Drawing up a clear Focused Improvement plan before the official TPM kickoff will help your site enormously in attaining its TPM goals. Start by identifying all the current losses relating to equipment, resource consumption, and human labor for each department, area, production line, process, and machine, and work out what improvements need to be made by the time of your site’s assessment for the Award for TPM Excellence. When drawing up the plan, bear the following points in mind:
Where labor productivity is concerned, staffing levels are particularly important. When setting your baseline values, you will need to forecast future production volumes and headcounts, factoring in your existing restructuring plans. Then, based on these figures, you should work out the staffing levels required in your ideal factory, given the OEE improvements you intend to make.
In an equipment-intensive factory, implementing Focused Improvements aimed at maximizing OEE will naturally lower the 7 Big Equipment Losses, reducing the involvement of human operators in the production process and raising labor productivity. In a labor-intensive assembly operation, however, conscious efforts will need to be made to maximize labor productivity by carrying out Focused Improvements targeting the 5 Big Labour Losses.
In practice, it is difficult in the time leading up to the kickoff to identify every single topic that needs to be addressed. It is therefore a good idea to draw up tables for all production lines and process equipment, and begin by filling in the details of the topics you will be tackling first. You can then get going with the topics you have identified while continuing to fill in the remaining ones. In any case, you should contrive to have all your topics mapped out by six months after kickoff, at the latest. It is essential to formulate a sound implementation plan and follow it through systematically, and this is clearly the responsibility of the Focused Improvement Pillar Subcommittee in conjunction with the TPM Promotion Office.
When actually rolling out the Focused Improvement program, it works best if you divide it into two distinct stages: an introductory stage and a post-kickoff stage. These two stages will now be explained.
(1) The introductory stage
At the TPM Introduction stage, select site pilot model machines to work on, and form project teams consisting of the managers, supervisors, production engineers, and equipment maintenance staff assigned to the production lines where those machines are situated. Have these project teams implement the Focused Improvements needed to lower the 16 Big Losses and raise production efficiency, in accordance with the procedures shown in Figure “How to Implement Focused Improvement”, and make sure the teams produce visible results. It is important for people to learn and appreciate for themselves the best way of carrying out Focused Improvements, and the benefits they can deliver.
(2) The post-kickoff stage
After the TPM kickoff, each department, section, and the area should select their topics, based on a sound analysis of their losses, and form project teams including managers, supervisors, and technical staff, to address those topics by means of Focused Improvements (depending on the nature of the problem to be tackled, it may be appropriate to assign some topics to single individuals). The project is, of course, a team activity. To ensure that this activity is carried out methodically and efficiently, and enable you to attain the TPM goals set before the kickoff a Focused Improvement Plan like that is shown in Table “A Typical Focused Improvement Plan” should be drawn up.
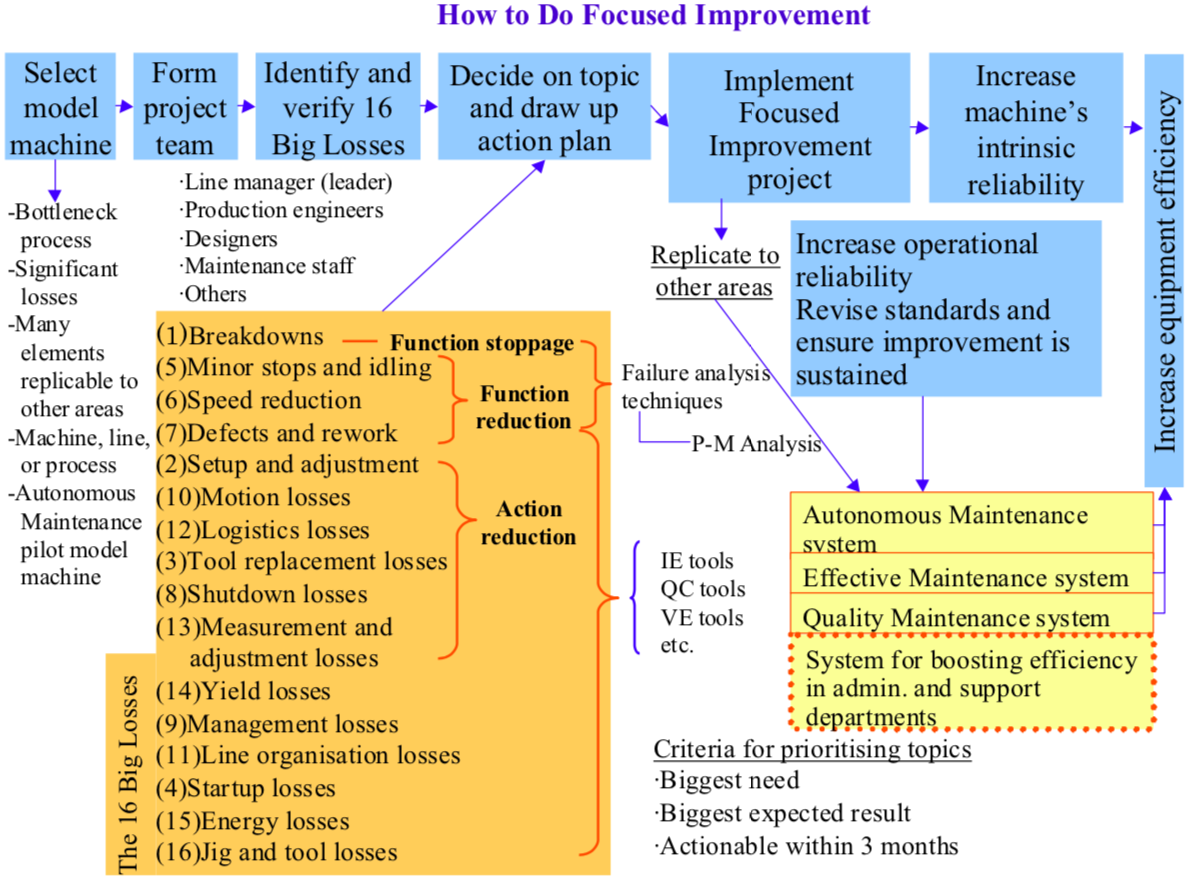
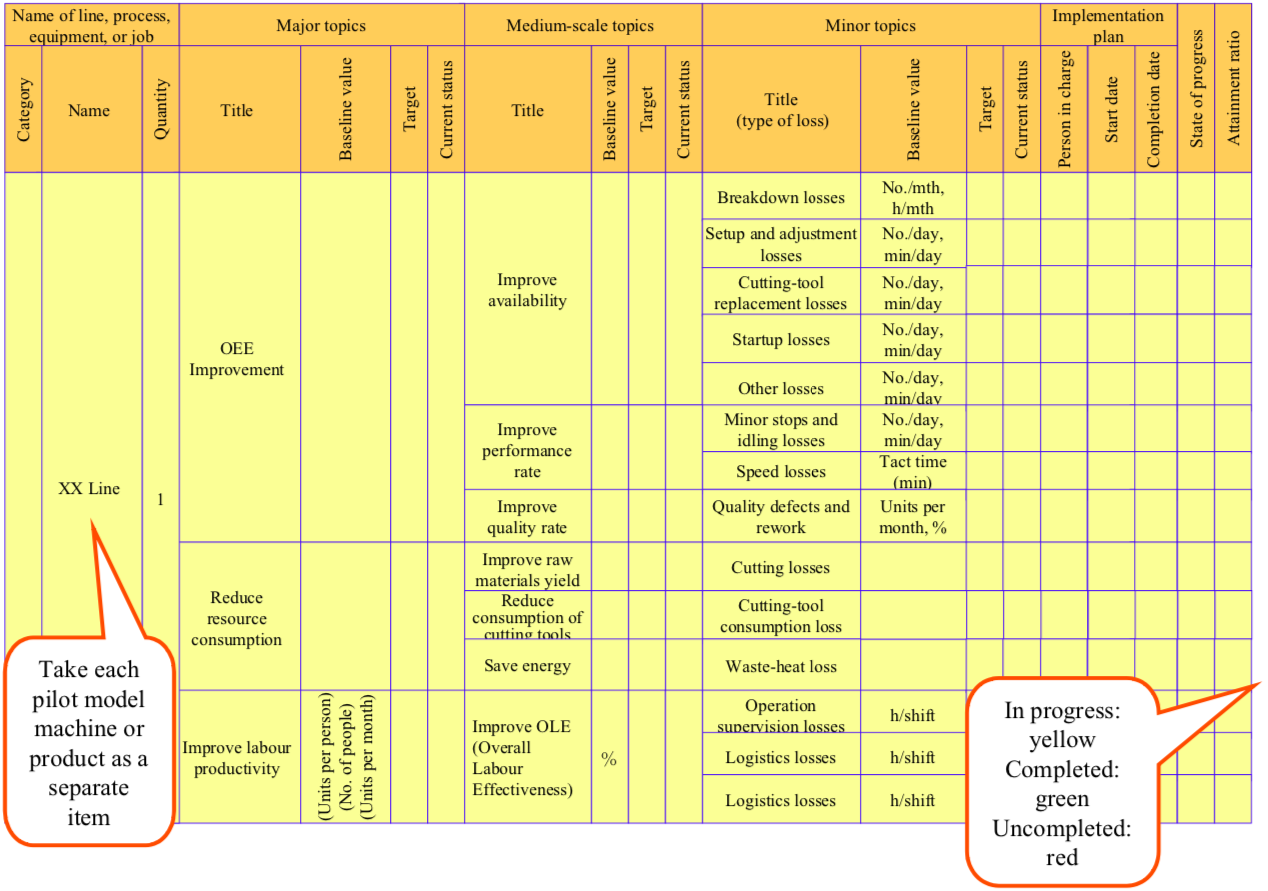