- Step 4: Fabrication In this step, the equipment is fabricated in accordance with the detailed design. The principal dimensions and progress against schedule should be checked at intermediate stages in order to raise the reliability of the fabrication process.
- Step 5: Manufacturer’s test-run In this step, the manufacturer tests the equipment under load. Problems identified up to and including Step 4 are solved, and fresh issues are identified and measures taken to eliminate them before the equipment is delivered. In short, every effort is made to ensure that no trouble will arise once the equipment has been set up at its final destination. Particular attention should be given to making sure (using checksheets) that the MP information on the Common Specifications Sheet has all been incorporated into the equipment. It is very helpful to have operators and maintenance technicians participate in the process at this stage.
- Step 6: Installation The managers, supervisors and other key personnel in the department that will be using the equipment should now be consulted regarding the installation schedule, and any necessary adjustments should be made. The reliability of installation should also be raised by checking the equipment carefully against the design diagrams as it is being installed. The test-run is then carried out in cooperation with the key personnel. Careful checks are made to ensure that the design requirements have actually been met, and remaining problems are identified and corrected. Products are produced on a test basis, and checked to see whether they come up to quality targets. The equipment is also evaluated to see whether its parameters meet their target values. Manufacturing conditions and work standardization will need to be given careful consideration ahead of time.
- Step 7: Commissioning At this step, the production department takes over and monitors the process capability while manufacturing the product. If equipment problems have already been comprehensively addressed and corrected, they are not carried over to this stage, so vertical startup can be achieved and the equipment can attain 100% of the target values on the basic specifications sheet within a relatively short commissioning period.
- Recording problems detected in the period from intermediate inspection to test-run, and during commissioning Details of all the equipment problems discovered should be recorded, their causes identified, countermeasures devised and implemented, and the results assessed. Figure “A Typical Test-Run Record” shows a typical record of this process. Such problems arise because of failure to build one hundred percent quality into the equipment at a previous stage of the Early Management process, so it is important to work out how to stop the same problems from happening again, and find ways of improving the Early Management system.
Figure “Flow Diagram for Commissioning Control” is a typical commissioning control flowchart. Its first striking feature is that several departments work together to carry out the commissioning, with clearly- demarcated roles allocated to the department that will be using the equipment, and to the maintenance and planning (or design) departments. Commissioning control is the point at which design, operation, and maintenance meet, so a system of this sort is obviously essential if the process is to run smoothly. The second striking feature of this example is that the initiation and termination of commissioning control are clearly defined. The parameters for deciding whether to terminate or continue commissioning control (such as production capacity, stoppage frequency, stoppage severity, and defect rate) are specified when commissioning control is initiated.
Finally, Figure “A Typical Commissioning Control Initiation and Termination Notice Forms 1 and 2” shows a typical Commissioning Control Notification Sheet.
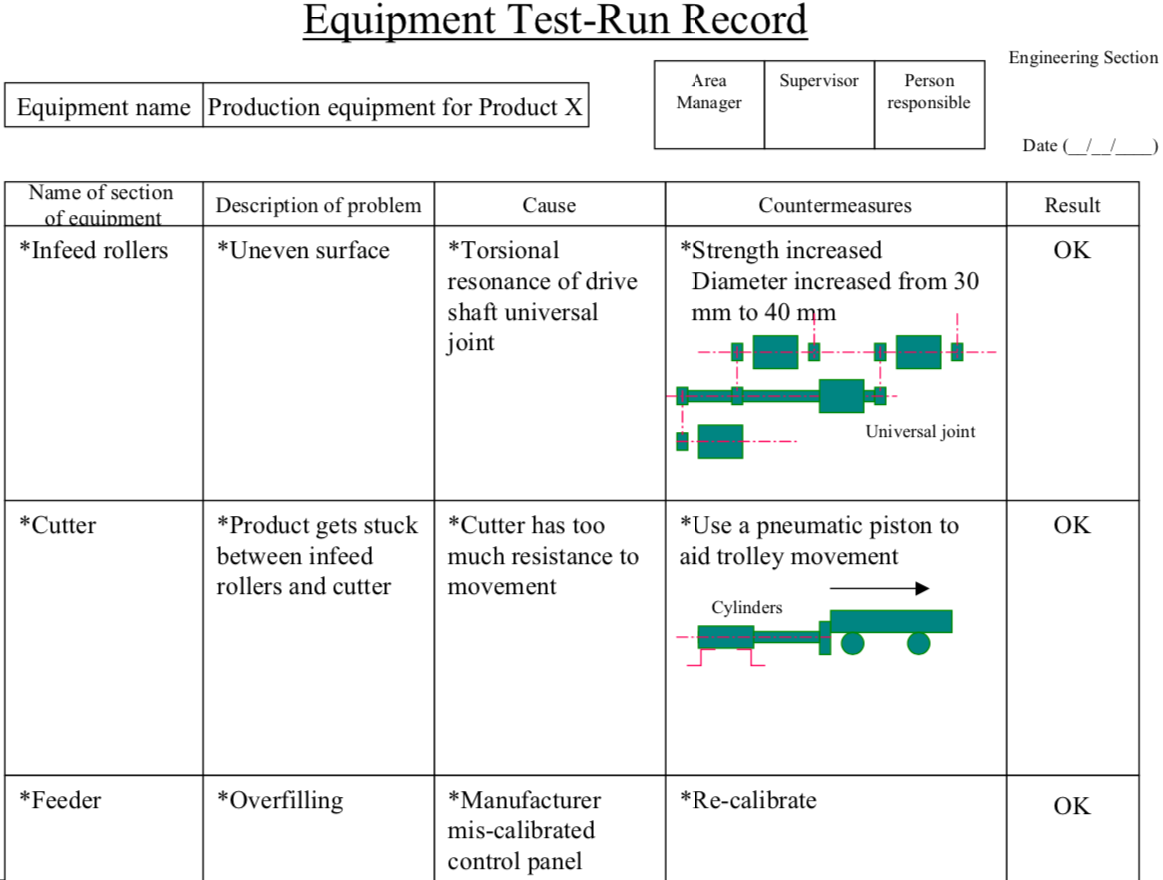
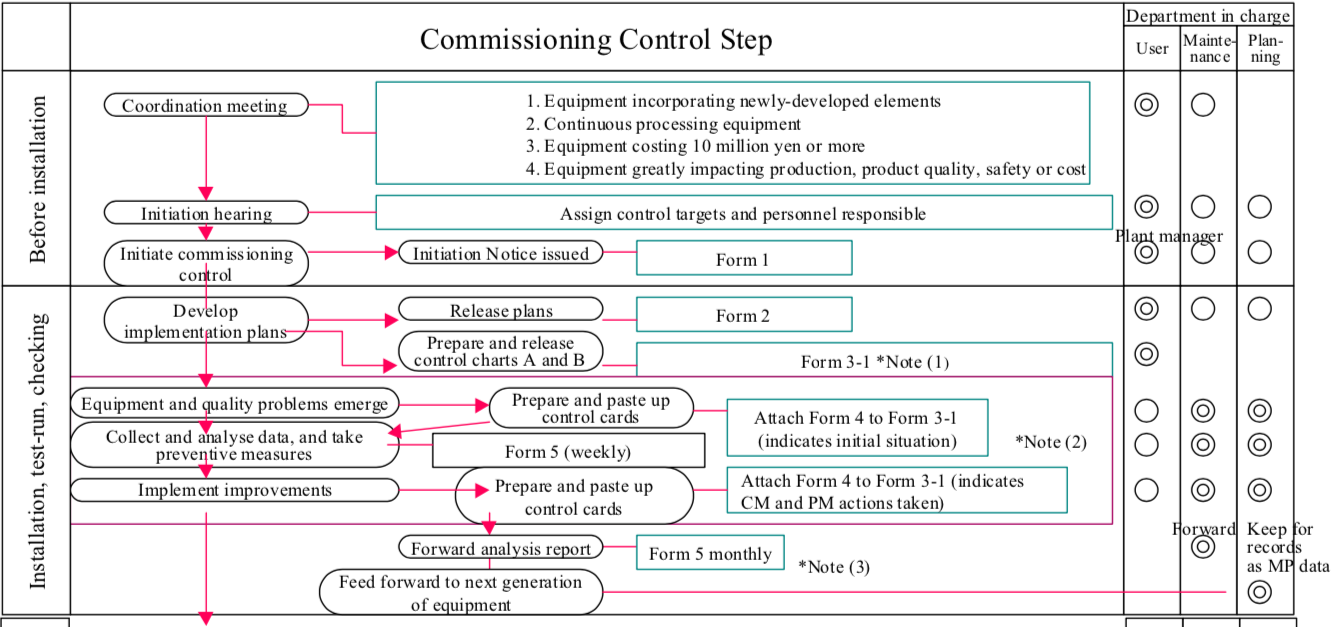
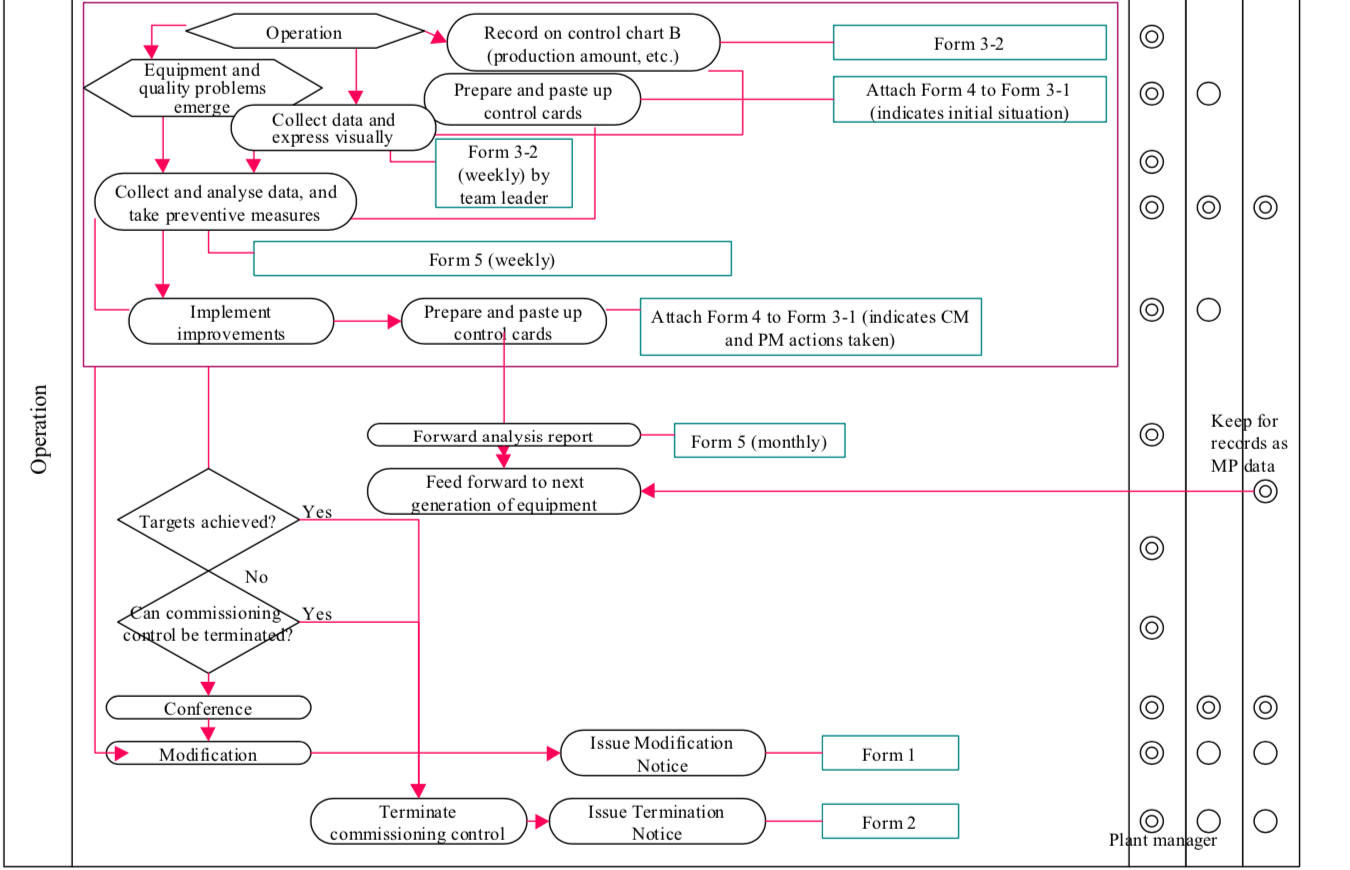