6. Why-Why Analysis
7. Industrial Engineering (IE) Techniques
Products are manufactured on the shop floor through a combination of people, equipment and raw materials. This means that the efficiency of what people do must be raised at the same time as the efficiency of the equipment they operate, and IE techniques are an important weapon for doing this. Figure “Improvement Procedure and Key Points” shows the procedure and key points for effecting improvements by using IE techniques to highlight current issues.
IE techniques include measurement techniques and analytical methods (see Figure “IE Measurement and Analysis Techniques”). It is important to use these effectively to come up with improvement ideas and examine improvement proposals thoroughly.
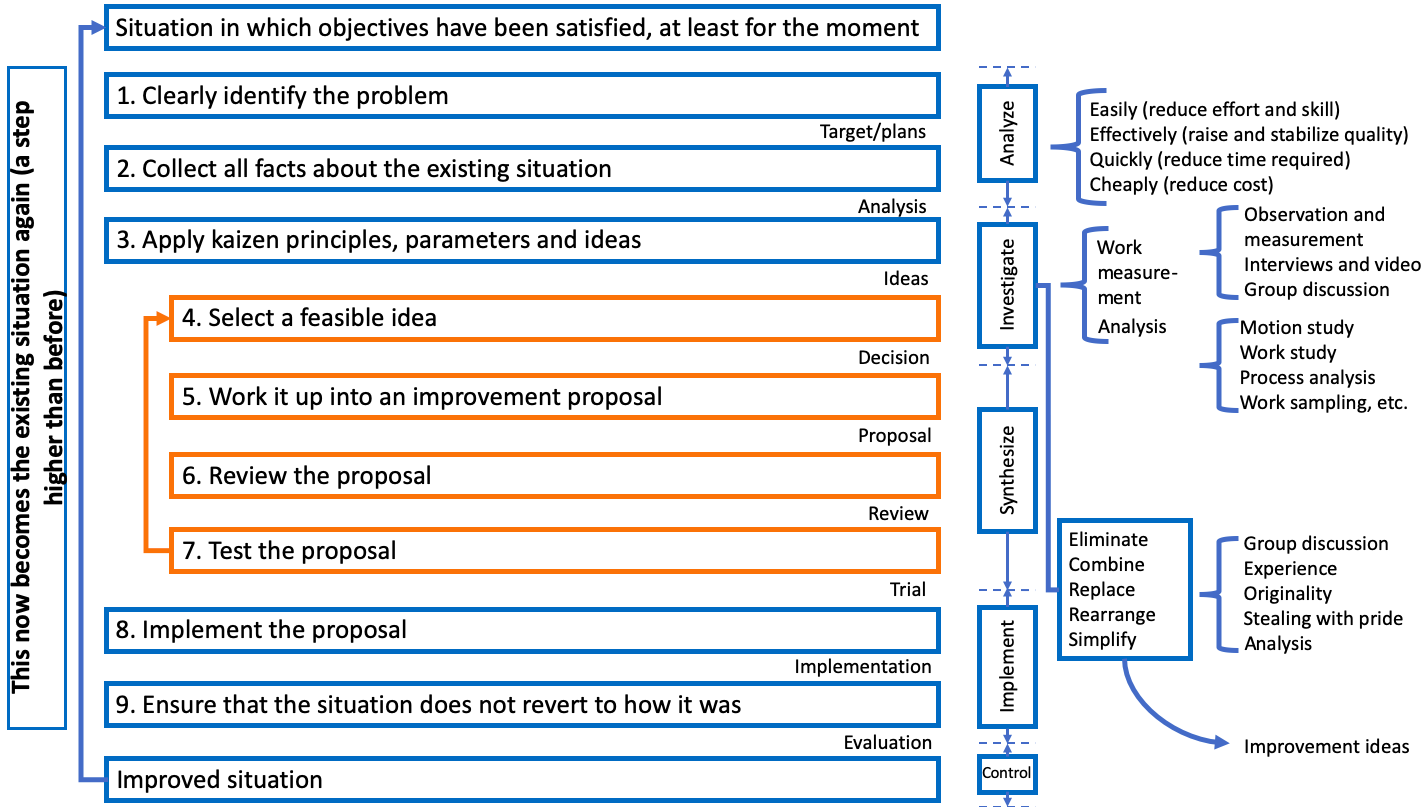
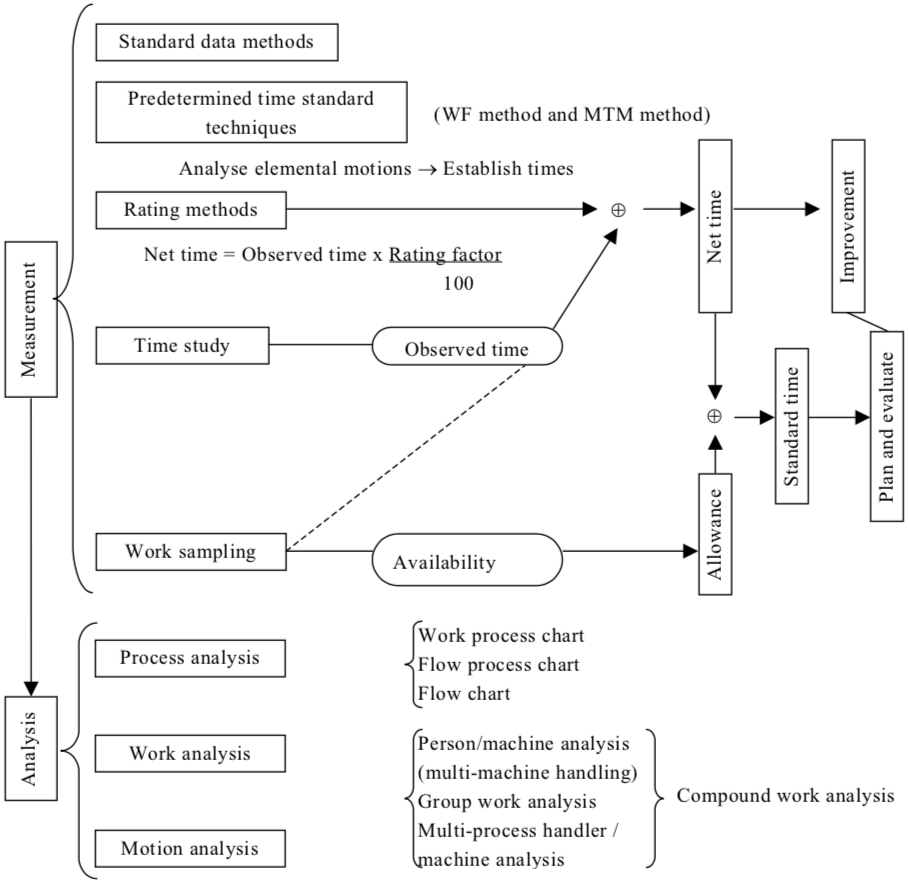
Human behaviour and motion take place for a purpose, and the key issue is their efficiency relative to their purpose. It is important to be ‘motion-minded’, that is, to adopt an analytical, businesslike approach. Being “motion-minded” means:
- Always noticing and being concerned about wasteful working methods
- Always being aware of the principles for improving such methods, as a matter of common sense
Mastering the procedure for devising more efficient working methods, and practising it habitually.