As Figure “A Typical Early Equipment Management System” in next chapter shows, in a typical Early Equipment Management system, the process from planning until commissioning is split into seven steps. A comprehensive design review (DR) should be performed at each step.
The first three steps, which constitute the planning stage, are especially important.
Step 1: Concept planning
Step 2: Action planning
Step 3: Design
To accomplish these steps, start by drawing up a Quality Assurance (QA) matrix. Next, carry out a 4-M analysis. Finally, perform a process FMEA. If you have the people with the relevant knowledge go through the design with a fine-tooth comb at various stages beforehand, fewer minor equipment defects will emerge during and after the witnessed test-run, and the commissioning period can be shortened.
The length of the startup period, from when the equipment is installed until it is in stable operation, is one of the elements that increase or reduce the LCC. Technology today is moving so fast that falling behind production schedules can have a major impact on business. This is why MP design explicitly addresses the challenge of reducing equipment efficiency shortfalls and commissioning control costs arising during startup. Commissioning control is regarded not as a separate entity, but as part of the equipment’s LCC.
The purpose of design reviews is to catch any problems that have slipped through the MP design net, so that they are not carried over to the commissioning stage. This ensures that once the equipment has been installed, an immediate, ‘vertical’ startup can be achieved. In other words, instead of leaving the identification of problems to the commissioning stage after installation and adjustment, thorough design reviews are carried out before installation.
As Figure “Design Review and Startup Period” in next chapter shows, the design reviews at each stage can be ranked in descending order of importance as follows: (1) design, (2) fabrication, (3) witnessed test-run, (4) installation. This underlines the crucial importance of the review carried out at the design stage.
Step 1 is the crucial stage at which the equipment plan is formulated and finalised, based on the company’s annual and mid-term business plans. In general, companies tend to put the cart before the horse, and give too much weight to the budget framework. Estimates are made without examining the proposals thoroughly enough, and it often proves necessary to correct the details, the amount budgeted, the time-frame and other parameters after the budget has been decided. To avoid this scenario, MP design aims to achieve higher planning precision by focusing on the following:
(1) Equipment engineers should get involved early in the product development or improvement process (from the conceptual design stage on) and already make a start on designing the equipment.
(2) To this end, the purpose and necessity of the investment should be made explicit, as should the economic requirements the equipment must satisfy (in terms of LCC and LCP), and more than one proposal should be considered.
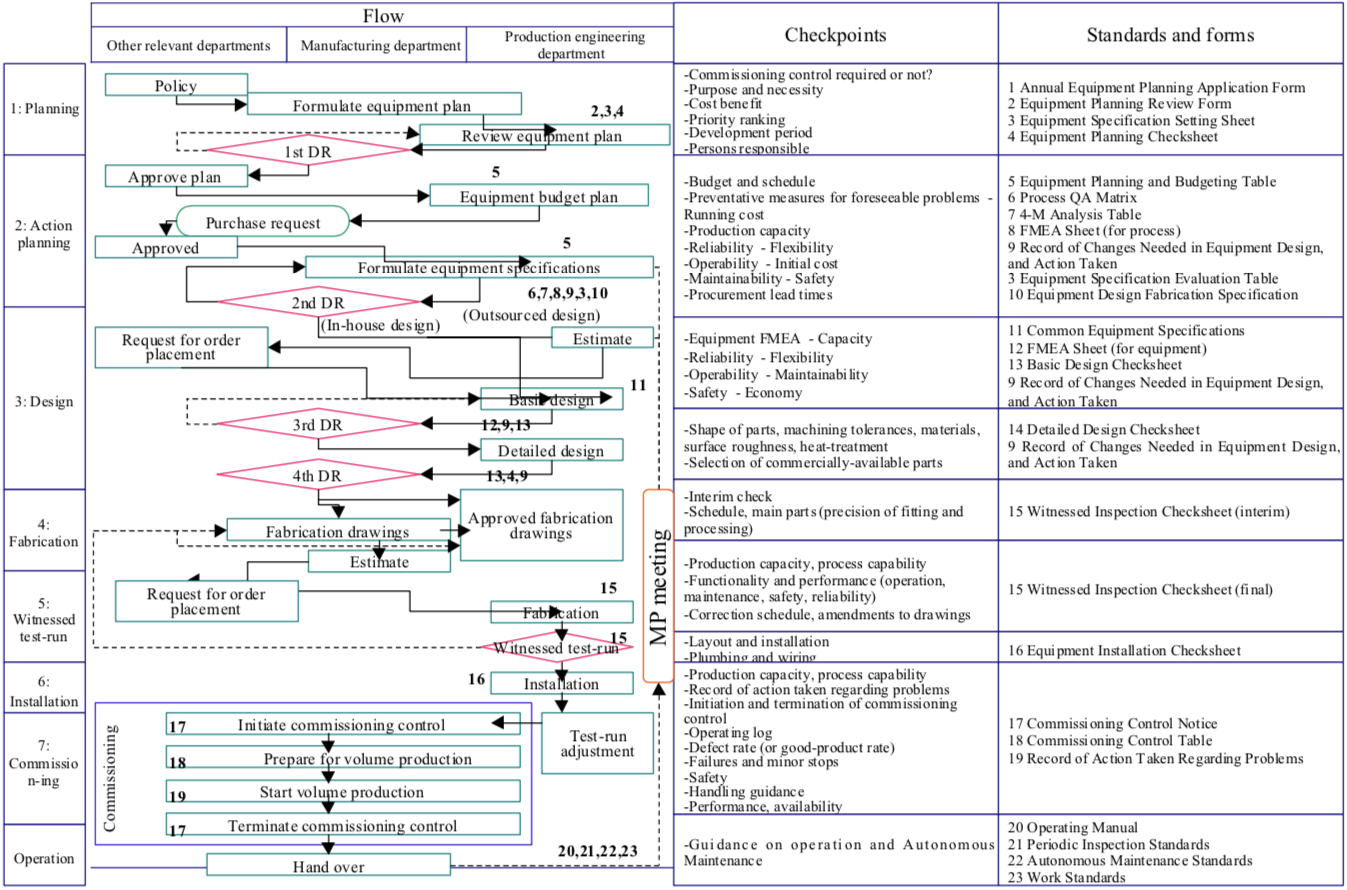
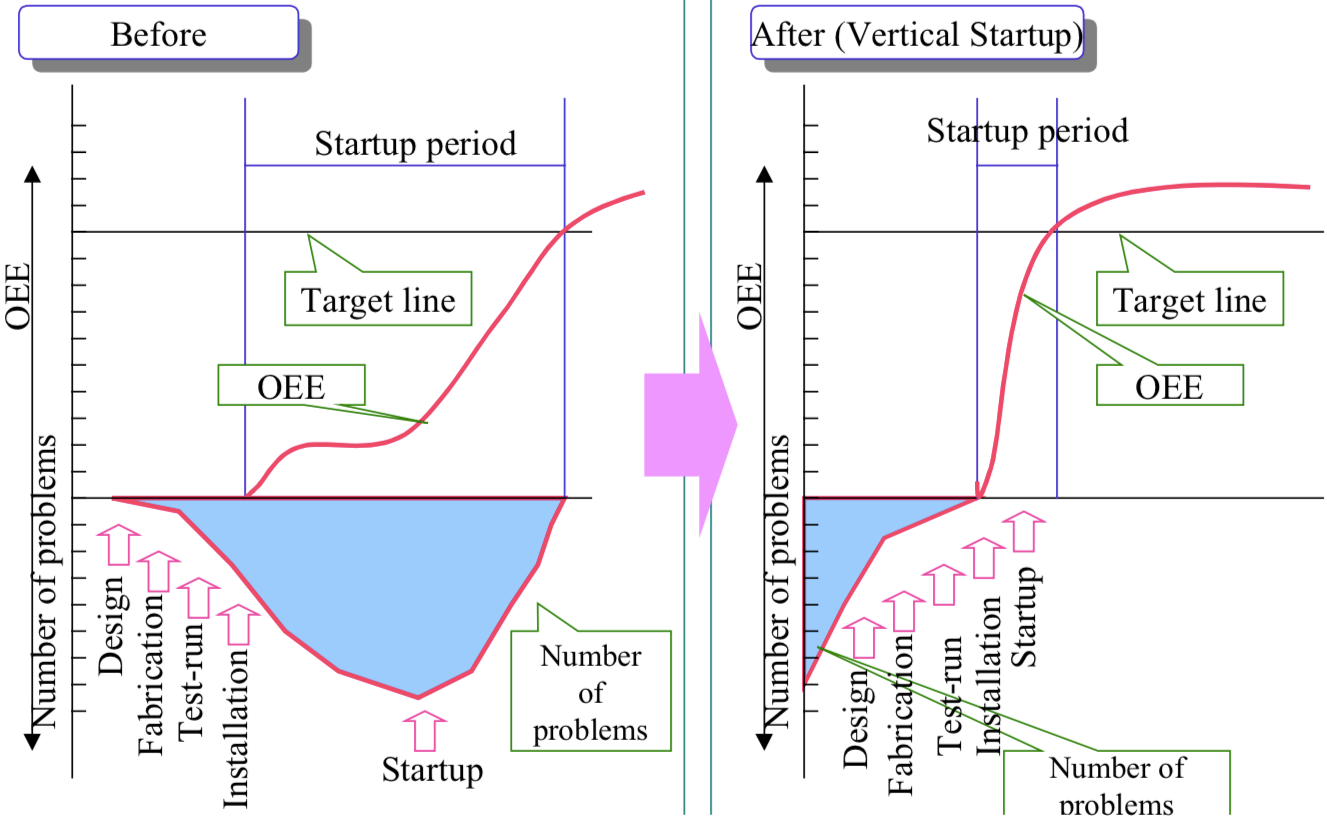
(3) Estimate the cost benefit of each proposal
(4) A design review should be carried out by knowledgeable staff from the relevant departments. This design review should include a thorough investigation of the appropriateness of each proposed investment, its future potential, the degree of technical difficulty it presents, its necessity, how economical it is, the order and schedule in which it should be carried out, and so forth. Only after all this information has been carefully clarified should the most appropriate proposal be selected. Prototypes fabricated on experimental equipment should then be assessed, and technical information from internal and external sources regarding this and similar equipment should be carefully studied in order to flesh out the proposal to be implemented. Figure “A Typical Investment Proposal Comparison Table” shows an example of a proposal comparison table prepared at this stage.
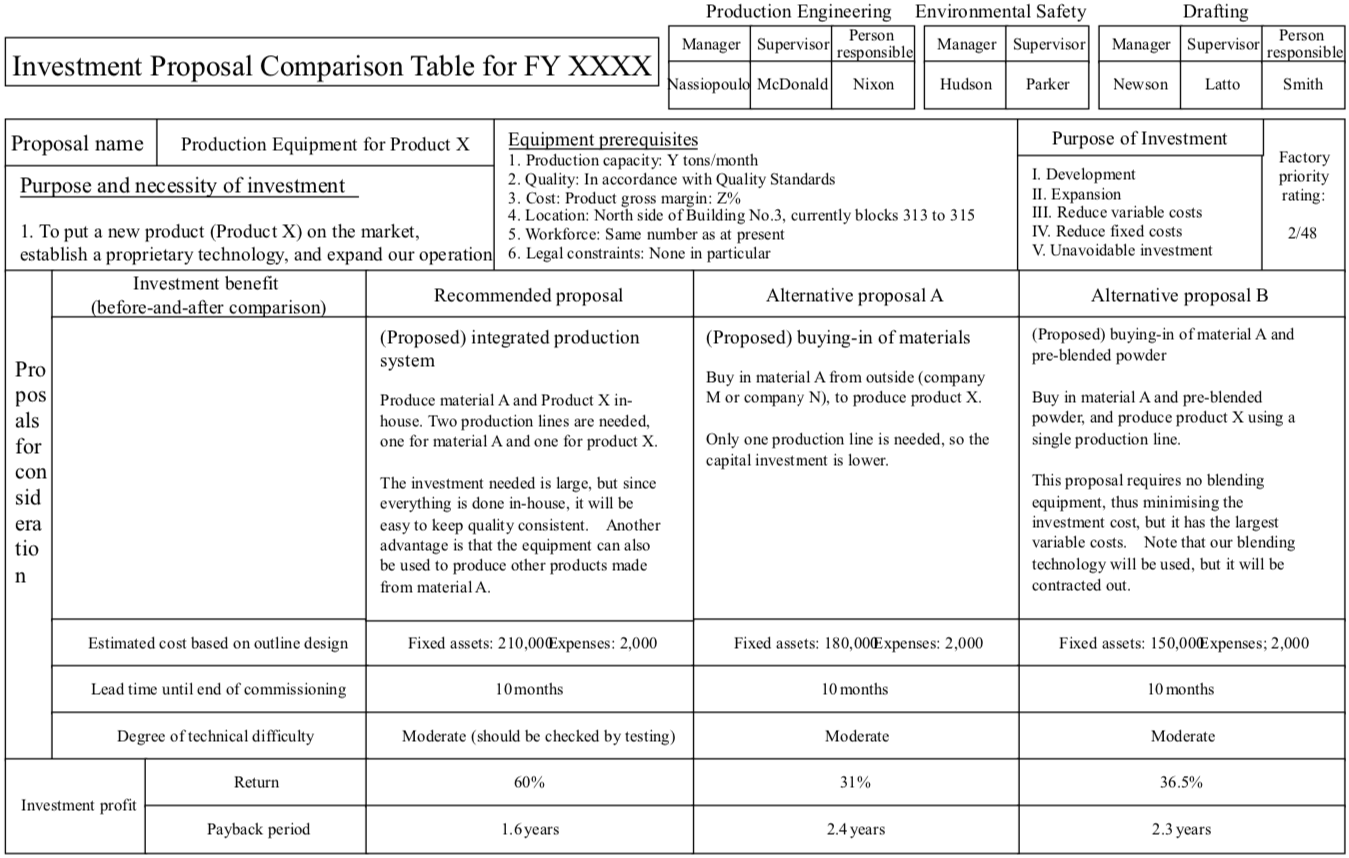