Mastering Production Efficiency with PDCA
In the ever-evolving world of production, efficiency is not just a nice-to-have—it’s a must-have. To stay competitive and profitable, organizations must constantly evaluate their processes and seek improvements. One powerful tool that has proven its worth in this regard is the PDCA cycle, a four-step methodology for continuous process improvement. The PDCA (Plan-Do-Check-Act) cycle was first introduced by Dr. Walter Andrew Shewhart in 1939 and was further developed by Dr. William Edwards Deming in the 1950s. Today, it is recognized as a leading strategy tool for businesses across all industries, helping organizations achieve progressive improvements and monitor the quality of changes in their processes.
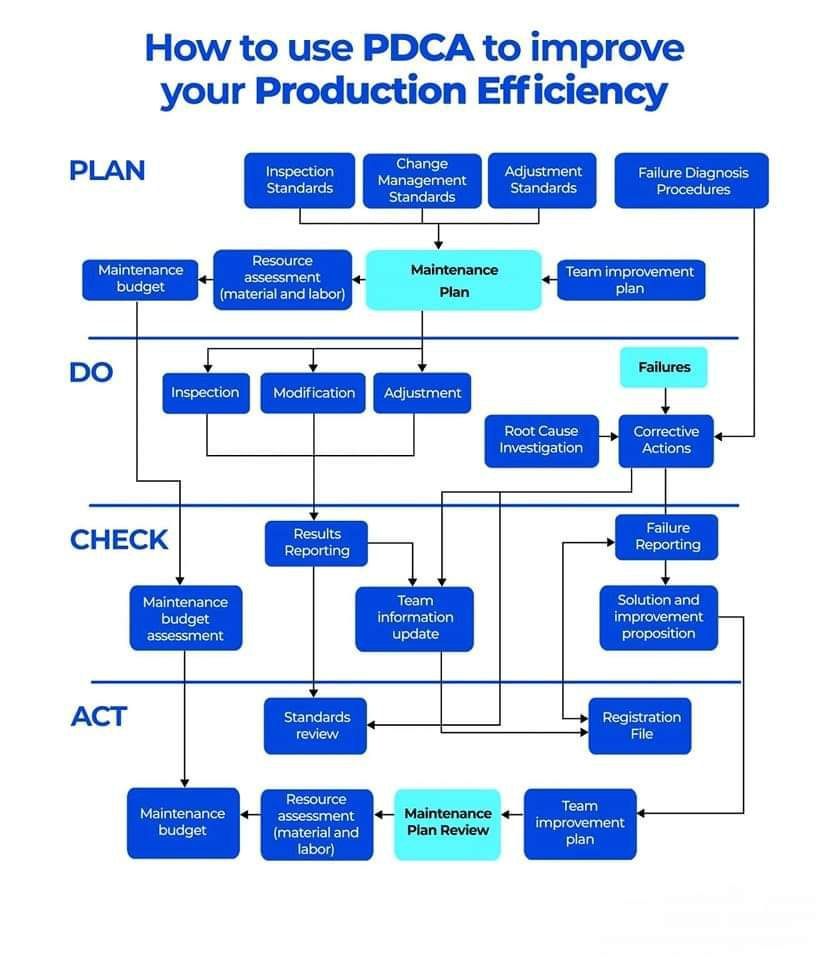
The Power of PDCA
The PDCA cycle contributes to the goal of identifying which business processes work and which need further improvement. It is a methodical approach to avoid recurring mistakes and errors in operations. Furthermore, PDCA is one of the widely used methods of monitoring quality management systems and applies to international standards such as ISO 22301, ISO 9001, ISO 45001, and ISO 27001. Through this data-driven method, organizations can work to improve their processes, products, and services continuously.
How PDCA Enhances Production Efficiency
At its core, PDCA is a cycle of continuous improvement loop that restarts whenever an element of the implemented change is found to be ineffective. The cycle repeats until the most desired outcome is reached. Here’s how to use PDCA to improve production efficiency:
Plan: Identify an area of production that needs improvement and define the problem or opportunity. This stage is the backbone of the whole cycle and requires a comprehensive and detailed approach. Create SMART (Specific, Measurable, Achievable, Relevant, and Time-bound) goals that your team members and relevant stakeholders agree upon. Consider the resources needed to implement proposed changes and potential hindrances in achieving project goals. The end of this stage should materialize in a comprehensive plan answering key questions such as the cause of the problem, current standards and procedures, and criteria for project success.
Do: Implement the plan on a small scale or in a controlled environment and gather data on the results. This approach ensures that any potential negative impacts of the changes are minimized. In this stage, proposed solutions are tested, and relevant data is collected to assess their effectiveness.
Check: Analyze the data collected during the “Do” phase to determine the effectiveness of the changes. Compare the results to the goals and targets in the “Plan” phase. Assess if the result is satisfactory and the solutions are working according to the objective or if further improvements are needed to achieve the overall goal. If so, return to the “Plan” stage and try other alternatives. If it’s a success, proceed to the “Act” stage.
Act: Based on the data analysis, take action to either continue with the changes or make further improvements. Fully implement effective solutions as part of your business process. Address questions such as what resources are needed for successful implementation, whether training is necessary, and how results can be measured more accurately. The PDCA cycle allows you to repeat the cycle if you believe the solutions can still be improved or if changes could affect how the implemented solutions work.
Organizations can gradually enhance production efficiency and achieve better results by following the PDCA cycle and continually making minor improvements. The PDCA cycle’s iterative nature ensures that the improvement process is continuous and responsive to the changing needs and circumstances of the business.
Embrace the PDCA Cycle
In conclusion, the PDCA cycle is invaluable for any organization striving to improve production efficiency. Its systematic approach allows continuous process improvement, enhancing productivity, quality, and operational efficiency. It enables businesses to be proactive and adaptive, fostering a culture of constant growth and learning.
Remember, the journey to improved production efficiency is not a sprint—it’s a marathon. The beauty of the PDCA cycle lies in its cyclical nature: there is always an opportunity for evaluation and improvement, making it a powerful ally in the quest for continuous improvement. Embrace the PDCA cycle, and embark on a journey of constant growth and lasting efficiency.
To paraphrase the words of Dr. William Edwards Deming, without data, you’re just another person with an opinion. With the PDCA cycle, you’ll be an organization with a plan, a direction, and a method to succeed.
MUITO BOM
Me pues envié un copia
QUERO UMA COPIA DESSE EXCELENTE TRABALHO