The steps involved in the activity will now be explained in detail. This practical program for reducing failures consists of five strategies implemented in five phases, expressed in the form of seven steps.
The seven steps are intensely practical – the important thing is to work out precisely what needs to be done. This is essential because no action takes place on the basis of abstract thinking alone.
Step 1: Assess the current situation
(1) Aims
This activity could be described as initial cleaning by maintenance engineers; as well as identifying every minor equipment defect that could be a source of failure, it enables them to check for themselves through failure analysis the reasons why each failure was bound to occur. It also allows them to develop their understanding of how the equipment is constructed and how it works.
(2) Main activities
- Identifying and correcting visible and hidden equipment defects
- Tagging minor equipment defects and removing the tags by correcting the defects or improving the equipment (simple defects are rectified at this step)
- Analyzing failures (in particular, stratifying the causes of failures)
- Analyze each failure on a separate sheet of paper and classify its cause as inadequate basic conditions, inadequate operating conditions, insufficient restoration, leaving deterioration untended, sporadic failure, design weakness, maintenance error, operating error, etc.
- Monitoring the number of tags applied and removed
- Collecting baseline data on the number of sporadic failures, quality defect rates, MTBF and MTTR
- Using failure maps
- To lead into Step 2, formulating an improvement plan for the equipment defects identified
(3) Summary
By identifying concealed and obvious equipment defects and analyzing failures, determine what kinds of losses are concentrated on which parts of the equipment, and acquire hands-on experience of the extent of the deterioration under which the equipment is being operated. Also, to lead into Step 2 by formulating an improvement plan for the equipment defects identified.
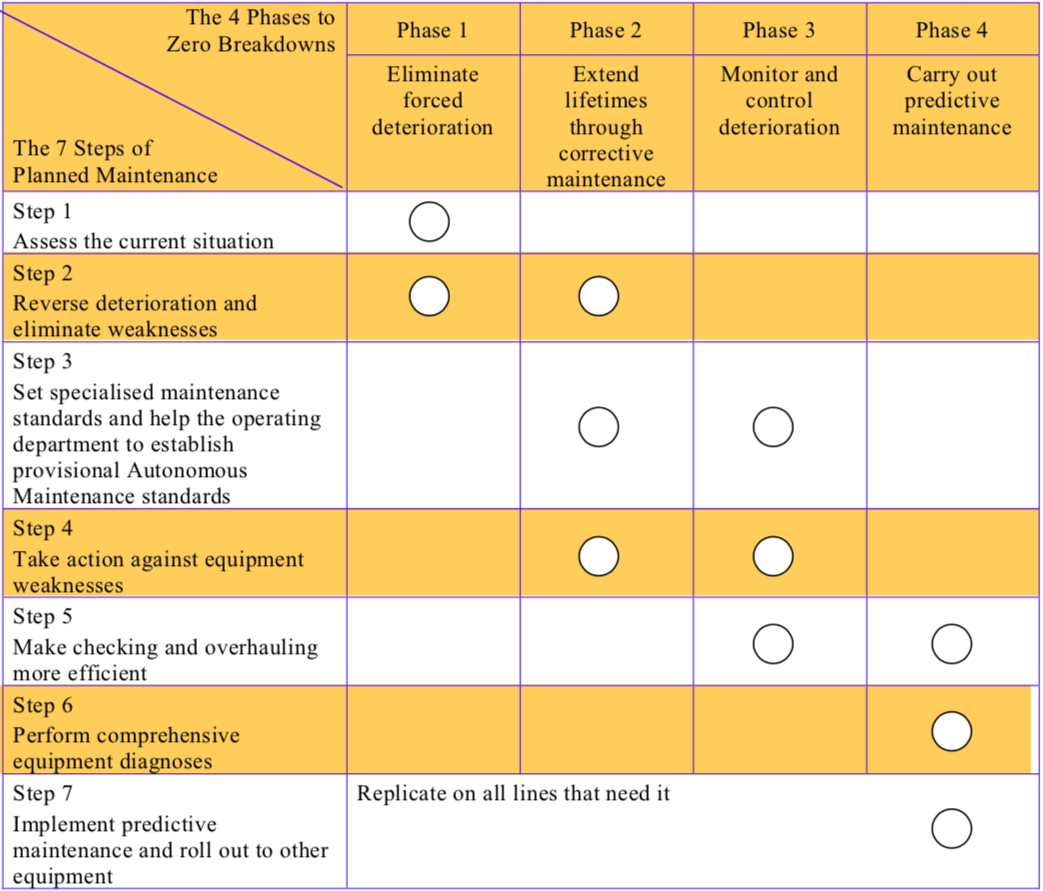
Step 2: Reverse deterioration and eliminate weaknesses
(1) Aims
To restore the equipment and make improvements in order to eliminate the problems identified in Step 1. To continue analyzing failures and painstakingly tracking down their causes to ensure they can be prevented from recurring. They are also carrying out corrective maintenance to prolong the lifetimes of short-lived sections and components at the same time as raising the level of maintenance skill.
(2) Main activities
- Eliminating forced deterioration and correcting existing deterioration. Think about restoring before improving
- Painstakingly tracking down the causes of failures (using techniques such as Why- Why Analysis, FTA, FMEA, and P-M Analysis)
- Ensuring that no failures can recur
- Carrying out corrective maintenance to prolong the lifetimes of short-lived sections and components
- Considering handing over responsibility for some checks to Autonomous Maintenance
- Stratifying restoration and improvements, and monitoring progress against plans Improving the maintenance department’s maintenance skills
- Identifying which parts are to be maintained by means of standards (leading into Step 3)
(3) Summary
In this step, the equipment is brought back into tip-top condition through restoration and improvement, and failures and quality defects are reduced dramatically. Short-lived components are also made to last longer through corrective maintenance.
Step 3: Set specialized maintenance standards and help the operating department to establish provisional Autonomous Maintenance standards
(1) Aims
To keep the equipment in the improved condition achieved in Steps 1 and 2, the maintenance work must be organized in the form of standards. Preventive maintenance is then started in accordance with these. To begin with, periodic (time-based) maintenance is used.
(2) Main activities
- Examine each machine in turn and identify the parts that should be subjected to preventive maintenance
- Also identify everything that needs to be cleaned, lubricated, or otherwise attended to as part of routine daily maintenance
- Draw up a preventive maintenance (mainly periodic maintenance) standard for each machine
- Specify exactly what the operators are supposed to do under Autonomous Maintenance and what the maintenance engineers are supposed to do under Effective Maintenance
- Start by using provisional standards for checking and replacement intervals
- Prepare a maintenance calendar and begin faithfully implementing whatever has been decided
(3) Summary
The main task in Effective Maintenance is to overhaul the equipment based on the results of checking and inspecting it. Begin by identifying the routine daily maintenance tasks that must be performed (including cleaning and lubricating) and indicate the standards which are responsible for carrying out these tasks. Preventive maintenance should start with periodic (time-based) maintenance; the first thing that needs to be done is to set up and begin implementing a system for maintaining the equipment and replacing parts at specified intervals.
Step 4: Take action against equipment weaknesses
(1) Aims
Although we start by trying to eliminate “function-stoppage failures” (catastrophic failures that cause a machine to stop working entirely), our eventual goal is also to eliminate “function-reduction failures” (losses where the machine keeps on working but at a lower level of performance). In other words, we want to maintain the equipment in such a way as to eliminate product quality defects as well as breakdowns. In this step, we identify the relationships between quality defects and the functional sections or components of the machine and try to restore these sections or components to perfect condition by comprehensive checking and overhauling. This is what is meant by performing quality maintenance.
(2) Main activities
- Continue to deepen the understanding of how the equipment is constructed and how it works
- Learn how, and in accordance with what principles, the machine processes the product
- Perform a comprehensive inspection with the aim of identifying minor defects in everything associated with the equipment, including jigs, tools, fixtures, and so on
- Clearly understand the product’s quality characteristics
- Keep investigating until all the equipment components that determine the quality of the product (i.e. the parts to be maintained) have been identified.
- In practice, this means pinpointing the quality components through the use of P-M Analysis
(3) Summary
Given that quality is built into the product by the equipment, equipment maintenance must also significantly affect product quality. This step is essential to identify the relationships between the equipment’s functional sections and components and the product’s quality characteristics. From now on, equipment maintenance must incorporate quality maintenance per these principles. P-M Analysis is a potent tool for clarifying the relevant relationships.
Step 5: Make checking and overhauling more efficient
(1) Aims
To ensure that preventive maintenance (principally periodic maintenance) is faithfully carried out and reduce the labour-hours required by adding maintenance tasks relating to the quality function sections and components identified in Step 4 into the provisional standards prepared in Step 3 and making these tasks more accessible and more efficient to complete.
(2) Main activities
- Draw up a QM Matrix showing the relationships between quality defects and equipment functions
- Ensure that all the items to be maintained and controlled are incorporated into the Effective Maintenance and Autonomous Maintenance standards and faithfully implemented
- Improve awkward checks to make them easier to perform
- Continue to develop the maintenance calendar, consolidate checks (integrate several checks into a single one to reduce their number), and extend the intervals between checks
- Increase reliability by increasing the number of periodic maintenance items on the basis of deterioration measurements
- Reduce maintenance costs by overhauling at the unit level and only replacing those parts that have deteriorated beyond the acceptable limit
- Reduce the time and cost of overhauls by standardizing parts, etc.
- Begin researching and utilizing commercially available diagnostic equipment
- Promote various management techniques (spare-parts management, maintenance planning management, maintenance information management, maintenance budget management, etc.)
(3) Summary
This step consists of creating a system for the maintenance tasks and effecting improvements to streamline those tasks. A program of inspection and repair is rolled out in accordance with monthly and weekly maintenance schedules based on a maintenance calendar. In conjunction with this, various management activities (spare- parts management, maintenance planning management, maintenance information management, maintenance budget management, and so on) for promoting Effective Maintenance are carried out. The study of predictive maintenance is also commenced with a view to compensating for the weaknesses in periodic maintenance.
Step 6: Perform comprehensive equipment diagnoses
(1) Aims
In this step, equipment diagnostics are employed to add predictive maintenance to the maintenance mix to monitor trends in the state of deterioration of the equipment and identify the optimal point in time for maintenance. Predictive maintenance is used for equipment sections that have failed seriously in the past, or that would cause severe damage if they failed now.
(2) Main activities
• Identify sections of the equipment that have failed seriously in the past or that would cause severe damage if they failed now
• Identify the parts of each machine that are to be subjected to predictive maintenance
• Find out what diagnostic equipment is available on the market and make use of it
• Study the patterns of natural deterioration and the parameters available for measuring it
• Use simple diagnosis to perform trend monitoring and periodically carry out precision diagnosis. Monitor the data.
• Try to develop the company’s own original diagnostic devices (using various types of the sensor)
• Begin by using vibration diagnosis to detect abnormal levels of vibration
• Develop equipment diagnostic experts
• Train all maintenance engineers in equipment diagnostics
(3) Summary
The primary purpose of predictive maintenance is to assess how much longer a piece of equipment will keep working. As well as using hands-on activities to develop the ability to judge how much life is left in a machine or component, the subject should be studied thoroughly to acquire the ability to establish the best possible diagnostic techniques for the company.
Step 7: Implement predictive maintenance and roll out to other equipment
(1) Aims
The program is then rolled out to all the equipment that requires it, based on the experience and results obtained so far. To accomplish this effectively, the focus should be kept on the key points of the steps carried out so far. In other words, the equipment’s level of restoration and improvement should be checked, maintenance standards should be formulated, and time-based and predictive maintenance should be applied to the parts that need it.
(2) Main activities
- The maintenance department prepares inspection and maintenance standards for all existing equipment that requires them
- The rollout procedure is as follows:
- Survey the level of restoration and improvement of the equipment being addressed
- Painstakingly improve any parts that have been neglected or have not been dealt with satisfactorily
- Identify every item to be checked, including those relating to product quality
- Prepare the inspection and repair standards
- Put together a maintenance calendar and carry out preventive maintenance
- Implement the maintenance standards as far as possible on all equipment that requires them
- Continue to maintain the equipment in accordance with the standards while progressively enhancing those standards
(3) Summary
The lines that require this approach include all equipment subject to preventive maintenance as identified when the equipment was prioritized.