TQM is a management approach for an organization, centred on quality, based on the participation of all its members and aiming at long-term success through customer satisfaction and benefits to all members of the organization and society.
According to International Organization for Standardization (ISO)
TQM is consists of three models:
- Total: involving the whole organization, supply chain, and/or product life cycle
- Quality: with its usual definitions, with all its complexness
- Management: the system of driving with steps like Planning, Organizing, Leading, and Controlling
Eight Principles of Total Quality Management
The American Society for Quality (ASQ) defines total quality management as an organizational strategy in which all employees continuously improve processes that will improve customer satisfaction.
To accomplish this, they follow these eight principles of total quality management:
- Customer focus – all quality efforts should be to increase customer satisfaction.
- Full employee involvement – management must provide a work environment in which everyone is committed to the quality goals.
- Process-centered – processes must be clearly defined, measured, and improved.
- Integrated system – the critical processes of a business run horizontally across the different departments and functions of the organization. Quality improvement projects should focus on these critical processes.
- Strategic and systematic approach – management must provide a strategic plan that includes quality as a significant part of the organization’s mission and goals.
- Continuous improvement – processes must be continuously improved to increase customer satisfaction.
- Fact-based decision-making – performance must be measured, data must be analyzed, and decisions must be based on that information.
- Communications – an effective communication strategy motivates employees to perform at a high level.
Philosophy, principles and concepts of TQM
TQM is a vision in which the firm can only succeed through long-term planning by drawing up and executing annual quality plans, which slowly lead the firm towards the realization of the vision, i.e. to the point where the following portrayal of TQM becomes a reality:
A corporate culture characterized by increased customer satisfaction through continuous improvements, in which all employees in the firm actively participate.
Quality is a part of this definition in that TQM can be said to be the culmination of a hierarchy of quality definitions:
- Quality – is to satisfy customers’ expectations continuously.
- Total quality – is to achieve quality at a low cost.
- Total Quality Management – is to achieve total quality through everybody’s participation.
TQM is no inconsequential vision. When most domestic and overseas markets are characterized by cutthroat competition, more and more firms realize that TQM is necessary to survive. Today, consumers can pick and choose between a mass of competing products – and they do. Consumers select the products that give the highest value for money, i.e. those products and services which provide the highest degree of customer satisfaction concerning price.
A verse from the Book of Proverbs reads: ‘A people without visions will perish.’ Likewise, firms without visions will also perish. As Professor Yoshio Kondo of Kyoto University, Japan, put it at one of his visiting lectures at the Århus School of Business in Spring 1992: Companies without CWQC will sooner or later disappear from the telephone directory.
The concept of company-wide quality control (CWQC) has been described in more detail in Dahlgaard, Kristensen and Kanji (1994), from which the following quote has been taken:
The concept of TQM is a logical development of Total Quality Control (TQC), a concept first introduced by A.V. Feigenbaum in 1960 in a book of the same name. Though Feigenbaum had other things in mind with TQC, it only really caught on in engineering circles and thus never achieved the total acceptance in western companies intended. TQC was a ‘hit’ in Japan, on the other hand, where the first quality circles were set up in 1962 and which later developed into what the Japanese themselves call CWQC, Company-Wide Quality Control. It is identical with what we in the West today call TQM.
Dr. Armand V. Feigenbaum, the developer of “Total Quality Control” concept, was President and CEO of General Systems Company, which he founded in 1968.
In his book Total Quality Control, Feigenbaum (1960) states that TQC is an effective system for integrating the various initiatives in the field of quality to enable production and services to be carried out as cheaply as possible consistent with customer satisfaction.
This definition contains the very root of the problem. The reason why TQC was not a success in Western forms is especially due to the fact that Western management was misled by Feigenbaum’s reference to an effective system into thinking that TQC could be left to a central quality department. As a result, the administration failed to realize that an essential ingredient of TQC is the management’s absolute commitment to quality improvements. Effective systems are necessary but by no means sufficient conditions for TQC.
The new TQM concept aims to ensure that history does not repeat itself by deliberately including management in the concept’s definition. It makes it impossible for management to disclaim its responsibility. It sends a clear message through the corridors of power that this is a task for top management and thus also for the board of directors.
Of course, there is more to it than substituting an M for a C. Visions and definitions must be operationalized before they can be applied in everyday life. We attempt to do this below by constructing the so-called TQM pyramid.
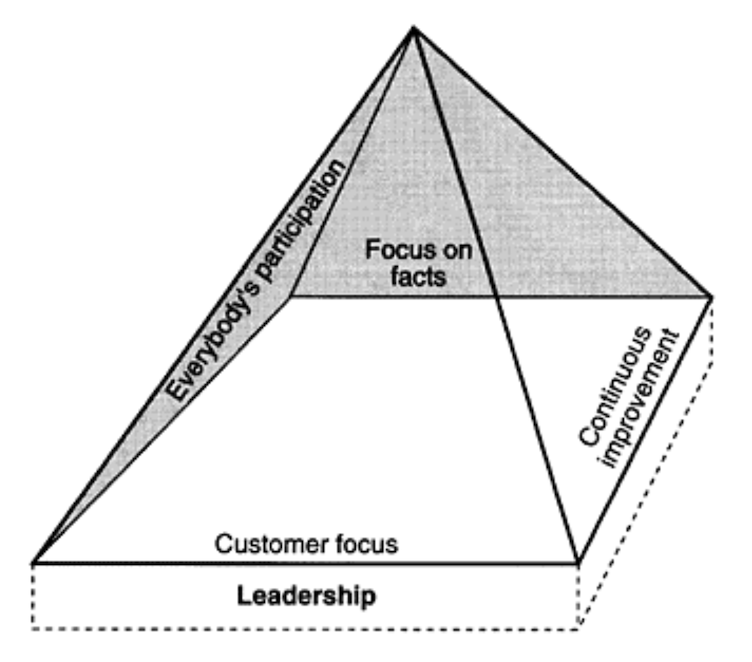
Quality and Business Performance
The association between quality, profitability, and market share has been studied in depth by the Strategic Planning Institute of Cambridge, Massachusetts. The finding, based on performance data of about 3000 strategic enterprise units, is unequivocal:
One factor above all others – quality – drives market stake. And when superior quality and substantial market share are present, profitability is virtually secured.
There is no doubt that relative sensed quality and profitability are strongly related. Whether the profit calculation is the return on sales or return on investment, businesses with a superior product/service offering beat those with inferior quality.
Even producers of commodity or near-commodity products strive and find ways to distinguish their products through cycle time, availability, or other quality attributes. In addition to profitability and market share, quality drives growth. The linkages between these correlates of quality are presented in the Figure below.
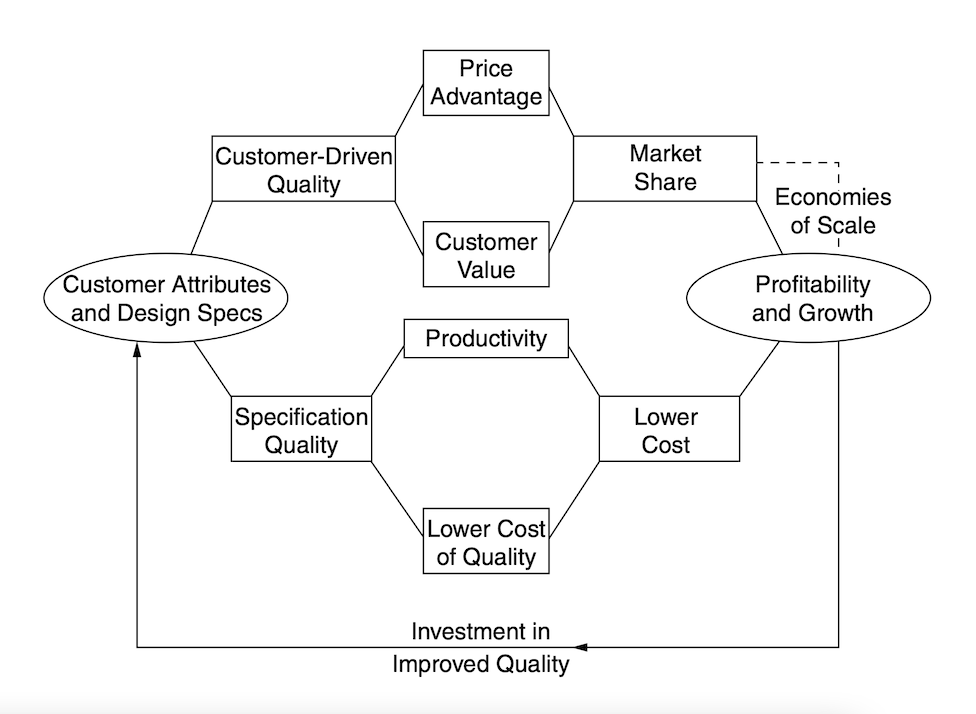
Quality can also reduce costs. This reduction, in turn, provides an additional competitive edge. Note that Figure “The Quality Circle” includes two types of quality: customer-driven quality and conformance or internal specification quality. The latter relates to appropriate product specifications and service standards that lead to cost reduction. Internal or conformance quality is inversely associated with costs, and thus, Crosby coined the phrase: “Quality Is Free.” As quality improves, so does cost, resulting in improved market share and profitability and growth. It provides a means for further investment in such quality improvement areas as research and development. The cycle goes on.
In summary, improving both internal (conformance) quality and external (customer-perceived) quality not only lowers the cost of poor quality or “non-quality” but also serves as a driver for growth, market share, and profitability.