7 steps of PM
- Step 1. Elimination of forced deterioration and prevention of accelerated deterioration
- Step 2. Reverse deterioration (Breakdown Analysis)
- Step 3. Establishment of maintenance standards
- Step 4. Countermeasures against weak points of the machine and lengthened equipment life
- Step 5. Build a periodic maintenance system
- Step 6. Build a predictive maintenance system (trend management)
- Step 7. Maintenance cost management. Establishment of a planned maintenance system
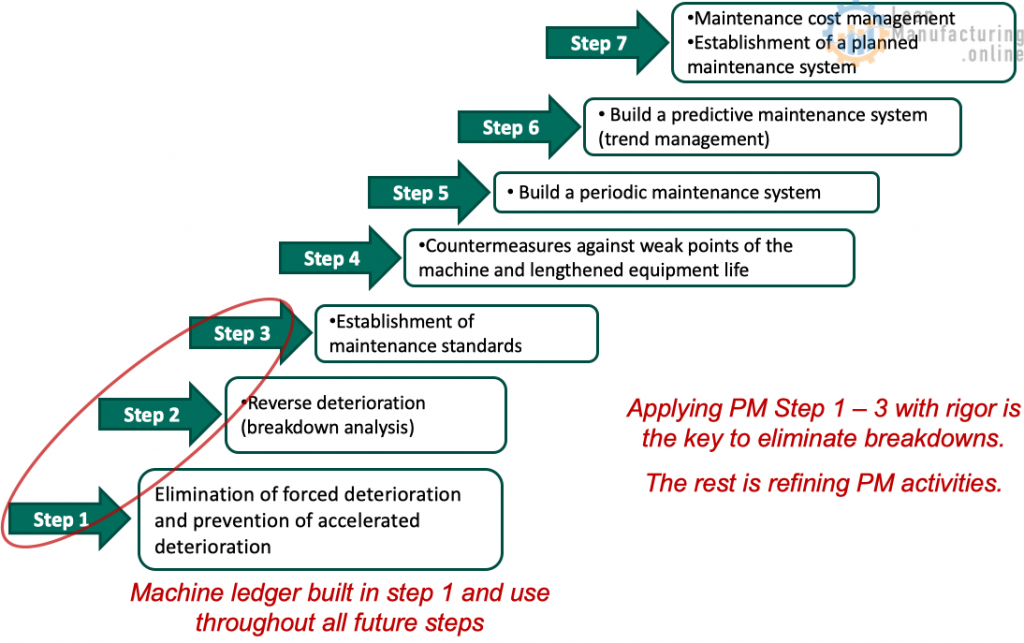
Machine Ledger
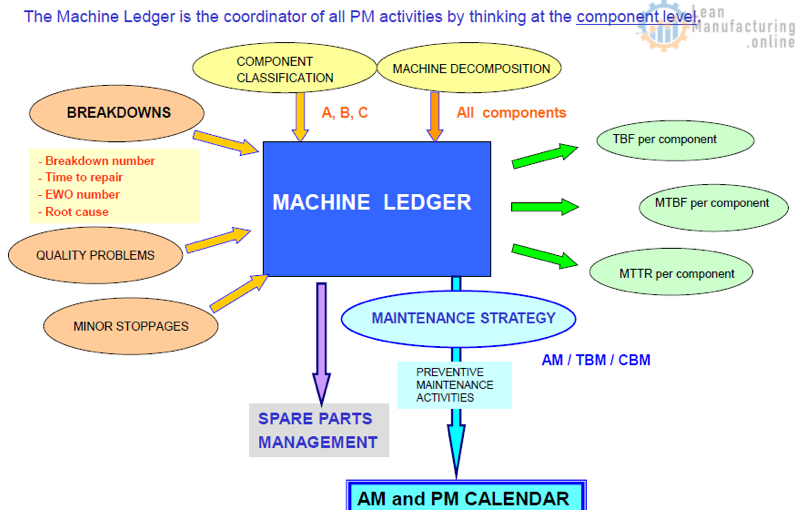
Who needs to have a Machine Ledger?
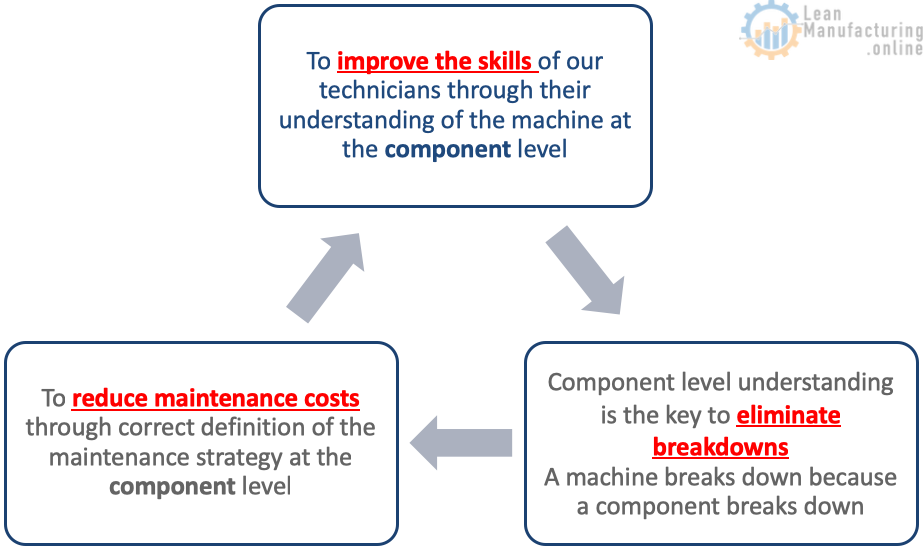
Machine Ledger and PM Calendar
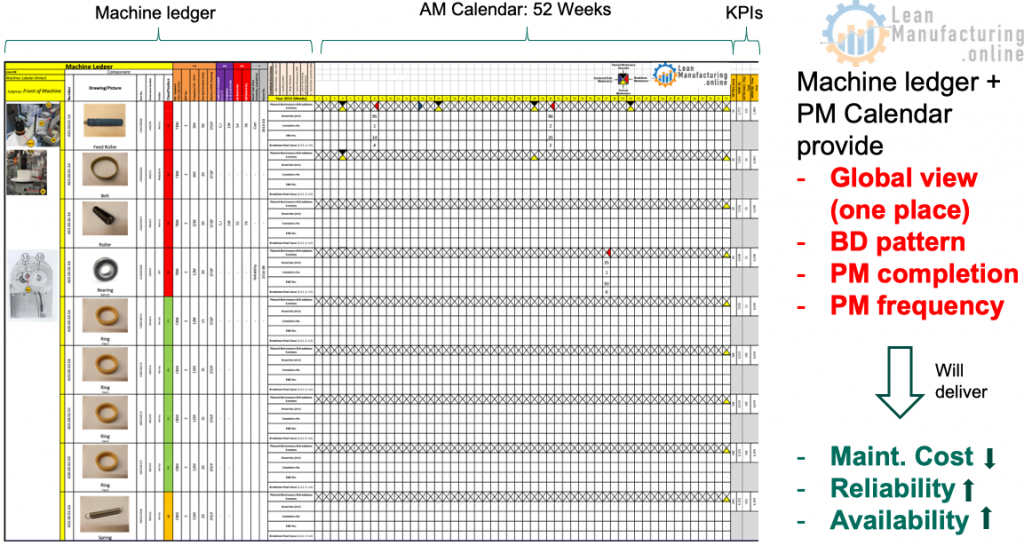
Spreadsheet can be purchased from our store
Machine Ledger Development (Plan-Do-Check-Act approach)
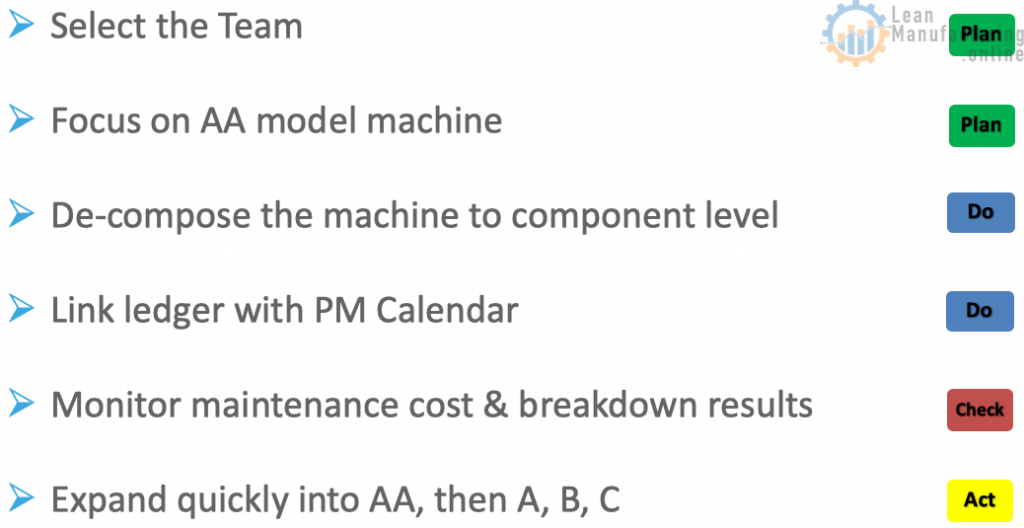
(PLAN) Select the team
- Select the Technicians with higher technical skills (i.e. Technical Trainer, Maintenance Lead Hand)
- Pair him/her with entry/developing level Technicians.
- It is a resource-intensive activity. Plan it well with clear deliverables x maintenance cost & OEE improvement
- One machine of 2000 components
- 1st machine ledger: 2 Technicians 100% for 10-12 weeks
- Allow the team time to study the machine ledger theory and equipment manuals
(PLAN) Focus on the pilot machine
Select your No. 1 PM – AA model machine based on Cost Diagram
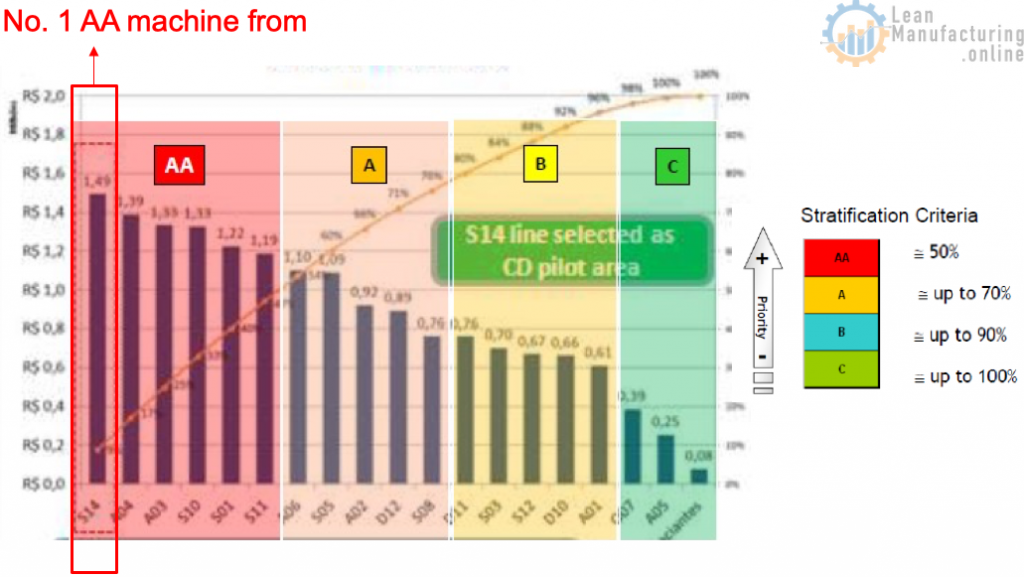
(DO) De-compose machine into components
- Divide the machine into subgroups
- De-compose the subgroups into each component
- Classify each component into ABC
- Gather component’s spare parts information
- Define maintenance strategy
- Link components to other pillars (first AM & Q, then others)
Divide the machine into subgroups
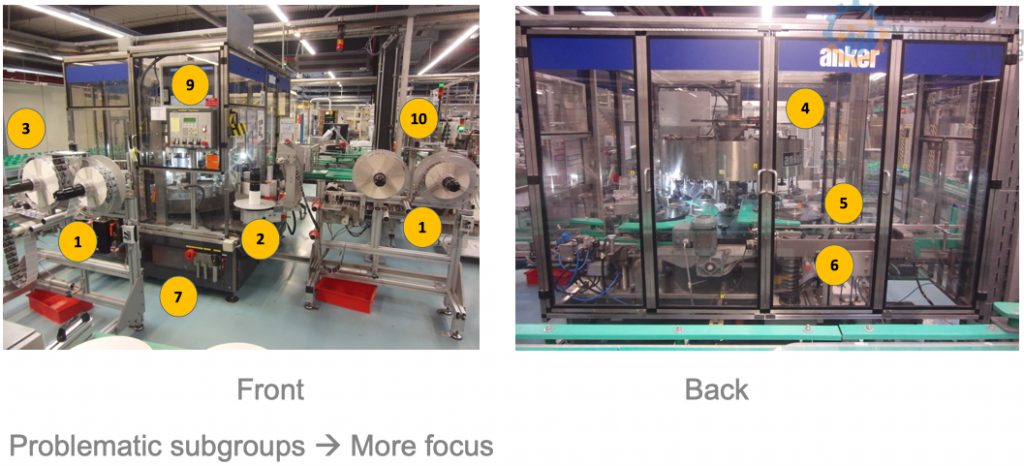
De-compose every subgroup into each component
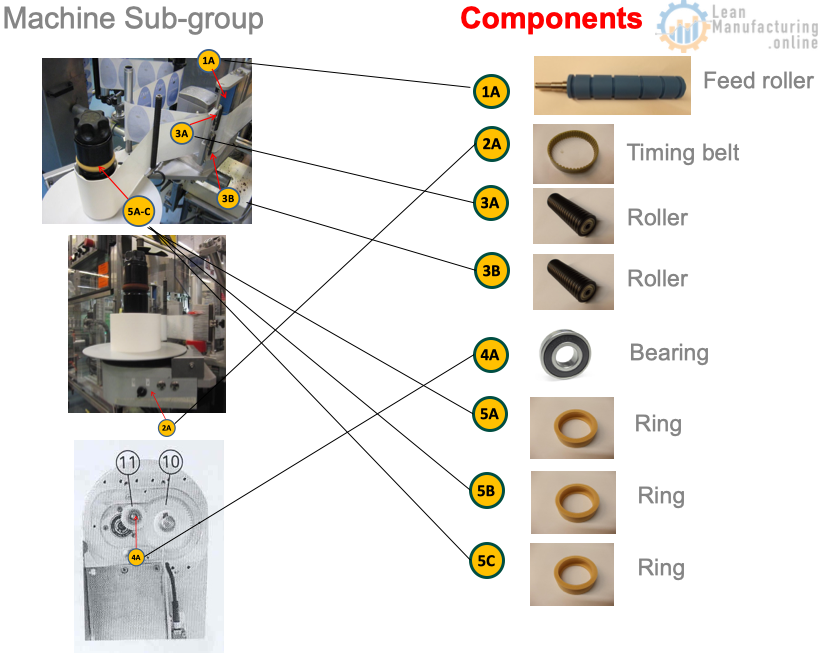
Classify components into A, B, C
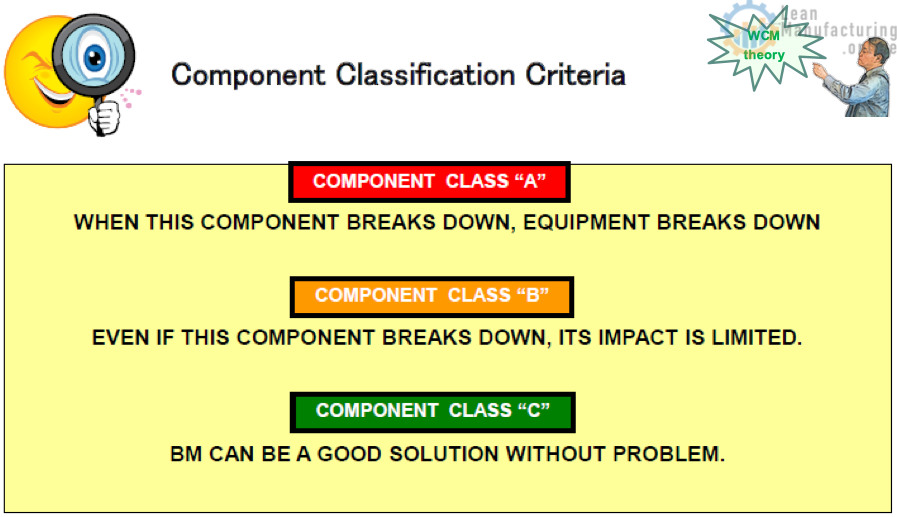
Gather component’s spare parts information

Define PM Strategy

Find the link with other pillars
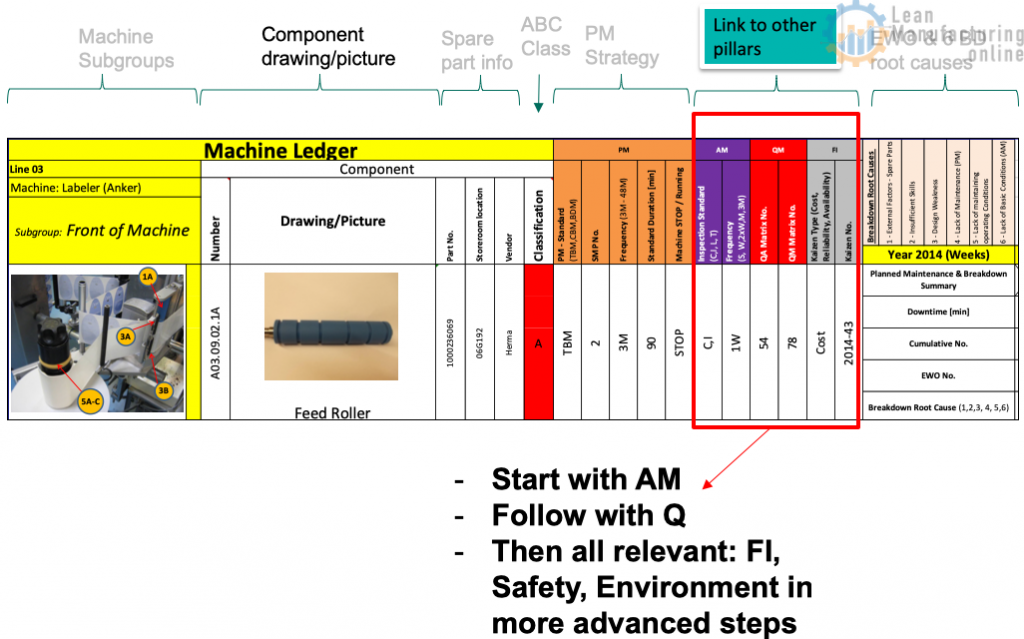
(DO) Create PM calendar using machine ledger
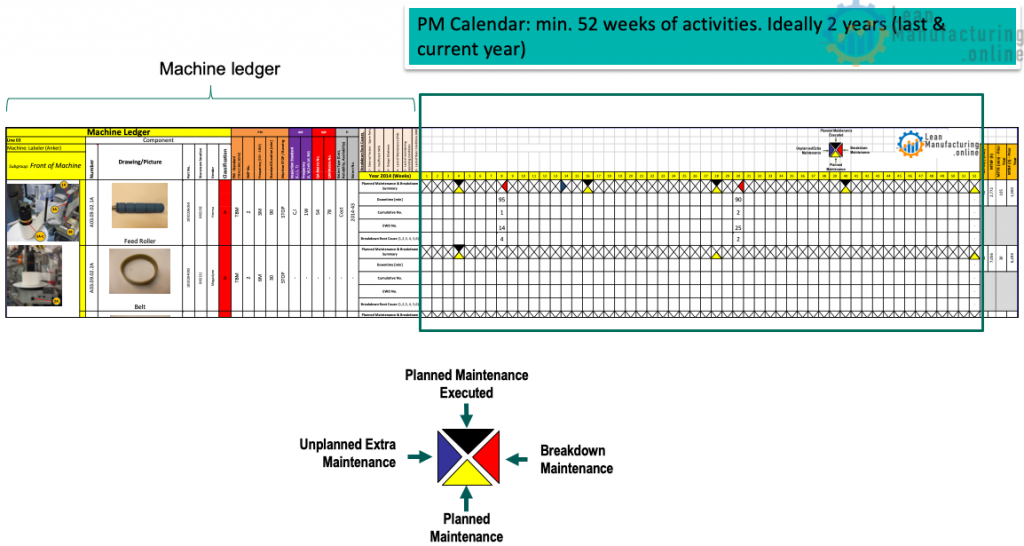
(DO) Valuable information
Update it in real-time and understand trends to improve
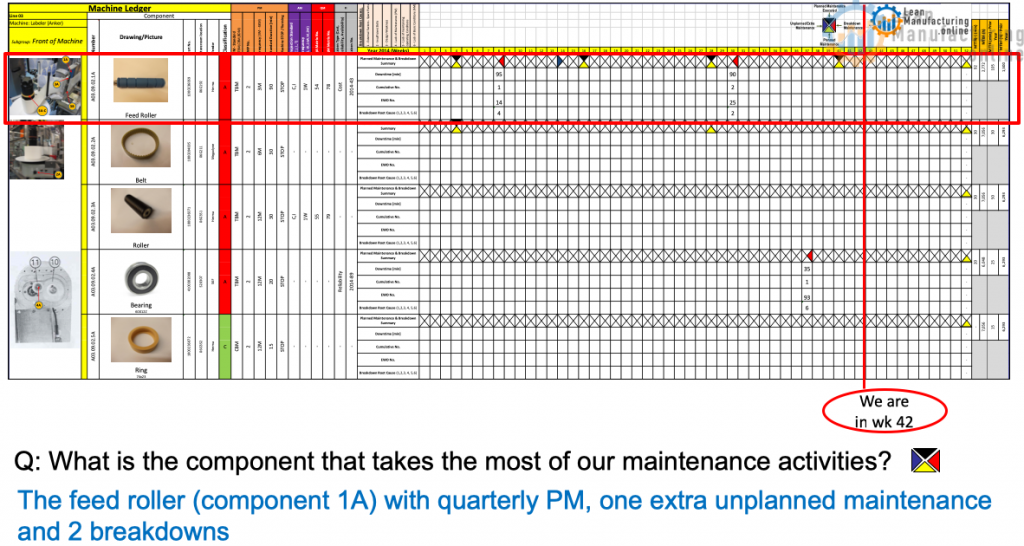
Q: What is our PM completion rate? It should be 100%
Can it be calculated by a week or by component, and can we extend the frequency of our PMs and reduce cost?
Q: When is the BD happening? Before/after PM, how close to the next PM?
One in between PMs, one just after PM (link with T&E pillar), one in week 37 due to lack of basic conditions (connection with AM)
Q: What are the root causes of the BDs?
Enterprise-Wide Optimization (EWO) will provide those details. In our cases, root causes are lack of PM (PM), insufficient skills (T&E/AM/PM), and lack of basic conditions (AM)
Q: How much extra unplanned maintenance?
Look for the blue triangles and ask yourself follow-up questions: Why did we have to do unplanned maintenance? How much are we spending on unplanned activities? Should we shorten the PM frequency?
Q: Can I increase the frequency of the PM and reduce cost?
We did not perform the scheduled maintenance on the belt, and we have not had any breakdown – There is an opportunity to evaluate extending the PM frequency.
Q: What is the MTBF and MTTR for each component?
They both should be updated every time we have a breakdown. If we have eliminated all the breakdowns, we measure MTTR (Mean time to replace) instead of MTTR (Mean time to repair).
Q: How does the MTTR compare against the standard time?
You can see if we are spending more or less vs. the standard time to complete the task by comparing MTTR and the Standard duration identified in the PM strategy section. If higher than standard, review the root causes.
Q: What components and time do I need for my next shutdown in week 52?
Look at the components and standard duration of activities for the shutdown week and plan your shutdown.
(DO) How do we get the benefits
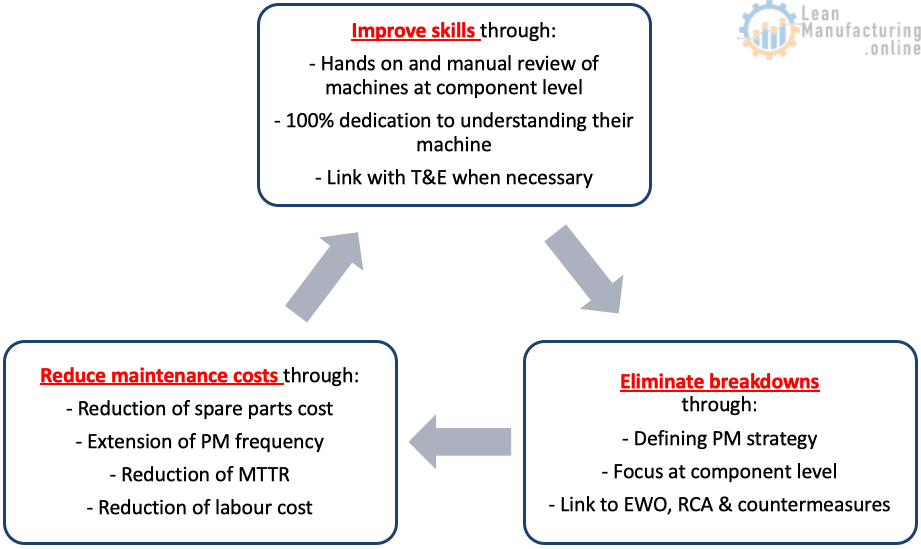
(DO) Other benefits that you can get as you do the activity
- Restore the equipment to basic conditions
- Define critical parameters
- Apply visual controls to sustain the basic conditions
- Identify, create or update the most critical Standard Maintenance Procedures (SMP)
- Update or create training manuals
(CHECK) Monitor breakdowns & maintenance cost results
Monthly tracking of results showing each step start & end date
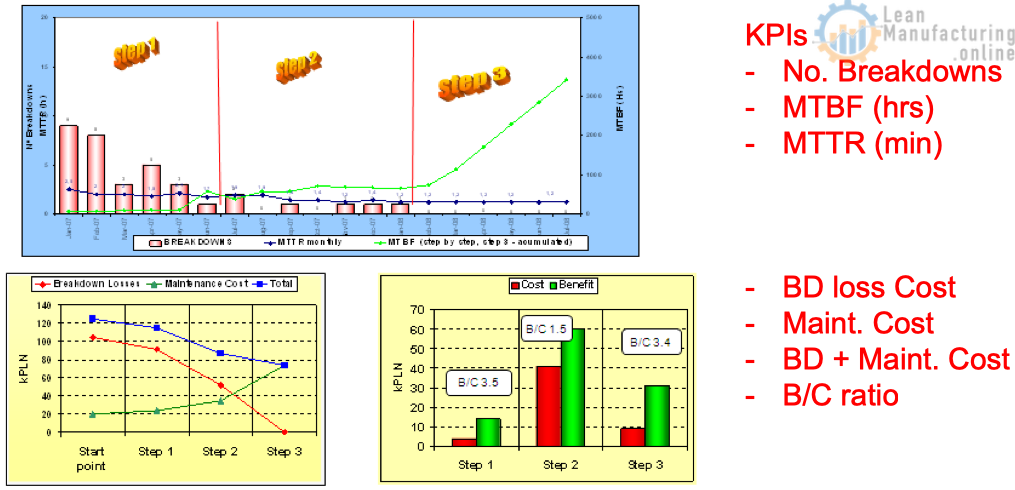
(ACT) Expand quickly into AA machines, then A, B, C
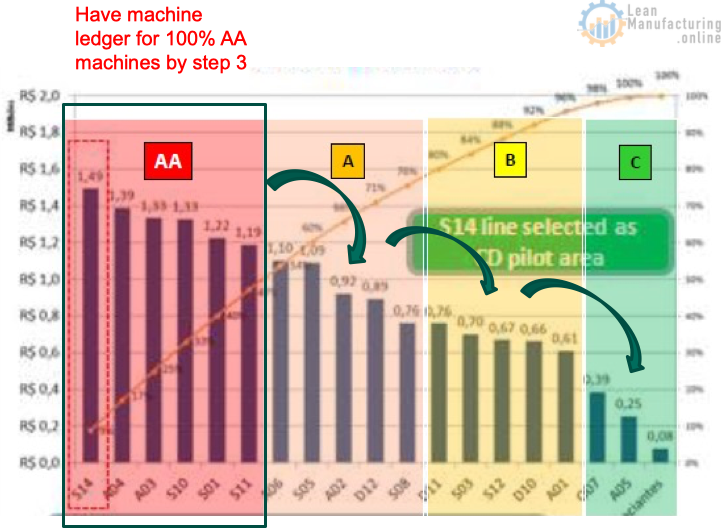
(ACT) Summary of key points
- Link the machine ledger with the PM calendar since the beginning.
- The machine ledger and PM calendar together are the single most powerful tool to drive maintenance results (cost and performance).
- They provide a horizontal view of your maintenance activities and improvement opportunities
- Track KPIs every month to check the results
More on Machine Ledger here (in italiano)