Industrial Engineering is concerned with the design, improvement, and installation of integrated systems of people, material and equipment. It draws upon specialized knowledge and skills in mathematics, physical and social science together with the principles and methods of engineering analysis and design.
Bottom line benefit
When it is all said and done, the goal is to have a system operate safely at the rated efficiency and quality throughput.
Techniques available to Industrial Engineering
- Complexity Analysis
- EPQ (Economic Production Quantity)
- Downtime Analysis
- A, B, C Analysis (Pareto Analysis)
- Material Movement Analysis
- PSMS (Production Scenario Management System)
- SMED (Single Minute Exchange Die)
- Safety Stock Determination
- Line Validation
- Yield Analysis
- SKU Pruning
- Activity Based Costing
- Plant Layout & Design
- Plant within Plant
- Warehouse efficiency studies
- Motion & Time Studies
- Work Station Design & Ergonomics
- Manufacturing Planning & Control Systems
- MRP (Materials Requirement Planning)
- Capacity Planning
- JIT (Just In Time)
- MPS (Master Production Schedule)
- Equipment Acceptance
- Line Balance “De-Bottlenecking”
- TPM Implementation
- Computer Simulations
- Automatic DT Data collection
- Line Performance Improvement Process
Industrial Engineering Techniques vs. Supply Chain
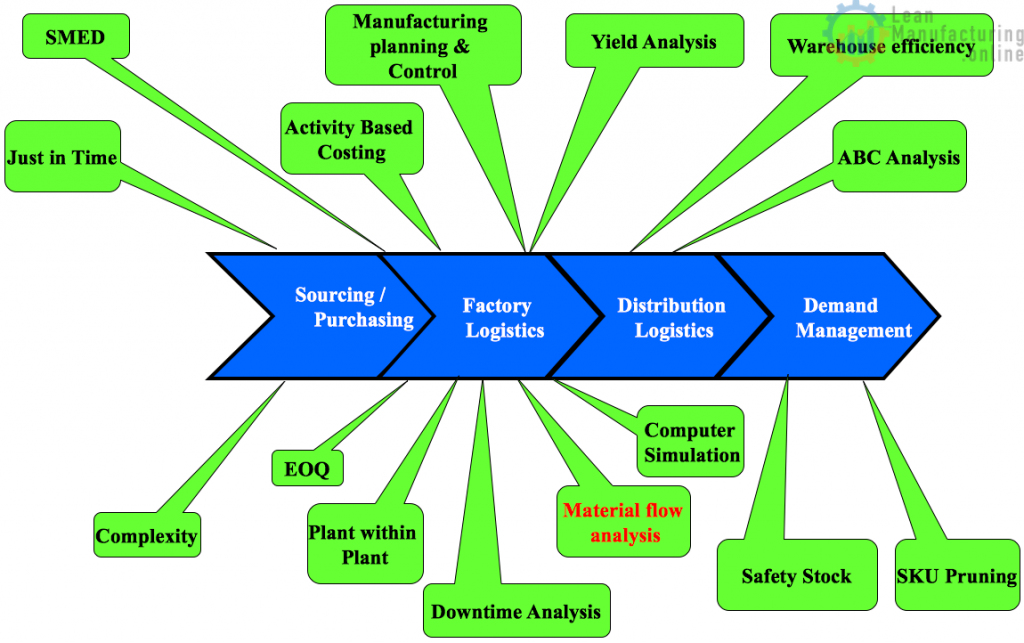
Each Industrial Engineering technique can provide insight and guidance to achieving maximum effectiveness and utilization of company assets through the entire supply chain, result Reduce costs & Grow Profits.
Overview and examples of application
Downtime Analysis – Data Collection Pyramid approach
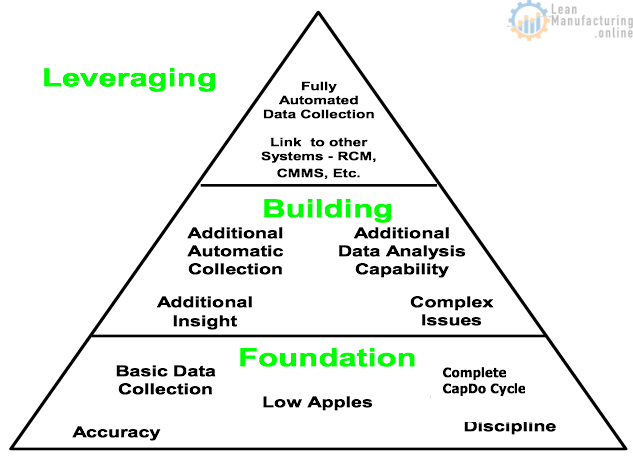
- Generate FUEL for GROWTH
- Strategy: accelerate manufacturing restructuring and reliability improvements
- Deliver Measurable Sustained Flexibility and Reliability Benefits from TPM
Downtime Analysis
- Identify and quantify equipment that needs attention
- Implement TPM FI Techniques
- Identify operator training needs
- Justify to upgrade or replace equipment
- Provide input for computer simulation
SMED Analysis
- What is it?
- A methodology to increase plant capacity and efficiency by optimizing the changeover and cleaning process;
- Experience has shown the SMED principle can be effectively applied to any process.

The basis for Rapid Changeover:
A ‘pit stop’ mentality achieves rapid response manufacturing. In auto racing, every second counts, so pit stops are highly organized and fast.
Key questions:
Can you get the changeovers on your machines faster? – are they fast and efficient? Do people know what they are doing?
Five step approach
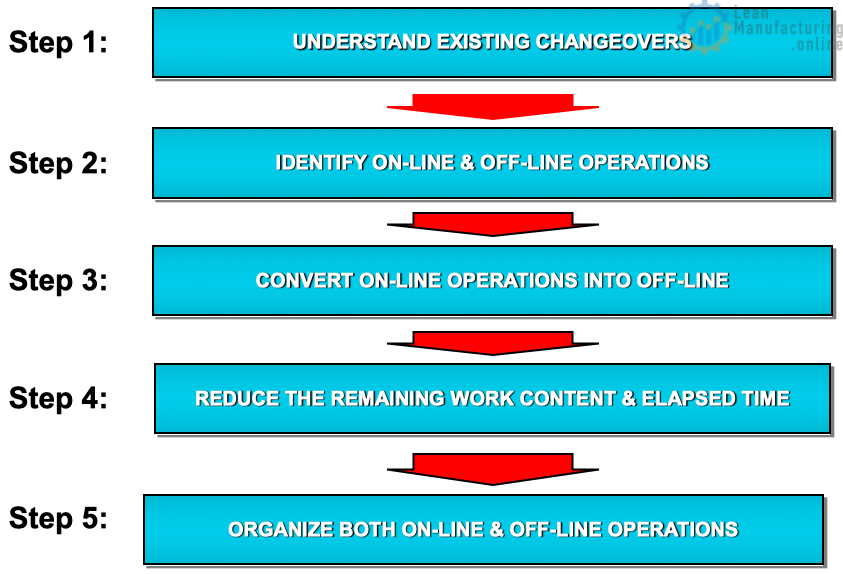
Complexity Analysis
It is a tool used to understand the relative amount of operational/organizational effort exerted to produce a quantity of product over a given timeframe.
How can it be used?
- Quantifies impact on production output due to different production scheduling strategies
- Long vs. short runs
- Campaign scheduling
- EOQ run rules
- Make to inventory
- Make to order
- Sequencing (Light to Dark or Allergens)
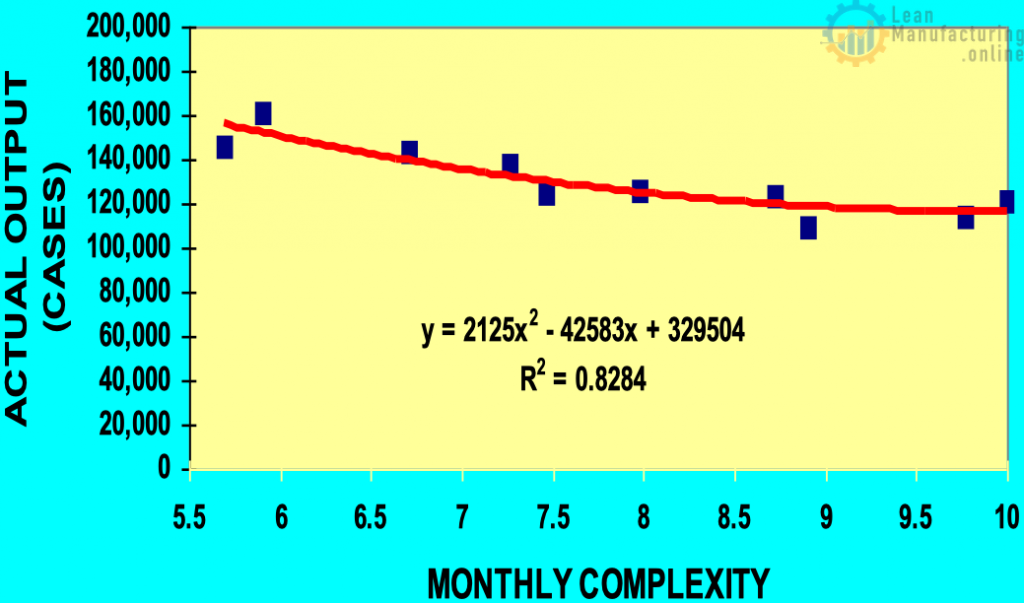
Complexity
- Reduces production efficiency;
- Dilutes management’s focus;
- It drives up the cost of doing business by increasing inefficiency in everything we do.
Economic Production Quantity (EPQ) Analysis
The quantity to be manufactured at one time minimizes the combined cost of manufacturing and the cost of carrying inventory.
- What can it be used for?
- Identify the lowest possible cost schedule for the business
- Provide insight to understand tradeoffs of different production schedules and customer service levels.
- Aid in developing accurate product costing for short-run cost penalties or high-volume price discounts
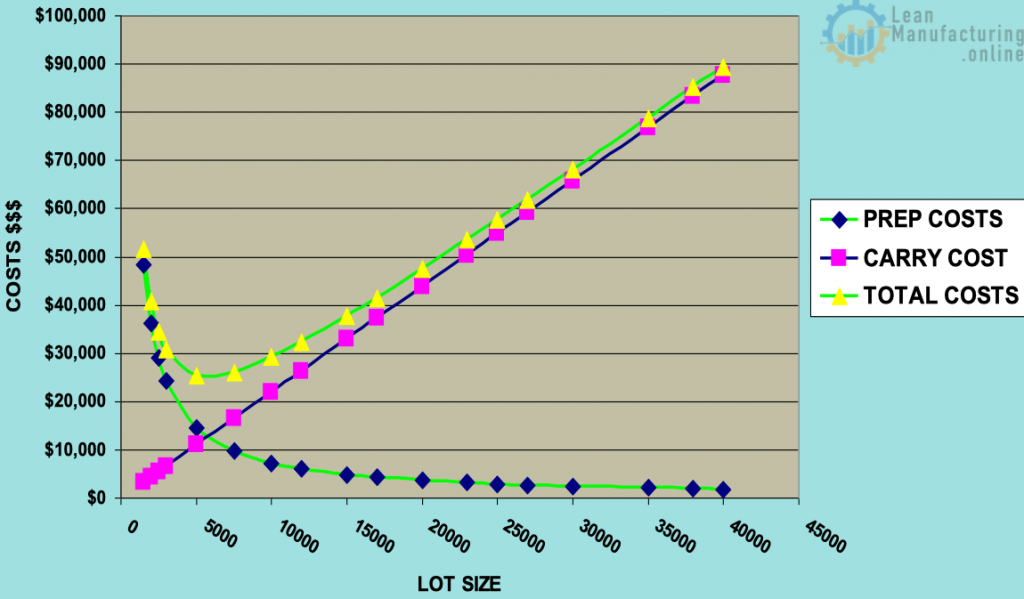
ABC Analysis
- What is it?
- Pareto Analysis (Sales, Profit, Costs, Etc.)
- A = Top 20%
- B = Upper Mid 30%
- C = Lower Mid 30%
- D = Bottom 20%
- How can it be used?
- Identify where management effort should be focused to gain the biggest bang for the buck.
- Supports SKU Pruning – low-profit SKUs
- Assist in production scheduling
- line selection
- plant within plant
Summary
- We have Rediscovered the Value Of Industrial Engineering.
- Benefits Of Optimizing Across Entire Supply Chain
- Need To Accelerate Change To Plant Floor
- New Techniques Can Be Added As We “Borrow With Pride” – Best Practice Team
- Need To Leverage These Techniques Were Appropriate
- Optimizing And Leveraging Existing Assets
What is Engineering Management?
Engineering management is the discipline that deals with applying engineering principles to the planning, design, operation, and control of projects, systems, and organizations. Engineering managers are responsible for ensuring that projects are completed on time, within budget, and to the required quality standards.
Responsibilities of an Engineering Manager
The responsibilities of an engineering manager are varied and can include the following:
- Project management: Engineering managers oversee projects from conception to completion. They ensure that all project objectives are met and the project is completed within the given time frame and budget.
- Team management: Engineering managers manage a team of engineers and other technical staff. This includes hiring, training, supervising team members, and ensuring they have the necessary resources to complete their work.
- Budget management: Engineering managers are responsible for managing their projects’ budgets. This includes creating budgets, monitoring expenditures, and making adjustments as necessary.
- Technical expertise: Engineering managers are expected to have a deep understanding of engineering principles and the technical aspects of their projects. This allows them to guide and oversee their team members and make informed decisions about project direction.
Skills Needed for Engineering Management
To succeed in engineering management, individuals must possess unique skills that balance technical expertise with business acumen. Some of the critical skills needed for engineering management include:
- Leadership: Engineering managers must be strong leaders who inspire and motivate their team members to achieve their goals.
- Communication: Effective communication skills are essential for engineering managers, as they must communicate complex technical concepts to non-technical stakeholders and vice versa.
- Problem-solving: Engineering managers must be skilled at problem-solving and think critically to identify solutions to complex problems.
- Project management: Strong project management skills are essential for engineering managers, as they ensure that projects are completed on time, within budget, and to the required quality standards.
- Technical expertise: Engineering managers must have a deep understanding of engineering principles and the technical aspects of their projects. This allows them to guide and oversee their team members and make informed decisions about project direction.
Conclusion
Engineering management plays a crucial role in any engineering organization. Engineering managers are responsible for ensuring that projects are completed on time, within budget, and to the required quality standards. To succeed in engineering management, individuals must possess unique skills that balance technical expertise with business acumen, including leadership, communication, problem-solving, project management, and technical expertise.