Quality engineering is also called the Taguchi method because most of the system was constructed by Dr. Genichi Taguchi, and although it is highly recognized worldwide, it requires considerable effort to understand the whole picture because the contents are quite complex.
Despite the fact that it is an unfinished technique with new mathematical proposals, the reason why it is used by well-known companies such as Toyota and Panasonic can be said to be “effective”.
Isn’t quality control alone good quality?
There are various definitions of quality control, but in short, it is an activity to prevent defects in the production process. Observing the quality data in the inspection is judged whether it is good or bad, and defective products will not be shipped.
In the old days, when small varieties were mass-produced, it was efficient to improve while producing what was designed for the time being, to “make quality on-site,” but in recent years, it has become a consumer need. Due to diversification and changes in the balance between supply and demand, the number of products produced per product has decreased, so the composition of “improving little by little” is no longer valid. In addition, as products have become more complex, the ratio of design costs to product costs has increased.
Evaluation method is important for efficient design
The Wright brothers made the world’s first successful human-crewed flight in the last century. While large-scale projects with the support of the government and the U.S. military were fiercely competing for development at that time, the brothers of the bicycle shop who did not even have a university were able to take the lead by using a lot of wind tunnel experiments. It is said to be one of the causes. Using a simple and low-cost evaluation method made it possible to design a competitive airplane without making a prototype of an aircraft that consumes considerable money.
Computer simulation would be more effective, but “functionality evaluation” in the Taguchi method is also an extremely efficient technical evaluation method.
The figure below summarizes the overall picture of the Taguchi method in my way. The late Genichi Taguchi, who created these, instructed many manufacturing companies and devised according to the situation each time. It took more than 50 years to establish this system, and it is not possible to understand the whole picture at once. It’s not easy. The most famous and often used part of this is parameter design, so let’s explain this part this time.
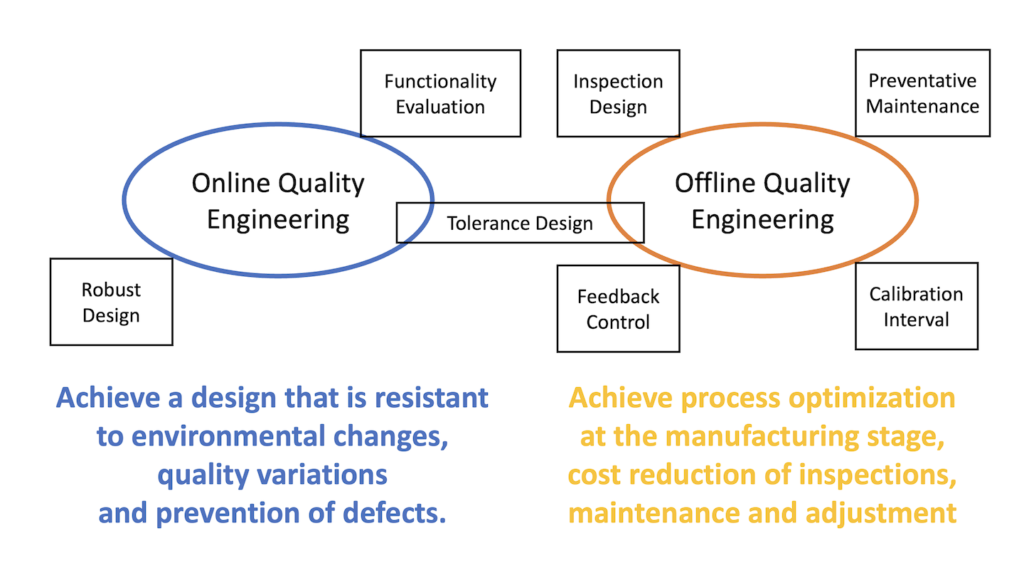
Incorporate variability into the experiment and evaluate
When the designer experimented with improving the reproducibility of the result, except for the experimental element (factor = parameter), it is made as constant as possible, and only the effect of the factor is extracted purely. If the purpose of the research institute is to write a dissertation, that’s fine, but in the case of industrial products, it’s not very good. Due to fluctuations in production conditions and various product usage environments, the same results as in the laboratory cannot consistently be reproduced. In many cases, the results do not follow the experiments. It is possible to stabilize the usage environment by tightening the delivery specifications of parts and materials, standardizing the manufacturing process in the work procedure manual, and limiting the usage conditions in the instruction manual, but it is often costly. In any case, increasing the cost and inconveniencing the user will reduce the product’s competitiveness.
Therefore, in the Taguchi method, the influence of the variable factor is evaluated by selecting factors that are likely to cause the characteristic change = variation and assessing the characteristic for the level combination of the design factors with the level of the factor changed intentionally. It determines the design factor level of features that are difficult to receive and satisfy the required specifications.