The Key Tool for Executing Focused Improvement
- Check – Observe, Collect Data
- Analyze – Determine Root Cause
- Plan – Formulate Actions
- Do
- Implement Plan
- REVIEW – Monitor results and return to Check
Cap-Do form can be found here.
CAP-Do: The Check Phase
- Identify the Problem
- “A state of difficulty that needs to be resolved”
- “A question raised for consideration or solution”
- Understand the Ideal Situation
- Identify the Phenomenon
- “Whatever, in matter or spirit, is comprehended by observation”
- “Any state or process is known through the senses rather than by intuition or reasoning”
Phenomenon Means:
- Observing the facts with our own
eyes & all senses - The facts without presumption
CAP-Do: Check Step 1
- Identify the Problem
- “A state of difficulty that needs to be resolved”
- “A question raised for consideration or solution”
- Understand the Ideal Situation
- Identify the Phenomenon
Check Step 1: Identify the Problem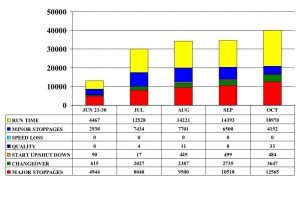
- Collect Data
- Go to the “actual place”
- Observe
- Take Photographs / Videos
- Interview
- Collect Data*
- Assemble all available related data from Loss Tree Analysis
CAP-Do: Check Step 2 Understand the Ideal Situation
Machine
- Equipment Sketches
- Operational principles & model
Material
- Material samples
Man & Method
- Flow charts of the process
- Forms and procedures
Check Step 3: Identify the Phenomenon
5W’s 1H* (Define the problem, show loss data)
- What, When, Where, Who, Which, and How.
- Requires information collected in CHECK Steps 1 & 2 to complete the 5W1H form and identify the “phenomenon”.
- If there is not enough data from CHECK Steps 1&2, the 5W1H must be paused to get the data.
- The cause is NOT assigned/implied in the Phenomenon statement.
What:
- What thing or product did you see the problem?
When:
- When did the problem occur?
Where:
- Where did you see the problem? (Line/Machine/Location)
- Where on the work or material did you see the problem?
Who:
- Is the problem related to skill? (Skill dependant or independent)
Which:
- Which trend (pattern) did you see the problem have?
- Is the trend random or is there a pattern?
How:
- How is the state different from a normal condition?
CAP-Do: The Analyze Phase
- Determine Root Cause
- 5 Why (Why-Why)
- Principle of Operation
- SEND Analysis
- Formulate Possible Actions
CAP-Do: The Plan Phase
- Review and Prioritize Possible Actions
- Short and Long Term Actions
- Assemble Required Materials
- Write OPL’s
- Schedule Work
- Create OPLs
CAP-Do: The Do Phase
- Safety Comes First
- Implement Actions
- Review
- Observe Results
- Hold the Gains
- Return to Check