Converting the customer’s requirements into “quality characteristics” and developing a design quality for the finished product by systematically deploying the relationships between the requirements and the characteristics, starting with the quality of each functional component and extending the deployment to the quality of each part and process.
System for obtaining the customer’s prioritized required quality
Quality Function Deployment & Quality Deployment
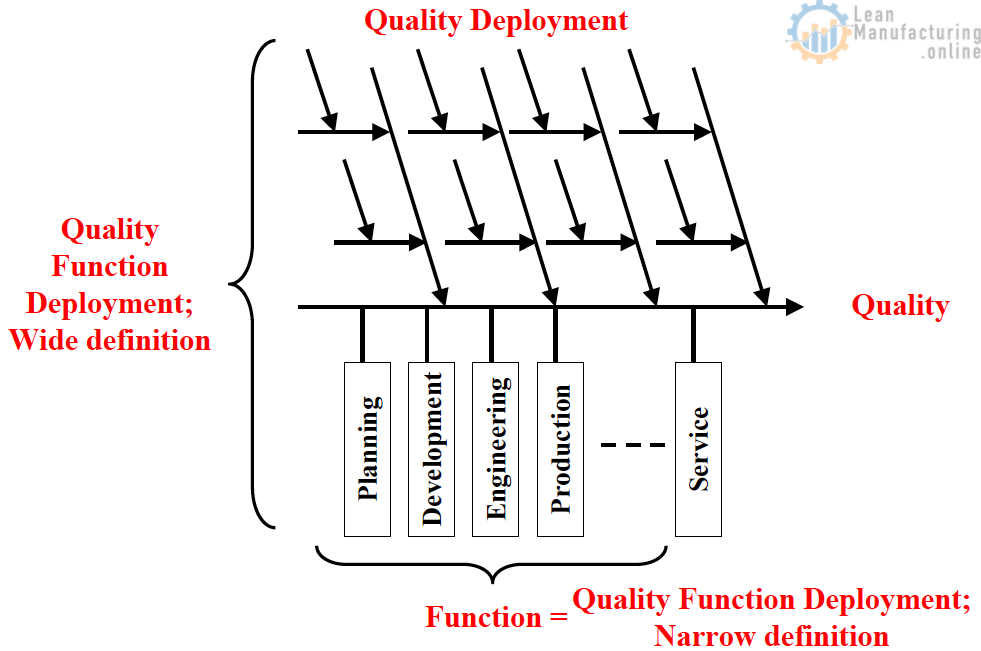
Definition of Quality Function Deployment
- QFD narrowly defined:
- To deploy job functions or operations, through which quality is built, into the detail of the workplace by the objective-means relation system.
- QFD widely defined:
- A generic name for quality deployment and quality function deployment in the narrow sense of the term combined.
Total Concept of QFD
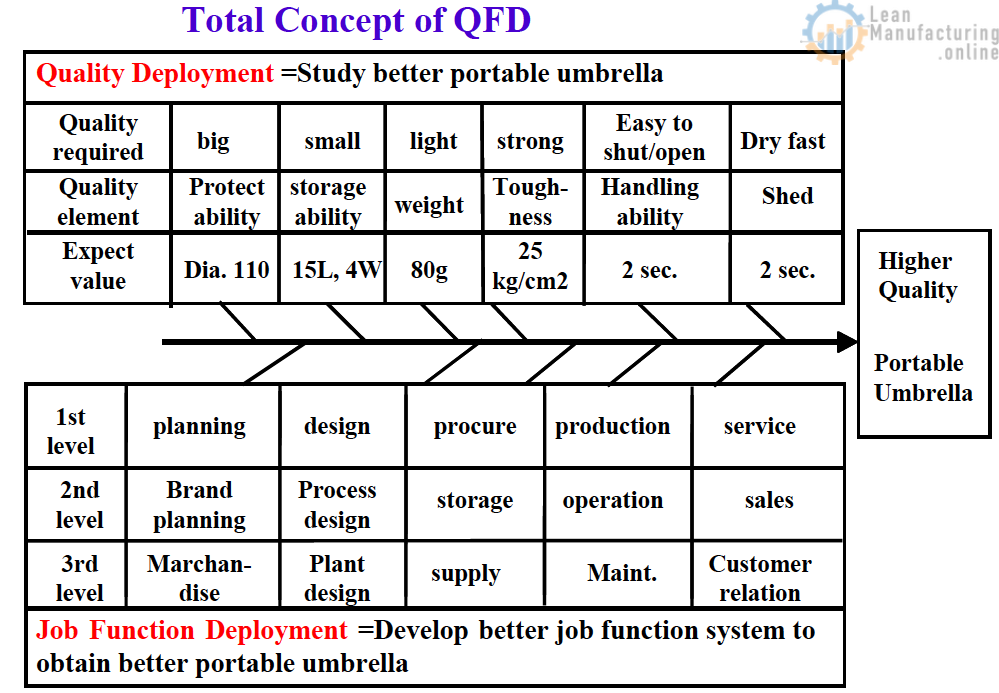
Definition of Quality Tables
- The Quality Tables are the series of matrices that formulate the terms of the user’s required actual product quality and express its relationship with the quality characteristics (quality elements).
- Hence, the Quality Tables serve to translate the customer’s required quality into counterpart characteristics in order to achieve the designed quality.
Quality Design through Quality Table
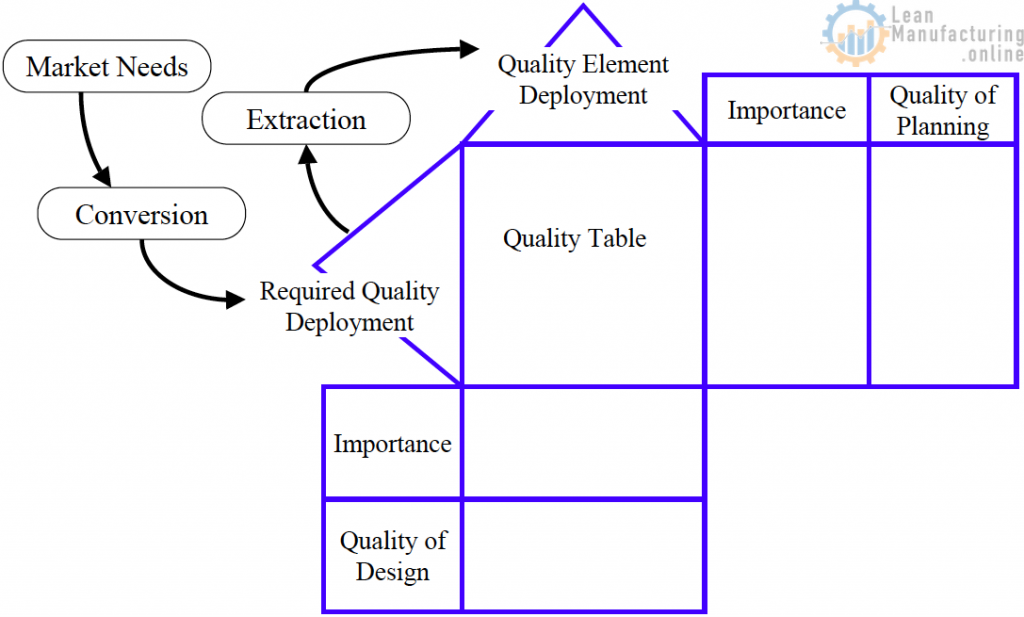
Three Points to Translate Customer Voice Objectively
- Translate from Emotional words to Logical words
- Changing Two-valued expression to Multi-valued expression
- Cautious on the stratum of Word-Abstraction Level
1. Translate from Emotional words to Logical words
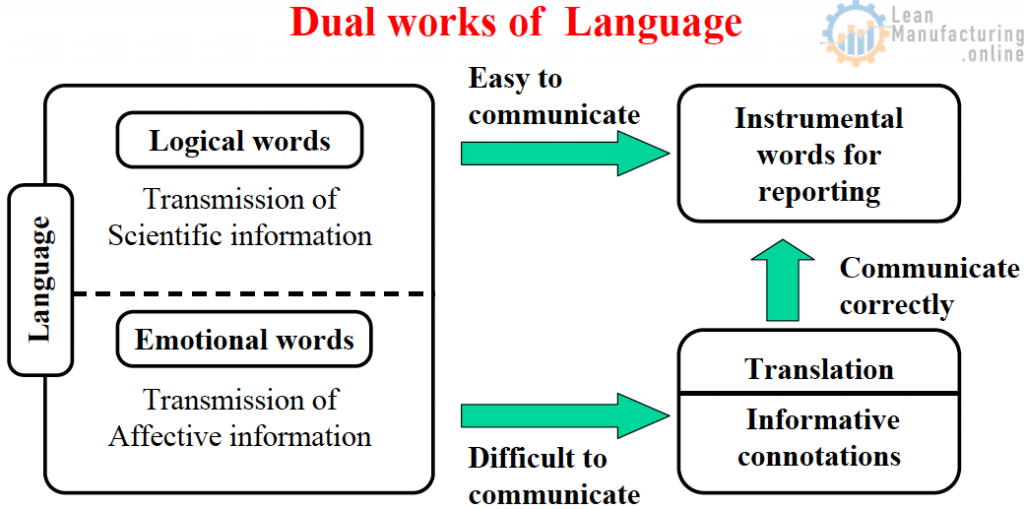
2. Changing Two-valued expression to Multi-valued expression.
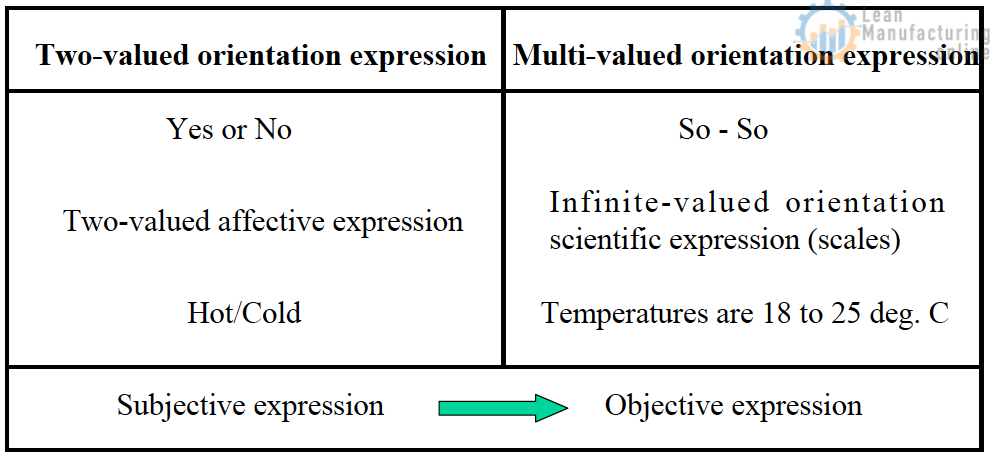
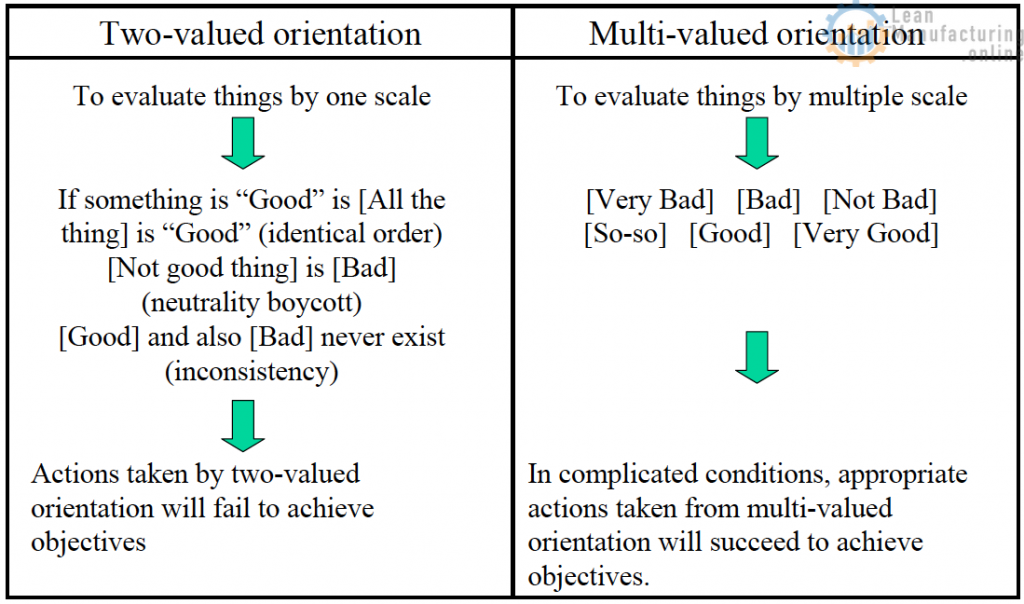
3. Cautious on the stratum of Word-Abstraction Level
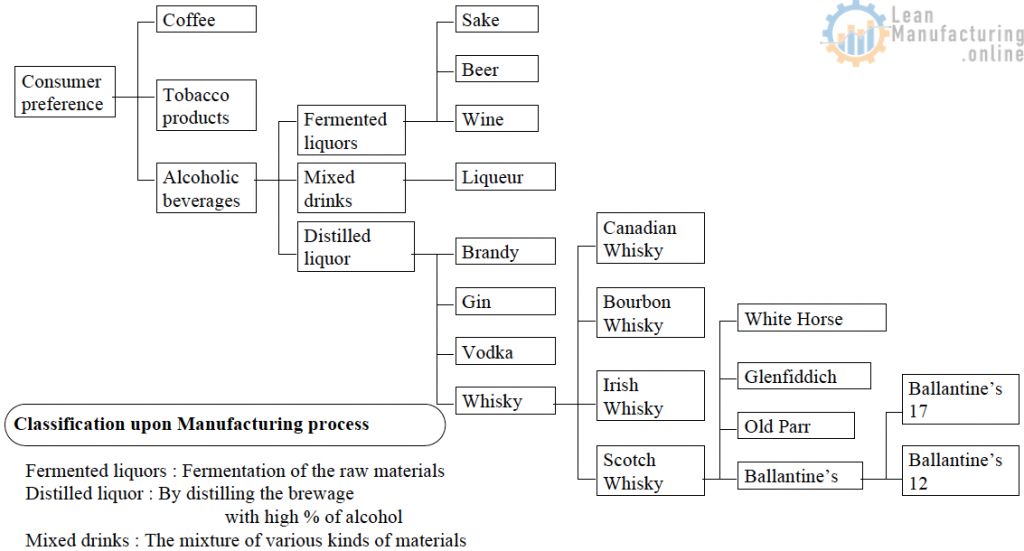
The Subject of QFD, Products or Commodities
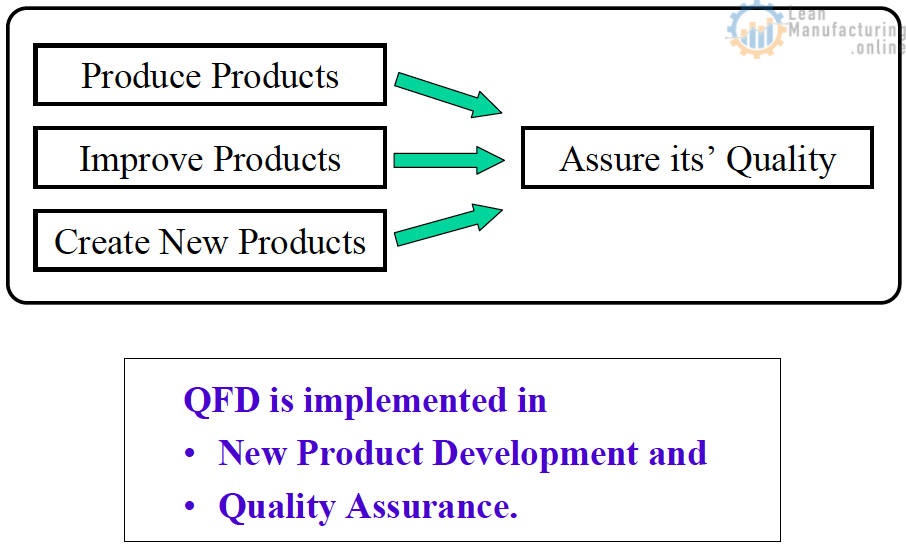
Effects of QFD
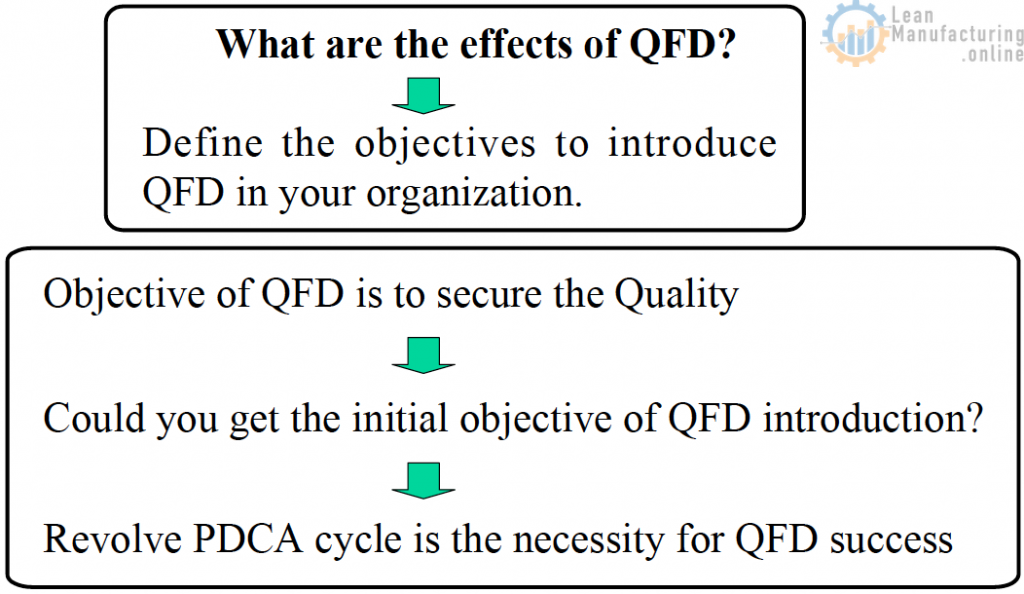
Features of QFD
- Begin to understand from consumer requirement
- Study and discuss on quality by the project team
- Clarify qualities and functions
- Put verbal information in order by focusing on qualities
- Understand required qualities by making its stratum
- Understand quality elements by making its stratum
- Put numerical values by giving correlation between two
- The quality chart makes one understand quality at a glance
- Compare & analyze the quality with competitors’ by figures
- Determine the planning quality by the quality chart
- Determine the specific design quality by the quality chart
- Deploy the business functional process by focusing on qualities
- Develop new products efficiently
- Develop quality management systems by focusing on qualities
Effects of QFD Implementation

Definition of the QFD Terms
Required Item
- Required Item is the item that is extracted from original data expressed in words (information) that are required by customer/user.
- Required Item is the comprehensive term that includes Price, Function, Production volume, Delivery time or place, Safety, Reliability, and Quality that are required by customer/user.
Required Quality
Required Quality is the term for customer/user’s requirements, demands, wants, and need which are related to the quality of products/services.
Quality Element
- Quality Element is the element of measure which evaluates the quality of products/services.
- Quality Elements are used commonly in service areas where there are no measurable characteristics for things such as “pleasantness”.
- When Quality Element acquires the measurable means, it is termed as a Quality Characteristic such as “height, width or depth”
- under the higher abstraction level of Quality Characteristic such as “shape”.
QFD Examples

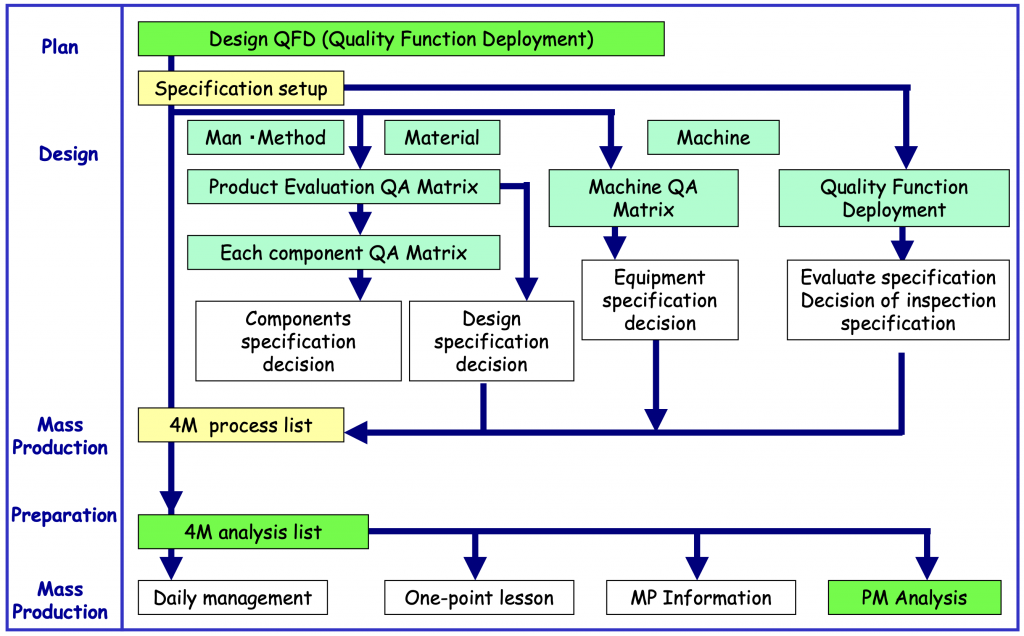