When a bearing is used under ideal conditions, it will only be damaged by rolling fatigue. Damage due to rolling fatigue may occur very early, however.
If damage is found on a bearing, it is important to examine the phenomenon properly and identify the causes, even if the damage is very small. In addition, it is essential to examine it comprehensively, checking not only the bearing but also the shaft, housing and lubricant.
To identify the cause of the bearing damage, it is required to have sufficient knowledge and expertise regarding bearings and lubrication, to be familiar with the characteristics of the application machine, and to be well-informed of the conditions under which the bearing is installed and of the past records of the machine operation.
1. Flaking
Flaking is a phenomenon when material is removed in flakes from a surface layer of the bearing raceways or rolling elements due to rolling fatigue.
This phenomenon is generally attributed to the approaching end of bearing service life.
However, if flaking occurs at early stages of bearing service life, it is necessary to determine causes and adopt countermeasures
Pitting is another type of failure caused by rolling fatigue, in which minute holes of approx.0.1 mm in depth are generated on the raceway surface.
2. Cracking, Chipping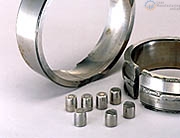
3. Brinelling, Nicks
Brinelling is a small surface indentation generated either on the raceway through plastic deformation at the contact point between the raceway and rolling elements, or on the rolling surfaces from insertion of foreign matter, when heavy load is applied while the bearing is stationary or rotating at a low rotation speed. Nicks are those indentations produced directly by rough handling such as hammering.
4. Pear skin, Discolouration
Pear skin is a phenomenon in which minute brinell marks cover the entire rolling surface, caused by the insertion of contaminants. This is characterized by loss of luster and a rolling surface that is rough in appearance.
In extreme cases, this is accompanied by discolouration due to heat generation. Discolouration is a phenomenon in which the surface colour changes because of staining or heat generation during rotation. Colour change caused by rust and corrosion is generally separate from this phenomenon. Discolouration is a phenomenon in which the surface colour changes because of staining or heat generation during rotation. Colour change caused by rust and corrosion is generally separate from this phenomenon.
5. Scratch, Scuffing
Scratches are relatively shallow marks generated by sliding contact, in the same direction as the sliding. This is not accompanied by apparent melting of material.
Scuffing refers to marks, the surfaces of which are partially melted due to higher contact pressure and therefore a greater heat effect. Generally, scuffing may be regarded as a serious case of scratches.
6. Smearing
Smearing is a phenomenon in which clusters of minute seizures cover the rolling contact surface. Since smearing is caused by high temperature due to friction, the surface of the material usually melts partially; and the smeared surfaces appear very rough in many cases.
7. Rust, Corrosion
Rust is a film of oxides, or hydroxides, or carbonates formed on a metal surface due to chemical reaction. Corrosion is a phenomenon in which a metal surface is eroded by acid or alkali solutions through chemical reaction (electrochemical reaction such as chemical combination and battery formation); resulting in oxidation or dissolution. It often occurs when sulfur or chloride contained in the lubricant additives is dissolved at high temperature.
8. Electric pitting
When an electric current passes through a bearing while in operation, it can generate sparks between the raceway and rolling elements through a very thin oil film, resulting in melting of the surface metal in this area. This phenomenon appears to be pitting at first sight. (The resultant flaw is referred to as a pit.) When the pit is magnified, it appears as a hole like a crater, indicating that the material melted when it was sparking. In some cases, the rolling surface becomes corrugated by pitting.
9. Wear
Normally, wear of bearing is observed on sliding contact surfaces such as roller end faces and rib faces, cage pockets, the guide surface of cages and cage riding lands. Wear is not directly related to material fatigue. Wear caused by foreign matter and corrosion can affect not only sliding surfaces but also rolling surfaces.
10. Fretting
Fretting occurs to bearings which are subject to vibration while in stationary condition or which are exposed to minute vibration. It is characterized by rust-coloured wear particles. Since fretting on the raceways often appears similar to brinelling, it is sometimes called “false brinelling”.
11. Creeping
Creeping is a phenomenon in which bearing rings move relative to the shaft or housing during operation.
12. Damage to cage
Since cages are made of low hardness materials, external pressure and contact with other parts can easily produce flaws and distortion. In some causes, these are aggravated and become chipping and cracks. Large chipping and cracks are often accompanied by deformation, which may reduce the accuracy of the cage itself and may hinder the smooth movement of rolling elements.
13. Seizure
A phenomenon caused by abnormal heating in bearings.
Lubricant checking
This method detects abnormalities from the foreign matter, including dirt and metallic powder, in lubricants collected as samples. This method is recommended for inspection of bearings, which cannot be checked by close visual inspection, and large size bearings.
Temperature checking
After the start of operation, bearing temperature rises gradually and becomes constant within one to two hours. Temperature should be monitored and recorded continuously during operation for evaluation by comparison. Trouble may cause irregular changes in temperature, such as a sudden rise.
Maintenance and checking
To ensure that bearings can demonstrate their optimal performance and provide service over a long time, regular maintenance and inspection are required. Inspect uninstalled bearings by the following procedure:
1. Cleaning
When a bearing is uninstalled, check how much lubricant is remaining first. Clean the bearing with anhydrous, neutral light oil or kerosene. Warm alkali solution or other material may be used as necessary. Clean the bearing preliminarily under cleaning oil, removing grease and sticking foreign matter with a brush or other tool. Do not rotate the bearing excessively during the preliminary cleaning.
After such foreign matter is removed, perform finishing cleaning while rotating the bearing slowly. Provide anti-corrosion treatment promptly when the cleaning is complete.
2. Checking
To determine whether the removed bearing can be used further, examine the bearing rings, rolling elements and cage carefully. If any of the damages shown in the Examples of Bearing Failures is found, use a new bearing.