Unlocking the True Potential of Your Production Line
In the world of manufacturing, efficiency is everything. To ensure that operations run smoothly and that companies can get the most out of their equipment, a metric known as Overall Equipment Effectiveness (OEE) is used to evaluate and improve productivity. This valuable tool can help businesses identify areas of inefficiency, minimize downtime, and boost overall performance.
In this blog post, we will delve into the concept of OEE, discussing its importance in manufacturing, its components, and how it can be used to enhance production processes. By understanding and implementing this powerful metric, manufacturers can unlock the true potential of their production lines.
The Importance of OEE
OEE is a crucial metric for measuring the performance of a manufacturing process. Evaluating a production line’s overall efficiency provides actionable insights that can help companies identify bottlenecks, reduce waste, and ultimately increase productivity.
Some of the key benefits of using OEE include:
- Identifying inefficiencies: OEE allows manufacturers to pinpoint areas where improvements can be made, helping to reduce waste and increase productivity.
- Benchmarking performance: By comparing OEE scores with industry standards, companies can gauge their competitive standing and set targets for improvement.
- Monitoring equipment health: Regularly measuring OEE can help detect issues with machinery before they escalate, reducing downtime and maintenance costs.
- Facilitating continuous improvement: OEE provides a quantitative basis for monitoring progress and driving ongoing improvements in production processes.
Components of OEE
OEE is calculated using three key components: Availability, Performance, and Quality. These factors represent different aspects of the manufacturing process and can be combined to create a comprehensive picture of overall efficiency.
- Availability: This metric measures the proportion of scheduled production time a machine is available for use. Availability is affected by breakdowns, maintenance, and changeovers and is calculated by dividing the actual production time by the scheduled production time.
- Performance: Performance evaluates how quickly a machine produces parts compared to its optimal speed. This component accounts for factors such as machine slowdowns and minor stops. Performance is calculated by dividing the total number of parts produced by the product by the scheduled production time and the ideal cycle time.
- Quality: Quality measures the proportion of goods produced compared to the total number of parts produced. This component considers defects and rework and is calculated by dividing the number of good parts by the total number of parts produced.
To calculate the OEE score, multiply Availability, Performance, and Quality.
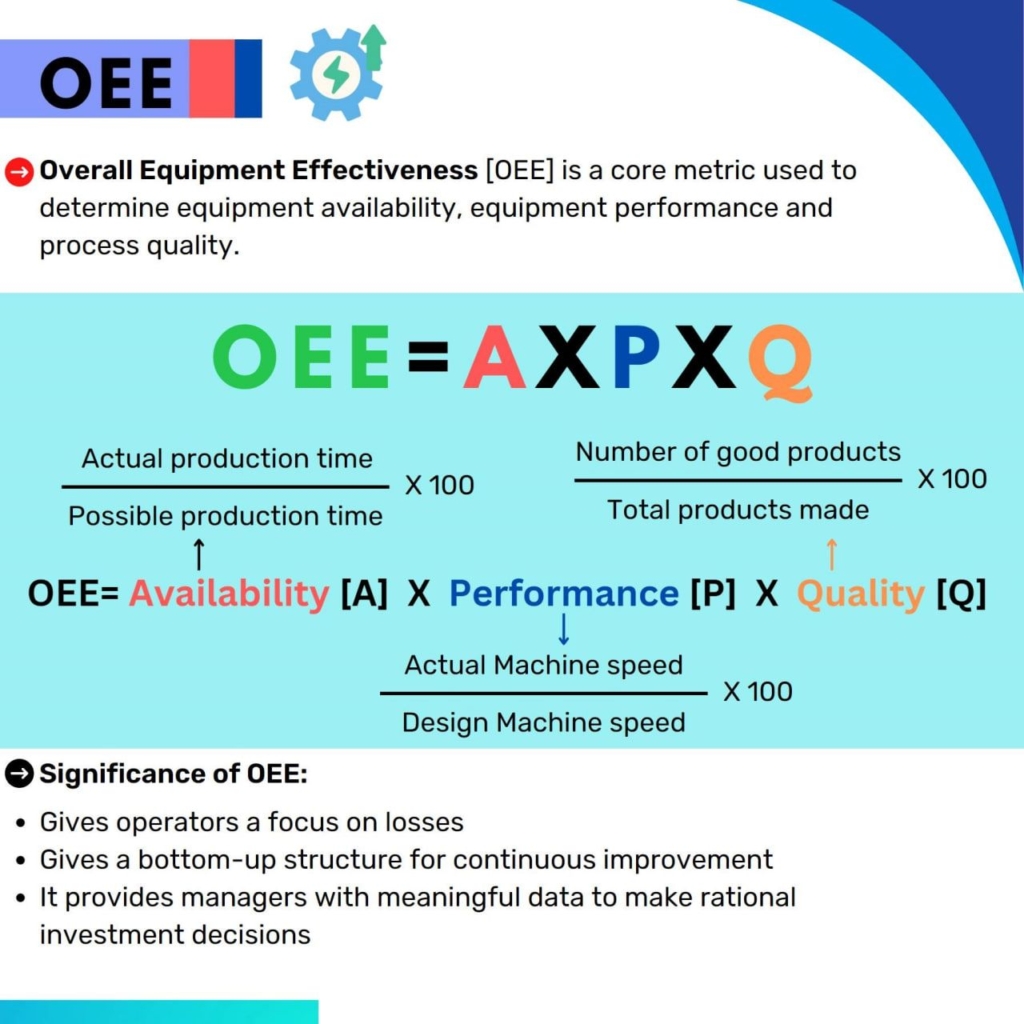
Using OEE to Enhance Production Processes
Once a company has calculated its OEE score, it can use this information to drive improvements in the manufacturing process. Here are a few strategies for doing so:
- Analyze data: By examining the individual components of OEE, companies can identify specific areas of inefficiency and focus their improvement efforts accordingly.
- Set targets: Establishing target OEE scores can help companies stay competitive and drive continuous improvement. Setting realistic, achievable targets that reflect industry benchmarks and a company’s unique circumstances is essential.
- Implement improvement initiatives: Companies can use the insights from OEE analysis to develop and implement targeted improvement initiatives, such as preventive maintenance programs, operator training, and equipment upgrades.
- Monitor progress: Regularly measuring OEE and tracking progress over time can help companies ensure that their improvement efforts are effective and drive sustained gains in efficiency.
Conclusion
Overall Equipment Effectiveness is a powerful tool that can help manufacturers optimize their production processes and unlock the true potential of their equipment. By understanding and leveraging this metric, businesses can identify inefficiencies, set targets for improvement, and implement targeted initiatives to boost productivity and performance. Companies can ensure that their improvement efforts yield tangible, sustainable results by regularly monitoring OEE scores and tracking progress over time.
Great. Thank you for your support