One rationale for the existence of a private enterprise is that it contributes to the community by creating value. Thus it is only natural that companies that provide no value or that are harmful to the community should fall by the wayside. A reputation for maintaining a hazard-free, healthy workplace and a cheerful and animated corporate culture can only enhance a company’s value and help make it an attractive career choice. Attracting talented people able to contribute significantly to their company’s future is an essential part of ensuring its continued prosperity. The establishment and maintenance of such a corporate image depend upon every single employee has a strong sense of belonging to the organization and behaving appropriately. Practices that result in accidents, hazards, or pollution are a threat to a company’s very existence and should be systematically eliminated by means of a comprehensive SHE (safety, health, and environment) program.
Companies that are constantly afflicted by malfunctioning equipment or whose employees are forever troubleshooting unexpected problems cannot expect to establish a reputation for having a cheerful and animated corporate culture. SHE programs do not require anything highly specialized or out of the ordinary; they simply entail establishing entirely ordinary conditions through entirely ordinary activities that anyone can perform. They can be undertaken within the TPM program and can be performed in the workplace as part of any other daily activity, and they do in fact constitute a basic part of all other activities.
The basic approach to safety, health, and environmental management in TPM is multi-pronged. A zero-accident scenario must be achieved by eliminating every conceivable hazard or concern that might give rise to a safety incident. At the same time, all sources of health or environmental problems must be rooted out, enabling the company to create pleasant and hospitable workplaces whilst protecting the natural environment.
A TPM program is developed in practice by using an approach based on eight main activities, or “pillars”, each of which is advanced step by step to progressively higher levels. Section “How Safety Relates to the other TPM Pillars” describes how safety ties into each of the eight pillars, while Figure “Zero-Loss Business Management” shows how a Safety, Health, and Environment program, together with Training and Development, forms the foundation of effective business management.
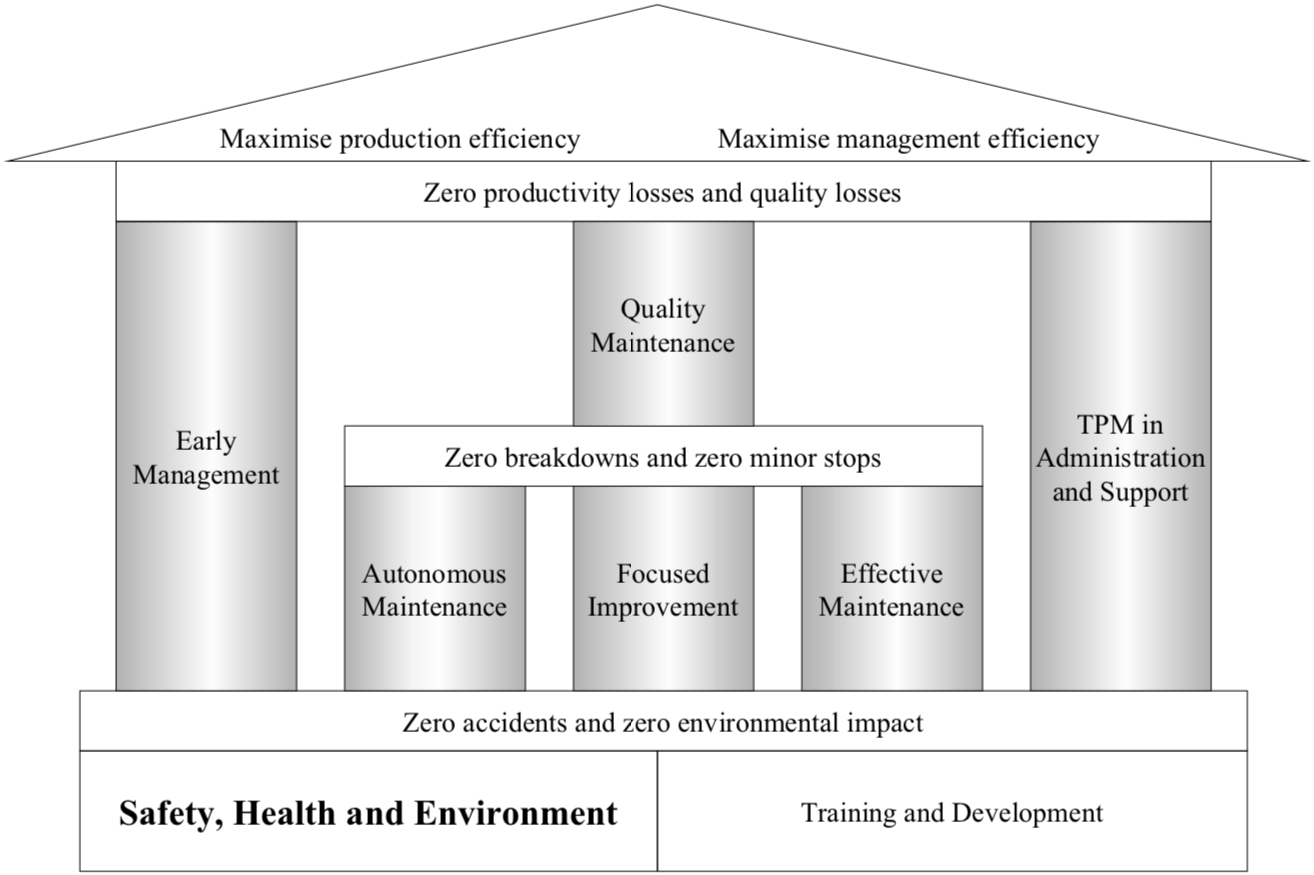
1 Autonomous Maintenance
Step 1 of Autonomous Maintenance is Initial Cleaning. Safety problems, (unsafe situations, unsafe behaviors, and other hazards) are identified during this step along with the other problems usually addressed in Autonomous Maintenance. The problems are then tackled through restoration and improvement during Step 2, and provisional standards are established in Step 3 to sustain the situation. Effective action must be taken during these steps to clear up any nagging concerns that operators may have relating to the possibility of behavioral accidents, fire, explosion, or other undesirable incidents. From Step 4 onwards, activities are pitched at progressively higher levels, with the aim of creating worker-friendly, accident-free workplaces. However, this cannot be achieved through Autonomous Maintenance alone and must be developed in conjunction with the other TPM pillars.
2 Effective Maintenance (also applies to Focused Improvements aimed at reducing equipment failures)
The key objective of Effective Maintenance is to eliminate unexpected breakdowns. This improves safety because equipment problems often lead to accidents, which are often due to operators’ lack of experience in dealing with abnormalities or carrying out non-routine tasks. Working towards zero breakdowns, minor stops and other equipment-related problems lessens the chance of accidents happening. However, maintenance itself necessitates a great deal of non-routine work, so painstaking efforts must be made to identify unsafe situations or unsafe behaviors and nip every possible accident in the bud.
3 Early Management
This pillar aims to create user-friendly, hazard-free equipment that can be operated with confidence. Fail-safe mechanisms and error-proofing systems should be incorporated into machinery and plant from the early design stages, and ways found to simplify operating and maintenance tasks to avoid the need for strenuous physical effort. The purpose of Early Management is to work towards achieving robust, trouble-free equipment and comfortable work environments, from the development phase onward
4 Quality Maintenance (also applies to Focused Improvements aimed at reducing quality defects)
Quality Maintenance aims to sustain zero-defect conditions (conditions guaranteeing defect-free products) in every production process. Any lapse in managing these conditions creates the possibility not only of quality defects but also of accidents or other mishaps. Rigorous establishment and sustainment of processing conditions are particularly crucial when hazardous materials are being handled. If a quality defect occurs, non-routine work will be required to deal with the problem, increasing the risk of an accident, which is why Quality Maintenance is important not only for guaranteeing product quality but also for improving safety.
5 Training and Development
In Training and Development within TPM, skills (the ability to do the job) are divided into five levels, ranging from level 0 (no knowledge at all) to level 4 (capable of teaching others), and the capabilities of individual operators are upgraded level by level. Accidents can happen if operators do not know how to handle tools correctly, for example, so this pillar of TPM helps to eliminate unsafe behavior by improving people’s operating and maintenance skills.
6 TPM in Administration and Support
Safety is also important in administrative and support departments. Development departments, for example, operate equipment such as pilot plants and test rigs in their laboratories to test new products and manufacturing processes, so they must manage safety effectively in order to prevent any accidents from occurring when using this equipment. Support departments may be responsible for packaging and transporting the final products, so they must also identify and resolve any unsafe situations or behaviors occurring in their workplaces through the step-by-step development of an Autonomous Maintenance program as described in (1) above.