3. TPM Techniques (Principally Quality Maintenance)
The basic thinking behind the techniques used in TPM to reduce equipment losses and reverse deterioration is to apply physical principles and parameters (such as principles of processing). This contrasts with the approach used in TQM (typically, in SQC), where potential causes are analysed by examining the data. In other words, while SQC uses the inductive approach, TPM can be said to employ the deductive approach, in which principles and parameters are studied and then applied from the top down. P-M (Phenomenon/Mechanism) Analysis is the foremost example of this.
P-M Analysis has been defined as ‘an approach for physically analysing a chronic problem phenomenon in accordance with principles and parameters, explaining the phenomenon mechanism, and listing all the factors that could logically be considered to affect it, from the standpoint of equipment mechanisms, people, materials and methods’. It was originally devised in order to overcome the weaknesses inherent in conventional SQC-type techniques for analysing potential causes. Gaps are identified by comparing the existing state of the phenomenon with the ‘ideal, optimal’ state derived deductively, enabling even minor defects to be highlighted as problems and equipment to be restored and improved through the elimination of chronic losses.
Figure 2 shows the P-M Analysis approach together with an example. The 4 Ms in this example are the basic 3 Ms (machines, materials and methods) together with the measurements (sometimes men/women are also included as a fifth M) needed for securing the required product quality. Starting with the phenomenon, the conditions that give rise to that phenomenon (the ‘contributing conditions’) are listed, based on the mechanism by which the phenomenon occurs. These conditions are then broken down into their relationships with the 4 Ms, and the actual situation is verified. All the ‘Not-OK’ items (items for which the correct conditions are not in place) are found, enabling the true causes of the phenomenon to be identified and eradicated. To implement P-M Analysis like this, it is essential to understand the principles of processing and other theoretical aspects, which is why the training operators receive during Step 4 (General Inspection) of Autonomous Maintenance is so important. In practice, simpler versions of P-M Analysis such as ‘Why-Why Analysis’ (in which the question “Why?” is asked repeatedly) are often used.
In Quality Maintenance, which has close parallels with TQM, a procedure called the Figure-of-Eight Method, consisting of the seven steps shown in Figure 3 (identifying the existing situation, carrying out restoration, establishing and maintaining the conditions that will ensure zero defects, and so on) is adopted. In the process of applying this method, the investigating team checks what kinds of defect arise in which processes and draws up a QA Matrix showing what equipment conditions, method conditions and other conditions must break down in which processes in order for these defects to occur. At the same time, they apply P-M Analysis and other techniques to each defect mode in order to eradicate its causes and develop more and more ‘zero cases’ (situations in which quality defects have been eliminated).
Through these activities, new conditions (‘zero-defect conditions’) are established that will ensure consistently defect-free products. Details of the 4-M checks that must be carried out in order to sustain the zero-defect conditions for each of the product’s quality characteristics are compiled on a matrix called a ‘QM Matrix’. Any equipment components that will inevitably give rise to quality problems if allowed to deviate from the standards specified in these checks are highlighted as ‘Q components’ on this matrix. The Q components are also identified by stickers on the machines themselves, with information on what part must be checked, what standard must be maintained, and how often the check should be performed. The idea of doing all this is to ensure that the conditions are rigorously controlled.
During the development of this system, SQC tools such as design of experiments or quality engineering may be used at the steps in which the zero-defect conditions are being established or improved. Outstanding results are often efficiently achieved by applying refined approaches such as these after any deterioration in equipment, methods or conditions has been corrected; in other words, after any unnecessary sources of error have been eliminated. This may indeed be a result of the synergy generated by combining TPM with the QC approach. There is a tendency in Japan to think of TPM and QC as being in separate camps, but some organisations in other countries have combined the two approaches into a single initiative that they call TPQM.
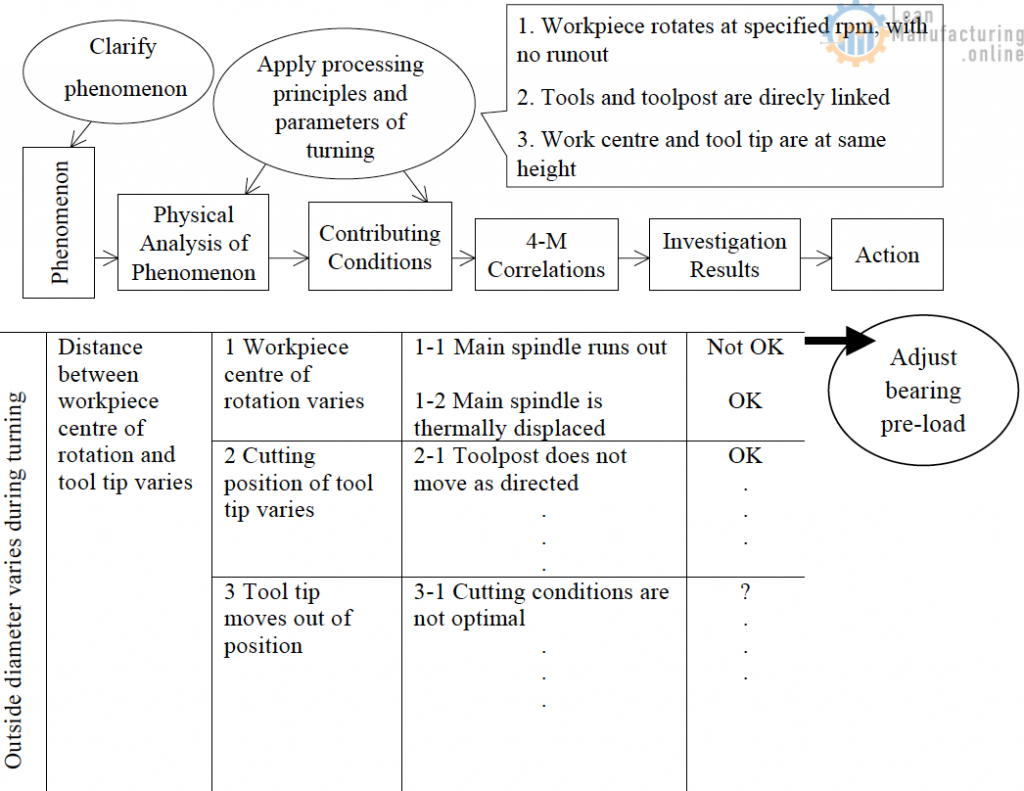
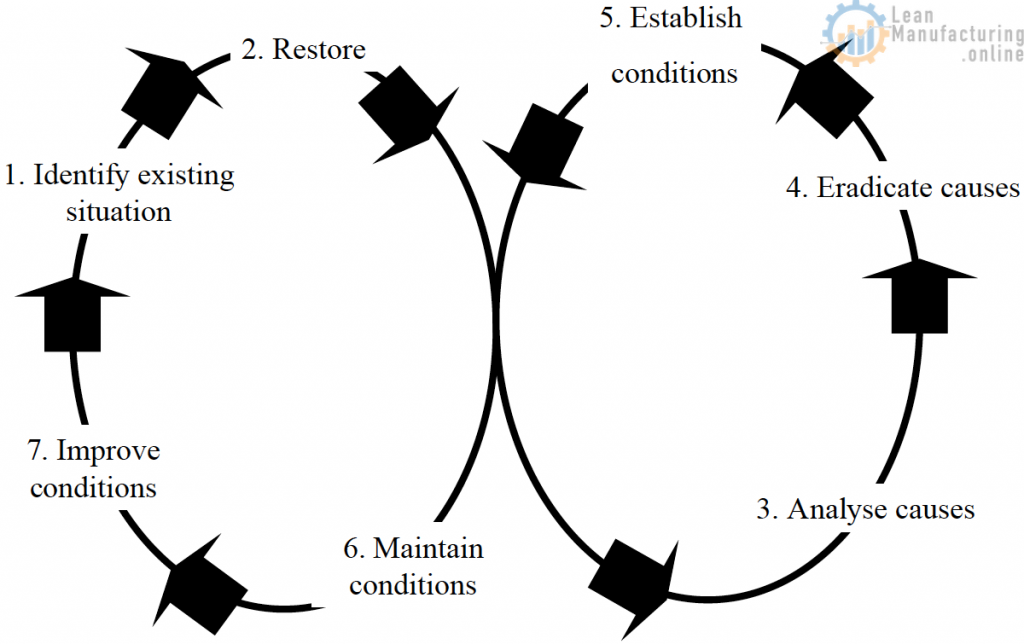
4. The TPM Awards and Recent Trends
There is a twelve-step set of guidelines describing what an organisation must do to introduce TPM systematically and reach the level required to receive an audit for the JIPM’s Award for TPM Excellence. Companies usually take about three years to reach this level. Most prizewinning sites call this stage Level 1, and most of them continue their TPM journey into Levels 2 and 3, aiming for successively higher awards. In addition to the Awards for TPM Excellence in the 1st and 2nd Categories (the 2nd Category is for small to medium-sized enterprises, while the 1st Category is for large ones) and their associated Awards for Excellence in Consistent TPM Commitment, there are higher awards such as the Special Award for TPM Achievement, the Advanced Special Award for TPM Achievement, and the Award for World-Class TPM Achievement.
TPM has penetrated into all types of industry, including process as well as fabrication and assembly. Hundreds of awards have been won by sites operating in each of the following sectors, listed in descending order of numbers of awards won: automobile components, transportation equipment, semiconductors and electronic devices, chemicals, foods, and rubber and plastic. Most of the awards won by companies in Japan have been Awards for TPM Excellence in the 1st category, but the proportion of Awards for Excellence in Consistent TPM Commitment and the next-higher Special Awards for TPM Achievement has increased recently, particularly in Japan. As discussed later, the basic form of TPM now seems to have reached its maturity stage.
Due to the increasing introduction of TPM by sectors close to being service industries, such as printing and foods. Because of the food industry scandals in recent years, and because food manufacturing faces its own particular issues, TPM is making a particular contribution to quality assurance in this sector. Identifying and eliminating sources of contamination by insects and other foreign materials, for example, is built into Autonomous Maintenance programs and other TPM problem-prevention initiatives. While systems like ISO and HACCP consist of documenting rules and standards and ensuring they are complied with, TPM is positioned as an activity for eliminating the root causes of problems.
TPM at sites outside Japan is characterised by faithful adherence to the basic principles, against a background of strict hierarchical divisions (managers, engineers, technicians, associates) and demarcation of duties. The level of application is also sustained in developing countries, and the TPM program links directly to the business, or is made to link to it. For example, when a tough question like “How much does this loss reduction actually reduce your costs or boost your profit?” is asked at a site outside Japan, the reply usually quotes a much higher figure than when the same question is asked at a site in Japan.
5. TPM Levels 2 and 3
As an improvement methodology based on equipment or processing principles and parameters, TPM could be described as an essential manufacturing requirement. However, in a low-growth economy such as the one Japan has experienced recently, a site may still find its machines at a standstill, no matter how high their OEE may be, or how capable their equipment and people have grown through the application of TPM at Level 1. In circumstances like these, however much process losses within the factory are reduced by extending the activities carried out during Level 1, this does not always translate into an actual reduction in costs or a real increase in profit.
This situation can be described in terms of the theory of constraints (TOC) by saying that the constraints on profit and cash flow have shifted outside the factory into areas such as sales. The first requirement is therefore to expand the TPM program with the constraints determining present and future operating profits clearly in mind. A new form of TPM in sales and in the supply chain is now beginning to be implemented, and JIPM has started to construct a formal framework for it under the banner of Total Production Management.
An examination of the TPM Level 2 and 3 activities actually being carried out by companies or sites that have recently won an Award for Excellence in Consistent TPM Commitment or a Special Award for TPM Achievement reveals that they are implementing one of a number of different types of TPM (see below), depending on the constraints they face, while continuing to implement the basic seven-step Autonomous Maintenance cycle.
(1) Adopting a rigorous approach to craftsmanship and raising the level of sophistication of production technology (constraint: production technology)
Raising the standard of Focused Improvement, Quality Maintenance and Effective Maintenance can lead to the discovery of new production techniques. Some initiatives focus on accumulating improvements in which mechanisms have been thoroughly investigated, and refining SQC tools and analytical techniques with the aim of establishing optimal conditions, leading to the discovery of new production techniques that eliminate processes or render them fully automated, thereby establishing core manufacturing competencies. Other approaches focus on evolving new diagnostic techniques with the aim of sustaining zero-defect conditions by means of control systems based on electrical power usage patterns – initiatives that could well be described by the term ‘digital manufacturing’.
(2) Shifting the focus of TPM to new-product development or the sales department (constraint: the market)
When spare equipment or labour capacity is created through the activities carried out in Level 1, the issue turns to how to boost sales in order to utilise that spare capacity. In such a case, the constraint on business indicators such as profit has shifted from the factory to the market, and the TPM program must switch from a defensive posture to an attacking one, focusing on increasing sales of existing products or developing new ones. In TPM in sales, for example, the focus could be on identifying and reducing the losses that hold back sales, while in new-product development it could be strengthening the early product management pillar within the eight-pillar program.
(3) Creating new value by reforming the business structure (constraint: business)
This is a response to the shrinkage or even disappearance of the organisation’s core business as a consequence of rapidly-changing market conditions. For example, one Japanese firm responded to the halving of the number of buttons produced in Japan resulting from the rise of Chinese manufacturing by further developing the moulding expertise it had developed in Level 1 and diverting it into the production of components for electronic devices. Another firm that produced printing plates foresaw that its business would disappear as the process went electronic, and used its activities in Level 2 and Level 3 to switch into internet businesses and other totally different fields.
(4) Expanding into the supply chain (constraint: supply-chain transparency)
This type of TPM is now required throughout the whole of manufacturing. In the food industry, for example, freshness is a particularly important requirement, but it cannot be assured, nor can total stocks be reduced, if what happens between the factory and the wholesaler and retailer is still unclear, even if during Level 1 transparency in the factory has been increased and inventories there have been reduced. Conditions at raw-material suppliers must also be made visible if the quality of raw materials is to be assured. This represents an evolution of TPM to encompass the entire supply chain.
6. Competitive Advantage in Manufacturing
This article has described the basic form of TPM, its maturation, and recent trends in adapting it in response to changes in the business environment companies now find themselves in. To secure competitive advantage in manufacturing, improvement approaches such as TPM and TQM for responding to change are essential in addition to standardization. Two further viewpoints – the supply chain and product life-cycles – must now be introduced in order to gain a competitive advantage in today’s business environment. The first of these consists of making the entire supply chain transparent and sharing information throughout it, while the key to the second will probably be management at source, in addition to development technology expertise.
If a company or site can establish a vision that clearly orients the core competencies of itself and its production sites, having anticipated forthcoming changes from the perspective of its supply chain and product life-cycles and identified the constraints within these, while continuing to implement basic TPM (the foundation of good manufacturing), the unique form that its initiatives should take will naturally become apparent.