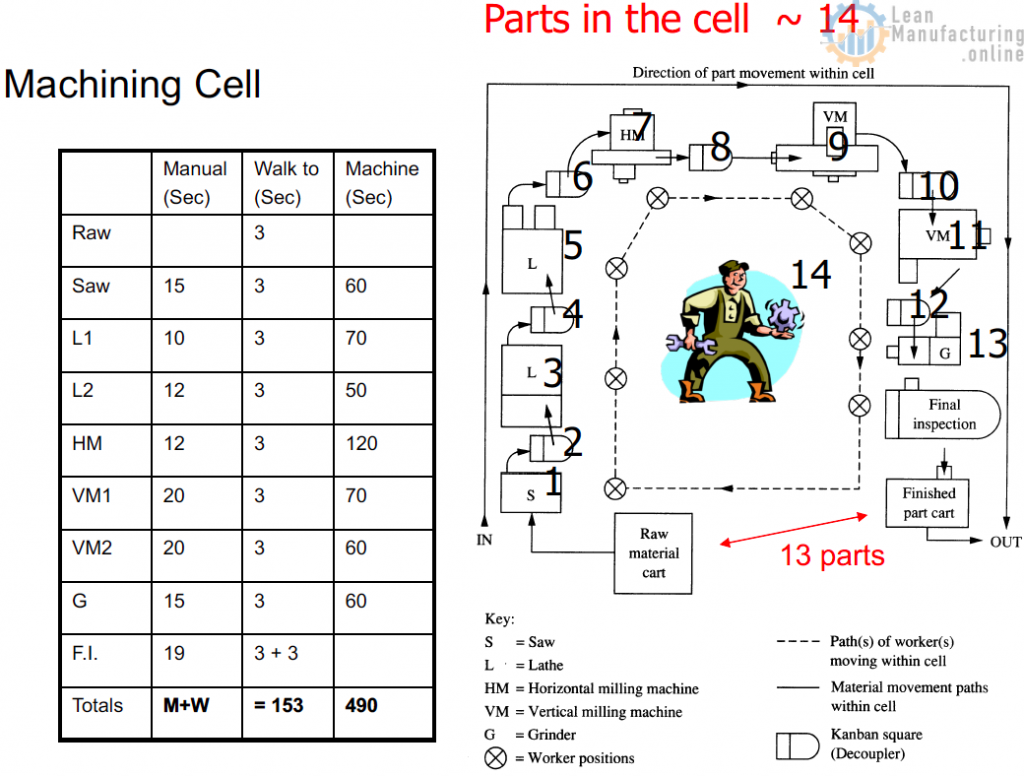
Standard Work for Cell

Cell produces one part every 153 sec
Note: machine time Max (MTj) < cycle time CT
i.e. 120+12 < 153
TPS Cell
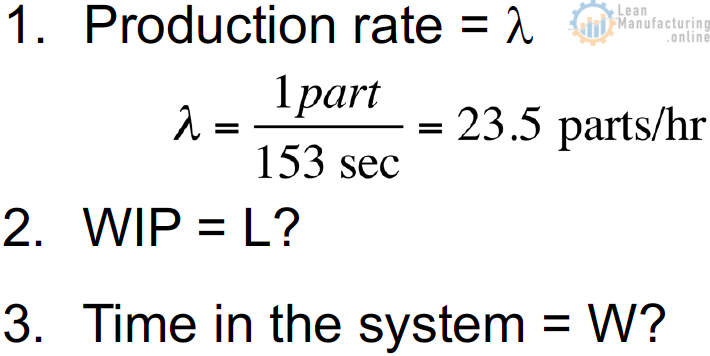
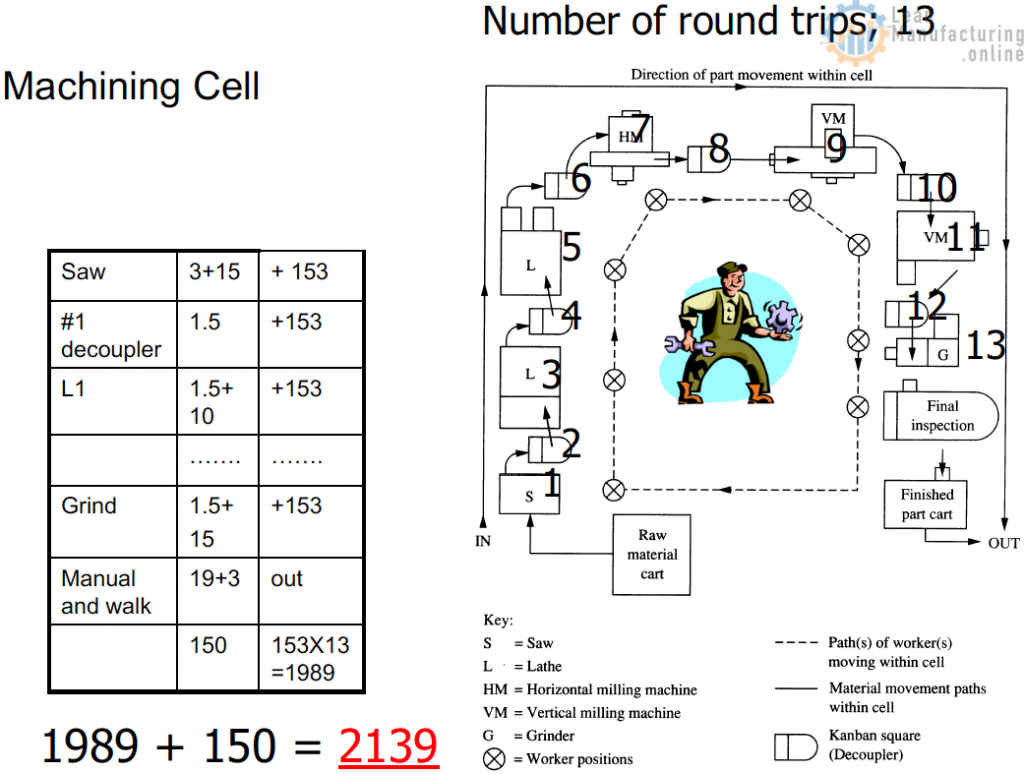
By Little’s Law
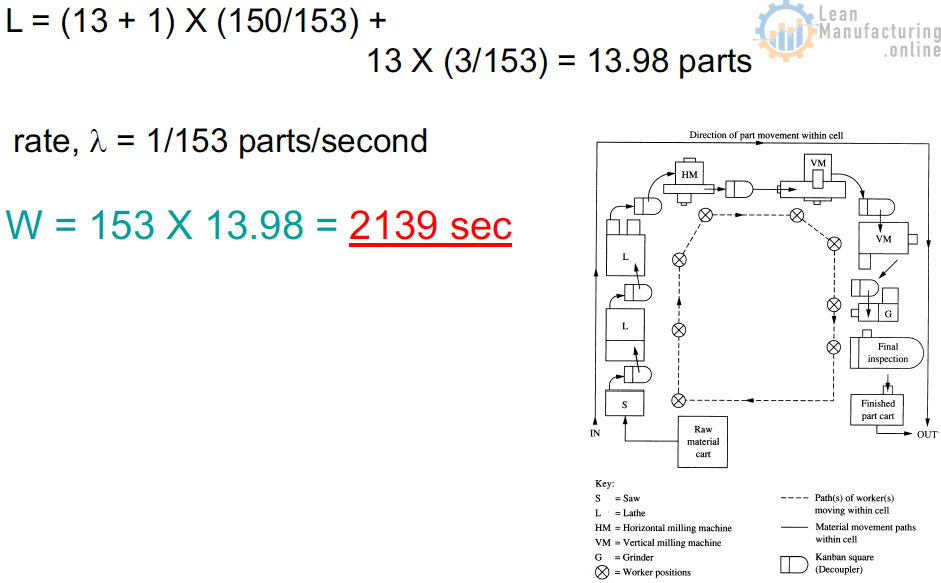
Increase production rate:
- a) add worker to the cell
- b) modify machine bottlenecks

What is the production rate for this new arrangement?
Check max(MTj) < CT
Worker 1; 80 = 80
Worker 2; 12+120 >79
One part every 132 seconds. We are limited by the HM (horizontal mill)

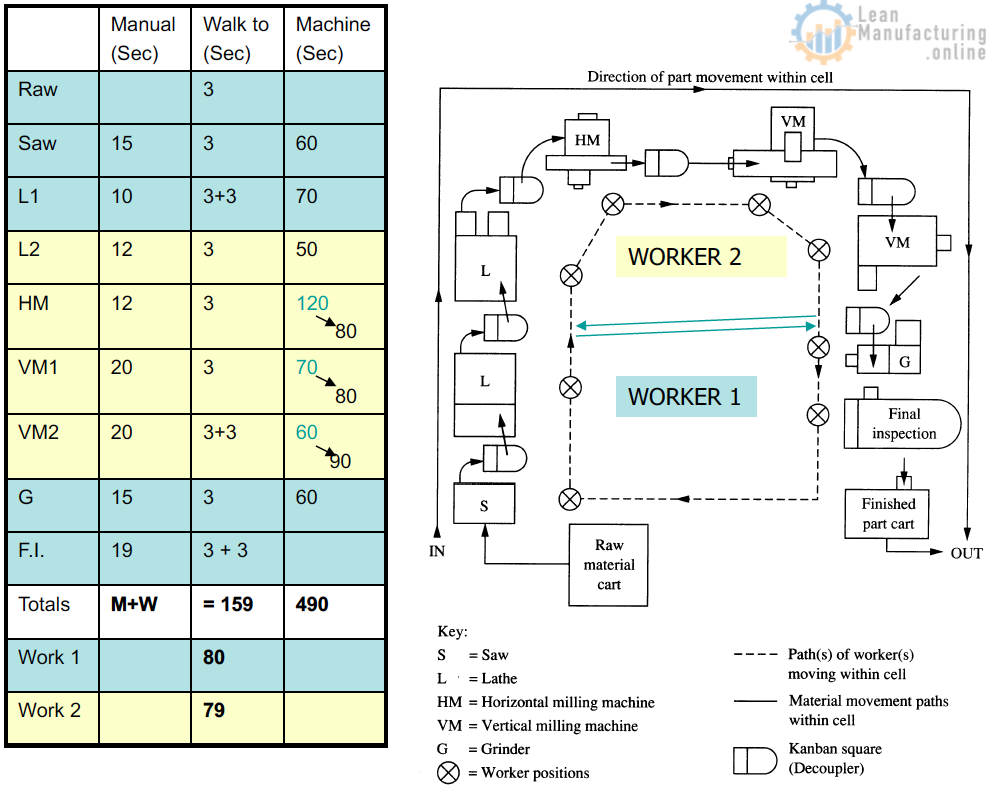
Standard Work for Worker #2
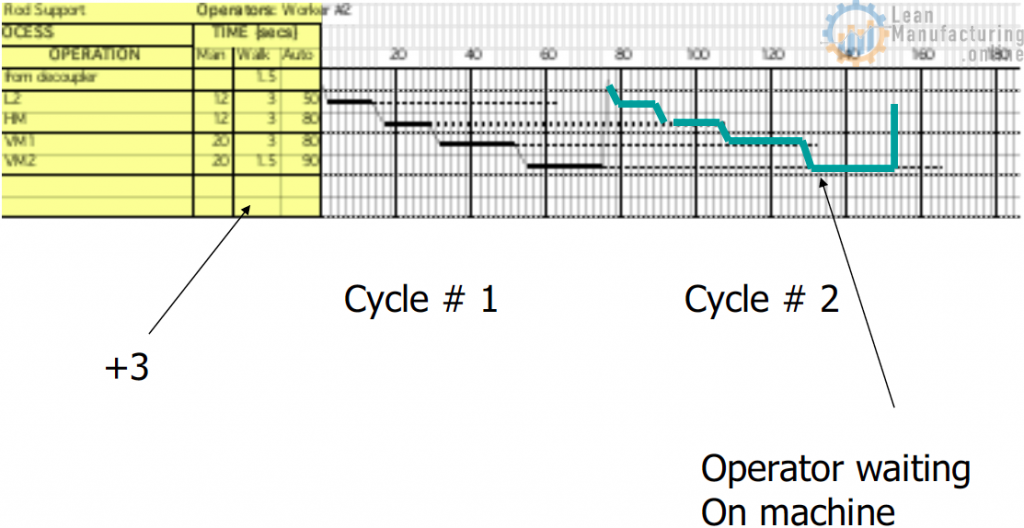
What is the new production rate?
Check max(MTj) < CT
Worker 1; 80 = 80
Worker 2; 110 > 79
Hence Worker #2 will be waiting on Vertical Mill #2
What is the new production Rate?
- The new production rate is; one part every 110 sec
- Pro and Cons; Worker “idle”, can’t speed up by adding additional worker
- Design for flexibility make; Max(MTj) < CT/2
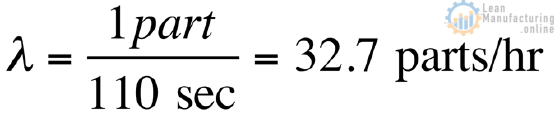

TPS cell summary
- Original cell – 23.5 parts/hr
- Additional worker- 27.3 parts/hr
- +Shift work- 32.7 parts/hr
- ++ add additional VM 40 parts/hr
TPS Implementation
- Physical part (machine placement, standard work, etc)
- Work practices and people issues
- Supply-chain part
- Corporate Strategy (trust, job security)
Is there a best way to build a car?
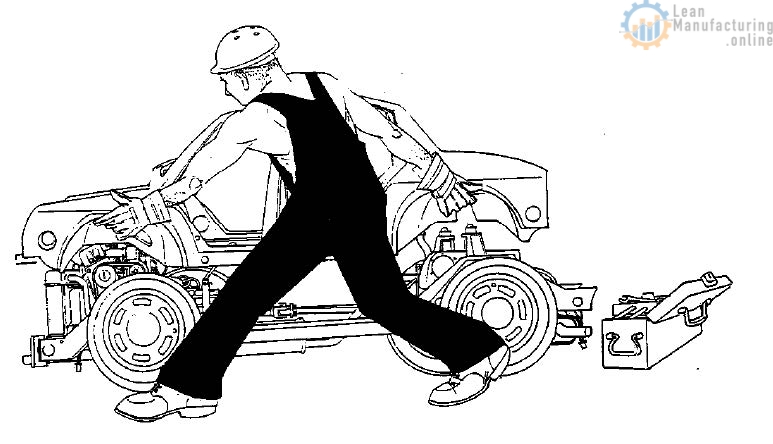
• Maccoby HBR 1997
• Other Ref: “Just Another Car Factory” Rinehart, Huxley, and Robertson
“Farewell to the Factory”, Milkman
Work practices and people issues
- “Failed” TPS attempts:
- GM Linden NJ
- CAMI, GM-Suzuki, ON Canada.
- Successes GM NUMMI, Saturn. Toyota Georgetown, KY
- Maccoby HBR 1997
- Other Ref: “Just Another Car Factory” Rinehart, Huxley, and Robertson, “Farewell to the Factory”, Milkman
According to Maccoby’s Review
- Failure Examples:
- failures at middle management
- pressure from above to meet targets, lack of trust from below, but…
- both plants adopted some aspects of lean, and
- both plants improved
NUMMI and Georgetown
- workers have a different attitude
- do not fear elimination
- play an important role
- …go to Georgetown and find out
TPS Summary
- High quality and low-cost paradigm shift
- Many elements of the system
- Make system observable
- Produce to demand
- Study defects and eliminate
- Institutionalize change
- Trust
- Many companies have imitated TPS
Key Elements for New Manufacturing Systems
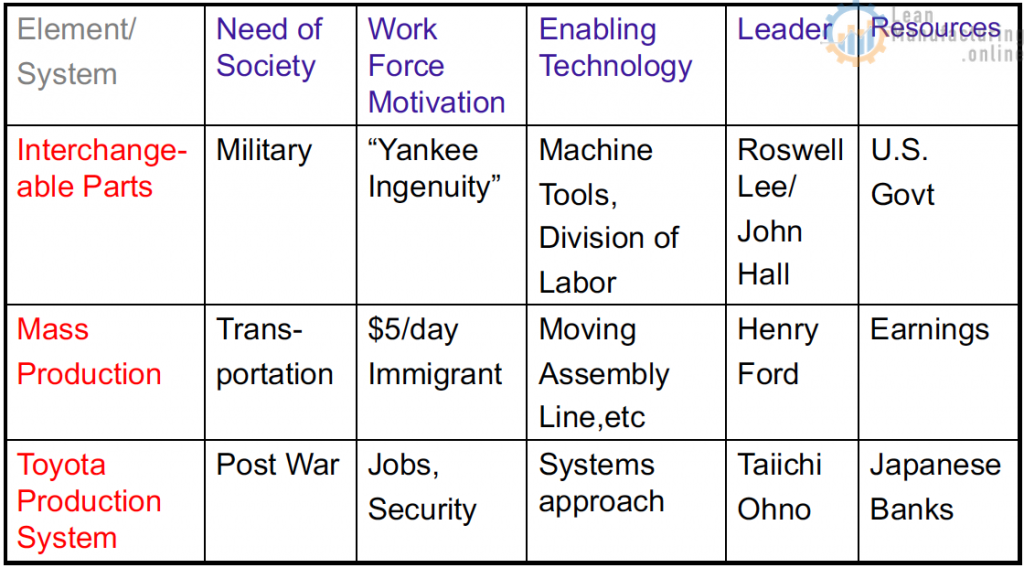
- James Womack, Daniel T. Jones, and Daniel Roos, The Machine that Changed the World, 1990, Chapters 3 and 4
- J T. Black “The Factory with a Future” Chapters 2 & 4
- Yasuhiro Moden Chapter 1
- Michael Maccoby, “Is There a Best Way to Build a Car?” HBR Nov-Dec 1997
“The DNA of the TPS”
- Spear and Bowen
- 4 years 40 plants
- HBR Sept-Oct 1999
- Four Rules:
- Rule 1: All work shall be highly specified as to the content, sequence, timing, and outcome.
- Rule 2: Every customer-supplier connection must be direct, and there must be an unambiguous yes-or-no way to send requests and receive responses.
- Rule 3: The pathway for every product and service must be simple and direct.
- Rule 4: Any improvement must be made per the scientific method, under the guidance of a teacher, at the lowest possible level in the organization.
Spear and Bowen
Very good