A strategy of implementing “fail-safe mechanisms” to prevent a process from producing defects.
A timeless common-sense concept that was more recently popularized by Japanese industrial engineer Shigeo Shingo.
Error-proofing is a philosophy whereby it is unacceptable to make even a very small number of defects or mistakes, and the only way to achieve this “zero-defect” goal is to prevent them from happening in the first place. This demands extremely high levels of process capability as well as the focus on the root cause of failure for prevention rather than detection (inspection) of defects or errors.
Error-Proofing
- Goal of eliminating errors & mistakes or, at a minimum, reducing the impact of them when they occur
- Five approaches:
- Elimination: Make it impossible for the defect to occur: “Square peg in a round hole”
- Replacement: Automate manual operations
- Facilitation: Work instructions or guidance to minimize the chance of error
- Mitigation: Lessen the impact of the error on the system when it occurs
- Flagging: Inspection methods to ensure defects are identified before they proceed further down the value stream or to the customer
Examples of Error-Proofing
- Childproof caps on medicine bottles
- Audible alarm at the low-clearance bridge that warns you if your vehicle height exceeds limits
- Making surgery notations on the patient’s body (ex. Remove this kidney) before surgery
- Color-coding of electronic connectors for easier set-up or installation
- Bar-code scanning of products to generate faster, more accurate price look-up
- Hotel rooms key holder which turns off all the power in the room when the key is removed
- Filing cabinets that only allow one draw to be open at a time
Is it possible to achieve zero defects?
- If we can identify the conditions that lead to errors, and prevent those errors, we can achieve Zero Defects.
- If errors can still happen, and we can detect the error condition and prevent it from becoming a defect, we can achieve Zero Defects.
- If we can’t prevent errors from becoming defects then at least detect any defects immediately, prevent them from passing to the next operation and correct them ASAP.
Why Error-Proofing is important?
The 1-10-100 rule states that as a product or service moves through the production system, the cost of correcting an error multiplies by 10.
Activity | Cost |
Order entered incorrectly | $1 |
Error detected in billing | $10 |
Error detected by the customer | $100 |
A dissatisfied customer shares the experience with others – the cost often escalates.
Correction, Corrective and Preventive Actions
- Correction
- Taking care of the immediate problem
- Corrective Action
- Taking steps so the same situation will not occur in the future
- Preventive Action
- Designing products, processes, and systems where it is impossible to make a mistake
Prevention vs. Detection
- Prevention of defects (Proactive)
- Make it impossible for the error to occur (“best solution”) OR
- 100% inspection to detect the error as it happens and make it impossible to progress to the defect stage (“next best solution”)
- Detection of defects (Reactive)
- The defect does not pass to the next operation/customer. (Should be the “minimum required solution”)
How Error-Proofing differs from the process of traditional inspection?
- The Lean Six Sigma view on errors is that they can be abolished.
- Not all errors can be eliminated, but many can, and others can be brought down.
- The more errors we can eliminate, the better our quality will be.
- The need for inspection can be reduced or eliminated.
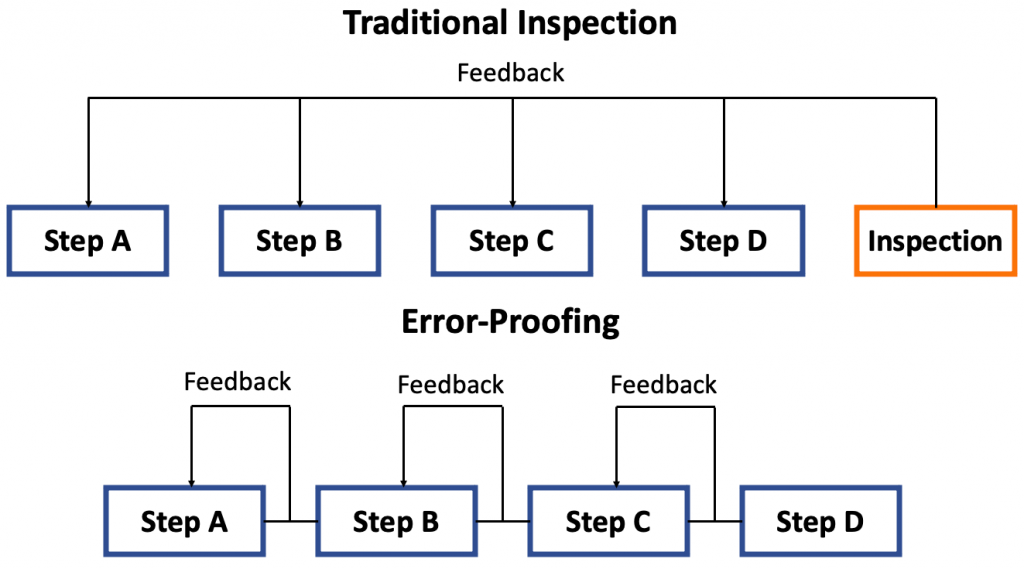
Traditional Inspection | Error-Proofing |
Defects are occurring at every possible step in the process, with compounding effects. | Every unit is inspected in a 100 percent informative inspection—workers know what to look for and what defines quality in a work product. |
Errors and defects are caught at the end of the process. | Immediate feedback on errors and defects is required so that action can be taken. |
Does not allow for an effective feedback loop of information with upstream process steps. | Relies on both self and successive checking of work quality. |
Causes much-wasted effort, labour, cost, material, and so on. | Helps to avoid producing additional units with the same defect. |
Main approach to error proofing
- Elimination
- At Source – make it impossible for the error to occur
- In Station – make it impossible for the error to progress to a defect
- Replacement
- Automate manual operations that are prone to error
- Facilitation
- Make it less likely that a mistake will be made
- Mitigation
- Minimize the adverse effects of the error when it occurs
- Detection
- Detect errors earlier, before they go to the next process step
Applying an error-proofing approach to main proof
- To error-proof a process we need to:
- Involve everyone in the process
- Understand the process
- Collect relevant performance information
- Analyze for potential errors/failure/priority and causes
- Reduce obvious sources of variation
- Implement preventive and detection techniques
- Validate the effectiveness of solutions and lock-in
I really love your posts. I want to get some of the pdf contents if possible. I just registered myself to the WhatsApp group.
Thanks
Leo