Shadow boards are tools which help organize workstations, setup carts, tool cribs and practically anything that needs organizing!
Let me take you through an example of how a company increased their productivity by 35% just by installing a simple shadow board.
Shadow boards help find a home for every object; in other words, they help you implement the second step of 5S – Straighten.
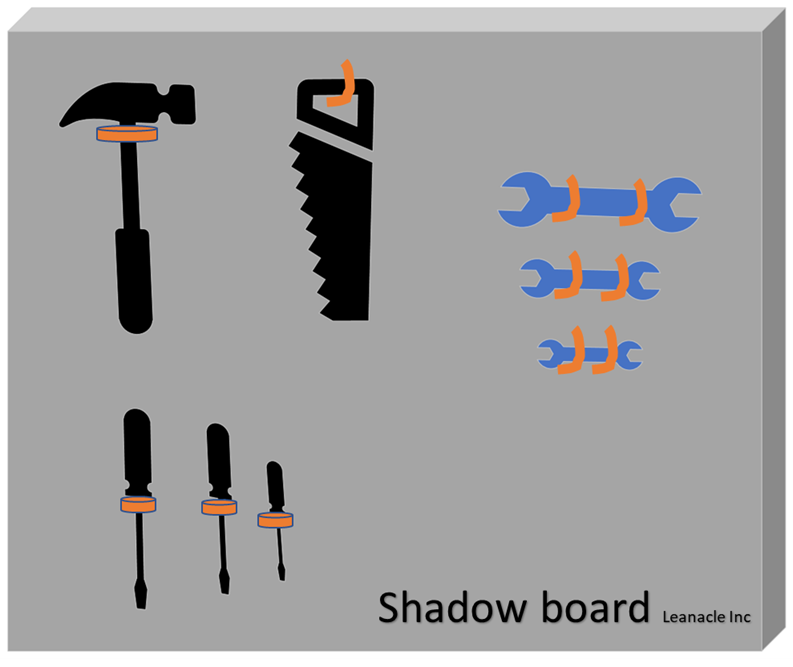
One of the welding machines in the plant was identified as a bottleneck operation in an automotive plant. When analyzed, it was found that the downtime caused by weld tip changes was enormously high. In a shift, 12 tip changes had to be done to meet the production target. Every tip change process would take 14 minutes on average. The team was surprised by this number as the tip change was quite a simple task which could be done within 2 minutes.
Was the operator not trained to do these tip changes? When we did a simulation trial, we found that most operators were able to perform a tip change within 2 minutes. So, what was causing the delay?
Upon further investigation, we found that, on average, the operators spent 10 minutes looking for the tools and ‘good’ tips to perform the tip change! Tools and tips were either taken by other operators as they had similar machines, or they would just get lost in the sea of parts, inventory, documents and whatnot!
This led the team to design a shadow board to find a home for each tool and have a bin on the shadow board to store good tips and bad tips for recycling. This simple idea helped them get 136 parts more/ shift! There was another aspect of savings in the form of recycled copper tips, which would just get lost in the past. Now not everything that can be counted counts, and not everything that counts can be counted! Yes, I am talking about the intangible benefits. Installing the shadow boards resulted in a huge boost in employee morale as it saved them from the frustration of looking for tools and tips. It also triggered a chain reaction where employees from other areas came up with several ideas to improve their workstations; in other words, ‘Kaizen mind’ development started taking place. If I were to pick the biggest benefit of this activity, I would pick the ‘Kaizen mind development,’ as there is no limit to the continuous improvement that can take place once it is triggered.
Key to the successful implementation of 5S, or any lean tool for that matter, is developing it to suit the process in question and deploying it in the right place. If you are struggling with the implementation or not seeing the benefits you expect to see, feel free to get in touch with us. We will be more than happy to assist your team with the implementation.
Let’s cast some shadows, for there is no light without a shadow!
About the author
Swathi Mohan
Swathi Mohan is a sought-after continuous improvement expert with over 12 years of experience in the manufacturing industry. Certified Lean Six Sigma Black Belt and a highly influential adult educator. Root cause analysis, Toyota problem-solving methodology, lean systems implementation and total Productive Maintenance are some of her areas of expertise. She provides consultation services to enable manufacturers to find time to do what they love by helping them establish world-class processes through Leanacle Inc.

Leanacle Inc
Helping you reach the pinnacle of operational excellence