Effective maintenance is progressed by initiating activities designed to reduce failures and gradually building up a preventive maintenance system.
Basic thinking
The starting point for creating an Effective Maintenance system is to try to eliminate sporadic breakdowns through a comprehensive program of restoration and improvement. To do this, the production and maintenance departments must work hand in hand to develop the activities described below.
To begin with, the production department must:
- Encourage the painstaking restoration and improvement of the equipment through its Autonomous Maintenance program
- Develop equipment-competent operators and institute thorough routine management of the equipment
Meanwhile, as a body of professionals, the maintenance department should aim to eliminate breakdowns through the following approaches:
- Identify the causes of forced deterioration and restore and improve the equipment (Prolonging equipment lifetimes, Phase 1)
- Further prolong the intrinsic lifetime of the equipment by applying corrective maintenance to the necessary parts (Prolonging equipment lifetimes, Phase 2)
- Study the natural deterioration patterns of the equipment’s functional sections and components
- Begin preventive maintenance, starting with periodic maintenance
- In addition, keep the equipment from breaking down by performing predictive maintenance on parts that still exhibit widely varying lifetimes, and by keeping their deterioration within specified limits
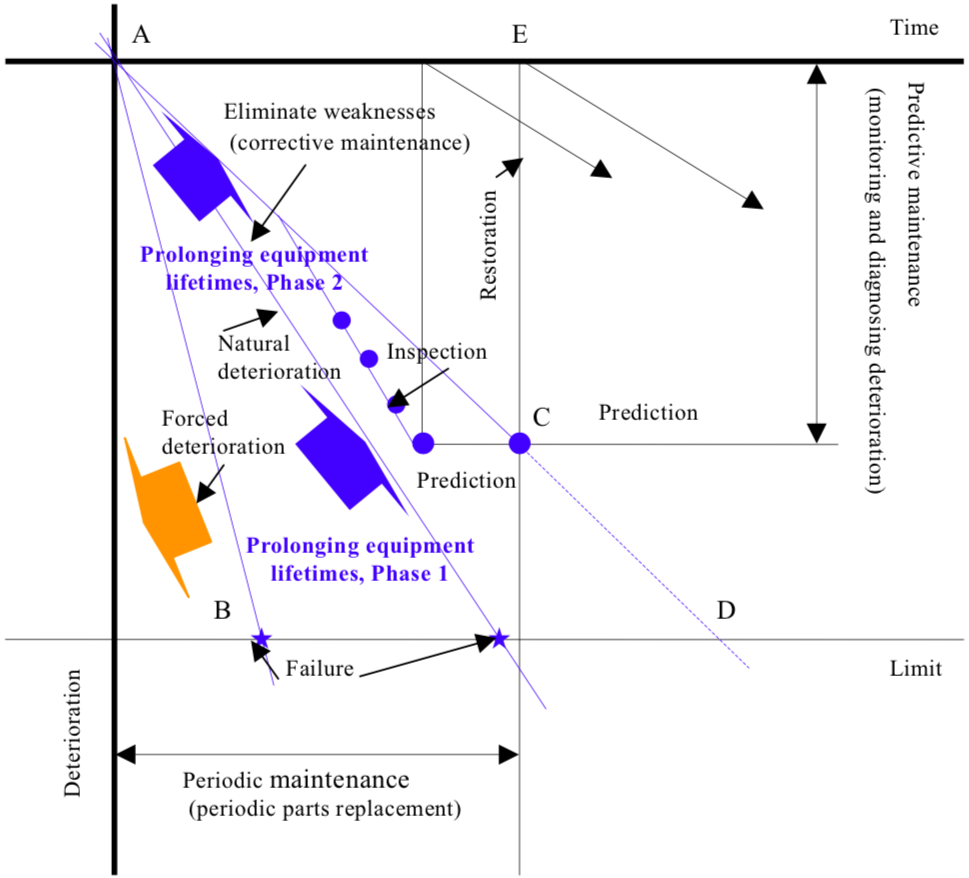
Approaching zero failure, and the 4 Phases
The conceptual approach to zero failure is built on the concepts of maintenance and prevention. However, as described earlier, there are various approaches to the practical realization of zero failures.
This section explains the procedure to be adopted, in the sense of supplementing the conventional approach, by focusing on how to identify the deterioration of functional parts of the equipment and what parameters to use in order to measure it.
Phase 1: Eliminate forced deterioration
The idea here is to establish equipment environments and conditions that permit only natural deterioration. This is done by eliminating the causes of forced deterioration and reversing any deterioration that has been left unchecked, as well as by improving the equipment.
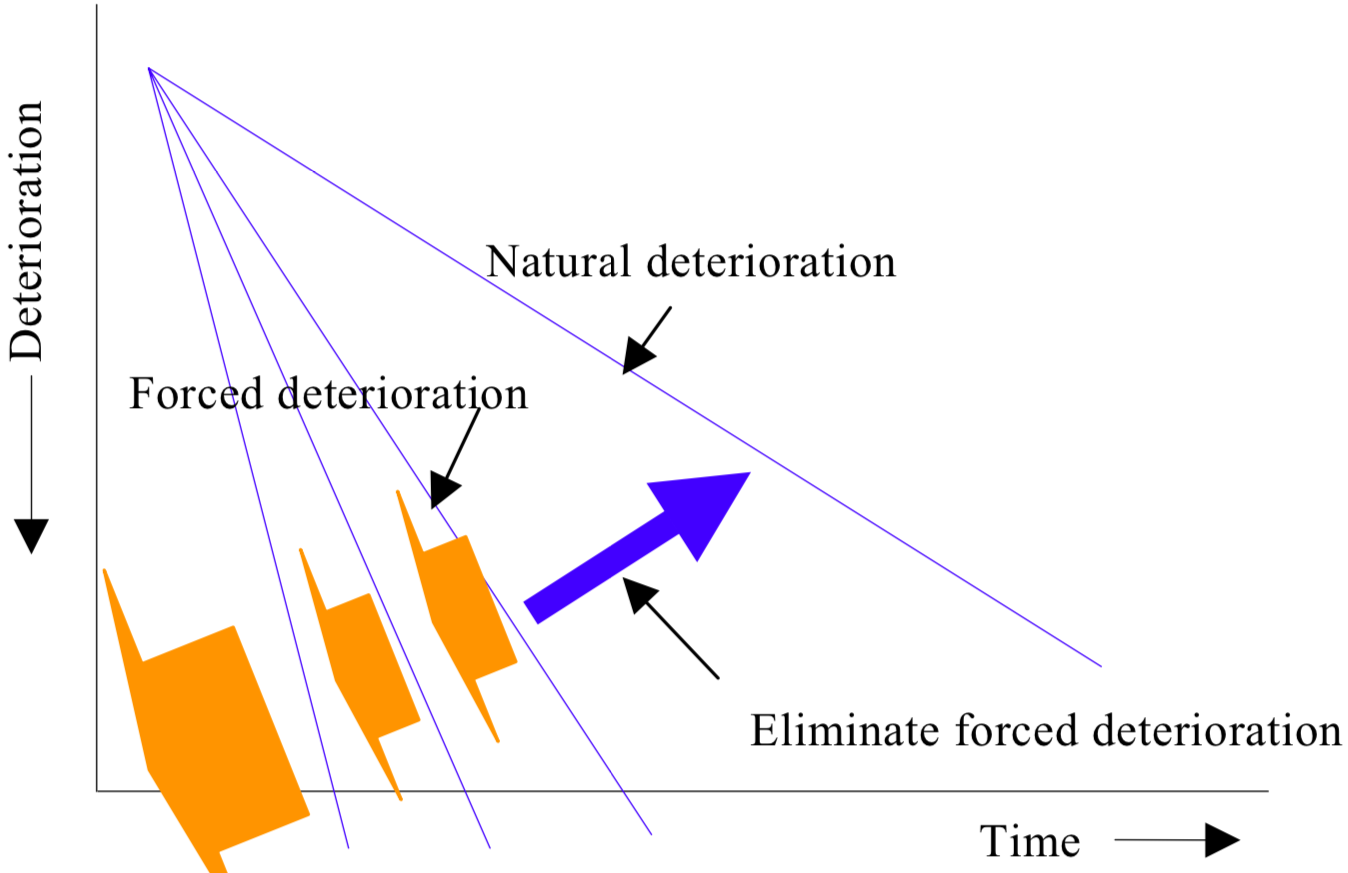
Key points
Begin by identifying and eliminating minor equipment defects through cleaning
- Act against sources of deterioration
- Identify and eliminate minor equipment defects
- Establish basic conditions
- Clarify and observe correct operating conditions
Phase 2: Extend lifetimes through corrective maintenance
However assiduously deterioration is reversed and equipment is improved, machines with inherent design weaknesses will require a commensurate amount of corrective maintenance. The decision as to whether corrective maintenance is required is usually based on the frequency with which maintenance is needed and the variation in the equipment’s lifetime.
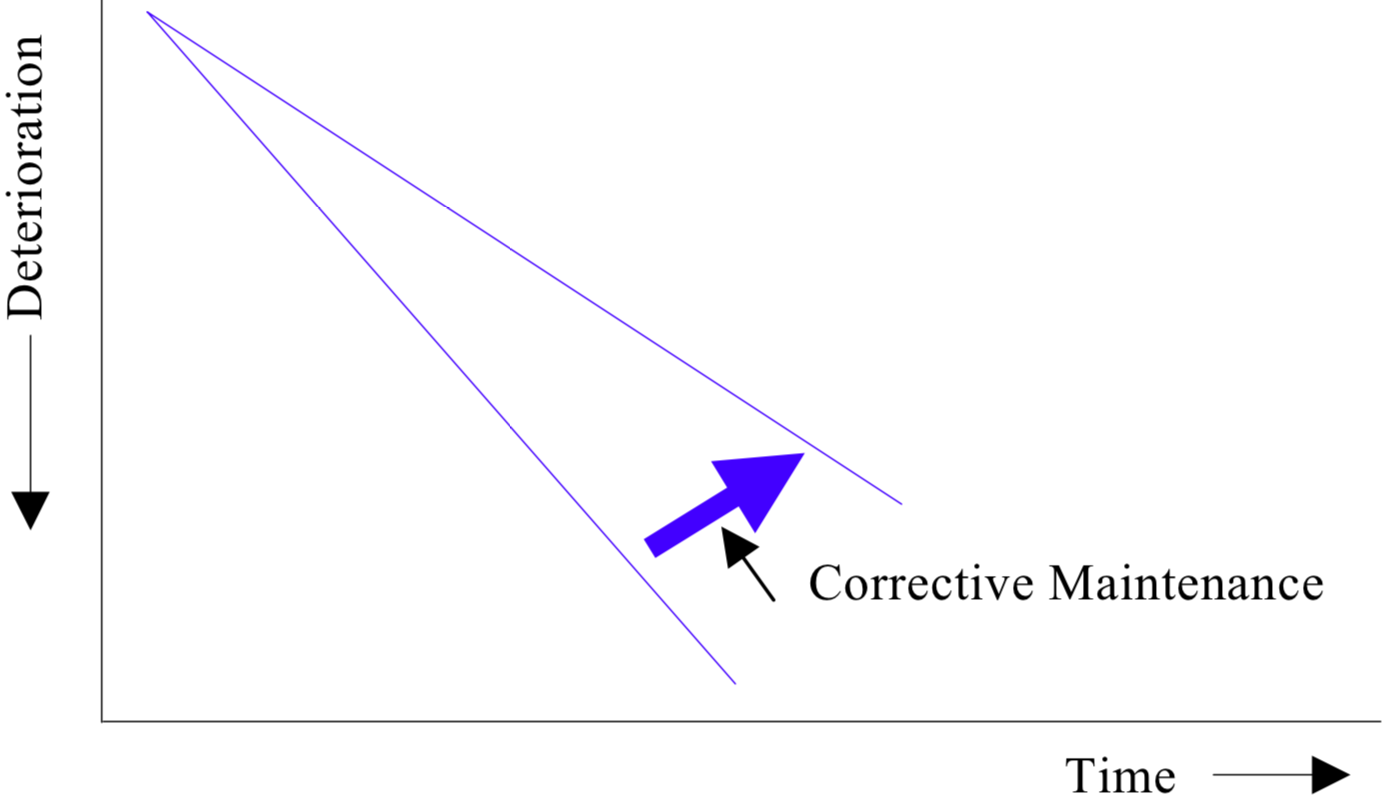
Key points
- Eliminate design weaknesses
- Heighten performance by increasing durability, strength, toughness, etc.
- Take action to reduce dynamic stresses
Phase 3-a: Monitor deterioration
In principle, maintenance should be restricted to those parts of the equipment that exhibit some kind of functional deterioration with the passage of time. In fact, all functional parts, i.e. all parts subject to stress, are always changing with time in some way or another. It may be more accurate to say it is just that our current level of expertise does not yet allow us to identify all these changes.
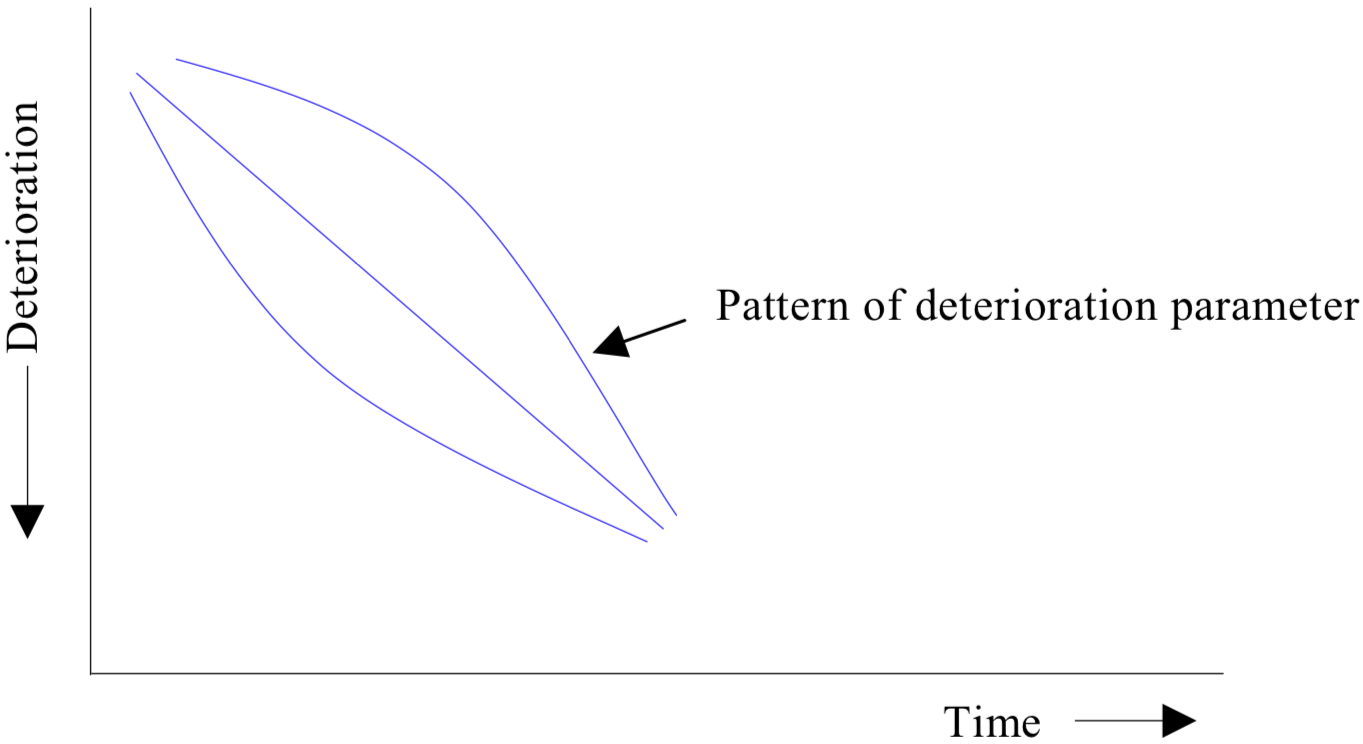
Key points
Investigate the patterns by which the deterioration changes with time
- Analyze the deterioration in physical terms
- Establish the relationship between deterioration and quality by monitoring the deterioration
Phase 3-b: Control deterioration
Once a deterioration pattern has been recognized, the next stage is to find out what parameter (specifically, what physical quantity) can be used to measure that deterioration. This step requires diagnostic expertise and is where the whole range of sensors and other diagnostic devices comes into play.
Key points
- Select a parameter from the deterioration pattern
- Select a measurement method from the parameter
- Identify what form of physical quantity the deterioration manifests itself in (displacement, dimensional change, vibration due to motion, current or power consumed, temperature, pressure, magnetic properties, etc.)
Phase 4: Carry out predictive maintenance
Equipment can be prevented from failing by appropriate periodic maintenance, but if we are seeking to extend its lifetime as far as possible, then predictive maintenance must form the basis for all our maintenance activities.
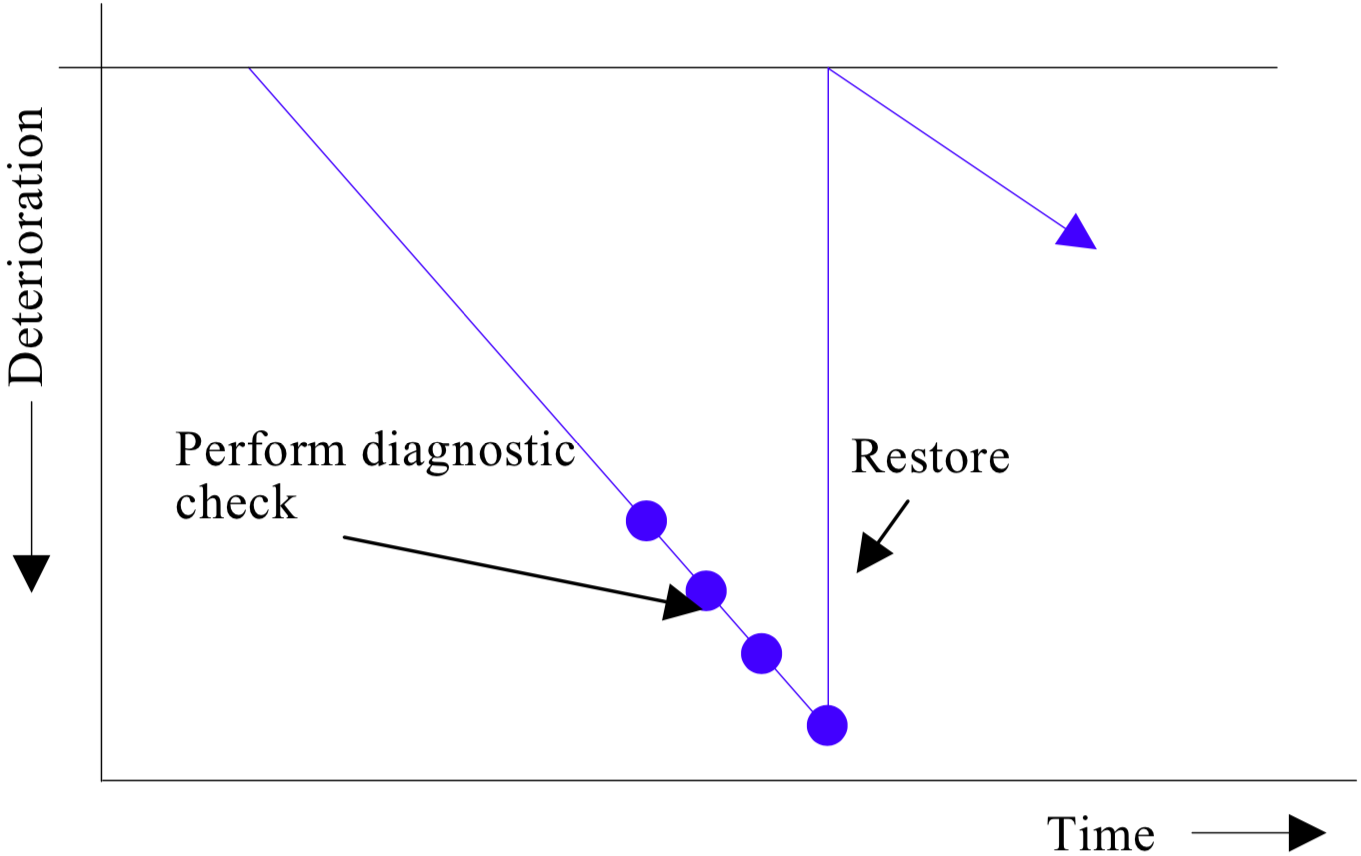
Key points
- Use simple diagnostics to monitor trends
- Use precision diagnostics to identify points of change
- Use and develop appropriate diagnostic techniques
- Systematically restore and overhaul the equipment
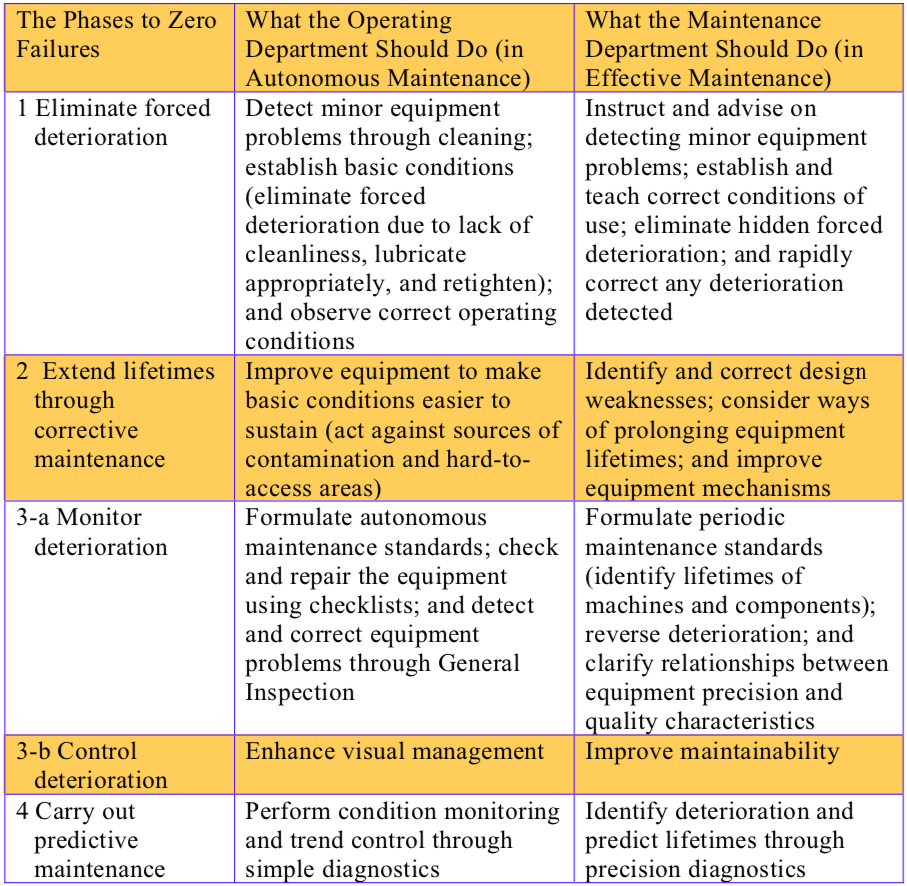
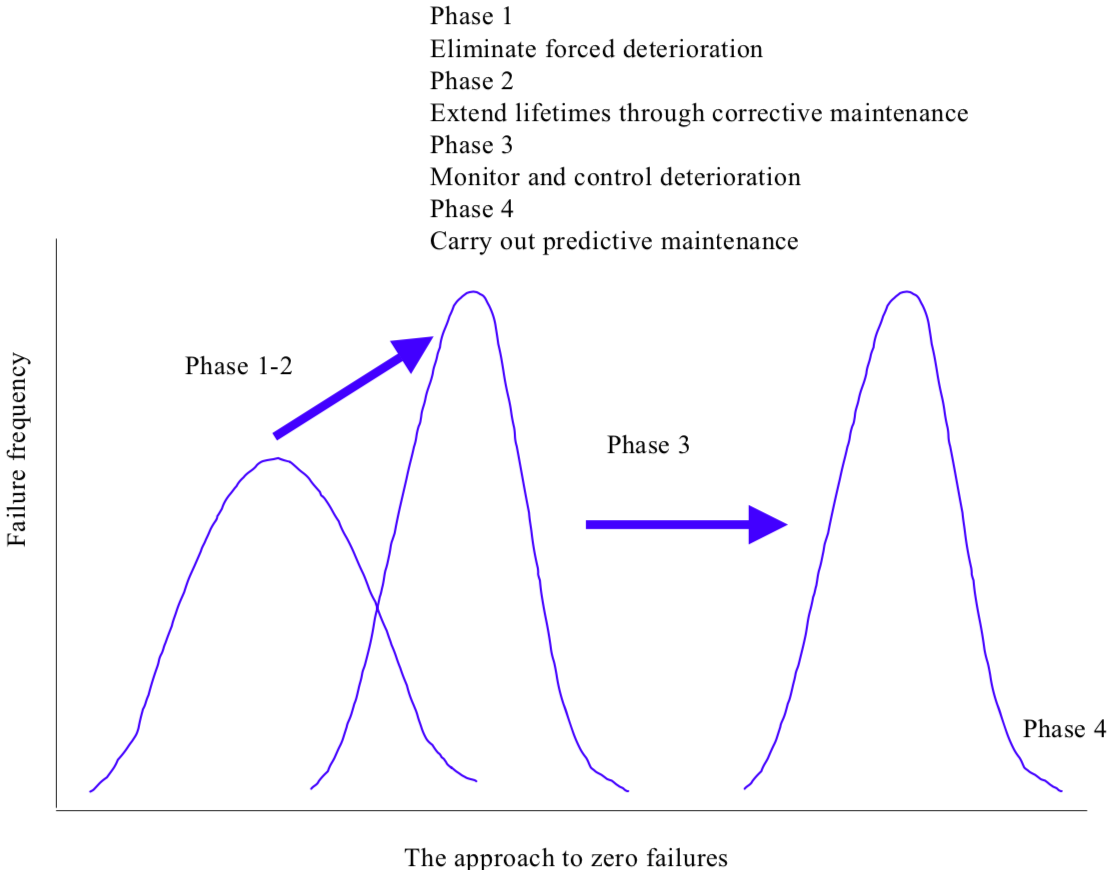