Verify the Existing Situation
In this step, the existing situation is analyzed to establish baseline values and targets for the Quality Maintenance project and plan for its smooth implementation.
The specifications for the product in question are confirmed, and all quality characteristics and defect modes that may affect these specifications are identified. A flow chart for the processes that determine the quality of the product is then created, and the defect situation and phenomena are studied and stratified. The financial costs of the defects themselves, together with the associated complaints and inspections, should be calculated and made known to everyone concerned.
(1) Confirm quality standards and characteristics
Based on the product specifications, product characteristics, production standards, and inspection standards, we identify the quality characteristics that must be maintained.
(2) Create a flow diagram of individual processes that determine product quality
First of all, a flow chart of the individual processes that determine product quality should be created (see the upper part of Figure “Example of Process Flow Diagram and Control Items”).
Also, the equipment systems’ mechanisms, functions, processing principles, sequences, etc. should be identified. The control items (standards and methods) that have been established for maintaining quality in each process should be surveyed and entered into the process control flowchart (see the lower part of Figure “Example of Process Flow Diagram and Control Items”).
(3) Investigate defect situation and phenomena, and stratify
Here, we seek to understand the circumstances under which a defect occurred during processing. We stratify the defect phenomena and identify the particular processes in which they occurred.
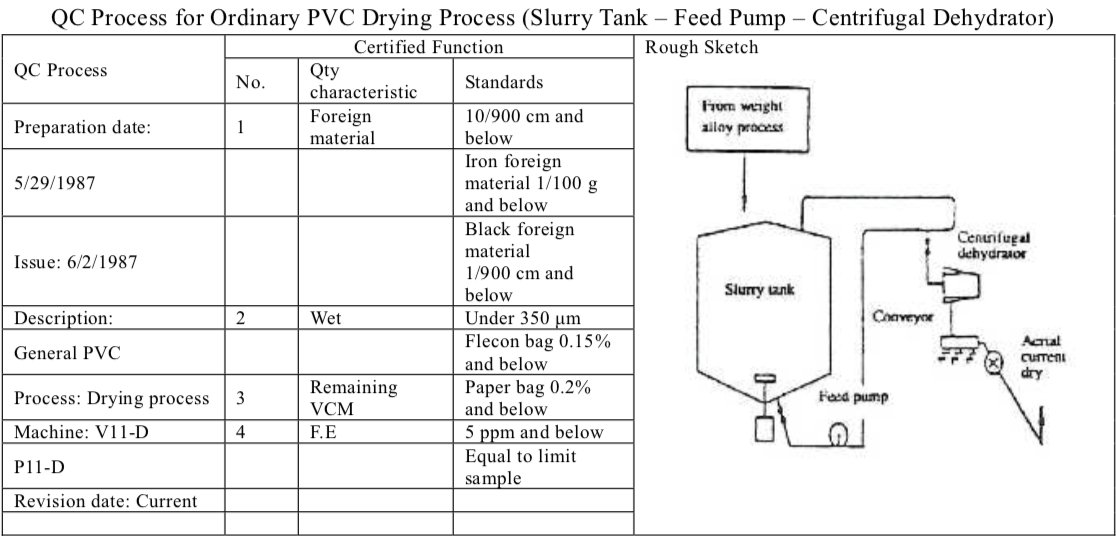
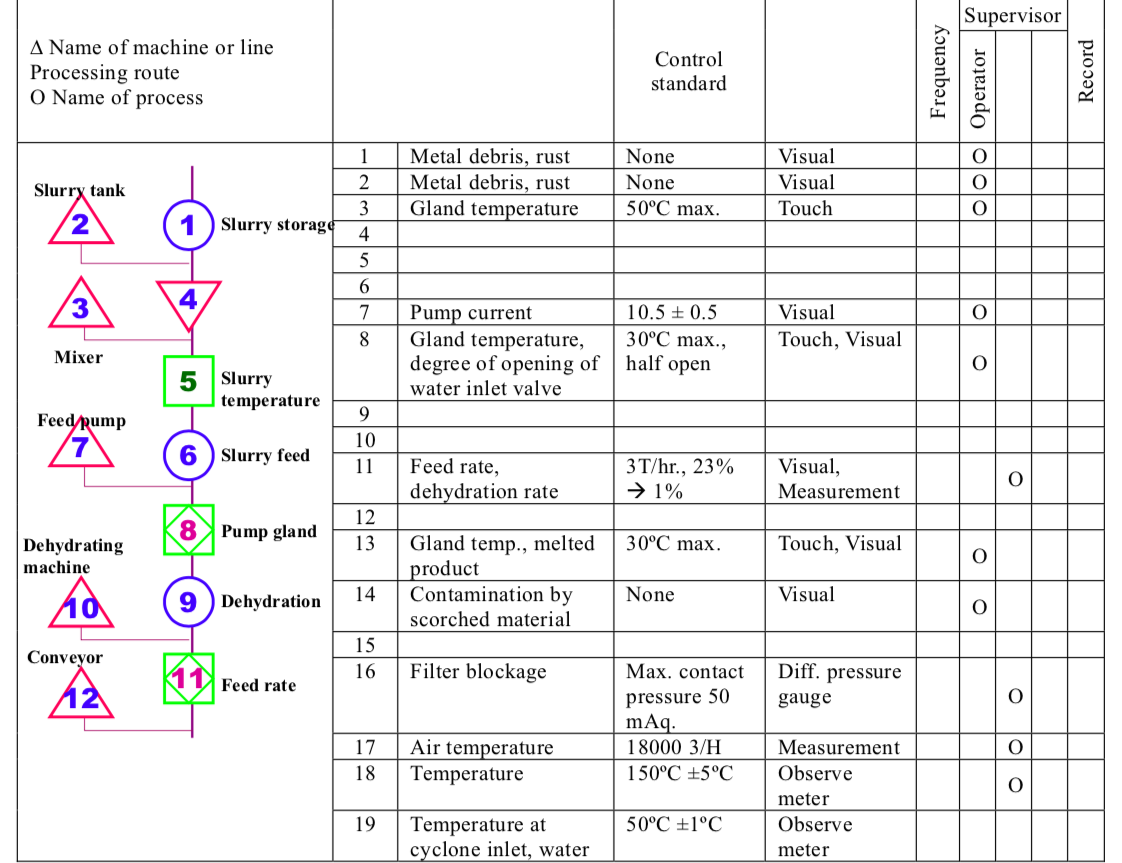