(1) Defining MP
Defining MP and MP design
MP is an abbreviation of “Maintenance Prevention”. It is defined as follows:
Activities carried out at the stage of planning and designing new equipment, to promote reliability, maintainability, economy, operability, safety etc. and minimize maintenance costs and deterioration losses, by incorporating maintenance information and new technology.
The ultimate aim of these activities is to create maintenance-free equipment. The activities can be divided into two categories: providing MP information and incorporating it into the equipment’s design.
Providing MP information means collecting and organizing knowledge about problems identified in the course of operating or maintaining existing equipment, and how they were resolved. In other words, it means finding out about improvements made to existing equipment, and feeding this knowledge back to the design department in a readily-usable format, so that it can be used to improve the design of new equipment.
This is important, because, as everyone knows, most advances in equipment technology have resulted from improvements made to correct problems or shortcomings in existing technology.
Today’s production machinery and process plant have become so large that a single operational error can have a major negative impact on the local and even the global environment. They have also evolved into systems that operate round the clock to produce high-precision products. This means that bad equipment design decisions can jeopardize a company’s future, so equipment designers need to stay closely in touch with reality and be careful not to get carried away by their own ideas. MP information provided by the operating and maintenance departments should be fully incorporated into the designs, and the design process should be aimed at ensuring trouble-free operation right from the outset.
Defining MP design
Equipment design aimed at minimizing LCC is called “MP design”. It was originally defined as follows:
The goal of MP design is to minimize the equipment’s life-cycle cost, or LCC (the total cost of the equipment over its entire life-cycle, i.e. the sum of its acquisition costs and running costs). The design approach in which the equipment’s LCC is included in the design specification along with its functionality, reliability, maintainability and so forth, is known as ‘LCC design’. MP design is the technical manifestation of LCC design.
In TPM, this approach to MP design is expanded, and the term “MP design” is used to mean a design philosophy pursuing efficiency to the extreme, by focusing not just on reliability and maintainability, but also on preventing all other losses that tend to drag down the efficiency of the production system.
(2) The importance of MP
To create equipment that itself can assure product quality, the causal relationship between product quality and equipment precision needs to be made explicit. The design philosophy that aims to do this is called the ‘design of core equipment functions’. However, the precision of the equipment will deteriorate over time, so it needs to be quantified and periodically restored to its original level. Reversing deterioration is principally the role of the operator. The aim of MP design is to make this role as easy as possible.
The temptation for the equipment designer is to focus on the equipment and its intrinsic reliability and thereby lose sight of the operator’s role in operating the equipment. Consequently, the operator’s role ends up being dictated by the equipment. In other words, the operators have to modify their behavior to suit the needs of the equipment. This might be acceptable in theory; but in practice, it tends to make life very difficult. And if it becomes difficult, or even impossible, to uphold maintenance standards, it will also be impossible to sustain the equipment’s core functions.
As Figure “The Concept of MP Design” illustrates, there is a trade-off between maintenance skills and the MP function.
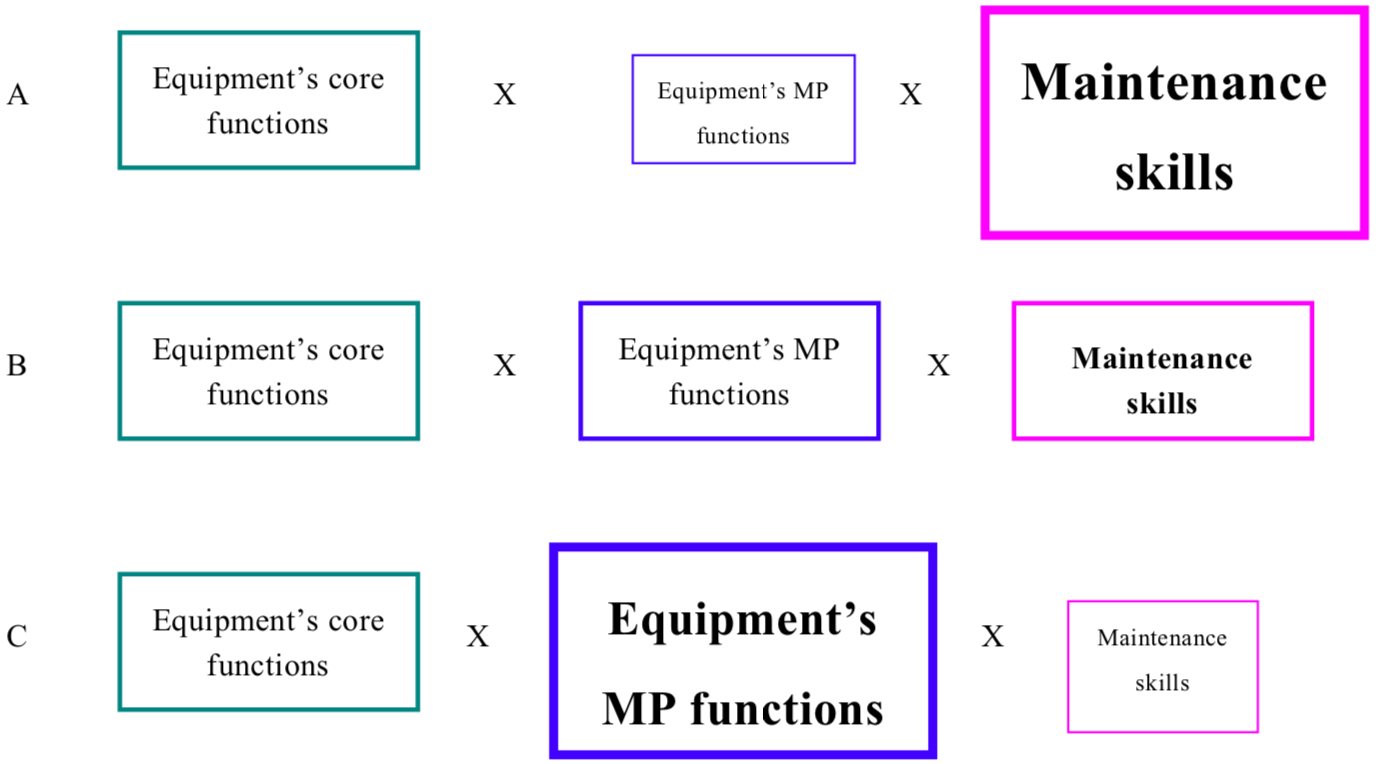
Pattern A results in a design highly dependent on maintenance skills, while Pattern C aims to lighten the maintenance burden by strengthening and enhancing the equipment’s MP functions. Ideally, MP design should be pitched correctly for the actual level of equipment maintenance skills possessed by your company.
(3) MP requirements
- Minimize the amount of breakdown maintenance generated by the equipment. In other words, design for higher reliability (i.e. a long MTBF (Mean Time Between Failures)).
- Design the equipment so that any breakdown maintenance generated by the equipment can be handled more efficiently. In other words, design for high breakdown maintainability (i.e. a short MTTR (Mean Time To Repair)).
- Design the equipment so that any preventive maintenance it requires can be handled more efficiently. In other words design for high preventive and autonomous maintainability.
- Design the equipment to facilitate CBM (condition-based monitoring). In other words, design for high diagnosability.
- Design the equipment to be safe and easy to operate.
Table “MP Design Attributes” shows the basic attributes that should be covered by MP design. Table “Main Contents of MP Design Checksheets” shows the principal items that should appear on MP design checksheets, while Figure “Typical Checksheet” shows a typical checksheet. Figure “Table of Equipment Design Issues” enumerates the equipment design issues covered so far.
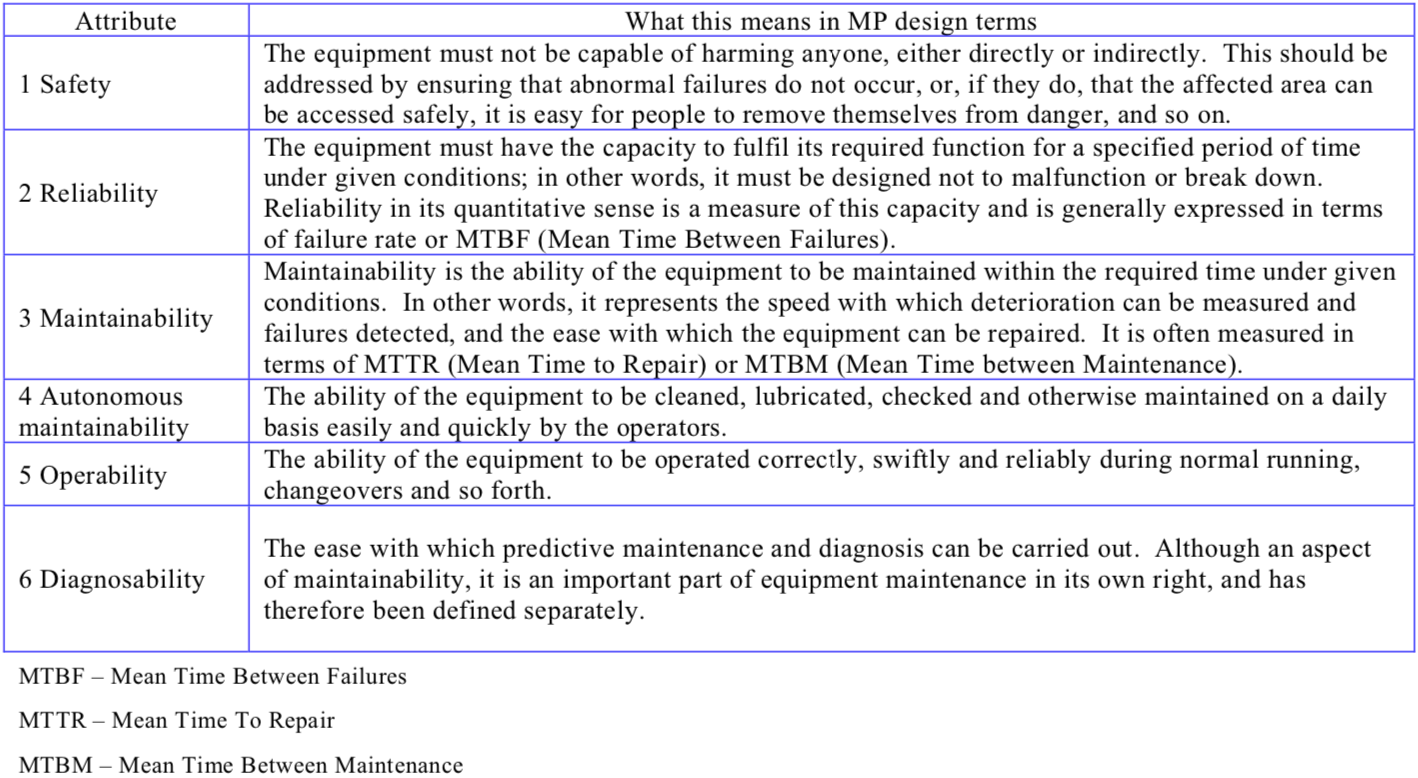
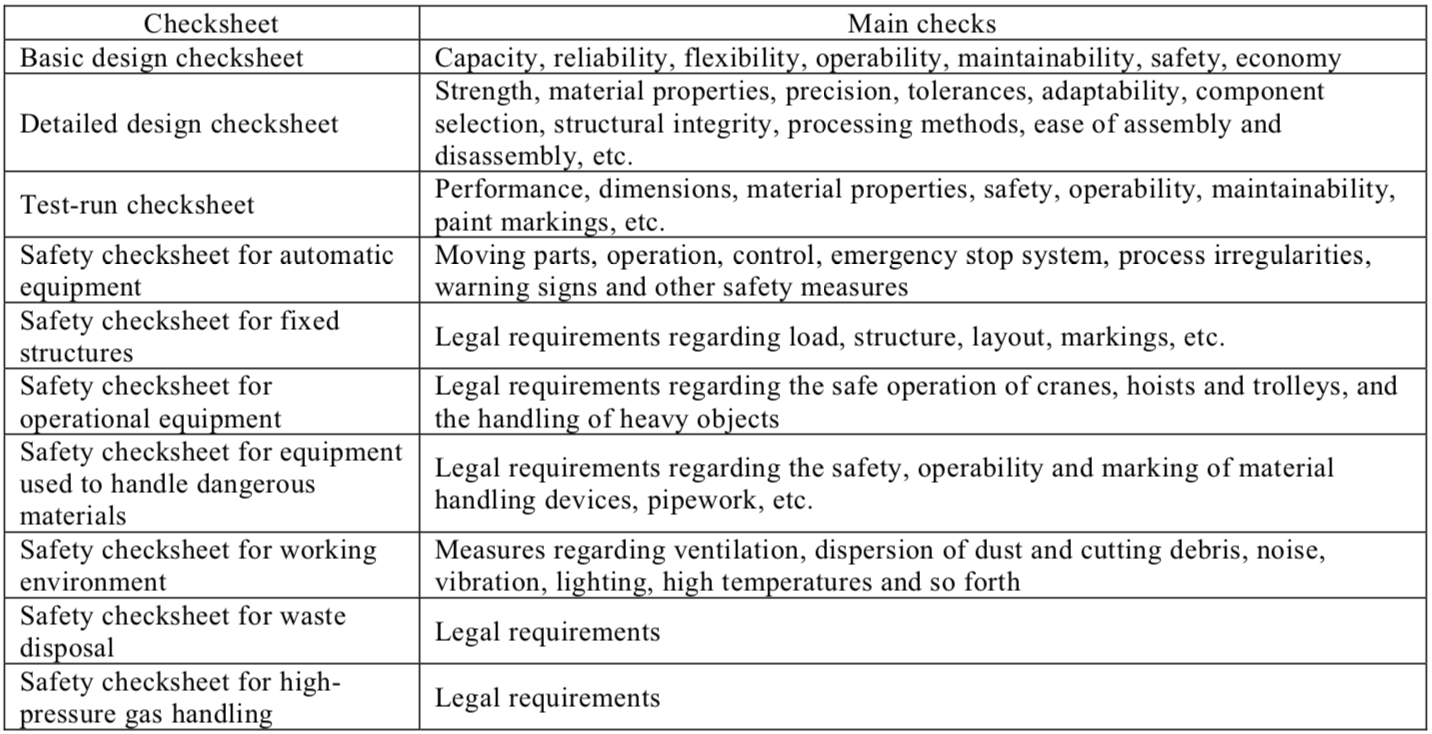
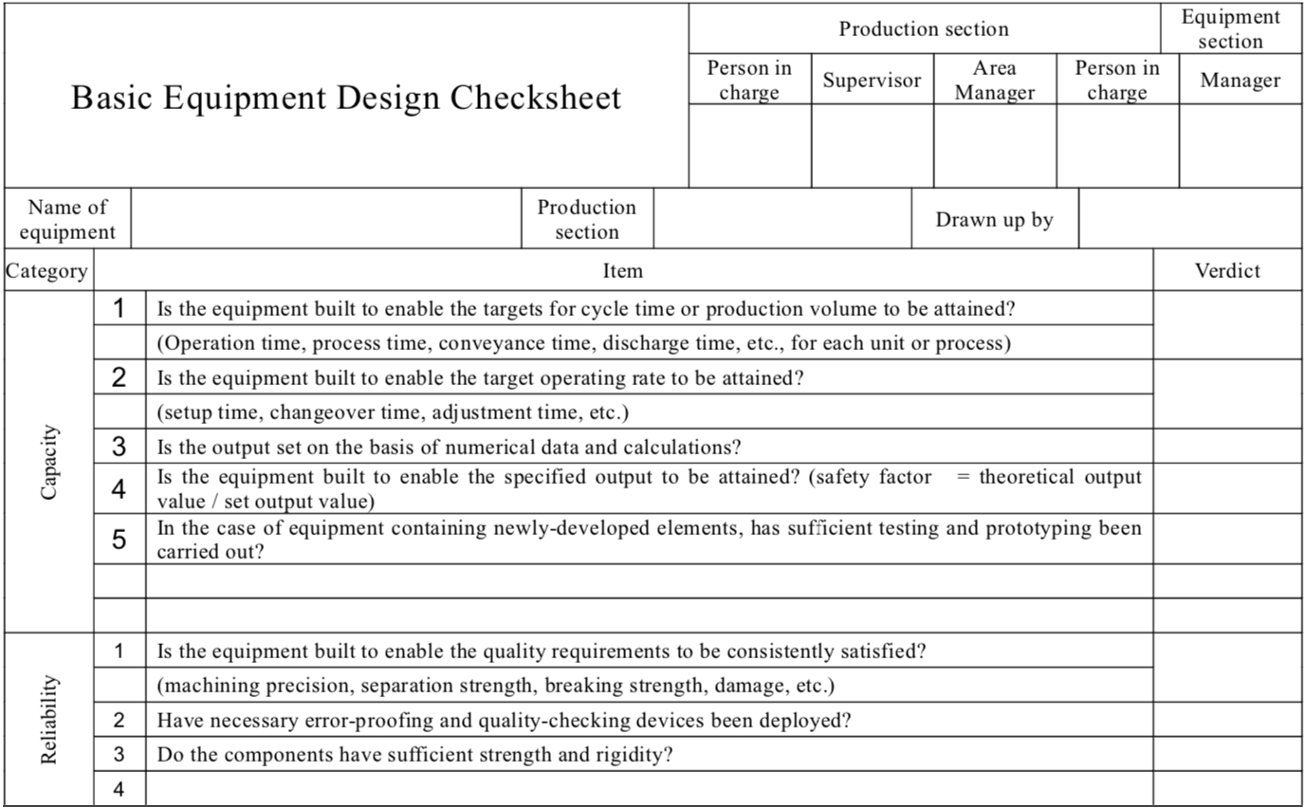
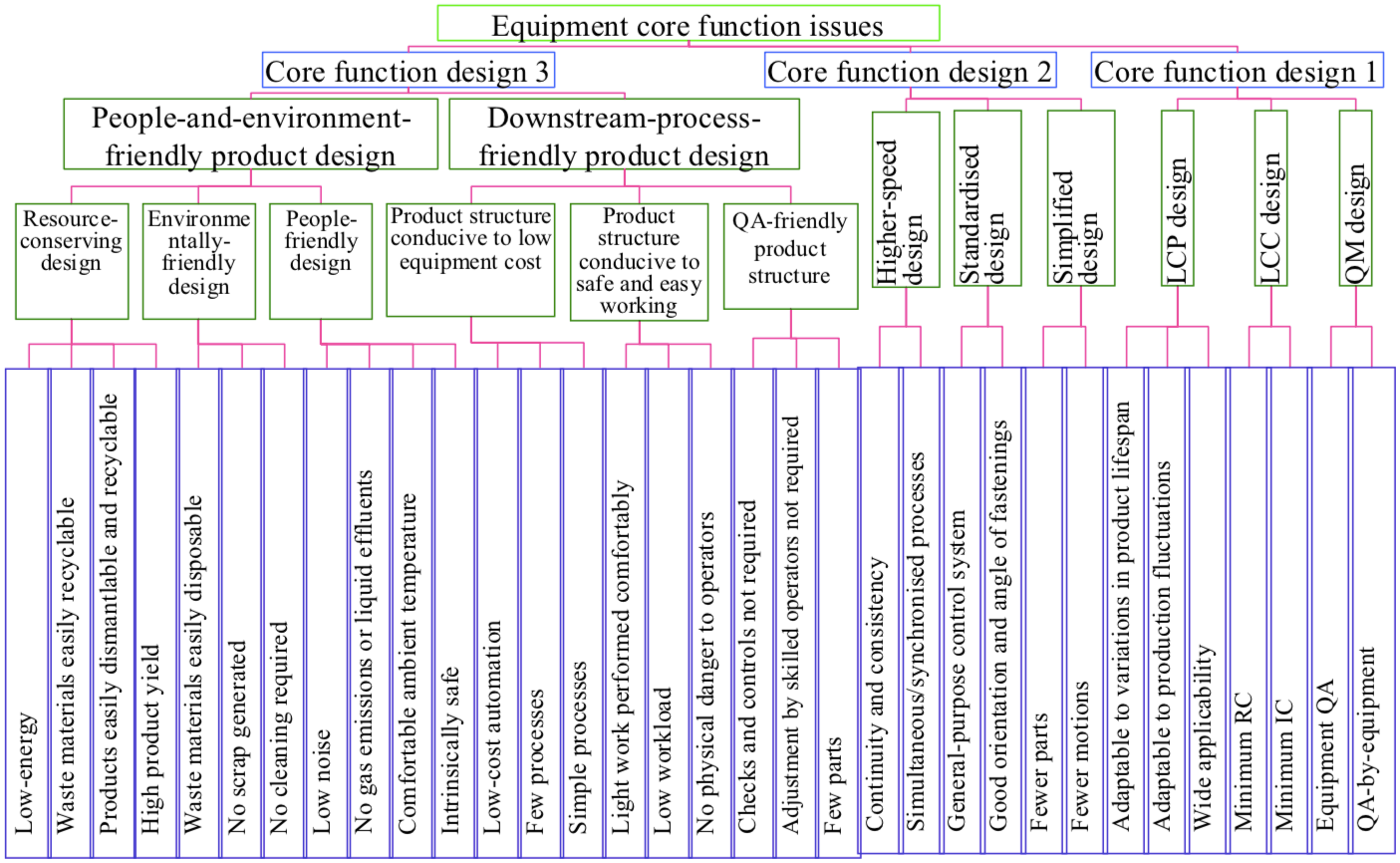