Process capability
Process Capability (Cp) is a statistical analysis of a process’s capacity to manufacture parts reliably within predetermined parameters. Depending on the stage of the process and the method used to calculate the standard deviation or sigma value, we can calculate Cp (Process Capability), Cpk (Process Capability Index), or Pp (Preliminary Process Capability), and Ppk (Preliminary Process Capability Index) to determine how our process is operating. Sample deviation or deviation mean within rational subgroups are used in the Cp and Cpk calculations. Based on the analyzed data, the Pp and Ppk computations employ the standard deviation (whole population). Statistical Control evaluates established processes using the Cp and Cpk indices. An innovative or changed approach is assessed using the Pp and Ppk criteria.
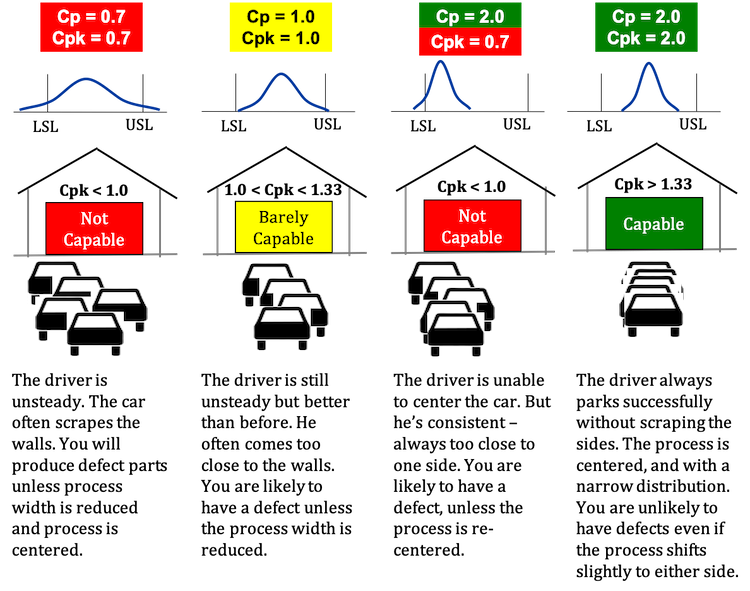
Process capability analysis is essential for quality assurance and continuous improvement projects because it makes finding opportunities for process enhancement, monitoring development, and making informed decisions easier.
Process control
Process control refers to regulating, managing, and manipulating industrial processes to produce desired results according to performance standards. It entails keeping an eye on process variables, identifying and fixing deviations from the planned performance, and modifying the process to keep it within predetermined operating parameters.
Process control ensures that a process runs within predetermined parameters and generates reliable and high-quality output. The process is monitored and adjusted by various control systems, including feedback control, feedforward control, and model-based Control, which employ sensors, actuators, and control algorithms.
Process control is frequently used to enhance productivity, continue strengthening, and reduce waste in manufacturing, chemical processing, power generation, and many other industrial operations. It ensures that the finished product complies with client demands and legal requirements, making it an essential component of quality control.
Statistical process control (SPC)
Statistics process control is a methodology used by industries to measure and control quality while products are manufactured. Statistic process control (SPC) is a scientific approach to monitoring, evaluating, and controlling systems. Statistical process contro –
- Reduce scrap and reprocess
- Assist in increasing productivity
- Assist in quality improvement
- Provide data that will help in the decision-making process
- Potential for improvements throughout the entire company.
The SPC method emphasizes continuous optimizing improvement through statistical tools to analyze data, make inferences about processes, and make decisions.
Process control vs process capability
Process control and capability are interrelated but distinctive from quality control and continuous improvement concepts. Process control refers to the procedures and methods used to maintain a production or manufacturing process within a predetermined set of guidelines. This entails real-time monitoring and modifying the process to ensure consistent output and avoid errors. Process control ensures that items produced by the process fulfill the required quality standards.
On the other hand, The capacity of a process to consistently produce outputs within a specific range of tolerance or standards is referred to as process capability. It evaluates how well an approach can provide outcomes up to par with the requirements. Analyzing historical data or carrying out a process capability analysis allows for determining process capability. Process capacity analysis seeks to understand how well a process can create outcomes that satisfy client needs while identifying areas for improvement.
In conclusion, while process capability concentrates on a process’ innate capacity to deliver outputs that satisfy client requirements, process control focuses on maintaining a consistent process output. For quality assurance and ongoing improvement, both ideas are essential.
i need training, six sigma, i really like this form
Hi ZUze, thanks for your comment. Six Sigma training can be found here