The key to ensuring quality (i.e. production standards) on the shop floor is achieving optimal conditions for the 4 Ms (Men/Women, Machinery, Materials, Methods), see Table “The 4-M Conditions – The Determinants of Quality”.
Improving quality means establishing optimal conditions for the 4 Ms, raising the quality assurance capability (Cp) of the process until it stabilizes at a high level, and setting work standards and inspection standards to maintain that capability. On the other hand, sustaining quality means faithfully applying the work standards and inspection standards that support the optimum conditions we have set. Figure “The 4-M Conditions – The Determinants of Quality” illustrates this relationship.
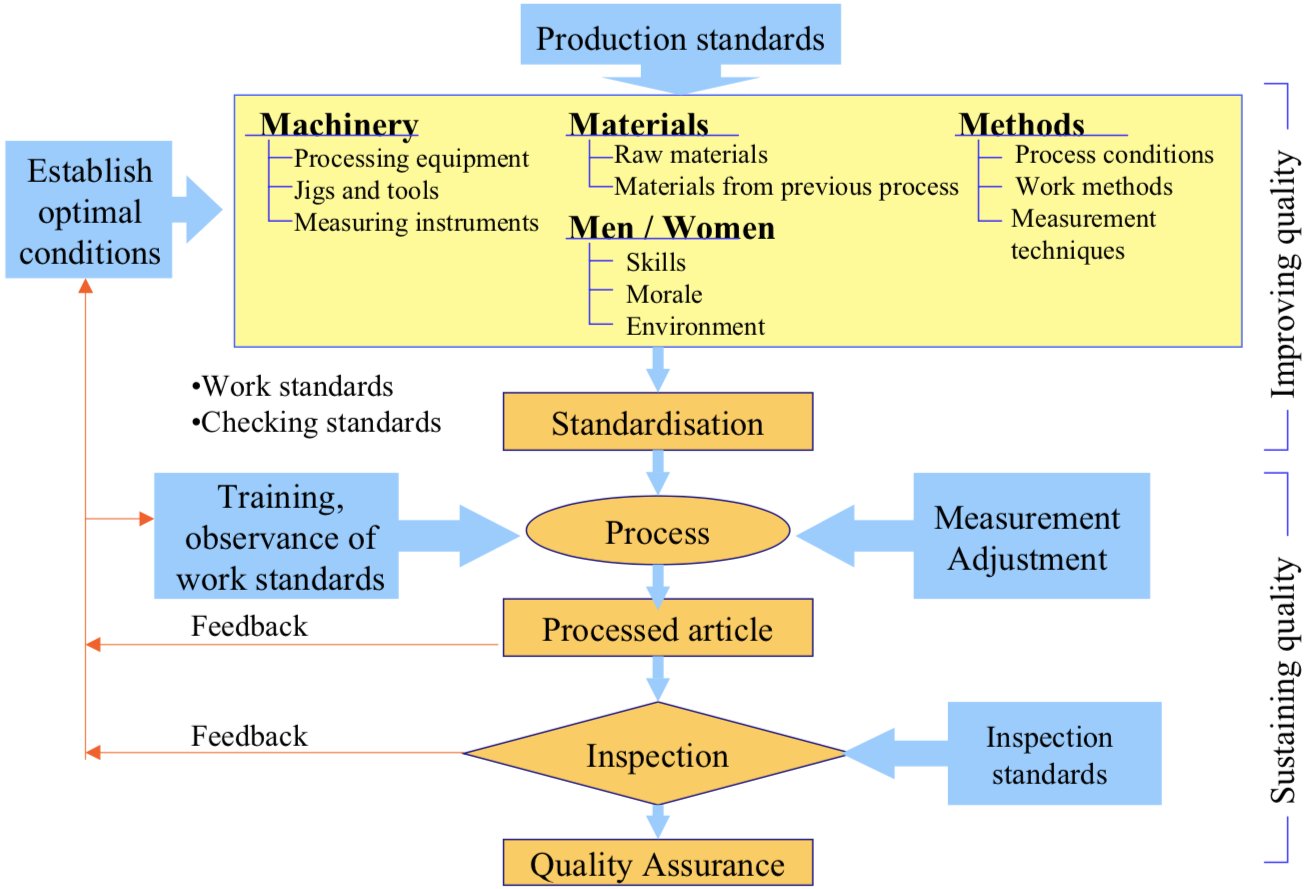
Conditions to be Satisfied
The 4 Ms | Conditions for machinery | Consequences of failure to sustain conditions |
Machinery | →Perfectly clean | →If the equipment is not kept clean, dirt can fall into it during processing and contaminate the product, making it defective |
→Properly lubricated | →Insufficient lubrication degrades equipment movement and leads to processing defects | |
→Nuts and bolts all correctly tightened | →Loose nuts or bolts create play in the machinery, leading to processing defects | |
→No loose parts | →Loose parts result in processing defects | |
Jigs and Tools | Conditions for jigs | Consequences of failure to sustain conditions |
→Fixings clean and undamaged | →Dented jigs damage the product or cause processing defects | |
→Reference surfaces for attaching workpiece clean and undamaged | →Worn jigs cause processing defects | |
→All parts are free of wear, chipping, etc. | ||
Conditions for cutting tools | Consequences of failure to sustain conditions | |
→Right tools used | →Using the wrong tools means that bolts are not tightened properly, etc., resulting in processing defects | |
Measuring Instruments | Conditions for measuring instruments | Consequences of failure to sustain conditions |
→Measuring elements clean | →Dirt on the components results in measurement errors | |
→Mechanisms operate smoothly | →Irregular movement causes measurement errors | |
→Properly calibrated | →The inaccurate setup produces measurement errors |
Materials | (1) Are the materials that may affect processing quality of good quality themselves? →Clean and undamaged →Of standard composition and form →Of uniform hardness, etc. (2) Is the quality of any previous processes that may affect the processing quality satisfactory? – Items from previous process clean and undamaged →Uniform dimensions in the previous process, etc. |
Processing conditions | Are the processing conditions suitable for building in quality? →Rotation speeds and feed rates set correctly? →Established conditions being maintained? →Temperature and humidity set correctly and maintained? →Pressures and flow rates set correctly and maintained, etc.? |
Working methods | Are the correct working methods being used? →Work securely positioned with no contamination between on reference surfaces? →Setup procedure specified and followed? →Work procedure specified and followed? |
Measurement techniques | Are the measurement methods correct? →Using measurement methods that prevent error? →Using the correct measurement pressures? →Are measurement standards written for measuring devices and followed? |
Men / Women (Morale) | Here, ‘morale’ refers to what is usually called ‘motivation.’ As well as being eager to improve quality continually, the operator is keenly aware of problems: they cannot abide minor flaws that hinder good quality and has a burning desire to find solutions. →A natural desire to produce good quality by sticking to standards at all times. →Keenly aware of problems. Tries to weed out any deficiencies (minor flaws) in the 4 Ms whenever a defect occurs. →Is very concerned if they notice something a little bit strange or slightly different from usual in their everyday work and report this to supervisors. Also has a strong urge to investigate problems him (or her) self. |