General Rules
- The goal of the Kaizen board is to give every employee opportunity to impact the company’s performance now and in the future. Each employee’s responsibility is to look at how to make the work easier, better, faster and cheaper.
- Each Team has its own Kaizen board to track the implementation of Kaizen ideas and define the colour of the Kaizen Card. The target is 3 Kaizens submitted per month per team – 3 Kaizen cards submitted monthly on the Kaizen board.
- All Kaizen implemented in each month will be collected on the last day of the month, and the Kaizen of the month will be selected by management. The winning team will be recognized.
- All Kaizen implemented will be moved to the Kaizen Wall of Fame and allocated to each company value.
- Kaizen Cards should be used for reduced problems/ideas/wastes that are easy to implement and in the team’s control. Small improvements like 2 minutes of time savings can significantly impact the company’s performance.
- Kaizen Cards are not dedicated to solving problems related to many departments involved; this type of problem should be marked on the whiteboard in the problem-solving section.
- All completed Kaizens will be moved to the Kaizen Wall of Fame and allocated to the company Value that the improvement is connected to the most.
- Kaizen is not about spending more money: we have the current resource and find a way to use them more efficiently.
Steps to Implement Kaizen
- Update Kaizen Card with Problems, Improvements, Start date, Expected benefits, Input needed and Priority.
- Priority levels:
- Priority high: implemented in 3 days
- Priority standard: implemented in 10 days
- Priority low: implemented in 30 days
- Add Kaizen Card on the whiteboard in the To Do section, talk with your manager the same day, and ask for approval to implement the improvement idea.
- Move Kaizen Card to the Doing section, and after improvement is implemented, ask your manager to check and confirm the improvement results. Should your manager tick Result Verify? YES, section.
- If the same improvement can be implemented in another team, please contact this team to prepare their Kaizen Card and mark the new method as standardized in the company.
- Add the completed date and move to a Done section on the Kaizen board.
Examples of Kaizen
- Kaizen is based on 8 Wastes (TIM WOODS). Waste is anything that is not adding value to the customer. If you ask the customer: would you pay for it and the answer is no: this is the Waste. A customer is everybody waiting for our work’s result: internal and external Customers.
- Transport (not necessarily a movement of items, goods, or parts but also the movement of information via email, messengers, files saved in more than one location, moving data from one tool to another: from invoice to excel and later to information system)
- Inventory (Inventory is everything that is the work in progress waiting to be delivered to the Customer. Inventory can be related to an unnecessary amount of parts ordered waiting to be used but also can be related to reports; data summary started but not finished)
- Motion (Motion is the movement of people; you can reduce motion by observing how people move in the office, between buildings, or on different floors to get information or part/product they need to continue their work. Opportunity to reduce motion by moving parts closer to people
- Waiting (Waiting for approval, for information, product or parts. Waiting occurs when there is no standard and we need to wait for confirmation on how something has to be done)
- Overproduction (Producing more than is needed, creating too many reports, collecting and creating data nobody uses later)
- Over-processing (Doing too much: too many columns in an Excel file that nobody needs, more work is done but the work is not needed, adding too much information in the report that nobody needs)
- Defect (Defect is anything that is not meeting the requirements of the customer)
- Skill under-utilized waste (Shop floor talent that is not used correctly, causing lower employee morale, drive, and creativity)
- Kaizen is based on small problems to be solved easily and in our control.
- Kaizen is based on the approach: of how we can make our work easier, better, faster and cheaper.
The Kaizen board is part of the visual management
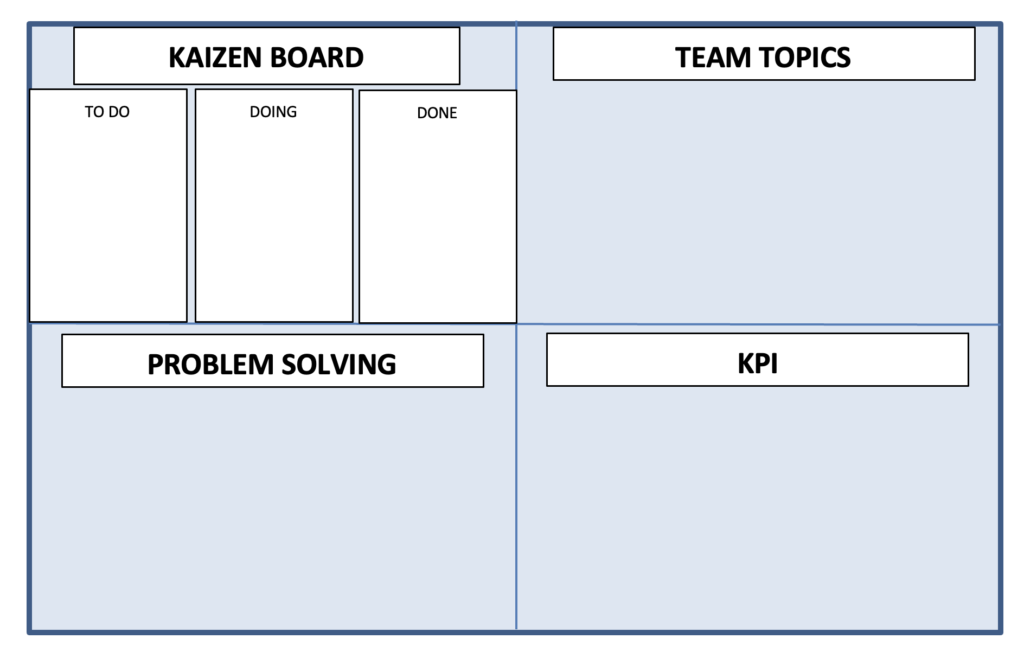
Would you like to identify wastes at your manufacturing facility? Use our template while walking all areas, observe and note so it can be analyzed and actioned later. Comes as a downloadable spreadsheet.