During this phase we have only one target – identify vital few and find solutions to improve them.
- Identify and select solution(s)
- Validate new process capability
- Assess and mitigate risk associated with implementing new process
- Pilot project solutions
- Implement solutions
Tools that will be used to make it happen, they are heavily dependent on the goals and objectives of your project.
- Kaizen
- Visual Workplace
- 5S
- Non-Value Added (NVA)/Waste Elimination
- Line Balancing
- JIT
- Cell Design
- Standardized Work
- Work Levelling
- SMED
If the project goal is to reduce cycle time or improve flow, tools such as 5S, Line Balancing, and Kaizen are appropriate. More complex projects, where the relationships between variables are not well understood, will rely on Six Sigma tools like regression.
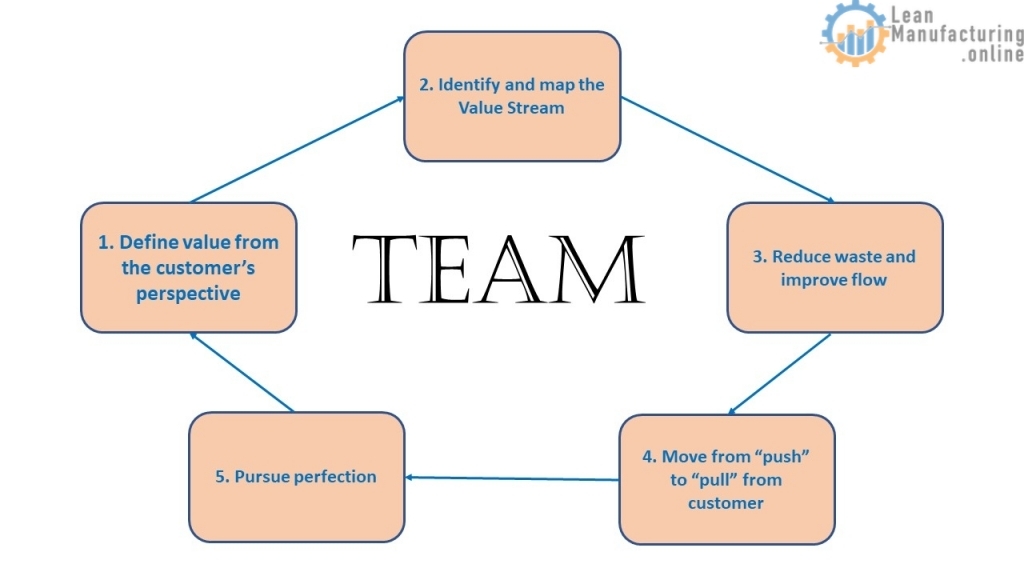
Let’s start with reviewing Lean Principles
- Reduce Waste and Improve Flow
- Move from “PUSH” to “PULL” from Customer
Basic tools to identify WASTE
- Value Stream Mapping
- Spaghetti Diagrams
- Process (Flow) Maps
- Cause and Effect Diagrams→Five Whys
- Pareto Chart
- Process Reports, Audits and Assessments
TIMWOODS
- Transportation
- Materials, inventory, information
- Inventory
- Storage, handling, carrying costs, etc.
- Motion
- Personnel, intra-office
- Waiting & Delays
- Information, people, upstream processes, etc.
- Over-Processing
- NVA steps, redundancies, etc.
- Overproduction
- More than what is required, “push”, before it is needed
- Defects, Errors, Mistakes
- Associated inspection and rework, re-do, scrap, etc.
- Skills Under-Utilized
- Knowledge and talent not leveraged Assigned to NVA activities,
Current VSM has been developed, time to create Future State one
- Aligned with organizational “Lean” strategy and objectives
- Requires significant knowledge of core lean tools and principles
- Identify waste and opportunity
- Eliminate waste, improve flow
- Not necessarily an “ideal” state but is a “future” state
- It is a “to be” model based which allows you identify and implement improvements to close gaps between current and desired future state.
How to create Future State VSM
- Calculate Takt Time
- Available time divided by the number of units required by the customer (forecasts)
- Identify Bottlenecks in the Value Stream
- Operations performed in batches?
- Operations with the longer cycle time?
- Work balancing/load levelling chart
- Identify Lot Sizing/Setup Opportunities
- Rapid/Quick change-over is key
- Identify Potential Work Cells
- Determine Kanban Locations
- Supplier to Cell? Cell to Customer?
- Establish Scheduling Methods
- Calculate Lead and Cycle Time
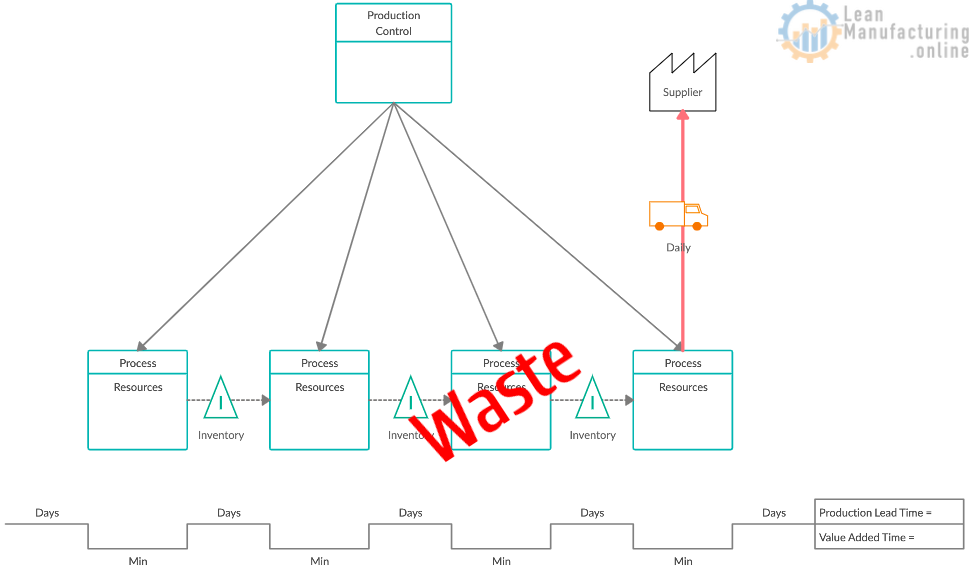
Implementation Plan
- Always keep business objectives of the product family in mind
- Avoid implementing “silo” improvements – driving sub optimization
- Break the Future State map into small manageable pieces or “loops”
- Complete a Gantt chart for all improvement activities. Include….
- What to do, when & by who?
- Goals
- Appropriate Metrics
- Breakdown of activities
- Time
- Support/Help
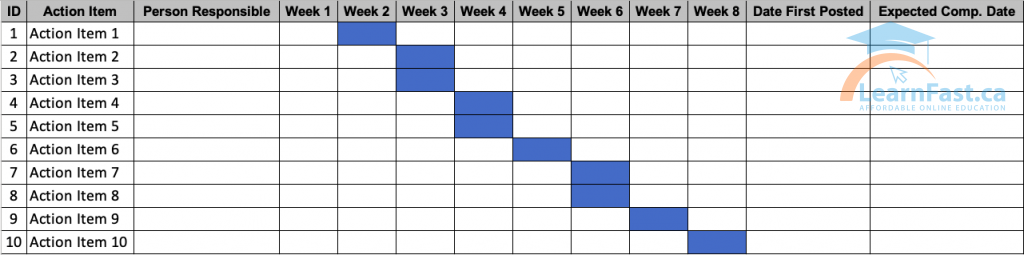
- Relate Future State map to floor layout
- Review your current layout and identify physical changes to support your Future State
- Include Layout changes on your Gantt Chart Plan
- Involve Stakeholders in Gap and Risk analysis – key to managing resistance
- Include behavioral changes in your analysis – not only process changes.