Just how important is Quality in QFD?
Prior to the spread across the world of QFD concepts, there were two main concepts used in the world of quality assurance: conformance quality and design quality. In the early years of quality assurance, it was manufacturing quality (conformance quality) that received the most attention. The reason for this was that variation occurred in manufacturing quality, not in design quality. In other words, the earliest forms of quality assurance were intended to ensure that the products being produced conformed to design quality with as little variation as possible, and that is why so much attention was paid to manufacturing quality.
Thanks to these activities, businesses learned how to manufacture products that conformed to design standards with very low variation. It goes without saying that the use of statistical and other methodologies contributed greatly to this success. Once businesses were able to produce according to design quality, however, they quickly realized that unless the design quality itself was also of a very high standard, their products would not sell. That was the point where they realized the importance of planning quality, which comes one step ahead of design quality in the process of product design. After giving some thought to the things that affect planning quality, the concept of required quality was born.
In other words, the required quality was defined as the level of quality required by the market, and planning quality was based on the extent to which quality was required and expected in the market. Design quality was then based on planning quality, and conformance quality was heightened by manufacturing products to conform exactly to design quality. Thus, conformance quality was no longer a matter conforming to design quality; it also came to represent conformity with market requirements. Let us look at the ball-point pen as an example. In order to manufacture a pen, the length and diameter of the pen shaft must be established. Let us suppose that these two dimensions are fixed at 140 mm and 8 mm, respectively. Since these two parameters comprise design quality, there will be no variation from them in the manufacturing process. The pens will be manufactured to these dimensions using an injection molding machine. There will be some slight variation in the actual size of the manufactured pens since no matter how good precision machinery is, there will still be some variation. The concept of conformance quality, however, is based on how closely the actual dimensions of the manufactured product match those specified by design quality. Japanese manufacturers have learned to achieve very high levels of conformance quality. Even when there is some variation, it is always within the range of tolerance permitted by the applicable manufacturing standards. There still remains, however, the question of why the dimensions were originally fixed at a 140 mm length and 8 mm diameter. What was the basis for determining that size?
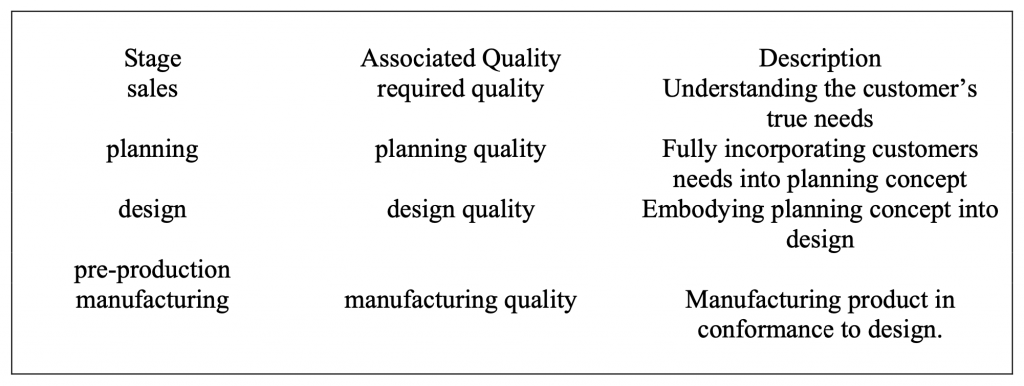

The length and diameter of the shaft of a ball-point pen are predicated on hidden requirements held by the customer when he purchases a pen, such as “easy to hold” and “can write for long periods of time without fatigue,” and the closer a product meets these requirements, the better it will sell. Customers might also have other reasons for choosing a particular product, such as “vivid colors,” “attractive shape,” or “interesting design.” It might not be possible to meet all of these requirements in a single product, but most successful products are designed to meet as many of these requirements as possible or sometimes are designed to be differentiated from the competition by fulfilling a particular requirement.
QFD activities begin with the determination of required quality, which is based on the needs of the market, and then continues through the stages of determining planning quality based on required quality, determining design quality that satisfies the requirements of planning quality, and manufacturing a product that conforms to the conditions specified by design quality. There are other considerations, as well, that some will say ought to be included in this flow of activities, such as end-of-life quality. In fact, the quality assurance from a selection of raw materials to end-of-life quality is fast becoming the standard.

Note: The lines that point toward the center of and circulate through the Sun represent the processes in which energy consumption and the disposal of non-recyclable materials occur on the Earth. The lines which circulate to the outside of the bold line are “positive” quality cycles and those which circulate to the inside are “negative” quality cycles.