The Key Tool for Executing Continuous Improvement
12 Step Kaizen is a Better Defined CAP-Do
- Check
- Identify where the losses are
- Justify the subject selection by stratifying the data
- Understand the process and equipment
- Grasp the actual situation (Identify the Phenomenon)
- Establish the objective
- Establish a Work Plan
- Analyze
- Determine Root Cause
- Plan
- Propose Countermeasures
- Do
- Carry out countermeasures
- Verify results
- Standardize improvement
- Make future plans

Step 1. Identify the losses
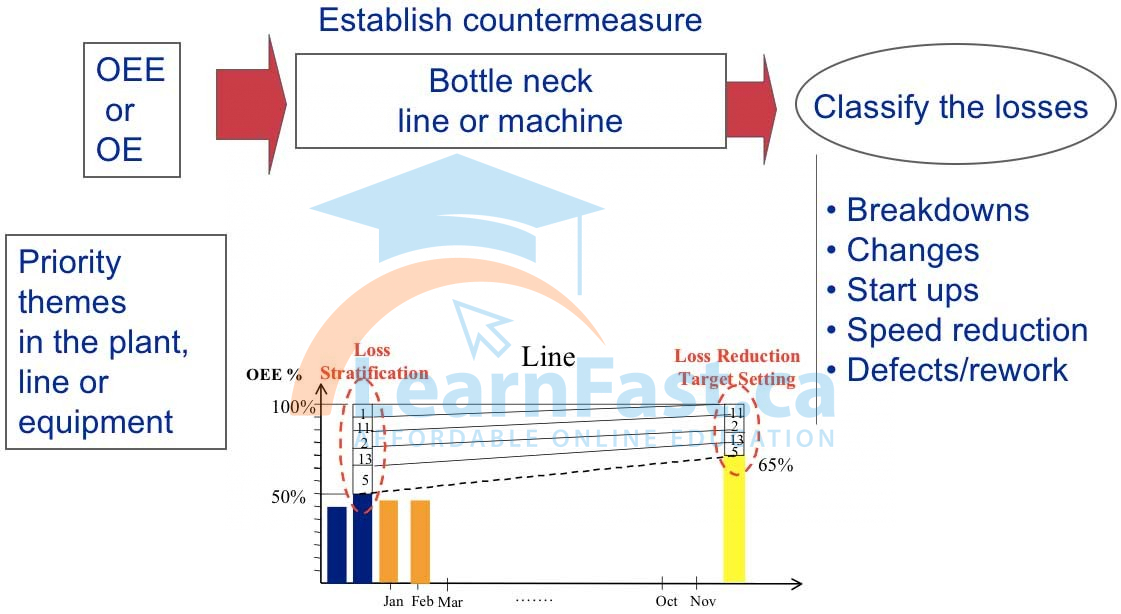
Selection & Justification of the subject
The reason why you chose the subject:
- Analyze the loss and make clear why you chose this loss
- Classify and quantify the loss
- Make clear what exactly you want to do with that loss, i.e. Improve the packing process task

How exactly do you want to improve?
Reduce the number of tasks involved?
Improve productivity?
Revise and improve ergonomics?
Step 2. Justification of the subject

Step 3: Understand the Process & Equipment
- Collect Data
- Go to the “Gemba” (actual place)
- Observe
- Take Photographs / Videos
- Interview
- Understand the Ideal Situation
- Collect the Available Data
- Assemble all available related data from Loss Tree Analysis
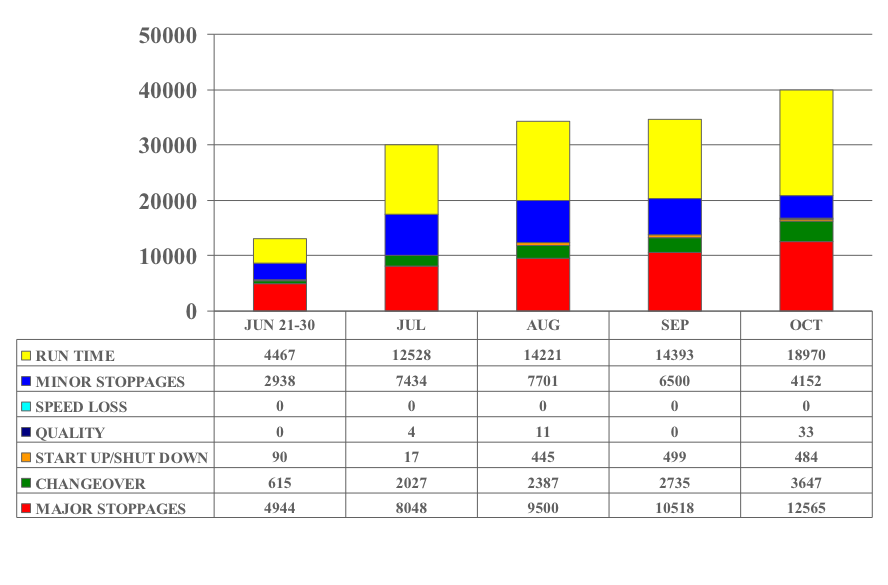
Go to the “Gemba” (or “actual place”)
- Take Photographs / Videos
- Observe
- Interview
Understand the Ideal Situation
- Summary of the process in question
- Overview of equipment in question
- Structure and mechanism of essential points (Structure diagram, layout)
Understand the basic rules and principles

Confirm and review basic knowledge for cause analysis
Step 4: Grasp the Actual Situation
(1) Clearly define the control characteristics
- For example, what is the defect?
- How can you quantify it?
- What time unit do you use to control this data? Monthly? Daily?
(2) Establish a Benchmark (initial reference point)
- If you do not know the level where you originally were before making the improvement, you will not be able to measure the improvement after applying the countermeasures.
- The benchmark should be the average of several months.
- If you are dealing with a breakdown, you need the data of at least three months. If this breakdown does not happen often, you will need the data of more than three months.
Turn the “problem” into a “Phenomenon.”
Phenomenon Means:
- Observing the facts with our own
eyes & all senses - The facts without presumption
5 Why 1 How (5W 1H) Define the problem, use loss data
What:
What thing or product did you see the problem?
When:
When did the problem occur?
Where:
- Where did you see the problem? (Line/Machine/Location)
- Where on the work or material did you see the problem?
Who:
Is the problem related to skill? (Skill dependent or independent)
Which:
Which trend (pattern) did you see the problem have?
Is the trend random, or is there a pattern?
How:
How is the state different from a normal condition?
The cause is NOT assigned or implied in the Phenomenon statement.
CHECK: 5W1H Graphically
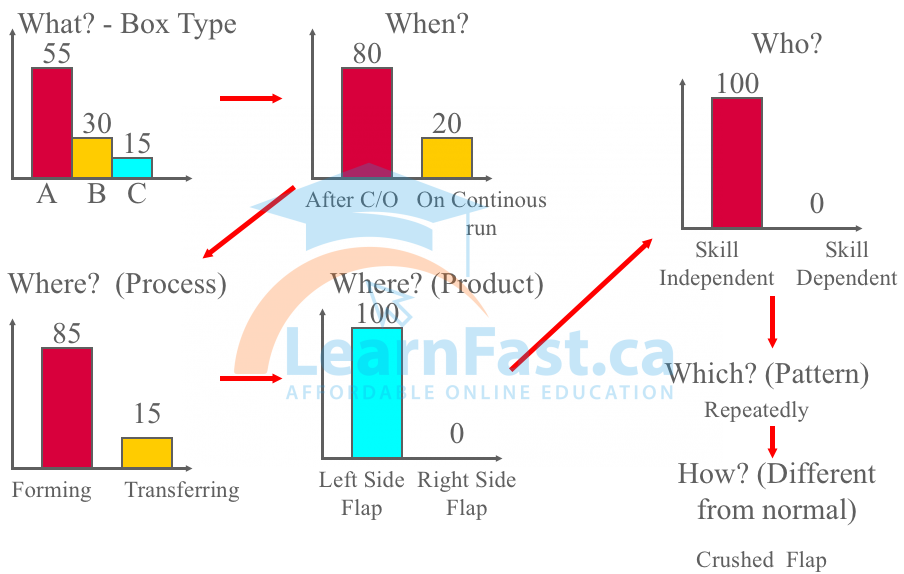
Step 5: Establish the Objective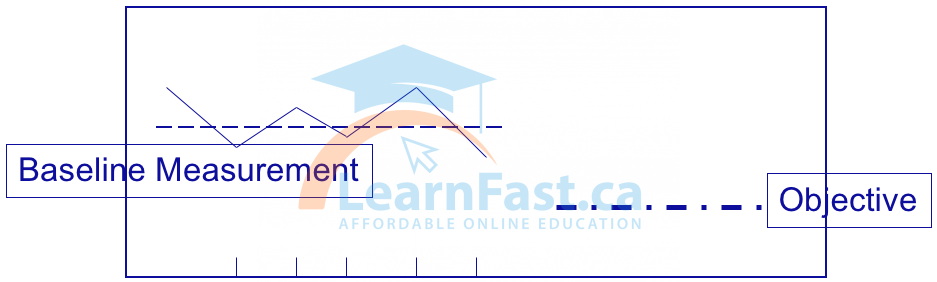
- What?: Control characteristics that were defined in Step 4?
- For when?: Due date to solve the problem
- What to do?: Numeric objective (Value)
Establish an ambitious but feasible target
Step 6: Make a Plan
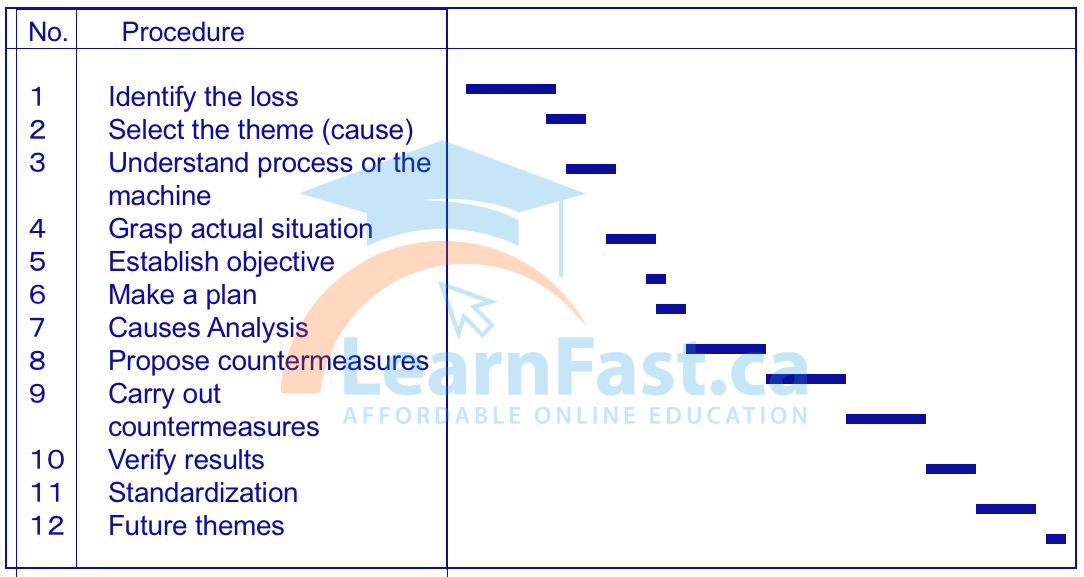
Step 7: Perform Cause Analysis
- Get to the root cause that makes the problem occur and have a clear picture of what is wrong.
- 5 Why – Approach the 5 Why from the 4M standpoint.
- Why-Why – Think of all thinkable causes based on the principles and basic rules.
The 5 Why

Root Cause Analysis – 5 Why

Causes to Consider
Equipment Branch
- Improper Equipment Ordered
- Poorly Designed Equipment
- Inadequate Maintenance
- Wear & Tear
- Abuse or Misuse
Procedural Branch
- Lack of Procedures
- Inadequate Procedures
- Misunderstood Procedures
- Failure to Warn or Respond
Note: Large losses often occur because of failure to take timely action
Behavioural Branch
- Lack of Knowledge
- Lack of Skill
- Physically Incapable
- Lack of Motivation
Step 7: Perform Cause Analysis – Types of Losses
Sporadic vs Chronic Losses
- Sporadic
- The problem has not always been there
- The relationship between cause & effect is clear
- Causes are traced easily
- Easy to establish remedial measures
- Remedial measures are commonly known
- Chronic
- The problem seems to have always been there
- The problem returns even when countermeasures are in place
- Causes cannot be clearly identified
- The relationship between cause and effect is not clear
- Remedial measures are inventive, not traditionally used
Step 8: Propose Countermeasures
- Study and evaluate countermeasures that are permanent and don’t allow the recurrence.
- Select the improvement measure considering the following points;
- the cost,
- the restricting conditions,
- impact on other processes and problems
- Review and Prioritize Possible Actions
- Short and Long Term Actions
- Assemble Required Materials
- Schedule Work
Detailed Action Plans for Short Term, Intermediate, and Long Term:

Short Term Action – within one week
Intermediate Action – within one month
Long Term Action – greater than one month
Step 9: Carry Out Countermeasures
- Even if the countermeasure is excellent, if the execution is not correct, the problem will not be solved
- You will need a mechanism to follow up on:
- If actions are completed by the due date
- Who is accountable if actions are not completed
- You will need a mechanism to measure and report results:
- What is reported, to whom, how often?
- What is the period of sustainable results required to achieve verification (Step 10)?
Step 10: Verification of Results
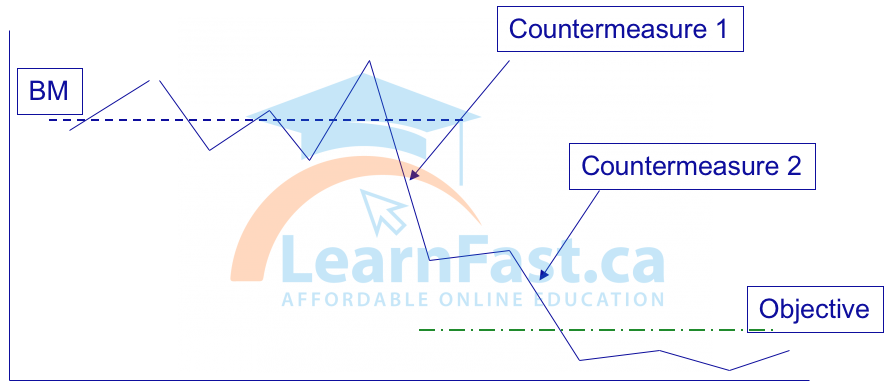
Decision Point: Were Objectives Obtained?
- Review data for the agreed period (typically 90 days)
- Was the objective stated in Step 5 achieved?
- If YES, progress to Step 11
- If NO, return to Step 7 and re-Analyze
Step 11: Standardize
- In order to prevent recurrences, clarify what items really have to do with the cause and need to be maintained & controlled.
- The results should be classified as follows so that you can
sustain and control them:- Equipment related
- “Cleaning, inspection and lubrication standards”
- “Annual Maintenance Program”
- “OPLs”
- “QM Matrix” (Quality)
- Labor-related
- “Manual for procedures and labors”
- Equipment related
Use the standards and verify that the results are being sustained.
Create OPLs
- Develop / Revise Standards to Hold the Gains
- Training Standards (i.e. One Point Lessons)
- Cleaning, Inspection and Lubrication Standards *
- Standard Operating Procedures *
- Processing Standards *
- Maintenance Standards *
- Engineering Standards *
* Do not forget to revise all SOPs and Standards to include information from OPL’s
Step 12: Define Future Plans
Ask yourself:
- What can you do to obtain greater results?
- What do you have to do to sustain and control the results?
- What other related subjects are there?
