Implementation Team

Values:
- Integrity
- Demand diversity of thought!
- Responsibility and accountability
- Define & communicate roles, responsibilities, and actions plans for teams and individuals!
5W & 1H
- WHAT: Major Stoppages/Breakdowns
- WHEN: Daily
- WHERE: Packaging Lines
- WHO: Mechanic
- WHICH: N/A
- HOW: Not Enough time to Eliminate
SUMMARY OF PROBLEM:
Mechanics do not have enough time to Eliminate Major Stoppages/Breakdowns that occur daily on the packaging lines.
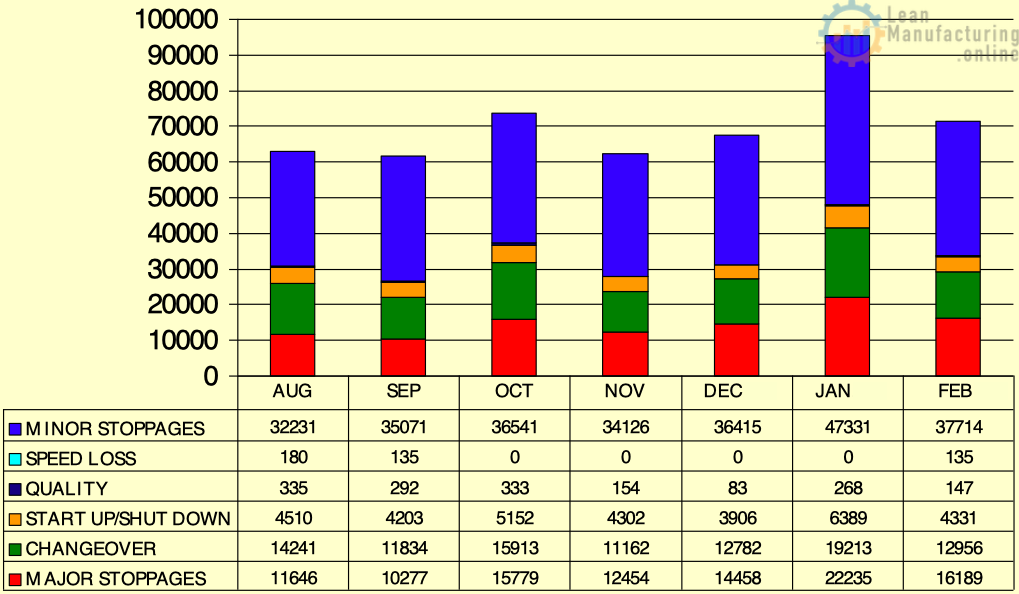
Why-Why Analysis
- WHY-1: Mechanics are still having to perform basic, routine preventative maintenance & repairs;
- WHY-2: Operators do not have the Skills & Knowledge to assist;
- WHY-3: NO FORMAL TRAINING PROGRAM EXISTS.
Developing training program
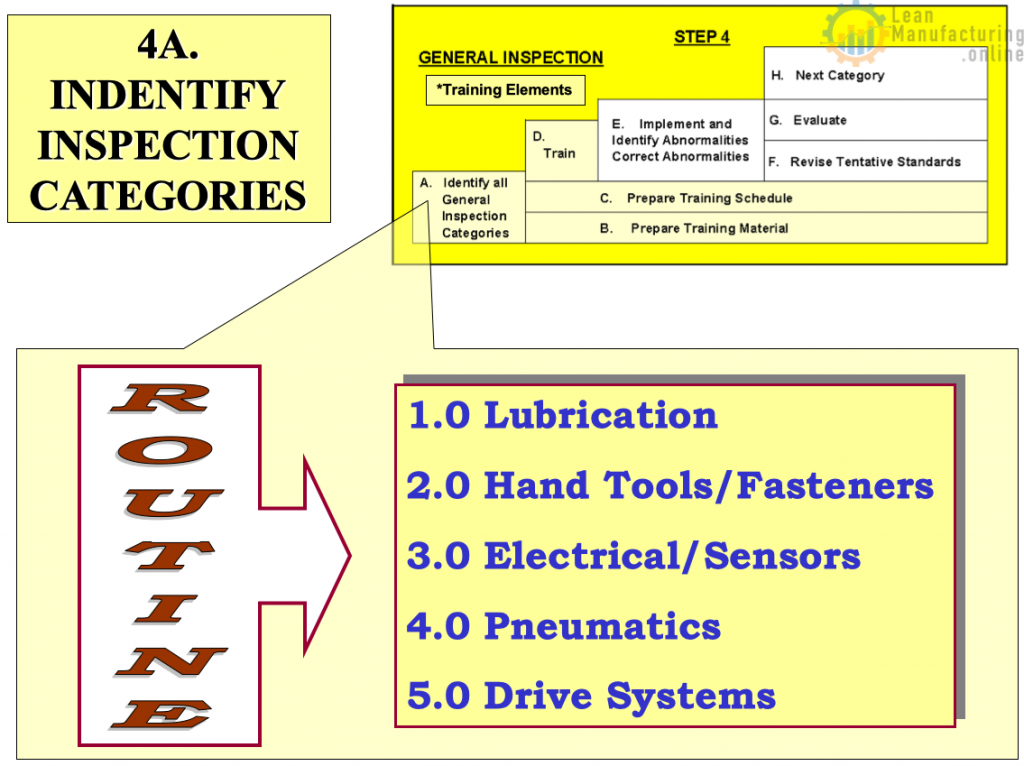
Define Skills & Knowledge
Each Module Developed with clear objectives:
- Understanding of Normal vs. Abnormal Conditions;
- Safe and proper use of or conditions for application;
- Proper Component Identification;
- Demonstrated Abilities and Skill Assessments.

Please use links below to get access to all 5 modules
- 1.0 Lubrication
- 2.0 Hand Tools/Fasteners
- 3.0 Electrical/Sensors
- 4.0 Pneumatics
- 5.0 Drive Systems
Create training schedule
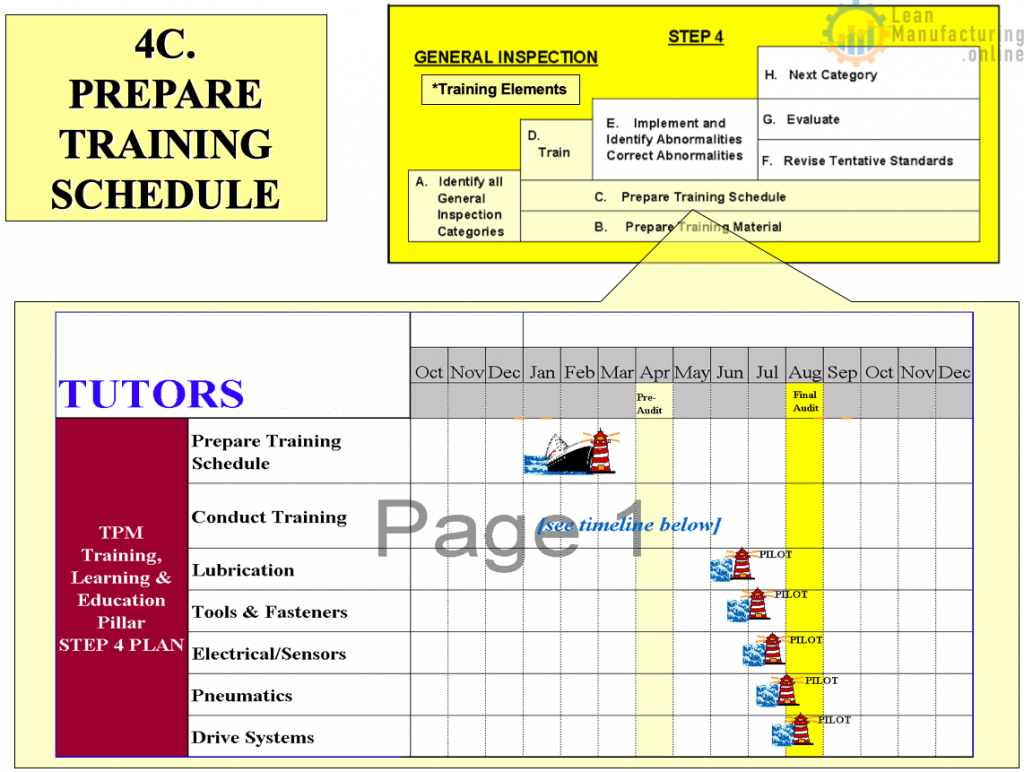
Train
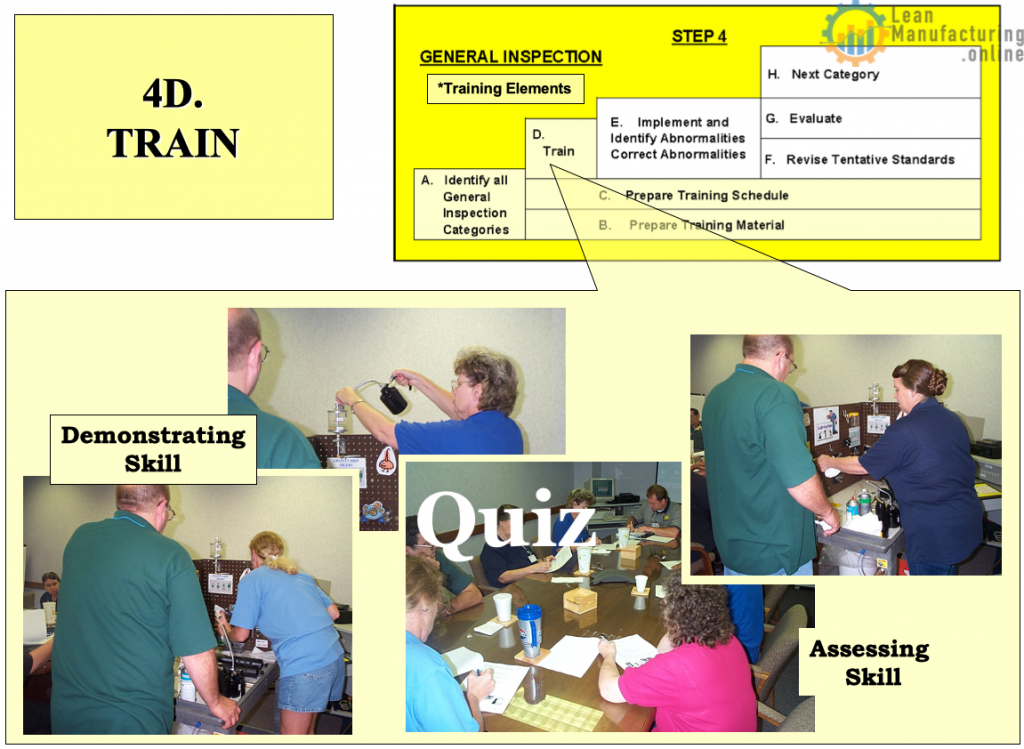
Benefits Old vs. New Training
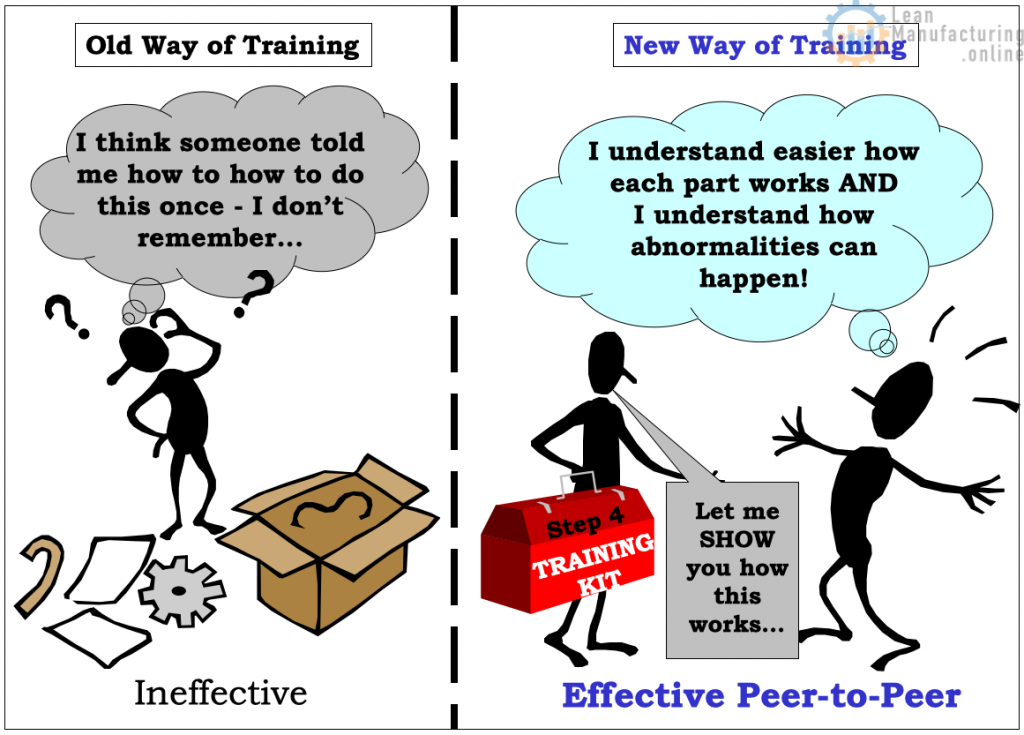
Training evaluation

Group composite scores from Pre-evaluation compared to Post-evaluation scores to evaluate effectiveness. Individual Associates must have a minimum passing score of 80% to move to the next module.
Knowledge and Skill Assessment Results. Module Session Average Scores
Pre / Post
1.0 Lubrication: 61% / 94% (100% passed)
2.0 Hand Tools/Fasteners: 75% / 94% (100% passed)
3.0 Electrical/Sensors: 52% / 92% (100% passed)
4.0 Pneumatics: 60% / 96% (87% passed)
5.0 Drive Systems: 50% / 92% (100% passed)
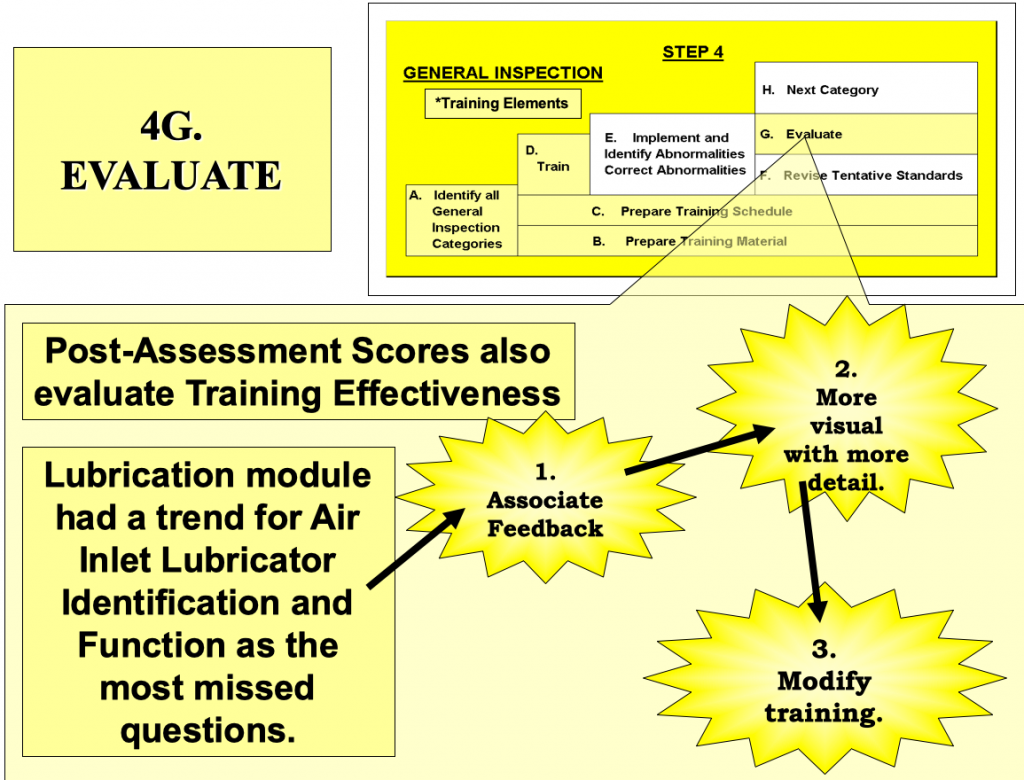
Post-Assessment Knowledge Evaluation

Modify training
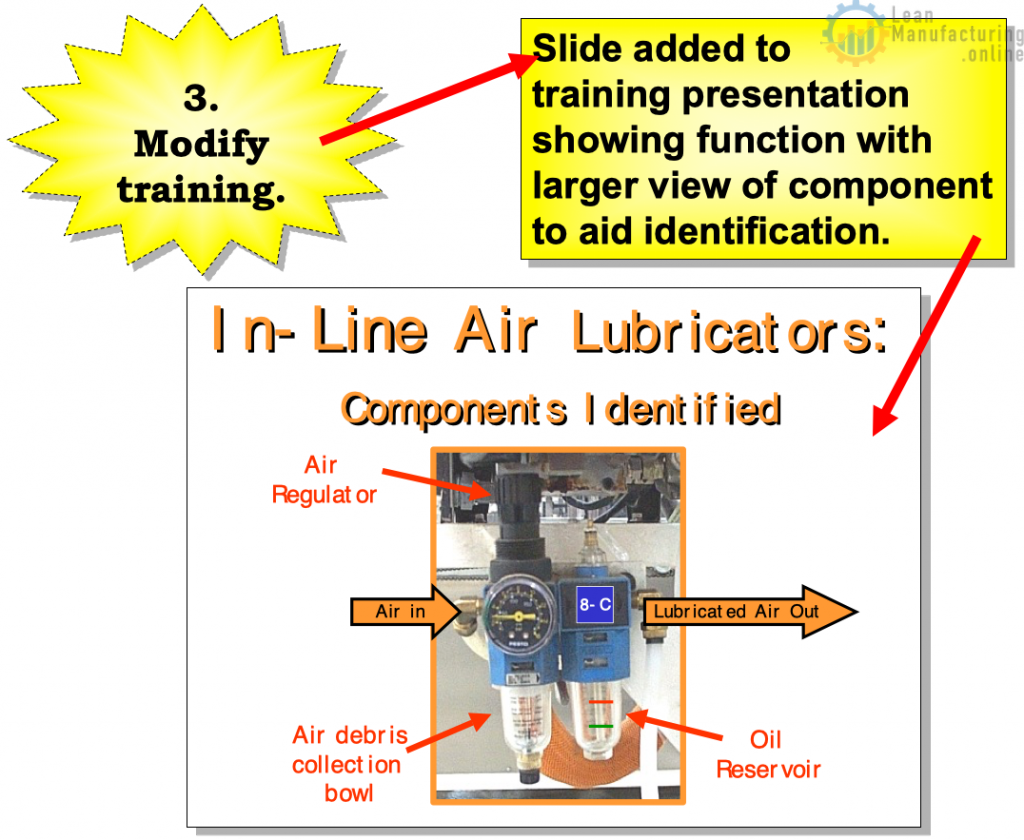
Associate Feedback = HIGHER MORALE:
- “I wish I had this training 20 years ago!”
- “I can use this.”
- “This training makes sense.”
- “No longer failures, but Planned Activity”.
Implement, Identify & Correct Abnormalities
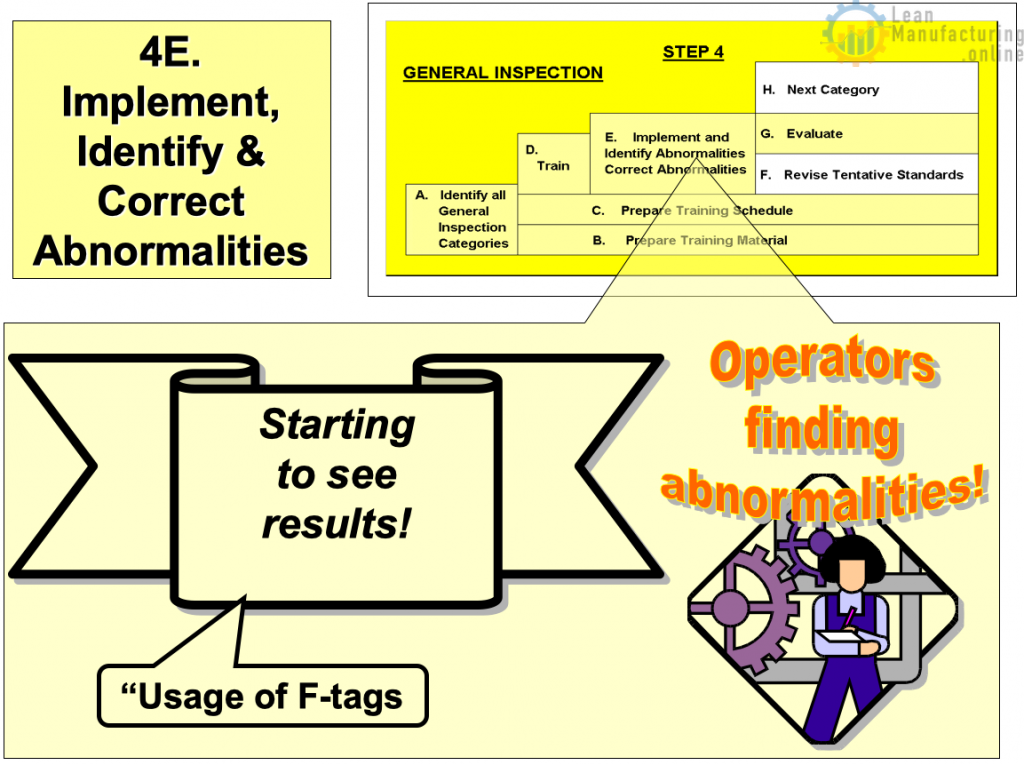