“Tell me, and I will forget
Teach me, and I might remember
Involve me, and I learn.”
Involving team members from all levels of the organization is key to the success of any organizational initiative, and visualization helps you achieve just that.
What does success mean to you? How do you know that you have achieved it? Defining this would lead us to the development of Key Performance Indicators (KPIs). KPIs need to be defined at various levels so that every level of the organization can have an impact.

This might be too vague a target for the working level. What does the working level need to do daily to help achieve this target at the end of the month? How does the working level involve in achieving the big picture?
That is when the next level of KPI comes into the picture: Process KPI.
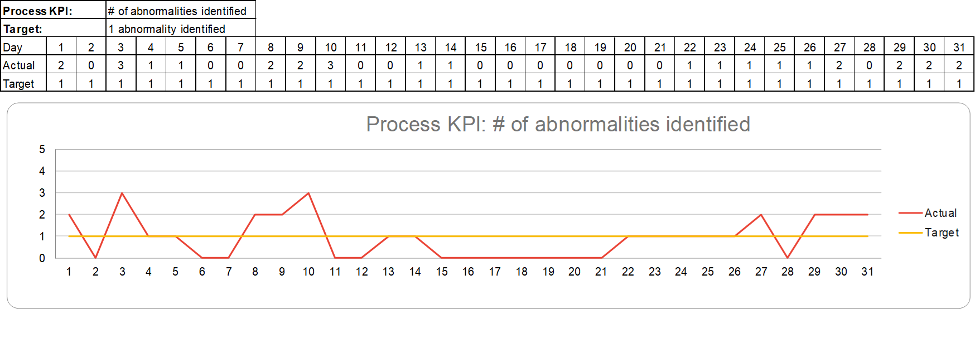
Process KPI is measured daily or every shift, depending on the plant’s operations. This KPI tells the working level what they need to do daily in order to achieve the monthly target of the Main KPI. In other words, it tells them how they are contributing to the ‘big picture’ of operating a safe plant.
If required, another level of KPI called the Sub KPI can be used to motivate middle management. Process KPI contributes to the Sub KPI, and Sub KPI, in turn, contributes to the Main KPI. For our example, the middle management charts the number of accidents for the process they own. This is how strategy connection can be achieved. Every level of the organization contributes to the achievement of KPIs. Every team member knows and understands the ‘purpose’ of their activity and is made to feel important by telling them they are part of the big picture. This is how the visualization of KPIs creates involvement and drives the engagement of employees.
Out of sight is out of mind, don’t let your team lose sight of the goal and visualize your KPIs today!
What type of visualization do you practice in your organization? I will be happy to receive your comments.
About the author
Swathi Mohan
Swathi Mohan is a sought-after continuous improvement expert with over 12 years of experience in the manufacturing industry. Certified Lean Six Sigma Black Belt and a highly influential adult educator. Root cause analysis, Toyota problem-solving methodology, lean systems implementation and total Productive Maintenance are some of her areas of expertise. Feel free to get in touch with her to get help with solving your operational problems.