Objectives
- What are control plans, and what is the purpose of control plans
- What does it do?
- Putting the control plan into place
- Control Charts
- Integrating control charts and plans
Control and Response plans must be prepared to ensure the following:
- Creating and aligning the system, structure, and processes
- Complete documentation of the processes and procedures
- Developing a monitoring and response plan in case the performance drops
- Training on the improvements made
- Hand over the improvements to the process owner
Control plans:
- One or more approved documents
- Provides status of a process
- Provides measurements/standards that define the process
- Includes monitoring procedures
- Includes response planning
Characteristics of control plans
- Characteristics to control
- Process step
- Process step and characteristics documentation
- Standards
- Specs
- Predictability
- The measurement system and analysis standards (verified by gauge R&R)
- Capability
- Methods
- Owner and collector
- Data collection method
- Sampling procedures
- Analysis
- Response Plan
- Out of specification
- Out of control
- Unacceptable measurement system
- Incapable process
- Improvement
- Data to report to process owner
- Format
- When to report
Why use a Control Plan
- Defines and describes the process
- Aids in training and audit activities
- Provides for timely process troubleshooting
- Links process knowledge and response
- Sustain process improvement
Plans link response to process information
- One point falls beyond zone A
- Two out of the three consecutive points fall in zone A or beyond
- Four out of five successive points fall in zone B or beyond
- Eight straight points fall on one side of the centerline
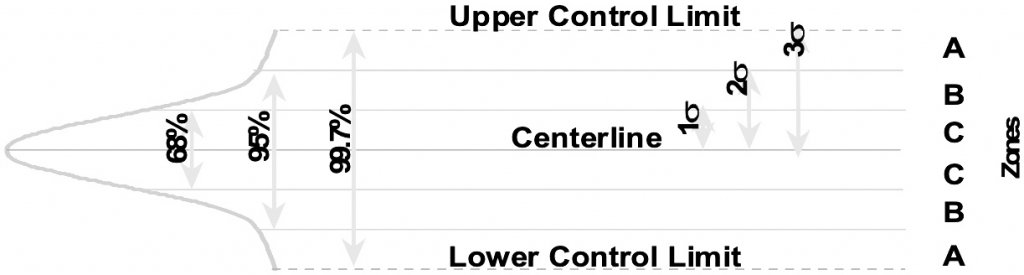
Once the improvements are implemented, the team must ensure that the project goals are attained and that the specified measures for sustainability are in-place. Lean principles, like mistake-proofing, encourage the team to style the method in a way that doesn’t permit errors to require a place, while SPC charting allows the method outputs and inputs to be monitored. The availability of process data, the value of collecting them, and the possibility of genuinely mistake-proofing a step are all critical considerations in determining what sort of control to use. Regardless of the tactic, the common theme among all Control phase tools remains the same: the functional owners of the improved process got to have bought into the new way of doing business. The buy-in is the ultimate Control plan, ensuring that the improvements will stay in situ long after the team has been disbanded.
Links to Measurement System
- Is the measurement system stable and predictable?
- Are parts or items different?
- Are operators different?
- Are operators consistent?
- What is the measurement resolution?
- What is the measurement uncertainty?
- What is measurement discrimination?
- Are the measurement units adequate?
- Are the measurements stable over time?
Control Plans how they are done?
- Administrative section
- Critical identification, approval, document control
- Plan
- Information on the process
- Measurement used
- Control chart (if appropriate)
- Corrective actions to Out-of-Control conditions
- Other
- References to Standard Operation Procedures (SOP)
- Emergency response plans
- Links to Failure Mode and Effects Analysis
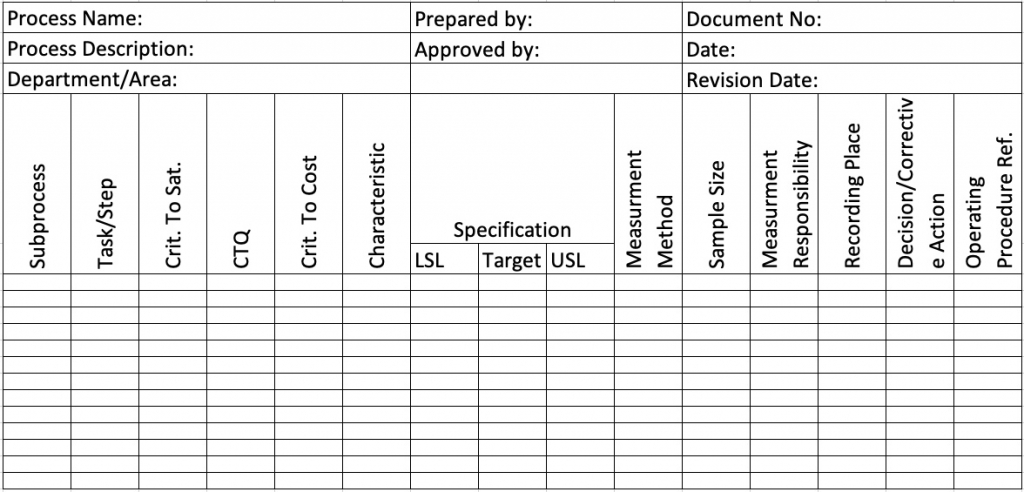
Summary – Control Plans
- Provides point of reference
- Links monitoring inputs and response
- Enables project completion
- Sustains long-term capability