“Equipment management” encompasses all of the activities undertaken to ensure that equipment is used as efficiently as possible in accordance with the business plan, in order to raise the company’s productivity and improve its profitability. More specifically, these activities consist of the following two things:
- Attaining business objectives by using equipment efficiently
- Shortening production lead times (the time spent getting ready for production)
Looking at these activities in terms of the service life of the equipment, we can divide them into two stages: one covering the period up to the “birth” of the equipment, and a second covering the period after the equipment is born. The stage up until the birth of the equipment is called the construction process, while the stage from the birth of the equipment onwards is called the maintenance process. In its broad sense, “equipment management” covers both stages, while in its narrow sense, it is taken to refer to the maintenance process only. The technical side of equipment management in the broad sense is called “plant engineering”, while the construction process is known as “project engineering”, or in other words, Early Equipment Management.
Using equipment efficiently means:
(1) Clarifying the core functions the equipment is supposed to fulfil throughout its life cycle in order to attain the company’s business objectives, and building these functions into the design;
(2) Ensuring that the core functions are sustained throughout the life of the equipment.
We shall call (1) the “core functions of the equipment”, and (2) its “MP (maintenance prevention) functions”. Table “Business Objectives and Equipment Functions Conducive to Attaining Them” shows how these factors relate to one another, while Table “Outline of Core Functions in Relation to Design Concepts” shows how various design concepts fit in.
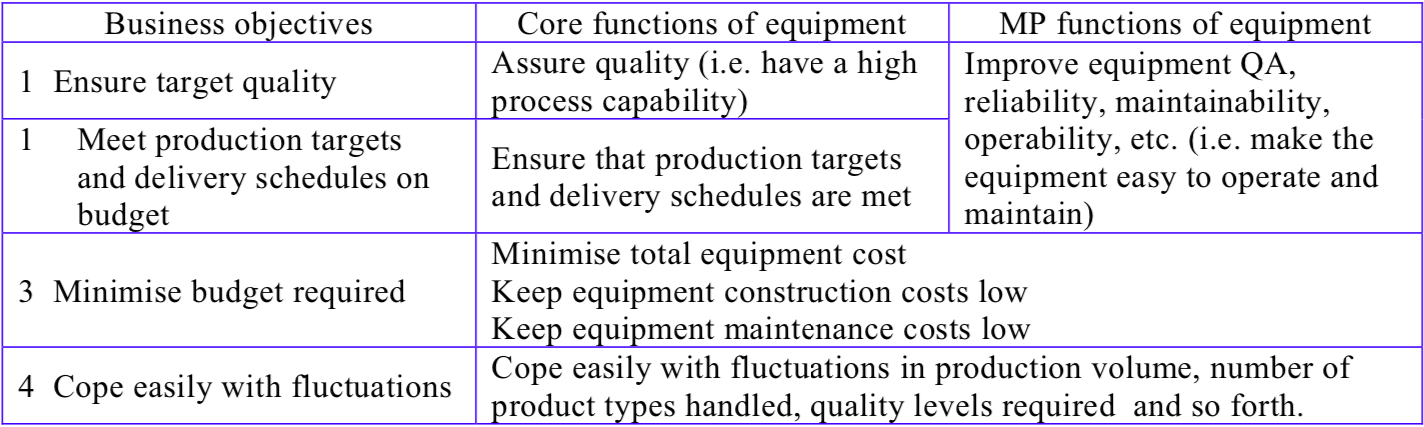
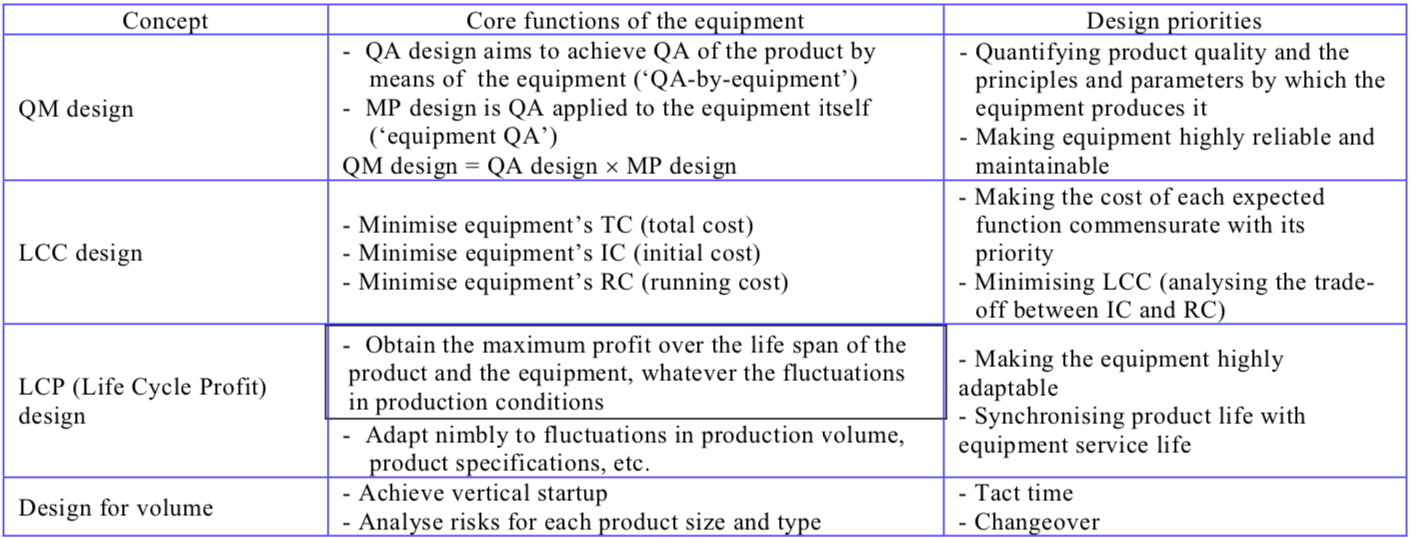
(1) Assuring target quality
Target quality is assured by QA-by-equipment in concert with equipment QA. Designing-in ‘”QA-by-equipment” means designing the equipment to have a high process capability, while designing-in “equipment QA” means designing the equipment in such a way that its core functions, and consequently its high process capability, are easy to sustain.
The function that makes the equipment’s core functions easy to sustain is called the “MP function”. The performance of any kind of equipment inevitably tends to deteriorate over time, and this deterioration needs to be predicted and periodically reversed by the equipment’s operators. The burden of maintenance can be lightened, but it can never be entirely eliminated, no matter how highly-automated and sophisticated the equipment, because the amount of investment required to automate the maintenance task itself would make it prohibitively expensive. The equipment designer’s mission is to find out what can be done to make this maintenance task easier, and design the equipment accordingly.
To achieve high levels of reliability, autonomous-maintenance-friendliness, operability, safety and so on, it is essential for the equipment designer to think about what the operator needs to do with the equipment, and design the equipment to make this as easy as possible. To this end, it is important to strike the right balance between designing-in QA-by-equipment and designing-in equipment QA. The design philosophy aimed at doing just this is called QM (quality maintainable) design (see Figure “QM (Quality Maintainable) Design”). Table “The Five Conditions for QA-Friendliness” shows the five conditions for achieving QA-friendliness.
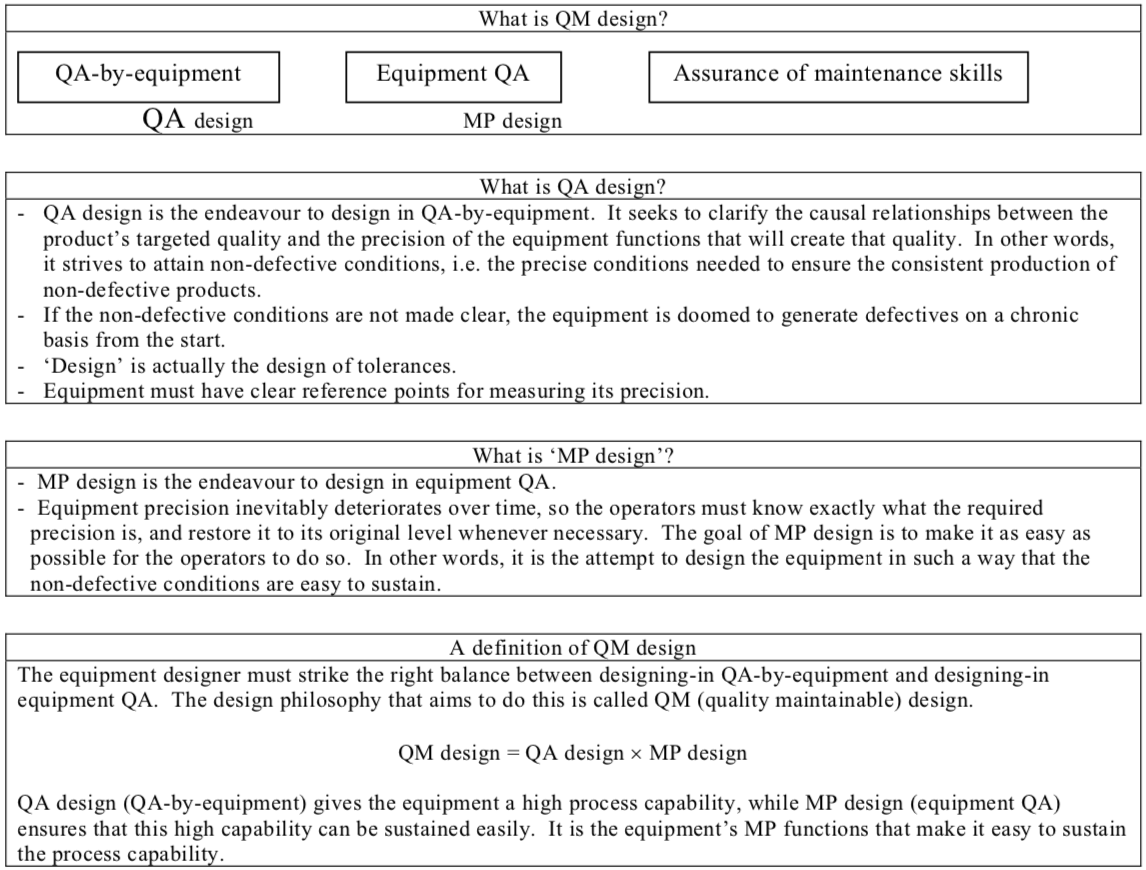

(2) Meeting production targets and delivery schedules on budget
The core functions required for meeting production targets and delivery schedules are the three elements of low-cost automation, i.e. simplification, standardization and specialization.
(3) LCC (life-cycle-cost) design
This is design aimed at minimizing the total cost of the equipment (see Figure “Relationship Between Total Equipment Cost and Number of Units Produced”). The total cost of the equipment (TC) is the sum of the initial cost (IC) and the running cost (RC). There is often a trade-off between IC and RC.
When the IC is at a maximum, the RC is at a minimum;
When the IC is at a minimum, the RC is at a maximum.
This relationship can be used to run a cost simulation aimed at finding the optimal total cost.
(4) LCP (life-cycle profit) design
Fluctuations can occur in production volume, number of product types handled, quality level, product specifications and so on. At the design stage, production volume is strictly hypothetical. In real life, fluctuations in production volume can reduce profits: if the equipment is over-specified, for example, a cut in production can raise the unit cost of the product, while if it is under-specified, an increase in production can lead to lost opportunities. The design philosophy that aims to create equipment able to accommodate fluctuations in indeterminate factors like production volume, is called LCP design. LCP design and LCC design are closely interrelated.
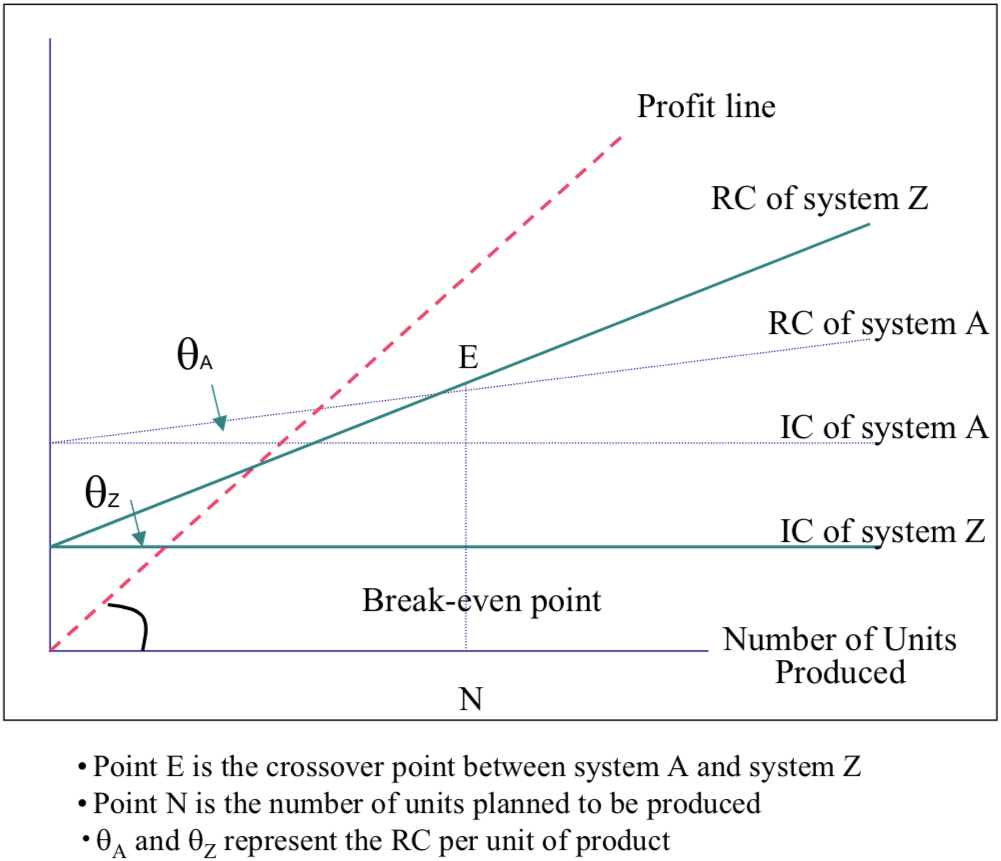
Figure “Cost-Reduction Strategies” shows the basic cost items used in LCC and LCP analysis and strategies for reducing them.
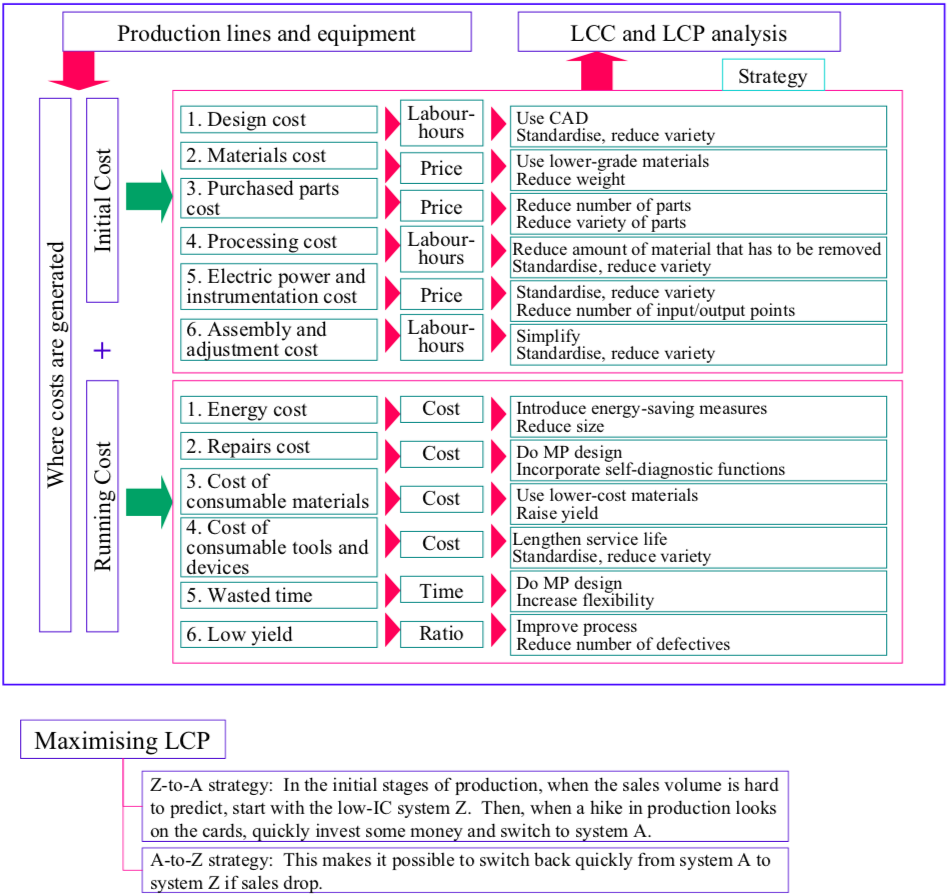
This idea, whereby the equipment’s cost structure can be switched according to production requirements, offers the best of both worlds. However, if this approach is to be used, it is vital that the switch can be made stage by stage, and that the equipment is rapidly adaptable to a wide range of purposes. The ability to respond nimbly to fluctuations in production requirements – in other words, high flexibility – is the key to maximizing LCP.