The 5 Zero-Breakdown Countermeasures will not work well if they are introduced in a rush or if more than one is implemented at a time. The best approach is to introduce them progressively in four phases. The main thrusts of the four phases, outlined in Table “The 4 Phases to Zero Breakdowns”, are explained below. If this approach is followed, breakdowns are certain to get closer and closer to zero.
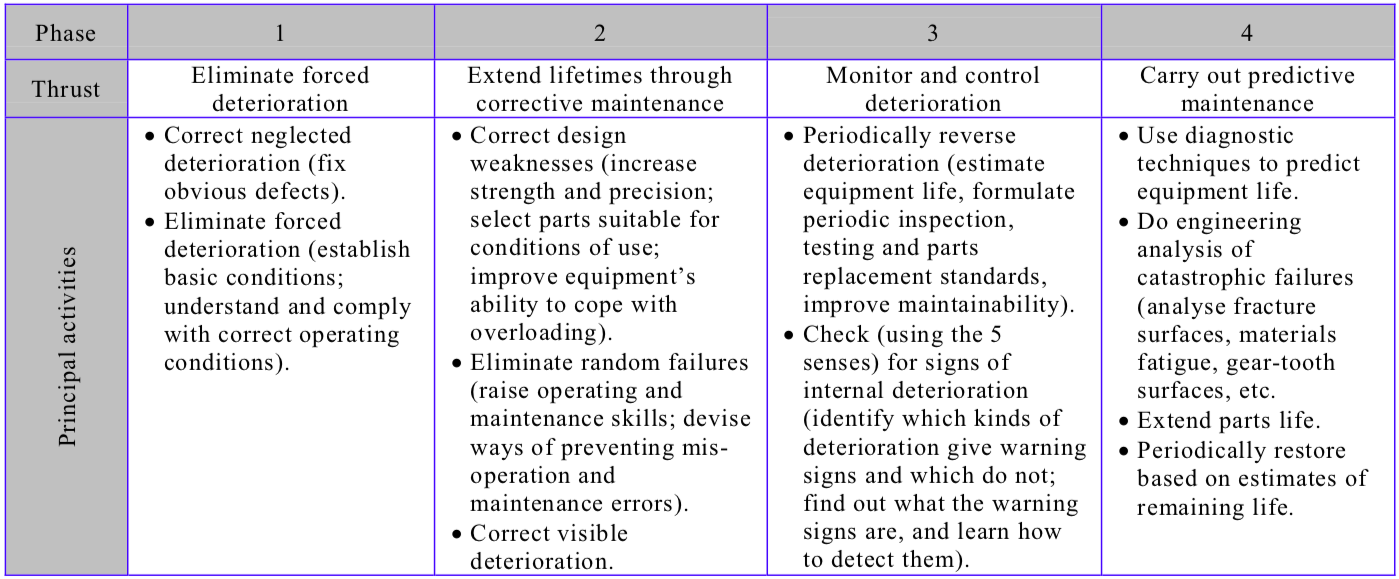
Phase 1: Eliminate forced deterioration
- Correct neglected deterioration. The first thing that needs to be done is to reverse any obvious deterioration that has been left untreated.
- Eliminate forced deterioration. Forced deterioration, which results from omitting to sustain basic equipment conditions and observe correct operating standards, is the biggest cause of variation in equipment failure intervals. Sustaining basic equipment conditions and adhering to operating standards will eliminate this variation.
Phase 2: Extend lifetimes through corrective maintenance
- Correct design weaknesses. Eliminating forced deterioration will bring the service life of equipment closer and closer to its natural lifespan (i.e. the length of time it would last for if subjected only to natural deterioration). If it still does not last long enough, this indicates a problem with the original design. In such cases, the lifetime of the equipment must be extended by correcting its inherent weaknesses. This approach to improving equipment reliability is called “corrective maintenance”.
- Eliminate sporadic breakdowns. Although most sporadic breakdowns result from misoperation, many are also due to faulty repair work. They are the most difficult kind of failure to deal with, since they are unpredictable and therefore cannot be prevented by checking or inspecting; moreover, they are often caused by excessive stress acting on a part which, under normal conditions, would never be expected to be subjected to it. They must be eliminated by reducing human error, which can be achieved by raising operating and maintenance skills, installing error-proofing devices, improving maintenance tools and procedures, and introducing fail-safe designs.
- Reverse visible deterioration. In phase 2, all relatively obvious external deterioration must be reversed, and the equipment restored to its original, pristine condition. Generally, more than 50% of all breakdowns can be avoided by eliminating visible deterioration.
Phase 3: Monitor and control deterioration
- Periodically reverse deterioration. Deterioration must be corrected regularly to maintain and further reduce the level of breakdowns attained in Phase 2. To accomplish this, parts life must be estimated, standards for periodically checking, inspecting and replacing them must be established, and equipment must be restored carefully on the basis of these standards. The most important thing when doing this is first to improve the maintainability of the equipment through corrective maintenance. If standards are set while the maintainability of the equipment is still poor, dismantling the equipment for checking or replacing parts will be excessively time-consuming and costly and in the end will not get done.
- Learn how to detect signs of internal deterioration. It is impossible to prevent every type of breakdown just by periodically reversing external, visible deterioration; operators must learn to use their five senses to detect warning signs of internal deterioration as well. Not every type of internal deterioration gives out such signs, but many do; and trained operators are often able to detect it by noticing unusual temperature, vibration, noise, light, colours, smells and movements. They should do all they can to sharpen their ability to detect the warning signs of abnormality.
Phase 4: Carry out predictive maintenance
- Predict equipment life using diagnostic techniques. When equipment life remains highly variable, or when the warning signs of breakdowns are not detectable by the five senses, cannot be detected reliably, or cannot be detected early enough, the only remaining approach is to use diagnostic techniques to predict equipment lifetimes – that is, to analyse deterioration parameters quantitatively using diagnostic equipment. Even with parts of the equipment that are on a time-based maintenance regime, it is often possible to reduce maintenance costs by the application of condition-based maintenance using diagnostic technology; in fact, it is essential to consider moving from time-based to condition-based maintenance whenever possible.
- Analyze catastrophic failures. Catastrophic failures are totally unpredictable, sudden failures that result in a total loss of function. Once the level of failures has been driven down by the application of the measures described above, almost all of the remaining failures will be of this type, or close to it. To prevent such failures from recurring, the causes of each should be subjected to a technical analysis (investigating the physics of fracture surfaces, materials fatigue, geartooth faces, stress concentrations, etc.), steps should be taken to increase the lifetimes of the relevant parts, and deterioration should be periodically reversed based on an estimate of those lifetimes. Table “A Program for Achieving Zero Breakdowns” shows a programme for achieving zero failures that summarises the points described in this section.
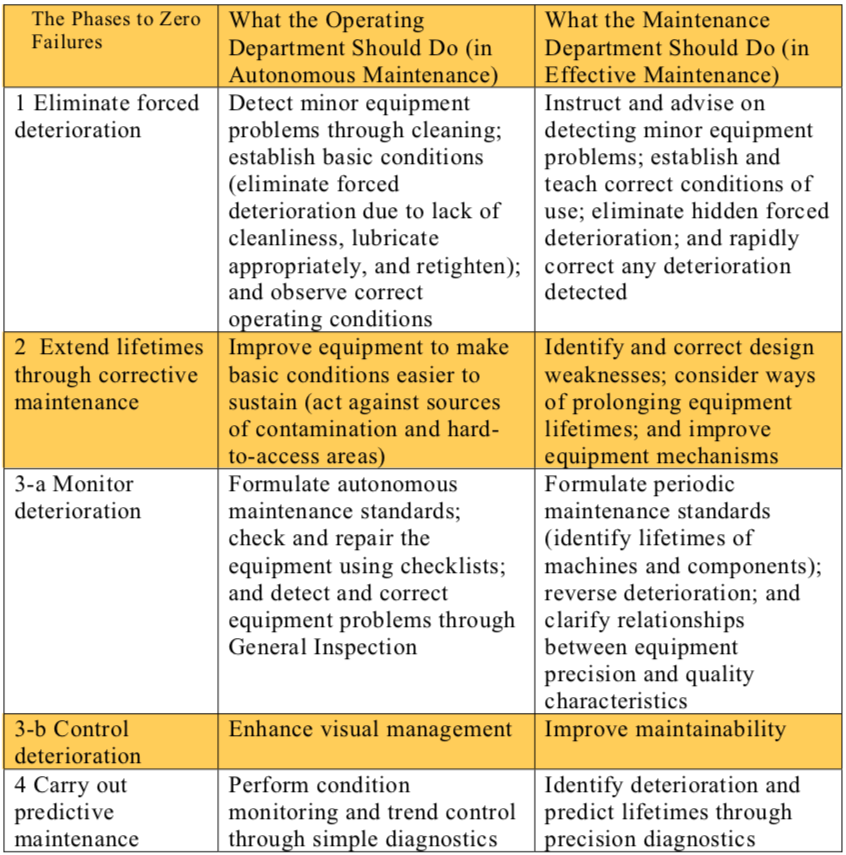