(1) Defining MP design
Maintenance Prevention (MP) design is the set of activities carried out to ensure that when new equipment is introduced, it will be highly functional, easy to use (adaptable and easily operable), resistant to failure, and maintenance-friendly and that its life-cycle profit (LCP) will be maximal, based on a forecast of the future of the products it is to produce. The weaknesses of existing equipment are studied, and the resultant knowledge is fed forward into the design of new equipment with the aim of making it more reliable and maintainable, and ultimately maintenance-free.
(2) The aims of MP design
MP design aims to break free of the constraints of equipment-centered design and focus instead on optimizing the operator-machine relationship. It seeks to do this by creating maintenance-free equipment whose high quality, high productivity, and safety are assured, and whose LCP is maximized, enabling the equipment to accommodate future needs.
In the MP design carried out during Steps 2 and 3 of the overall design process, activities aimed at building-in quality are of the utmost importance.
(3) The basic equipment prerequisites
When carrying out MP design, the basic attributes required of the equipment (such as reliability, maintainability, autonomous maintainability, operability, resource economy, safety, and flexibility) must be defined in concrete terms. However, these terms tend to be used rather loosely; reliability, for example, can mean different things to different people. Table “Equipment Prerequisites and Their Definitions” gives their definitions.
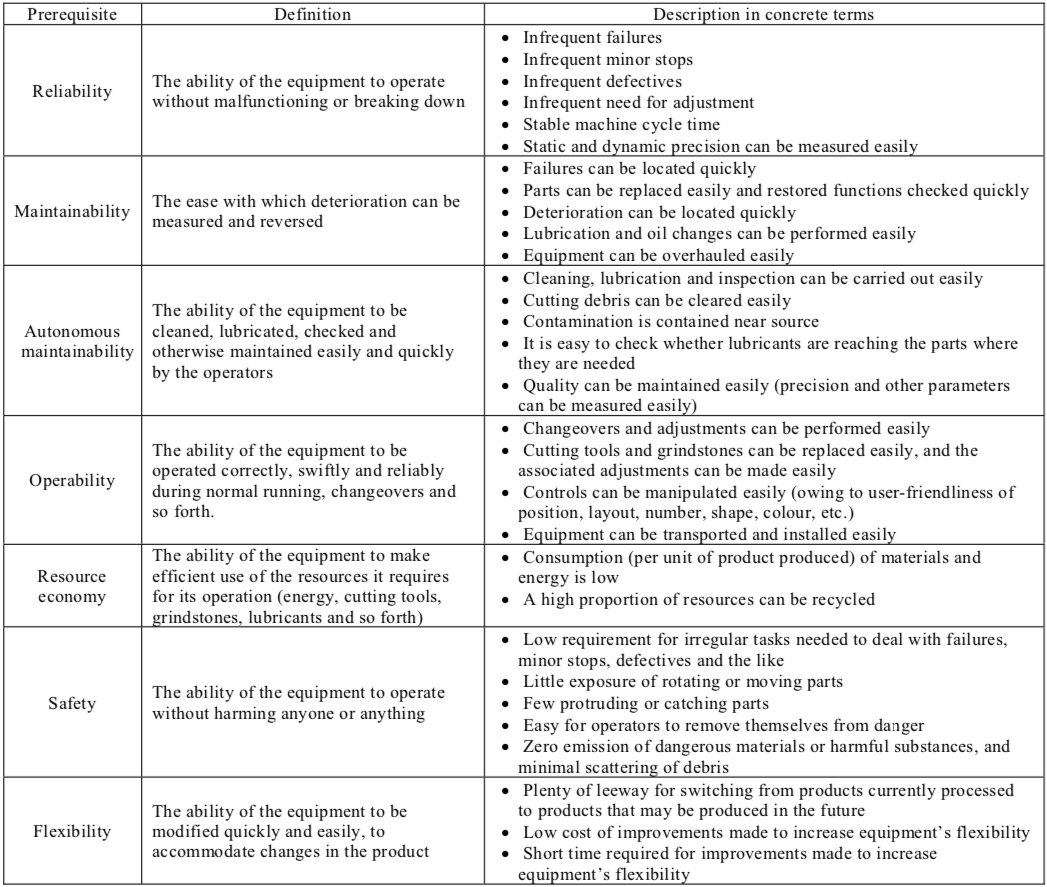
(4) Collecting and using information
MP design requires a system enabling information about daily operating and maintenance activities to be collected and compiled in a standard format, as shown in Figure ” Flow Diagram for Collecting and Using MP Information”. Many design standards are a good example of how information tends to mount up to such proportions that it becomes hard to understand, difficult to search, and easily outdated, and consequently not exploited effectively. Once design standards have been formulated, that is not the end of the matter: it is essential to keep revising them in the light of new information and keep trying to make them more user-friendly, even as you make use of them in the current design project. It is also vital that items common to all equipment should be standardized on a common specifications sheet, and incorporated rigorously into the standards used for designing and purchasing new equipment. It goes without saying that checksheets should also be drawn up, and checks should be carried out at every stage. Tables “Equipment Safety” to “Specification Checklist (Mechanical Design)” show examples of the principal checksheets.
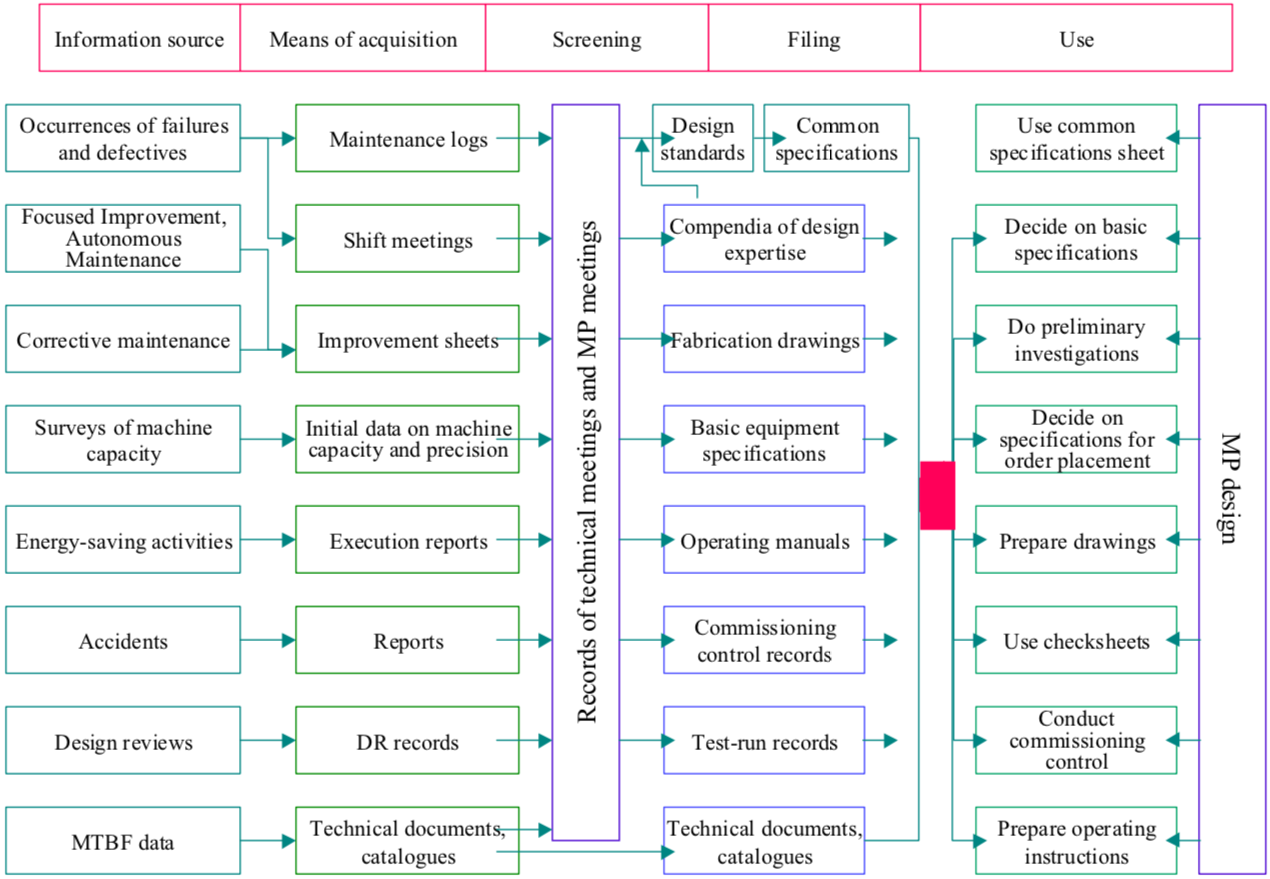
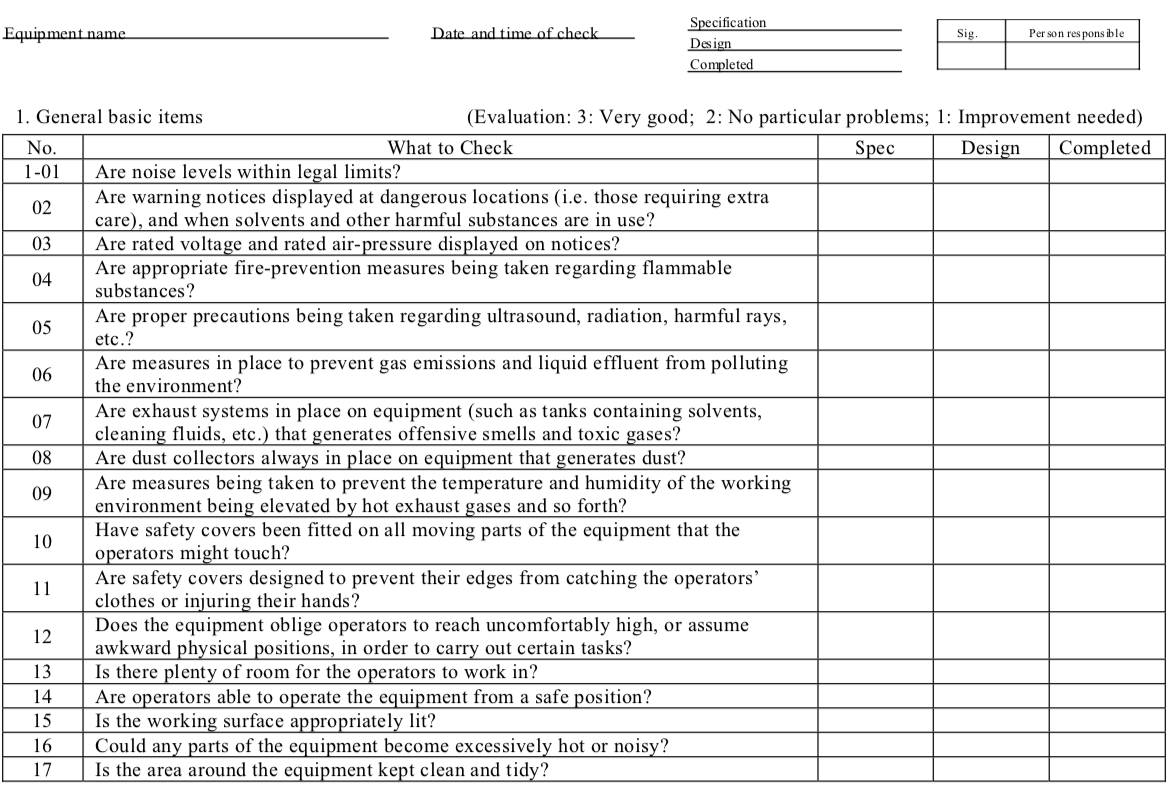
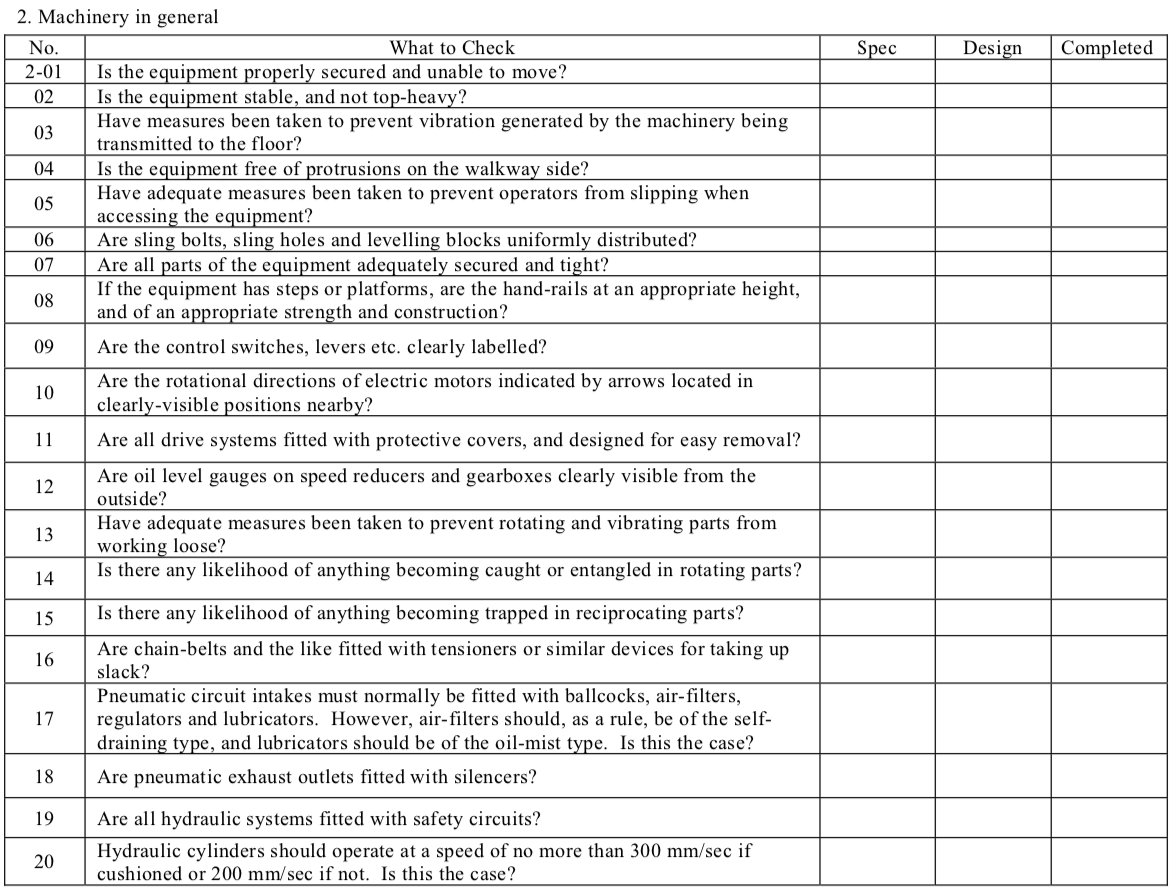
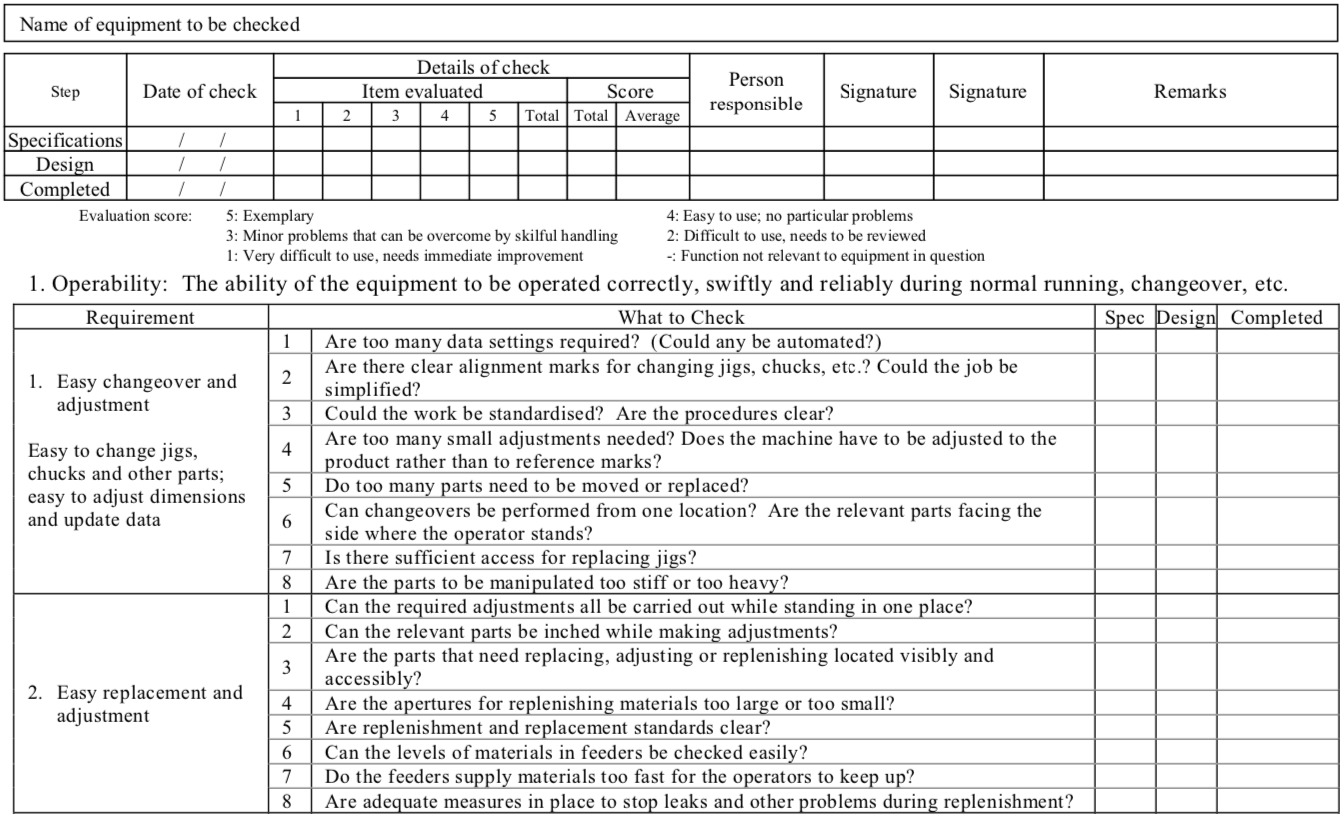
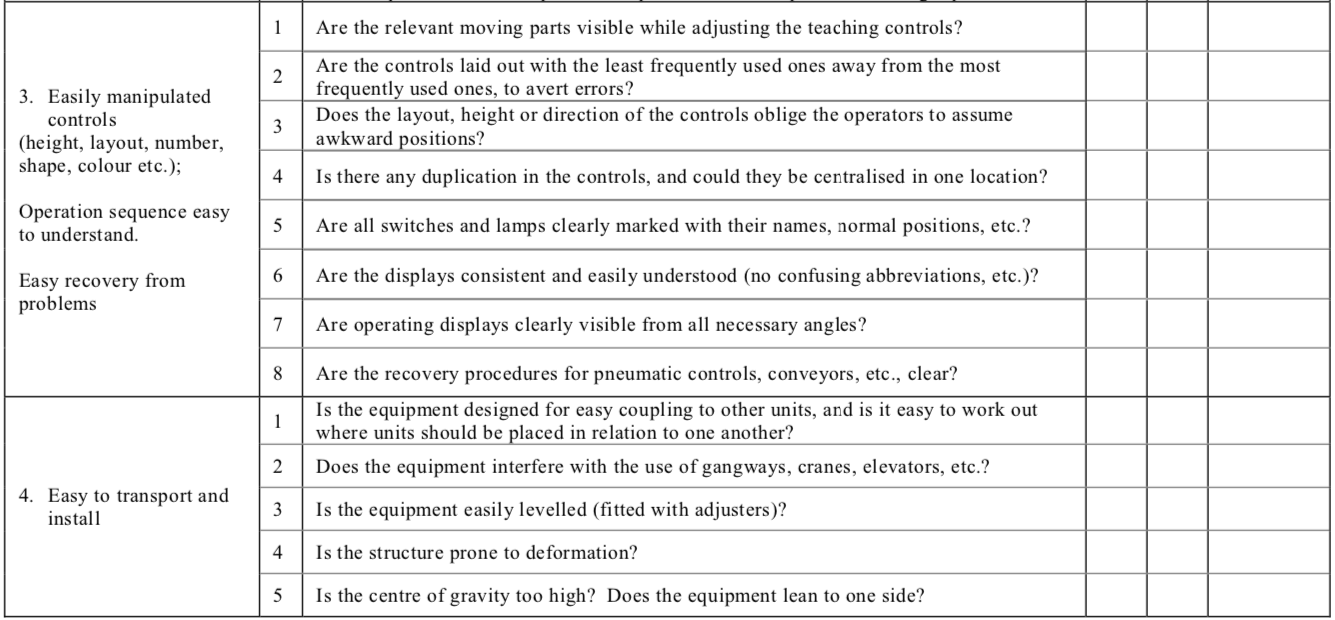

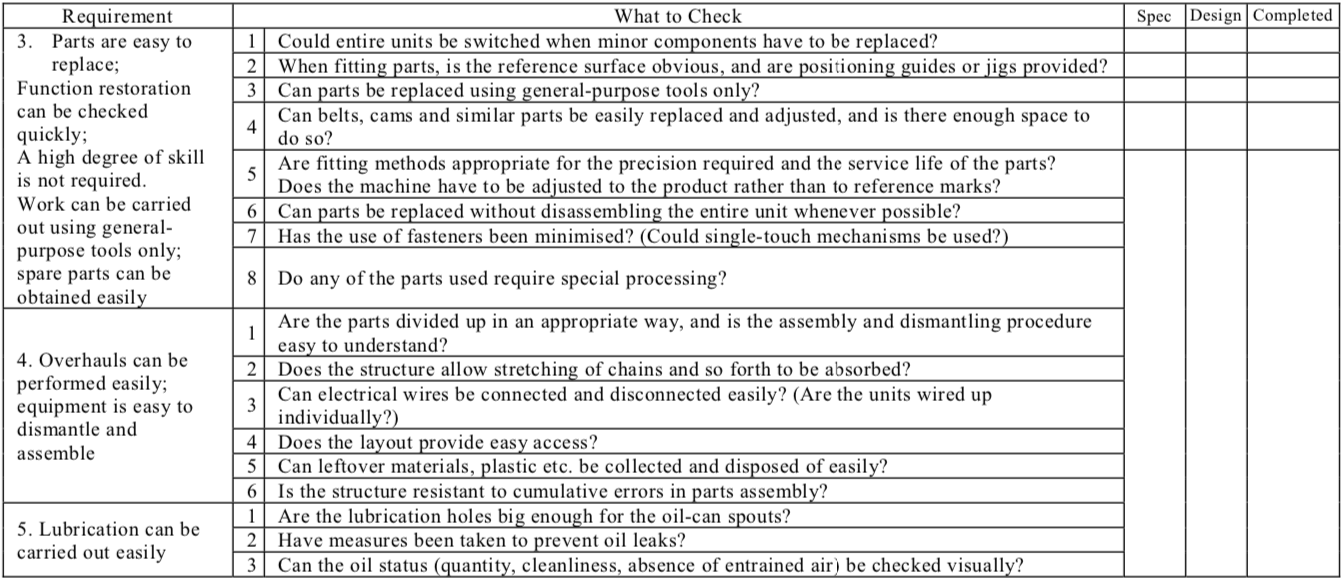
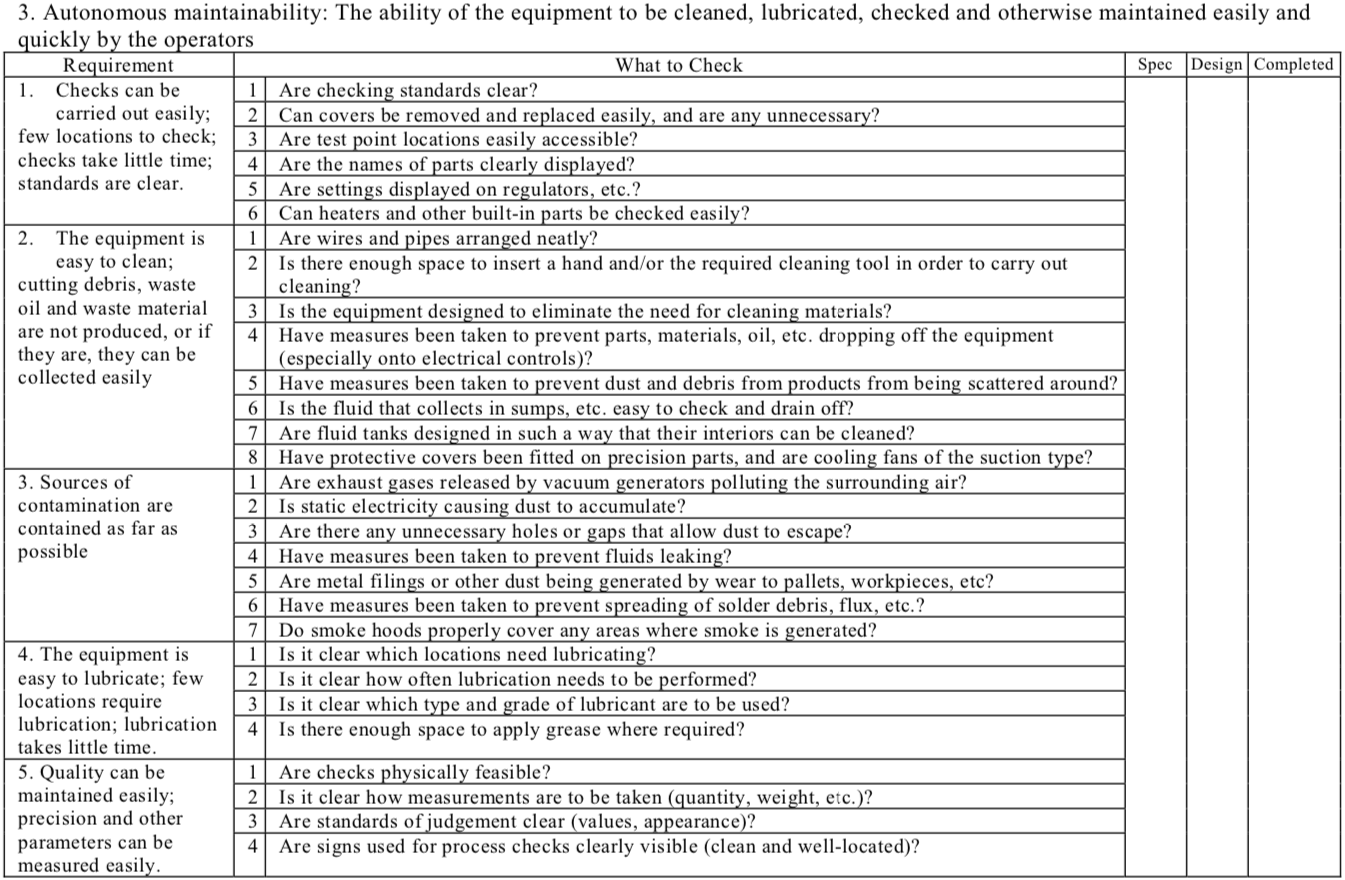
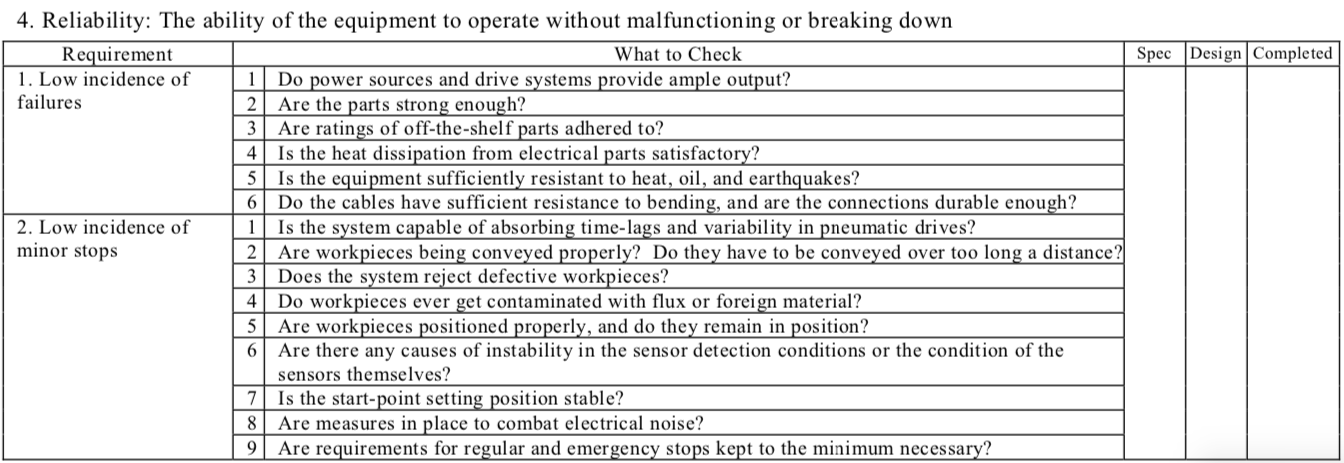
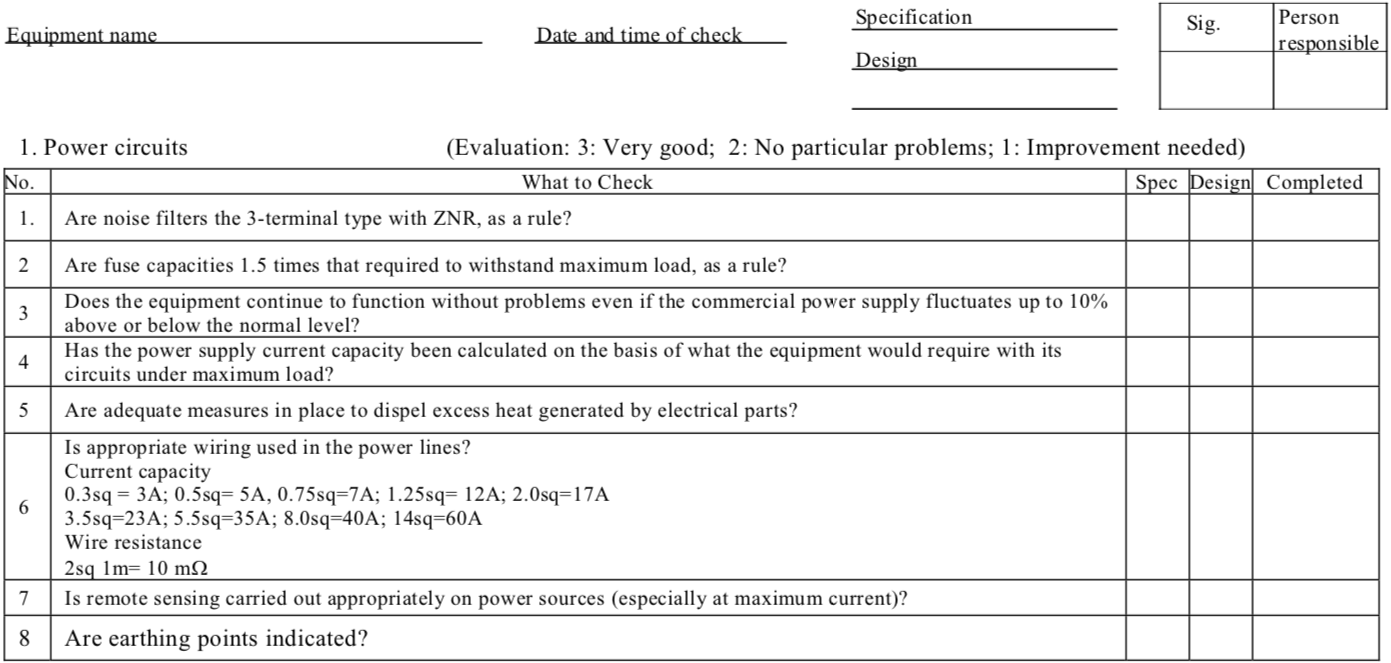
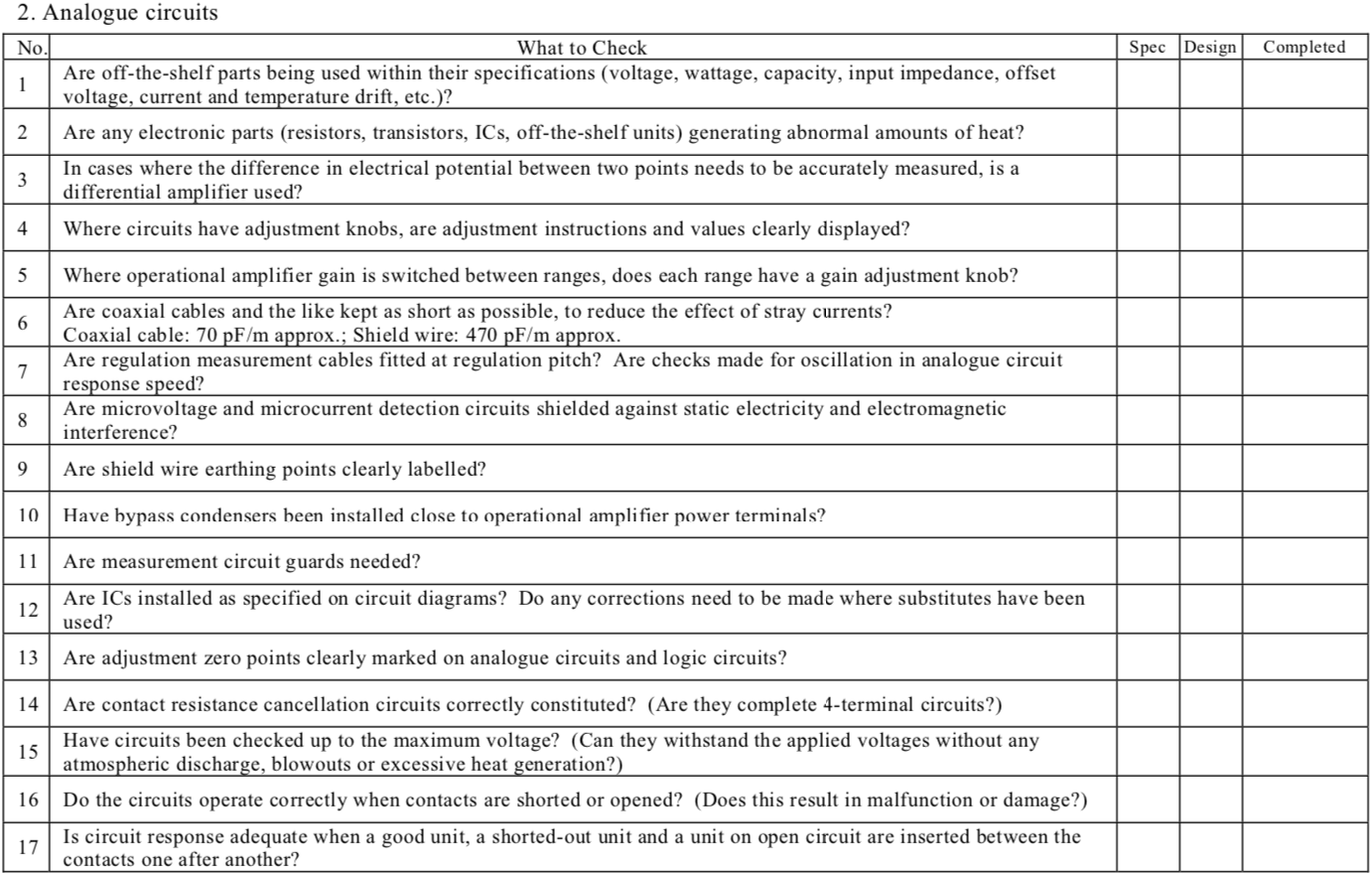
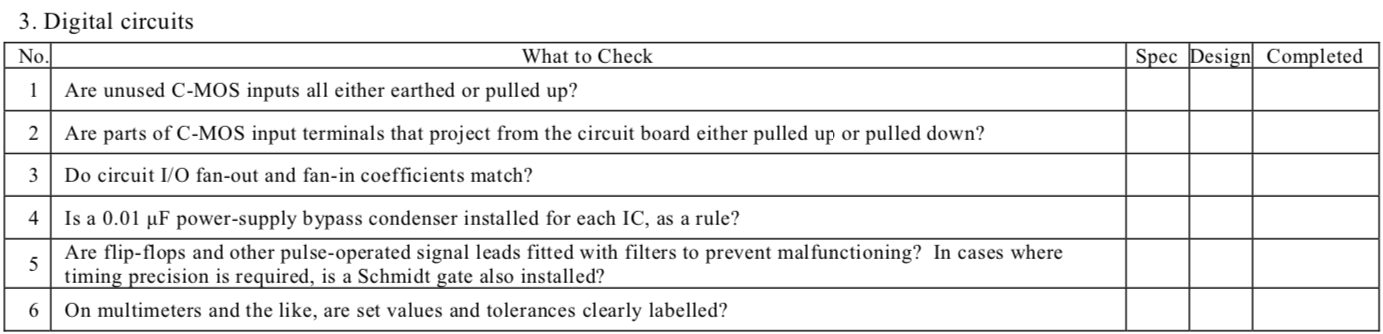
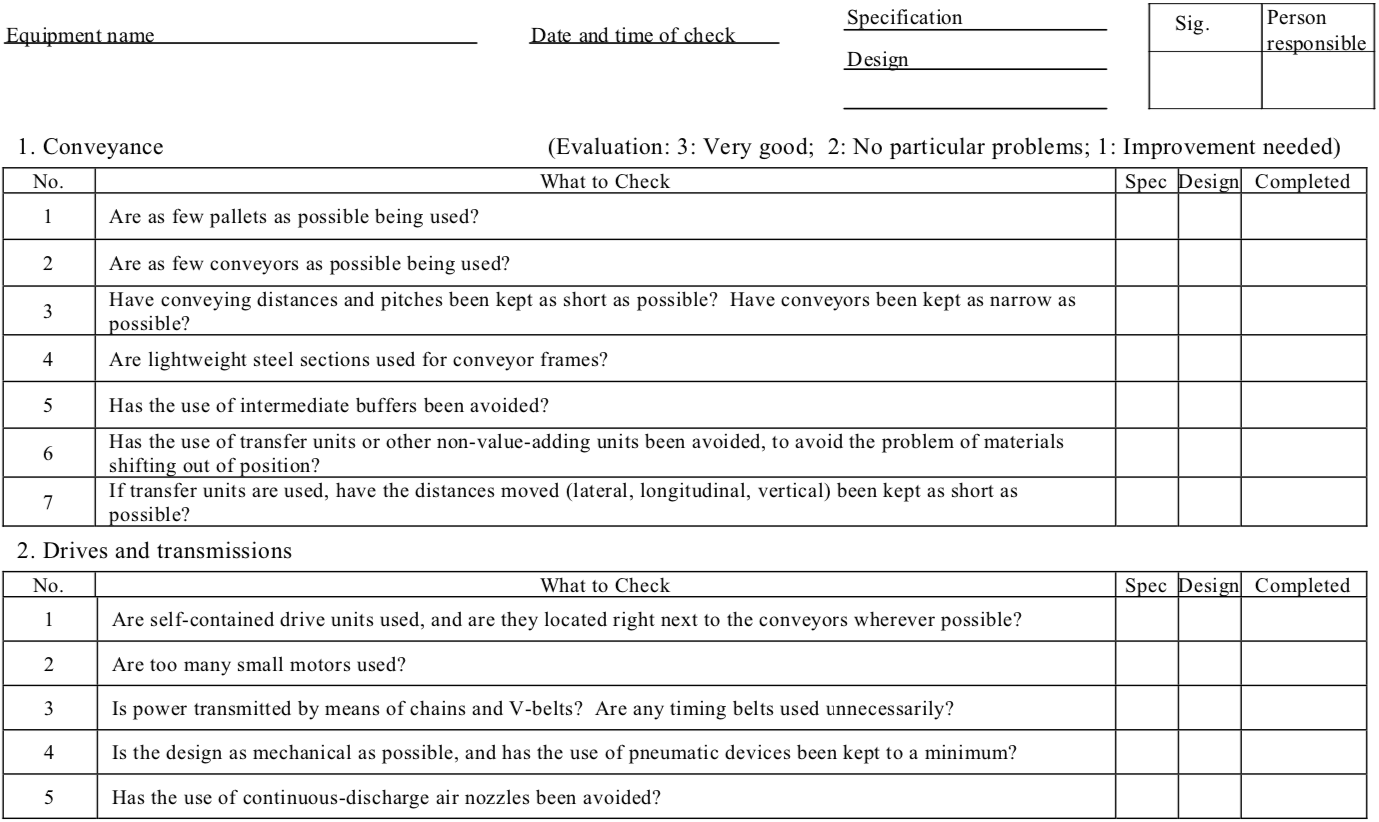
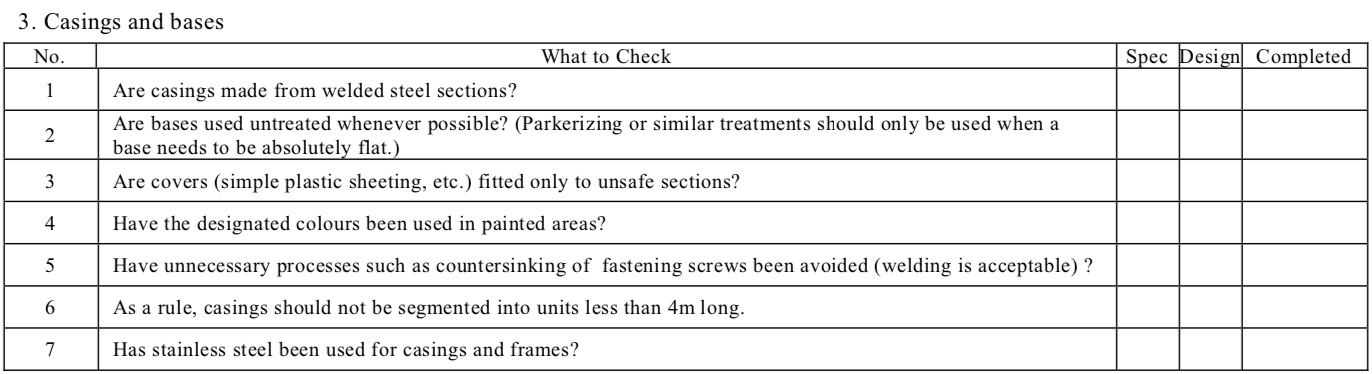
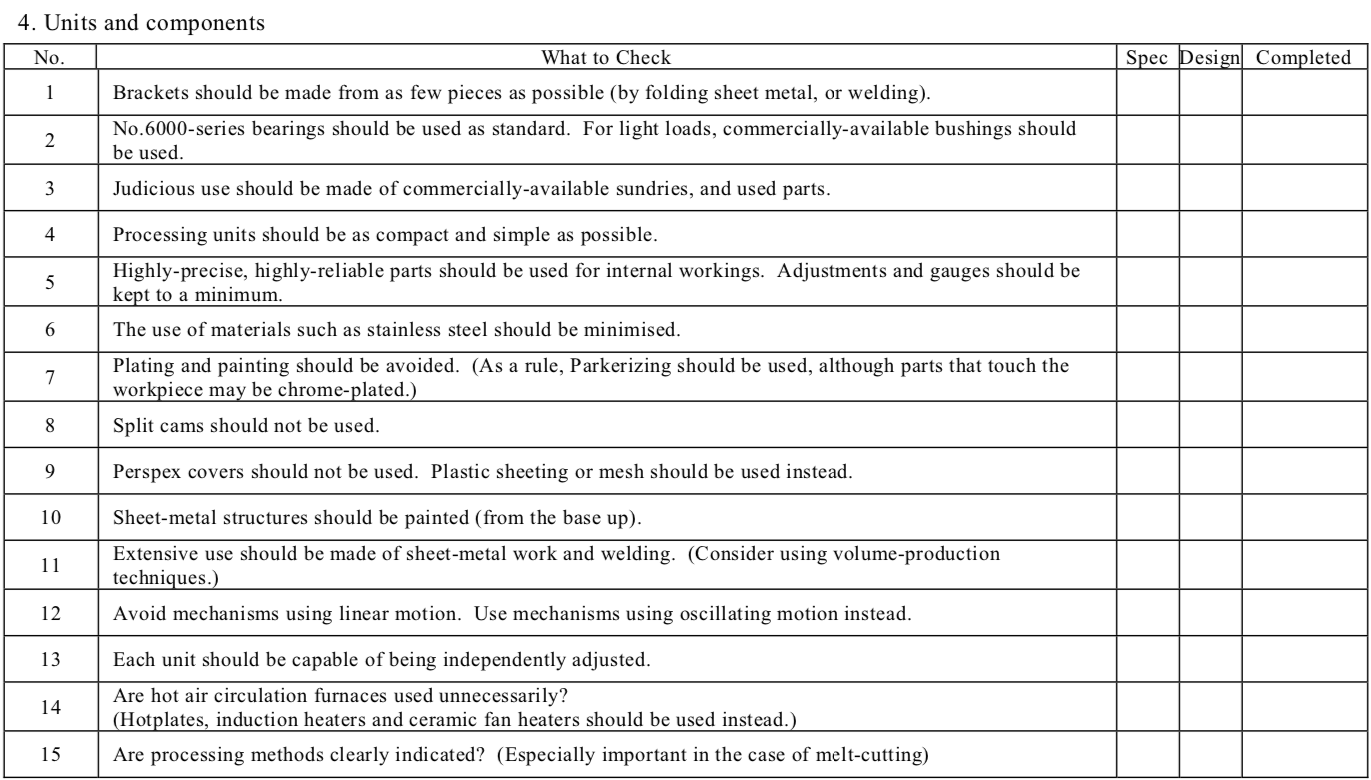