(1) Identify the true cause of the problem
When attempting to raise the speed of a machine, tests should be conducted to see what kind of problems occur in practice. The speed should be raised by about 50% and items such as the following should be checked:
- How did the Cp value change?
- Was there any change in the rate of occurrence of each type of quality defect?
- Were any new types of quality defects generated?
- How long did the cutting tools last?
- How much did the equipment vibrate?
- How many minor stops occurred?
- Was there any change in the behaviour of the materials handling equipment?
- How much did the materials handling equipment vibrate?
- Was there any vibration or change in sound during processing?
Raising the speed of a machine usually magnifies its defects, increasing the rate of occurrence of minor stops and quality problems. These should be analyzed and solved in the normal way. In the case of minor stops, this means observing them happening (or, if this is not possible, observing the behaviour of the products) until the causes are identified or at least narrowed down. In the case of quality defects, it means analyzing the equipment’s mechanisms and the construction and functions of its components until the specific causes are pinpointed.
(2) Check the effectiveness of the machine’s motions
Figure “An Approach to Increasing Equipment Speed” shows one approach to increasing equipment speed. This approach incorporates the following strategies:
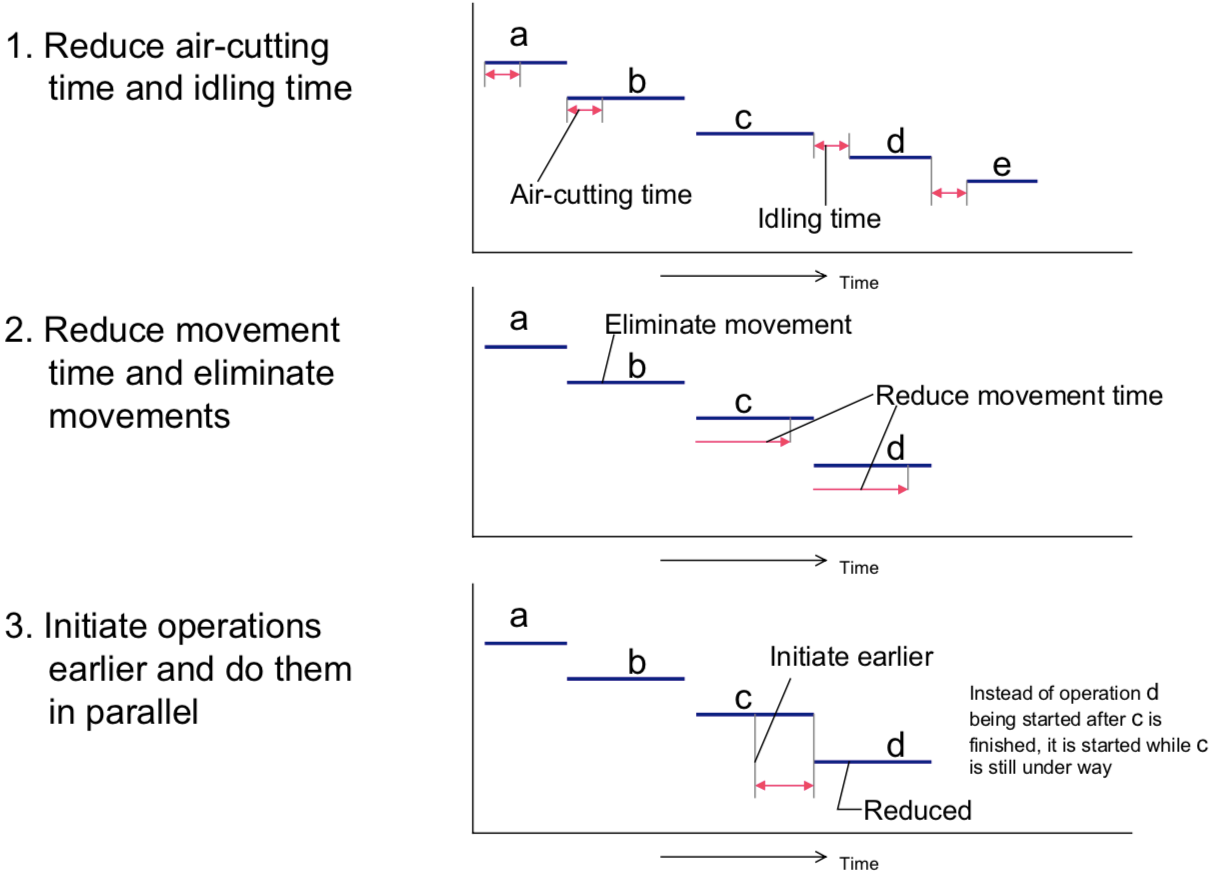
- Reduce the ‘air-cutting’ time
- Reduce the idling time between motions
- Increase the machine’s speed of movement
- If possible, perform motions in parallel
When attempting to reduce the idling time (the time wasted between motions), the first step is to measure it accurately using an instrument such as a visicorder. Such measurements often show that the idling time is surprisingly long (usually in the order of 1.5 to 2.5 seconds). The challenge is to minimize this without causing mechanical problems. If the overall cycle time is short, a reduction of as little as 0.7 to 1.0 seconds in the idling time will be of great benefit.
Increasing the machine’s speed of movement means reducing the time it takes to accomplish those movements. When doing this, the time for which the equipment is actually adding value should be measured. Three examples will be given to illustrate this:
- Grinding machines: the time interval between the loading of the workpiece and the appearance of the first spark can be monitored with a visicorder to see from the change in power consumption how much of it is value-adding and how much is not.
- Hydraulic loading and unloading devices: lost time can be calculated by comparing the theoretical value (obtained from the relationship between the weight of the workpiece, the distance moved vertically and horizontally, the diameter of the hydraulic cylinder and the capacity of the pump) with the actual value.
- Checking the possibility of parallel operations: operations conventionally performed in series should be examined to see whether there is any possibility of performing them in parallel. In many cases, sensors can be installed and the sequencer reprogrammed to allow one operation to start while another is still going on.
Regardless of which of the above three approaches is taken, the equipment’s mechanisms, the construction and functions of its parts, its timings, and the cycle line diagram prepared when the equipment was designed should all be examined carefully to determine whether any improvement is feasible. If an improvement is considered possible, it should be tested in practice. Any problems that arise should then be analyzed carefully in order to identify and eliminate their root causes. Table “Procedure for Reducing Speed Losses” shows a procedure for reducing speed losses.
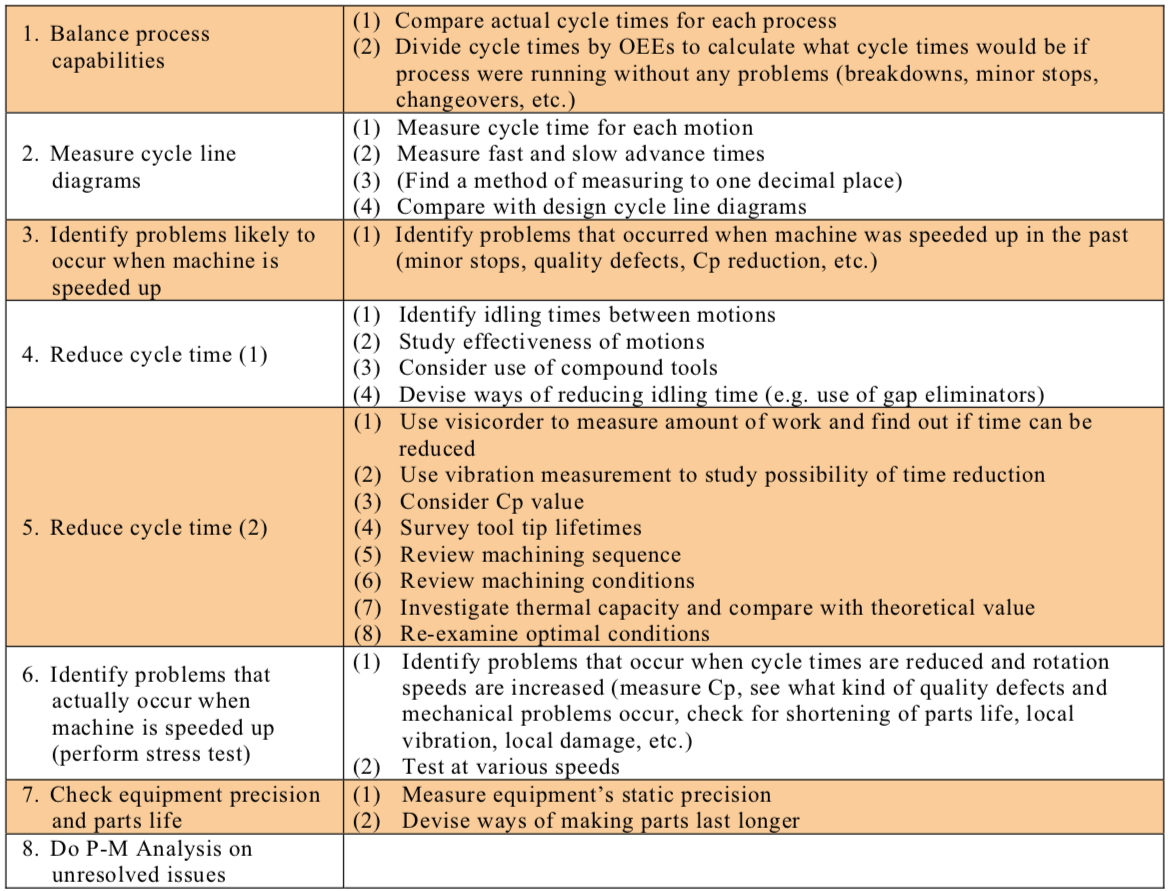