Changeovers are required to ensure that we can satisfy the different needs of a customer. Reducing the time to do a changeover holds the key to how quickly we can respond to a customer’s needs. Also, quick changeover means less downtime, which translates to more efficiency, productivity, and parts!
How is a quick changeover achieved? It all starts with the identification of external and internal activities.
Any activity performed with the equipment/machine running is called an external activity.
Any activity which needs to be performed with the equipment/machine shut down is called an internal activity.
Let’s look at an example:
Process: Washing clothes in a washing machine
Machine: Washing machine
Do you think loading clothes in the machine is an external activity or an internal activity?
To find that out you need to ask if the washing machine can run while you are loading clothes? Absolutely not! Therefore, this is an internal activity.
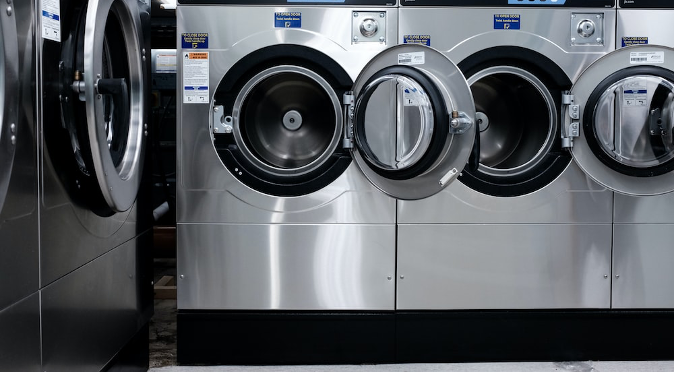
Next, imagine you are making donuts.
Process: Frying the donut
Equipment: Fryer
Is making a hole in the donut an external activity or an internal activity?
Again, we need to ask if the hole can be made with the fryer running? Yes, we can. Then it is an external activity.
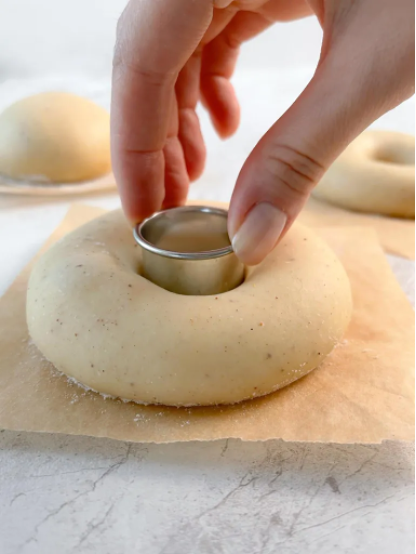
This concept can be extended to a machine while performing changeovers. Which activities can be done while the machine is still running and making parts? These activities need to be identified and performed before or after the changeover to optimize the amount of time the machine is down.
The perspective of internal and external activities has to be developed in every function of the organization involved in a changeover. For example, setup technicians need to know that they must make all the preparations (staging) before shutting down the machine for a changeover. The line supervisor needs to understand the difference between an internal and external activity to give the technician enough time to prepare for a changeover. An operator must be able to distinguish external and internal activities, so they are prepared to make the first good part immediately after the internal activities are completed. A responsibility matrix indicating who is responsible, accountable, and who needs to support the activity can be very helpful in achieving this.
Which activities in your current changeover process will you convert to external activities? Comment below or on the LinkedIn post.
About the author
Swathi Mohan
Swathi Mohan is a sought-after continuous improvement expert with over 12 years of experience in the manufacturing industry. Certified Lean Six Sigma Black Belt and a highly influential adult educator. Root cause analysis, Toyota problem-solving methodology, lean systems implementation, and total Productive Maintenance are some of her areas of expertise. Feel free to get in touch with her to get help with solving your operational problems.
Great article on understanding the difference between external and internal activities in changeovers! It’s essential to identify and distinguish these two types of activities as they can significantly affect the efficiency of the changeover process. By focusing on internal activities necessary for the changeover and minimizing or eliminating external activities that are not, manufacturers can improve their changeover times and reduce downtime.
I appreciate the practical tips and examples you provided, such as using a checklist to help identify and categorize activities and the importance of involving operators in the changeover process. Changeovers can be an opportunity for improvement rather than just a necessary evil, and by analyzing and improving the changeover process, manufacturers can increase their productivity and competitiveness.
Thanks for sharing your insights and expertise on lean manufacturing and changeovers, and looking forward to reading more of your articles in the future!
Thank you John for your wonderful comments on my article. I apologize for the delay in response. I had somehow missed the notification. Anyway I would love to connect with you and learn more about what you do and your journey in lean manufacturing. You can find me here:
https://www.linkedin.com/in/swathi-mohan/